1. 引言
车辆的安全性关键在于制动器的性能,常见的制动器类型有盘式制动器和鼓式制动器。盘式制动器具有结构简单、安装方便、散热效果好等优点,在汽车中广泛使用 [1] 。
研究人员对制动器进行了大量研究,包括制动盘和摩擦片的接触压力分析、热传导、温度场变化、热应力等方面。黄健萌在数值模拟的基础上,利用三维非稳态模型进行制动盘和摩擦片的接触压力分析,得到制动盘的形变量与压力的分布有关的结论,同时提出摩擦力,热应力变形之间存在着热力耦合现象 [2] 。吕振华提出制动盘的制动过程是非线性的过程,因此他使用间接耦合的方法分别求解制动盘的制动过程,分别分析了摩擦产生热量的热传导、温度场的变化及热应力的变化,又对制动盘和摩擦片之间的热量分配进行分析,将三者相互迭代计算进行耦合分析 [3] 。李亮针对制动器在制动时产生的热量问题,建立重复制动的分析模型,对制动过程中的热量分配和散失进行分析,考虑热传导、热辐射和对流换热系数等因素,最终计算求得制动器的瞬态温度场,并与实验进行对比分析 [4] 。鲁国富建立了三维制动盘瞬态温度模型,对紧急制动工况进行分析,分析了温度场和热应力进行分析 [5] 。韩建荣提出热源输出的方法进行计算温度场,同时用实验加以验证 [5] 。朱爱强对不同材料的制动盘和摩擦片进行耦合分析 [6] 。司杨建立了非线性热力耦合模型,分析了制动盘的温度场分布,接触压力场分布以及薄厚差的影响 [7] 。孟德建建立了三维瞬态热力耦合有限元模型,利用模型仿真和台架试验的验证,得出热力耦合特征的影响 [8] 。曲杰和苏海赋等人利用代理模型的设计方法,对通风盘式制动器结构进行优化 [9] 。潘公宇利用Insight软件,对通风盘式制动器进行仿真分析和进一步的结构优化 [10] 。浙江大学许增辉利用Solidworks、ABAQUS软件,建立盘式制动器热力耦合有限元模型,分析热力耦合特性,同时以台架试验进行试验验证,最后对盘式制动器进行结构参数的优化 [11] 。
目前的研究还未深入分析制动盘内部的热力耦合特性。因此,本文作者考虑了制动温度变化对材料参数和摩擦因数的影响,对不同工况下的制动器进行了详细分析,得出了应力、温度分布等规律,并进行了热力耦合分析,以提供更准确的计算结果和实际制动情况的参考。这些研究将为制动盘的设计和优化提供理论支持。
2. 建立三维模型
为了进行盘式制动器的热力耦合分析,首先需要建立其三维模型。本文采用ABAQUS建模模块建立了该模型。本文采用了简化模型。简化模型去除了对结构力学和热力学计算影响较小的零部件,以减少模型的复杂程度和网格划分的复杂性,从而减少了仿真计算所需的节点数和计算时间 [12] 。
建模简化条件如下:
1) 模型只包含制动盘和摩擦片,忽略其他部分如挡板、轮毂、制动钳及其连接结构。
2) 忽略细小工艺,如倒角、凹槽、螺孔。
3) 在热力耦合分析中,只保留主要受力和受热的面。
建立的模型如图1所示,其中两块摩擦片位于摩擦盘的上下两侧。制动盘的上下两侧分别有光滑的接触盘表面,并且中间有36根散热筋。这些散热筋的长度为38 mm,宽度为8 mm,厚度为15 mm,夹角为10˚。
模型结构参数如下表1:
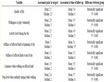
Table 1. Structural parameters of the brake disc and brake pads
表1. 制动盘和摩擦片结构参数
3. 盘式制动器热力耦合模型构建
3.1. 模型条件假设
热力耦合是一种复杂的过程,涉及制动盘和摩擦片之间的热量传递和对流换热 [13] 。制动过程中产生的热量主要源于制动盘和摩擦片之间的摩擦生热,以及摩擦片的微小形变和材料降解。这些热量通过热传导和热对流向周围环境传递 [14] 。研究热力耦合需要考虑摩擦生热理论、接触理论和传热理论。制动过程中,摩擦产生的热量主要由制动盘和摩擦片之间的相对运动引起。制动盘和摩擦片在接触区域发生摩擦,产生摩擦生热。此外,摩擦片在受压力和温度作用下发生微小形变,可能发生撕裂和粘结,导致制动盘表面微弱形变 [15] 。摩擦片的材料属性也会导致在一定温度下发生材料降解,产生一部分热量。热力耦合现象是非线性的力学问题,涉及材料的塑性变形和结构变化。制动盘和摩擦片在接触区域的温度和压力随时间改变,导致接触面积、接触状态和相对位置都在不断变化 [16] 。制动盘和摩擦片之间的接触条件是非线性的,会随时间变化。热量的传递方式包括热传导和热对流。热传导是最主要的传热方式,可以发生在物体内部或物体之间 [17] 。热对流是热量通过介质的流动传递的方式,可以发生在气体和液体介质中。在研究盘式制动器的热力耦合过程中,通常会考虑热传导和热对流这两种主要的热传递方式,而热辐射的作用相对较小,可以在简化模型时忽略。
为了模拟实际的制动工况并确保计算精度和计算效率,在采用热力耦合方法时,我们做出以下假设 [18] :
1) 制动时摩擦片受力均匀分布。
2) 材料被假设为各向同性的弹性材料,在制动过程中动能完全转化为热能。
3) 制动过程只考虑热对流和热传导,而忽略热辐射的影响。
4) 在制动过程中不考虑车轮抱死的情况。
5) 制动接触面被假设为理想平面,而初始温度T0为20℃。
3.2. 耦合模型理论计算
根据热传导理论,对于制动系统,得到柱坐标系下三维瞬态热传导微分方程 [19] :
(1)
式中:
为制动盘导热系数;
为制动盘密度;
为制动盘比热容;
为制动盘瞬态温度;
、
分别为径向坐标和周向坐标;
为制动时间;
为解域。
该微分方程主要描述某个区域内的温度随时间的特点,有限元计算的初始条件和边界条件如下 [20] :
(2)
(3)
(4)
(5)
(6)
(7)
(8)
式中:
为环境温度;
为圆盘吸收的热流密度;
为边界面上的换热系数;
为边界求解域;
为面外法向方向余弦;
为柱坐标下Z向坐标。
汽车的制动过程本质上是将汽车制动系统的动能和势能通过制动盘与摩擦片的相互作用转化为热能的过程。制动盘与摩擦片之间存在热流输入和自然传热,其中热流密度分别为 [21] :
(9)
式中:
为不同时刻的摩擦因数;
为接触压力;
为制动盘与摩擦片相对滑动速度;
为制动盘热流分派系数;
为摩擦片热流分配系数。
其中
和
满足以下关系 [22] :
(10)
(11)
式中:
为密度;
为比热容;
为导热系数;下标
、
表示制动盘和摩擦片。
由温度引起的线应变为 [23]
(12)
在存在初始应变,由温度引起的应力计算公式为 [3]
(13)
(14)
式中:
为应力矩阵;
为材料弹性矩阵;
为热变形引起的热应变。
圆盘的换热主要是对流换热,圆盘表面的对流换热系数经验计算公式如下 [24] :
(15)
式中:
为雷诺数;
为空气黏度;
为空气传热系数;
为空气密度;
为制动盘转速;
为制动盘外径。
3.3. ABAQUS 模型预处理与分析
为了保证计算效率和收敛性,并提高网格划分的质量,在ABAQUS中对制动盘模型进行了网格划分。 [14] 为了减少对热力耦合影响较小的特征,我们将制动盘切分为多个小模块。根据表2的材料参数属性设置材料参数,并使用ABAQUS软件进行有限元分析。该软件通过对计算模型的单元节点进行计算,并求解离散域方程,得出节点处的变量近似值。为了更好地求解单元,需要对模型进行网格划分,将其转换为网格化有限元模型。对于盘式制动器的复杂结构,合理的网格划分可以减轻计算负担。本研究采用ABAQUS自带的自适应网格划分功能,以满足分析要求并精简网格数量。总共使用了23,864个节点和14,756个线性六面体网格单元(类型为C3D8RT),划分的网格如图2所示。以上是对网格划分的描述,通过这种方式可以在保证计算效率和收敛性的同时,减少对热力耦合影响较小特征的计算。
有限元模型在模拟刹车制动过程时,需要进行一些假设以满足仿真计算的要求。为了尽可能地模拟真实的刹车过程,模型在初始状态下假设了制动盘和摩擦衬之间存在一定的间隙,并在摩擦片上施加均匀的力。因此,仿真过程至少需要两个载荷步来计算制动过程:第一步是制动盘施加一定的转速,摩擦片受到均匀力的作用,向制动盘移动,消除间隙,使制动盘和摩擦片接触;第二步是制动盘和摩擦片发生接触压力,产生摩擦,导致制动盘转速降低,直至停止运动。为了有效进行仿真计算并得出结果,建模过程中需要做出以下假设:
1) 使用的材料具有各向同性,且密度均匀。
2) 材料的物理参数是常数,并且不随温度变化而变化。
3) 摩擦片受到的压力均匀地施加在摩擦片表面,并保持恒定。
4) 制动时前后轮都处于抱死状态,并且制动路面是良好的沥青或混凝土路面。
5) 制动过程中不存在制动盘和摩擦片之间的磨损。
6) 制动盘和摩擦片之间的接触平面是理想平面,不存在凸峰,属于弹性接触。
这些假设有助于进行有效的仿真计算,并得出相应的结果。
制动盘和摩擦片材料和物理属性如下:
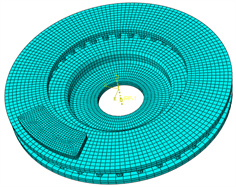
Figure 2. Disc brake meshing diagram
图2. 盘式制动器网格划分图
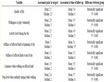
Table 2. Disc brake component material properties
表2. 盘式制动器部件材料属性
3.4. 模型主要参数
根据实际车辆运行状况,我们选择了500、1000、1500 r/min作为制动仿真的初始速度进行分析。为满足制动需求,大多数车辆都装配了带有自带空气泵的气刹装置。制动系统可以通过加压装置利用空气泵增加制动压力。我们选取了制动压力为5、6、7 MPa进行制动仿真分析 [25] 。
为了确保计算收敛和提高计算效率,我们采用了温度–位移耦合的方法建立了分析步骤。紧急制动时间被设定为5秒,计算初始步长为0.005,最小步长为5 × 10−10,最大步长为0.1。热流密度和换热系数分别使用公式(9)和公式(15)进行计算。以上是制动仿真分析的一些设置,通过这些设置可以确保计算的收敛性并提高计算效率。
4. 热力耦合仿真与结果分析
4.1. 制动转速
在制动压力为6 MPa的情况下,对于紧急制动转速分别为500、1000、1500 r/min的情况,进行了为期5秒的仿真制动。图3和图4展示了制动盘温度和应力的变化曲线。
制动盘表面温度的不均匀分布会引起应力的不均匀。短时间内温度的迅速上升会对制动效能产生影响。因此,需要对制动盘的温度场进行分析。可以选择有限元模型中某个节点的瞬时温度和温度分布规律进行详细分析。
从图3可以观察到,在制动过程的初期,温度迅速上升,呈陡峭的趋势,与整体温度图的上升变化相一致。随后,温度上升速度减缓,变化较小,并最终开始下降。温度的变化呈现锯齿形状,即温度的上升和下降交替出现。最初,温度显示出上升–下降–上升的齿形变化。随着时间的推移,锯齿形之间的间隔逐渐增大。这是因为开始时,制动盘的转速较高,制动盘和摩擦片之间的摩擦时间较短,导致制动盘和摩擦盘产生的温度无法及时散失,温度持续上升,从而导致锯齿形之间的间隔较小。随着制动盘转速的降低,制动盘和摩擦片之间的摩擦时间增加,持续时间相对延长,因此锯齿形之间的间隔增大。锯齿齿顶和齿谷温差的增加是由于相对摩擦时间的增加,导致对流换热时间的增加,从而热量散失较多,使得温度变化的幅度逐渐增大。在制动过程中,超过0.15秒后,三条曲线的趋势明显不同,不同的制动转速对制动盘整体温度产生较大影响。制动转速为500、1000、1500 r/min时,达到最高温度的时间分别为3.55、3.67、3.93秒,最高温度分别为185.74℃、303.80℃、363.71℃。由此可见,制动转速不同,达到最高温度所需的时间也不同,转速越大,达到最高温度所需时间越长。
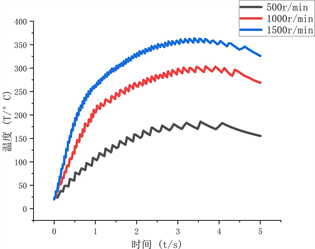
Figure 3. Temperature curves at different braking speed
图3. 不同制动转速下温度随时间变化曲线
应力是热力耦合过程中的另一个重要物理量。当局部应力过大时,会导致制动盘在高温和高应力区域出现热裂纹。热裂纹是导致制动效能下降的主要原因之一,在制动过程中属于高危情况。因此,需要进一步分析制动盘整体的应力情况。
图4展示了不同制动转速下应力随时间变化的曲线,与图3中制动盘温度变化的趋势相似。开始制动时,应力和温度均迅速上升,呈陡峭的斜坡状,但应力的上升速度比温度更快。随后,应力的上升逐渐减缓,达到最大值后开始缓慢下降,这与温度场的变化趋势相对应。这说明温度的上升导致了局部应力分布的不均匀性,从而影响应力的变化幅度,而应力变化又使得局部温度发生改变,形成了应力和温度相互影响的关系。总体上,图4中的应力变化呈现较小的上下波动,相对于温度的波动来说较小。这是因为应力在物体中的传递速度比温度更快,所以应力的变化在一个周期内(制动盘转动一圈)相对较平稳。然而,“锯齿形”的变化是由于制动盘转动和温度变化之间的交替影响所产生的变化规律。
在静力分析步内施加压力,三条应力曲线迅速上升,1秒后增长速度减缓,并逐渐上升到最高点。当制动初速度为500、1000和1500 r/min时,达到最高应力的时间分别为2.38、1.95和1.95秒,最大应力值分别为202.10、343.76和400.08 MPa。根据应力和温度达到最高点的时间对比,可以观察到温度的最大值总体上滞后于应力的最大值,这表明应力和温度之间存在着耦合特性,符合公式(12)和(13)中应力与温度呈线性变化的关系。然而,该公式仅描述了温度导致的应力变化,是单向的。本文采用了温度–位移耦合的方法,即应力和温度相互作用,因此应力变化曲线与温度变化曲线并不完全相同。

Figure 4. Stress curves at different braking speed
图4. 不同制动转速下应力随时间变化曲线
4.2. 制动压力
当制动转速为1000 r/min,制动比压分别为5、6、7 MPa时,进行5s的仿真制动。图5和图6展示了制动盘温度和应力的变化曲线。
根据图5,可以观察到随着制动压力的增加,制动盘的温度上升速度更快,最终温度也更高。随着压力增加,制动盘表面的温度也随之增加。这是因为随着压力增大,外部载荷引起的机械应力增加,导致更多的热量产生和能量转换,而散热效果较小,因此温度持续上升。同时,由于热传导和与空气对流的影响,温度会向周围区域扩散,形成明显的温度梯度。随着制动压力增大,制动盘的温度梯度也会迅速增大,导致盘面产生局部高温区域。这不均匀的温度分布会影响制动器的工作性能。此外,随着制动压力增大,达到最高温度所需的时间也缩短。这表明在短时间内,摩擦所产生的热量远远超过对流换热的作用,符合式(9)中制动压力增大导致热流输入增大的关系。具体而言,当制动压力分别为5、6、7 MPa时,制动盘的最高温度分别为278.40℃、303.80℃、323.63℃。可以发现,制动压力对制动器的最高温度有着巨大影响,制动压力越大,制动盘失效的概率也越高。
图6展示了不同制动压力下制动器等效应力随时间变化的曲线。可以观察到,制动压力增加会导致制动器的等效应力增大。具体而言,当制动压力分别为5、6、7 MPa时,制动器的最大应力分别为315.29、343.76、358.13 MPa。可以发现,制动压力为7 MPa时,最大应力比5 MPa时高出42.84 MPa。这表明制动压力增加对应力的影响非常显著。
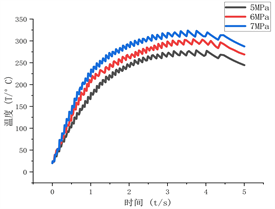
Figure 5. Temperature curves at different pressure
图5. 不同制动压力下温度随时间变化曲线
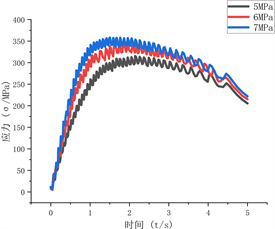
Figure 6. Stress curves at different pressure
图6. 不同制动压力下应力随时间变化曲线
4.3. 制动盘温度与应力分析
在制动转速为1000 r/min,制动压力为6 MPa的情况下,对制动盘的制动特性进行了分析,并得到了不同制动时刻的温度与应力的云图,如图7和图8所示。
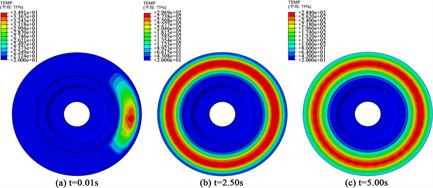
Figure 7. Temperature field distribution at different time
图7. 不同时刻温度云图
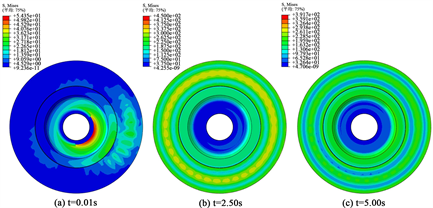
Figure 8. Stress field distribution at different time
图8. 不同时刻应力云图
制动盘表面温度的不均匀分布会引起应力的不均匀。短时间内温度的迅速上升会对制动效能产生影响。因此,需要对制动盘的温度场进行分析。可以选择有限元模型中某个节点的瞬时温度和温度分布规律进行详细分析。
根据图7,不同时刻制动盘的温度云图显示温度的变化幅度相对较小,且变化不明显。制动盘的温度受到传热和散热的影响,导致摩擦区域的温度升高较快,而边缘附近的区域温度上升较慢。散热筋式制动盘在轴向方向上的散热速度较快,相对于径向方向上的传热速度更快,这导致向两侧的热量传递较小,使得温度云图上的变化不太明显。在不同时刻,制动盘的温度分布是非轴对称的,尤其是在制动压力施加完成后的初始阶段和摩擦区域形成环状高温区的阶段。
图8展示了不同时刻制动盘的应力云图。应力主要集中在制动盘和摩擦片接触面区域。随着制动盘转动经历的摩擦次数增加,应力迅速增加。在制动前期,由于转速较快,摩擦次数较多,导致应力迅速上升。随着持续摩擦,制动盘受到的应力不断增加。在制动过程中,制动盘的温度上升趋势陡峭,导致制动盘微弱变形,使得应力不均匀分布,产生较高的应力。最高应力达到后,制动盘温度上升缓慢,应力维持在较高水平,并且受散热条件影响,应力会出现微弱的上下波动。随后,制动盘转速降低,接触摩擦次数减少,对流换热时间增加,温度开始下降,最大应力明显降低,直到制动盘停止转动。应力云图显示出应力的变化趋势与温度的变化趋势基本一致。最大应力首先迅速增大,然后在高位区域微弱地上下波动,最后开始逐步下降。应力沿着接触面的摩擦半径范围向转动方向传递,并在制动盘上形成间隔式的高应力和低应力分布。高应力区域主要位于制动盘内部的散热筋上,这也说明了在没有散热筋的区域温度相对较低,局部热应力较小。
综上所述,温度场和应力场在制动过程中相互影响,温度的分布情况对应着应力的分布情况。
5. 结语
在制动器的制动过程中,如果温度升高过快或最高温度过高,会导致热应力过大。这会使制动盘表面发生热变形,并可能引发热裂纹,从而降低安全性能,甚至引发交通事故。随着对汽车安全性能要求的不断提高,热力耦合研究的重要性也日益增加。本文对制动转速为500、1000、1500 r/min以及制动压力为5、6、7 MPa的制动工况进行分析,获取应力、温度等的分布规律,并对热力耦合进行分析。
在制动过程中,总体温度变化呈现非线性关系。温度先上升,然后在中间阶段出现稳定波动,最后下降。波动的幅度大小不一,并且上升阶段呈现出锯齿形状。这是因为制动时接触区域不断更换,导致温度周期性地升高和降低。高温主要分布在制动盘和摩擦片接触表面的中心线附近,然后沿径向、轴向方向传播,温度逐渐降低。
1) 在紧急制动过程中,盘式制动器的温度和应力的最大值与制动转速和制动压力成正相关。制动转速对温度和应力的最大值的影响比制动压力更加明显。
2) 制动盘温度和等效应力在圆周上都呈现环带状分布,并且二者具有一致性。温度的最高值滞后于等效应力的最高值,这表明在制动盘的热力耦合过程中,温度和应力相互耦合。
3) 摩擦接触挤压区域会产生大量热量,但热传导具有延迟性,导致温度高的区域更靠近摩擦区域。