1. 引言
随着科学技术的飞速发展,现代机械装备逐渐趋于多元化和复杂化,服役环境多种多样,变载荷、大扰动和强冲击等恶劣工况屡见不鲜,一旦发生故障,会造成严重的经济损失甚至人员伤亡 [1] [2] 。因此,对机械装备开展预测与健康管理(Prognostics and health management, PHM),进行健康评估与预测,基于预测结果订购备件,制定预测性维护策略,对保障机械装备安全服役、提高生产效率和增加经济效益至关重要 [3] 。
在电动汽车空调系统中,压缩机通过不断压缩冷媒改变其物质状态来达到控制车内温度的目的。其中,涡旋压缩机主要由电机驱动一个旋转的离心轴承来实现动涡盘与静涡盘的啮合,动涡盘轴承由于载荷变化大、工作条件复杂等原因常常成为涡旋压缩机损坏失效的主要原因。影响轴承疲劳失效的原因主要有载荷、转速、润滑、材料特性、制造等。滚动轴承的故障诊断和剩余寿命预测方法的研究对保障压缩机系统安全、可靠、稳定运行有着非常关键的作用。如何提高轴承疲劳寿命预测的准确性成为一个紧迫的问题,并引起了越来越多学者的关注。涂文兵 [4] 等人以滚子轴承NU306为研究对象,通过分析滚动体与套圈及保持架接触力的变化曲线,揭示了故障对轴承内部接触状态的影响规律;Lei Ren [5] 等人提出了一种基于深度卷积神经网络(CNN)的轴承剩余使用寿命预测新方法;Wei KOU [6] 等人基于ANSYS/LS-DYNA对深沟球轴承的红外特征进行了动态模拟。认为滚珠与滚道之间的滑动摩擦是发热的主要原因,并考虑了径向载荷、转速和摩擦系数对滚珠轴承的影响。详细讨论了热量的产生和红外分布特性;张永超 [7] 等人将受限玻尔兹曼机改进后引入滚动轴承寿命预测模型当中,提出了一种基于受限玻尔兹曼机与卷积神经网络的轴承寿命预测RBM-CNN模型;胡腾 [8] 等人在扩展Harris滚动轴承非线性分析模型、建立滚动轴承耦合刚度矩阵的基础上,建立了一种综合考虑主轴离心力效应和陀螺力矩效应的系统动力学数字模型,分析论述了主轴离心力效应等因素在高转速场中的动力学特性的影响规律;Yongwu Wang [9] 等人采用动力与有限元相结合的方法,验证了两种不同工况下轴承部件的应力分布、速度和加速度存在明显差异;滕文博 [10] 等人基于Romax仿真分析工业机器人轴承在高温工作条件下的寿命情况,发现轴承工作温度对轴承寿命的影响考虑了轴承材料的硬度下限;Jason Deutsch [11] 等人提出了一种集成了深度信念网络和粒子滤波器的用于混合陶瓷轴承的RUL预测的新方法;魏延刚 [12] 等人对某大兆瓦风电机组齿轮箱进行分析,发现内外圈相对倾斜对轴承疲劳寿命影响非常大,倾斜量越大,疲劳寿命越短;Nannan Zhang [13] 等人提出了一种数据驱动的剩余使用寿命预测方法,采用统计方法提取信号特征,并使用指数平滑算法对五个数据类别进行平滑处理以预测轴承的RUL。现有的关于轴承的研究大多集中在研究转速、载荷及模拟轴承的内外圈故障情况等因素对其应力大小或温度分布的影响,较少地涉及到关于轴承在正常使用条件下的疲劳寿命这一方面。
本文针对某电动汽车涡旋压缩机动盘轴承出现疲劳损坏概率较高的问题,采用ANSYS/Workbench中的显示动力学模块LS-DYNA结合疲劳寿命分析软件nCode Designlife,根据Miner线性累积损伤理论,对涡旋压缩机动盘轴承在3种不同载荷以及3种转速工况下的疲劳寿命进行分析,并在不同工况下对压缩机进行加速寿命台架试验,记录在相应工况下压缩机动盘轴承发生损坏的时间以验证其合理性。本文研究内容从压缩机使用过程中最容易发生失效的动盘轴承入手,为涡旋压缩机使用寿命预测提供了一种新思路,在工程上对的涡旋压缩机使用寿命的开发具有一定的参考意义。
2. 材料与方法
涡旋压缩机是由转子驱动曲轴旋转从而促使动涡盘与静涡盘啮合,本文以某电动汽车涡旋压缩机动盘轴承为研究对象,其在曲轴上的位置如图1所示,研究主要失效零部件动盘轴承的转速与径向载荷对其疲劳寿命的影响。该动盘轴承为NJ203圆柱滚子轴承,其结构如图2所示,轴承主要尺寸参数见表1。
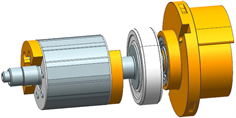
Figure 1. Rotating turbine bearing position
图1. 动盘轴承位置
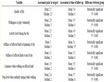
Table 1. NJ203 bearing parameters
表1. NJ203轴承参数
根据经典的轴承寿命L-P理论,当滚动体与内外圈接触时,滚动体的额定动载荷与其平均载荷之比相当于内外圈的额定动载荷与其当量动载荷之比。这近似假定滚动体的额定动载荷和当量动载荷与内外圈的额定动载荷和当量动载荷相同 [14] 。传统钢轴承的失效是由表面深度下的最大剪应力引起的,裂纹延伸至表面。本文研究的动盘轴承与动涡盘采用过盈配合的连接方式,主要承受由曲轴带来的转速载荷和动涡盘在压缩机的高压腔与静涡盘压缩冷媒啮合时所产生的径向载荷。压缩机在不同的吸排气压力工况下做功时,动盘轴承承受的径向载荷也不同。
该压缩机的额定电压为500 V,转速范围为0~6000 rpm,其中额定转速为4000 rpm,使用R134a冷媒时的标准吸排气压力为0.2/2.4 MPa [G]。本次研究分析压缩机常用的3种转速:2000/4000/6000 rpm下分别受到不同吸排气压力工况下径向负载时的动盘轴承疲劳寿命。研究步骤为:
通过结构分析计算不同吸排气压力工况下轴承受到的载荷,为仿真分析进行数据准备;
对轴承结构使用UG建模,导入ANSYS中进行网格划分与施加载荷等前处理并求解,将结果导入nCode中进行疲劳寿命的分析;
对分析工况进行台架试验,将试验结果与仿真数据进行对比,分析影响疲劳寿命的原因,验证有限元分析方法的可靠性。
3. 结果与分析
根据假设条件建立正常滚动轴承有限元模型,选取适当的单元类型和材料模型,定义接触对和约束,施加工况载荷进行求解。分析正常滚动轴承的应力和应变分布规律,得到滚动轴承的运动特性,并由轴承内部运动学关系验证仿真的正确性。
针对滚动轴承运动的特点,在仿真过程中的基本假设如下:
由于轴承的倒角对轴承内部应力分布的影响很小,可以忽略不计,为减少模型的计算量,不包括倒角与边棱;
由于轴承的塑性变形很小,所以不考虑材料非线性,假设轴承滚动体、内外圈均为线性弹性材料。
各轴承单元的失效形式为滚动疲劳失效,不考虑磨损和摩擦腐蚀。
3.1. 受力分析
涡旋压缩机主要由电机驱动曲轴转动,曲轴上的偏心轴使位于压缩机高压腔的动涡盘与静涡盘进行啮合,压缩冷媒做功从而达到制冷的效果。由动涡盘、轴承、偏心滑套组成的动盘组件受力情况如图3所示。
动盘组件的受力平衡方程,对X方向:
(1)
对Y方向:
(2)
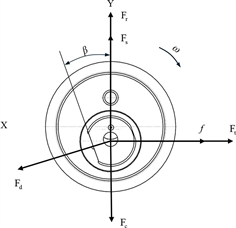
Figure 3. Direction of force on the rotating turbine assembly
图3. 动盘组件受力方向
(3)
(4)
当压缩机的转速、压力工况确定后,即可算得气体力与离心力,进而可算得曲轴偏心销对动盘组件的作用力以及涡盘啮合的密封力。再对图4所示偏心滑套进行单独受力分析:
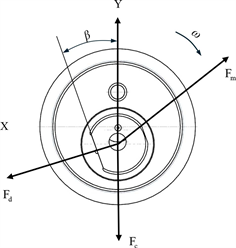
Figure 4. Direction of force on the eccentric sleeve
图4. 偏心滑套受力方向
偏心滑套的受力平衡方程:
(5)
(6)
(7)
(8)
(9)
由上式可算得偏心滑套对动盘轴承的作用力
。
式中:
为切向气体力,f为动盘背面与耐磨垫片之间摩擦力,
为曲轴偏心销对滑套的作用力,
为曲轴的推力角,
为涡盘侧壁啮合的径向密封力,其中涡盘啮合的设计要求为
,
为径向气体力,
为轴向气体力,
为吸气压力,
为动盘背面承受吸气压力区域的面积,
为动盘组件离心力,
为动盘组件质量,
为角速度,
为曲轴偏心距,
为动盘轴承对滑套的作用力,
为偏心滑套离心力,
为偏心滑套质量,
为动盘轴所承受的作用力。
3.2. 仿真分析
在UG中建立轴承的三维模型。随后将模型导入ANSYS Workbench中,首先设置轴承的材料属性,其中保持架为复合材料树脂聚酰胺,密度1140 Kg/m3,弹性模量1.62 GPa,泊松比0.41;内外圈以及滚子的材料为GCr15轴承钢,密度7830 Kg/m3,弹性模量206 GPa,泊松比0.3。
3.2.1. 网格划分
使用workbench对模型进行网格划分,选用SOLID164单元。为解决实体单元只有平动自由度而无转动自由度的问题,在内圈内表面增加一层壳单元与内圈实体单元共节点,定义为刚性面,并将其设置为SHELL163单元。有限元模型如图5所示,节点数为60,787个,单元数为45,624个。
3.2.2. 边界条件
LS-DYNA的接触摩擦基于库仑公式,摩擦因数为:
(10)
式中:
为动摩擦系数,
为静摩擦系数,DC为指数衰减系数,取值为0.00001,
为接触面间的相对速度,根据接触情况由程序自动计算得到。
动盘轴承在工作时,外圈被固定在动涡盘上,内圈固定在曲轴上随轴进行偏心运动,内外圈均为过盈配合。滚子分别与内圈滚道、外圈滚道以及保持架之间有共三对接触,选用自动面–面接触类型,定义每个滚动体表面为接触面,内圈外滚道、外圈内滚道和保持架兜孔前、后两面为目标面,在不考虑润滑的情况下,为真实模拟滚子与内外圈及保持架之间的接触关系,设置动、静摩擦系数如表2所示。
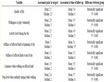
Table 2. Coefficient of friction between contacts
表2. 各接触之间摩擦系数
由公式计算得出压缩机在额定、标准和极限吸排气压力工况下的径向载荷分别为1000/1800/2300 N。在LS-DYNA模块中对外圈外表面进行全约束,设置径向载荷作用在内圈内表面的下半圆面上,对轴承分别施加不同的转速,作用在内圈内表面刚性面上。
3.2.3. 仿真结果分析
轴承运转过程中,滚动体与各组件之间存在着高度非线性接触行为。将模型提交LS-DYNA求解器求解计算。图6列举了在1000 N径向载荷下不同转速工况的等效应力云图,结果表明4000 rpm和6000 rpm下的最大等效应力大小分别为216.15 MPa和371.24 MPa,分别出现在滚子与内外圈接触区域,承载区的滚动体的应力明显大于非承载区滚动体的应力,应力最大值出现在接触表面以下一定深度区域处,并逐渐向外衰减,这与实际轴承故障优先滚子发生损坏情况一致。赫兹接触理论认为:轴承的椭圆形接触区域存在压应力;压应力的值沿曲面的轴向和法线方向变化,并且最大应力出现在接触区域一定深度处 [15] 。因此,本文的仿真结果与赫兹接触理论基本一致。
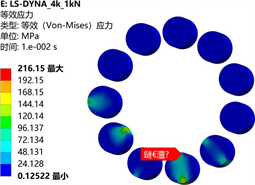
(a) 4000 rpm_1kN轴承整体等效应力云图 (b) 4000 rpm_1kN滚子等效应力最大值云图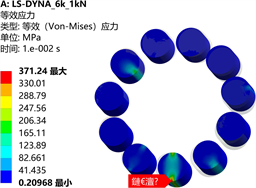
(c) 6000 rpm_1kN轴承整体等效应力云图 (d) 6000 rpm_1kN滚子等效应力最大值云图
Figure 6. Equivalent force maps at different rotational speeds
图6. 不同转速下等效应力云图
在nCode Designlife中创建如图7所示的分析流程框图,分别设置内外圈和滚子以及保持架的材料映射为GCr15和树脂聚酰胺,同时根据轴承表面处理方式和加工工艺标准对其平均应力采用Goodman法修正。轴承的疲劳类型属于高周疲劳,故采用名义应力分析法(S-N曲线法)进行求解。将求解得到的分析文件导入进行疲劳寿命分析,得到累积损伤云图和疲劳寿命云图如图8所示。
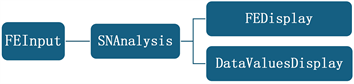
Figure 7. Fatigue life analysis process
图7. 疲劳寿命分析流程
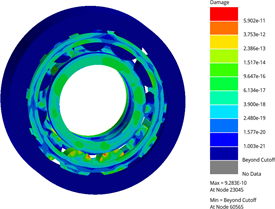
(a) (b)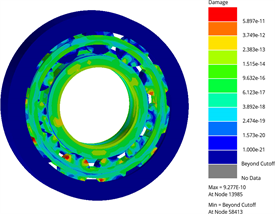
(c) (d)
Figure 8. Fatigue life and damage cloud at different rotational speeds
图8. 不同转速下疲劳寿命及损伤云图
仿真结果表明,损伤集中部位主要发生在轴承承载区,非承载区的损伤程度较小,各部件的疲劳寿命结果与之相应,最危险点位于承载区滚子与内外圈接触区域处,4000 rpm和6000 rpm时分别为1.119e9和1.077e9次循环,换算成时间分别为4662.5 h和2994.4 h。其他工况下的疲劳寿命计算结果如表3和图9所示。
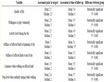
Table 3. Fatigue life simulation results for each condition
表3. 各工况疲劳寿命仿真结果
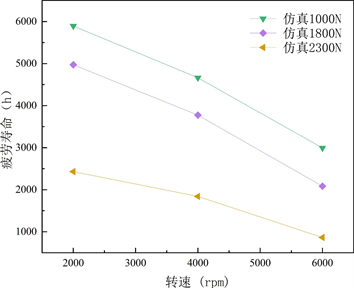
Figure 9. Line graph of fatigue life simulation results for each condition
图9. 各工况疲劳寿命仿真结果折线图
动盘轴承的疲劳寿命随着转速与径向载荷的下降整体呈下降趋势,但并不是简单的线性关系,在径向载荷上升到2300 N的极限工况下,疲劳寿命的下降尤为明显,在额定转速4000 rpm工况下,1800 N径向载荷下动盘轴承的疲劳寿命比1000 N工况下降了19.5%,而2300 N径向载荷工况下其疲劳寿命比1800 N工况下下降了50.9%;不同转速区域疲劳寿命的下降速度也存在一定的差异,在4000~6000 rpm区域疲劳寿命的下降速度高于2000~4000 rpm区域,在径向载荷为额定值1000 N时,4000 rpm转速工况下的疲劳寿命比2000 rpm工况下减少了20.8%,而6000 rpm转速下,对比4000 rpm工况其下降比例为35.8%,这说明动盘轴承在恶劣工况下的疲劳寿命可能会小于预期值。
4. 试验分析
对不同工况下的压缩机进行台架试验如图10所示。在额定电压下,根据不同工况对试验压缩机进行分组,分别施加不同大小的转速和径向载荷,调整吸排气压力对动盘轴承施加1000/1800/2300 N的径向载荷,并对压缩机充注足量的润滑油和冷媒后,由启动转速缓慢升至2000/4000/6000 rpm后进行连续耐久加速试验。
试验过程中若动盘轴承出现失效情况,贴附于壳体上的加速度传感器会发出警报,且通常伴随有高速转动下金属撞击的异响。试验结束后记录每组试验完成时所花时间如表4所示,对试验压缩机解体发现每台压缩机的动盘轴承均出现不同程度的疲劳磨损情况如图11所示。
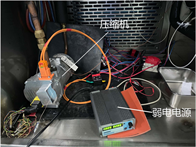
Figure 10. Compressor continuous endurance bench test
图10. 压缩机连续耐久台架试验
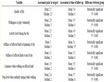
Table 4. Fatigue life test results for each condition
表4. 各工况疲劳寿命试验结果
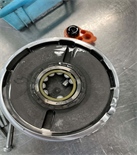
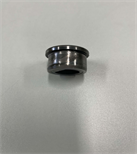
(a) (b) (c)
Figure 11. Bearing outer ring, inner ring, roller fatigue damage
图11. 轴承外圈、内圈、滚子疲劳损伤
试验结果表明,转速和径向载荷的增大对动盘轴承疲劳寿命均有明显的降低作用。其中,在转速2000 rpm径向载荷1000 N工况下动盘轴承的疲劳寿命低于预期,这是由于轴承工作条件复杂,存在因装配误差或清洁度等问题出现影响疲劳寿命的情况,试验结束解体后发现该轴承滚子出现严重的侧移导致的变形如图12,属于偶然误差,不计入疲劳寿命统计之内。

Figure 12. Failure of rollers with severe deformation
图12. 滚子严重变形失效
将仿真分析结果与试验结果进行对比,如表5所示。
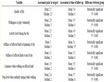
Table 5. Comparison of fatigue life test and simulation results under various operating conditions
表5. 各工况下疲劳寿命试验与仿真结果对比
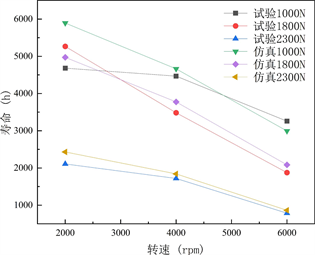
Figure 13. Comparison of fatigue life simulation and test results
图13. 疲劳寿命仿真与试验结果对比
对比结果表明,转速的提升与径向载荷的增加对动盘轴承疲劳寿命的下降均具有较大的影响,因同一批轴承在装配误差、清洁度等方面均可能存在差异,本文所提出的动盘轴承疲劳寿命仿真方法与实际试验所测值除去误差后,平均绝对值误差为8.7%,结果对比如图13所示,在一定程度上能较好地反映动轴承的疲劳寿命。
5. 结论
本文通过对某电动汽车涡旋压缩机的转子结构进行分析,计算其动盘轴承在不同工况下的径向载荷,并使用UG对动盘轴承进行建模,联合WORKBENCH/LS-DYNA和nCode Designlife对不同工况下的轴承进行疲劳仿真分析,得到该轴承的应力分布、损伤情况和寿命分布。并对其进行试验验证,具体结论如下:
动盘轴承转速的增加对疲劳寿命的影响呈线性下降的趋势,但并非是简单的线性关系,在不同转速区间内其影响程度不同,转速增长在高转速区间相比低转速区间对疲劳寿命下降的影响更大;
动盘轴承径向载荷的增加对疲劳寿命的影响大于转速,在相同转速下,径向载荷的增大会显著降低动盘轴承的疲劳寿命,在压缩机的设计阶段应该以吸排气压力的大小来预估其正常使用寿命;
动盘轴承的工作条件复杂,除去疲劳失效外还有因装配误差导致的滚子偏移挤压脱落以及润滑条件不足等意外情况,本文所提出的疲劳寿命计算方法在额定转速下的误差小于其它转速,整体绝对值平均误差在8.7%左右,符合疲劳寿命研究的误差要求。