摘要: 托板自锁螺母的高效合理安装对提高箭载仪器支架的装配质量和效率起决定性作用。针对当前箭载仪器支架托板螺母一次装配合格率低的问题,本文采用QC质量工具对其装配过程开展质量控制。基于分层筛选法发掘关键故障现象,从人、机、料、法、环五个方面深入分析,找到产生关键故障的两个要因;遵循5W1H的原则制定对策,通过试验改进定位工具、优化防护方法等,使支架铆接托板螺母一次合格率提高到99%,为后续类似结构铆接提供了借鉴依据和参考经验。
Abstract:
The efficient and reasonable installation of the self-locking nut of the support plate plays a decisive role in improving the assembly quality and efficiency of the rocket-borne instrument bracket. In this paper, in order to solve the current problem of low pass rate of one-time assembly of the rocket-borne instrument bracket support plate nut, QC quality tools are used to carry out quality control on the assembly process. Based on the hierarchical screening method, key fault phenomena were discovered, and the two main causes of key faults were found through in-depth analysis from the five aspects of human, machine, material, method, and environment. Countermeasures were formulated following the 5W1H principle, and through experiments, positioning tools were improved and protection methods were optimized, the one-time pass rate of bracket riveting support plate nuts was increased to 99%, providing a reference basis and reference experience for subsequent riveting of similar structures.
1. 引言
运载火箭舱段内表面需安装大量的仪器支架,主要是为各类仪器、仪表的安装提供载体和支撑。托板自锁螺母因其具有良好的防松效果、结构简单、附加重量轻、强度高等特点,被广泛应用于航空航天领域 [1] ,尤其在箭载仪器支架的组合中被大量应用。以现役运载火箭为例,托板螺母在舱内仪器支架安装面上广泛应用,占舱内仪器支架组合工作量的80%以上,其装配质量直接影响箭载仪器安装的协调性和连接可靠性,进而影响产品的质量和使用寿命,且对产品的装配周期有重要影响。当前,箭载仪器支架上托板螺母主要采用手工铆接的方式装配,存在一次合格率低的问题。经初步统计,某型运载火箭共涉及500多种规格仪器支架,每年需组合6000余件。目前,支架铆接托板螺母铆接一次合格率仅为51%,需再次返修后才能合格交付,影响了任务交付节点,制约着型号产品的高质量、高效率、高可靠性研制。
QC小组活动是一种在工业领域广泛使用的质量控制方法,其在缩短周期、节约成本和提高质量等方面具有明显优势 [2] 。尹璐等 [3] 通过QC方法,分析了各环节影响效率的关键因素,通过改进照明、调整工序及制作专用工具等措施,明显提升了人工清理效率。王彦卿等 [4] 开展了QC活动,将钢套一次镀锌合格率由49%提高到97%,缩短了生产周期,每年为公司节约20余万元;屈明亮等 [5] 使用QC工具,将定位螺柱合格率由0提升到86.67%;刘扬喜等 [6] 以QC小组形式强化技术交底,提高了钢柱垂直度合格率。
本文以箭载仪器支架装配合格率提升为目的,以支架上托板自锁螺母的铆接为例,运用QC方法提高托板自锁螺母的装配质量,为后续类似操作提供经验。
2. 托板自锁螺母装配合格率低问题求解
2.1. 原因分析
2.1.1. 基于分层筛选法的问题分类
分层筛选法是一种把性质相同、在同条件下的数据归集在一起进行比较分析的方法 [7] 。箭载仪器支架上铆接托板螺母的检查要求有表面质量、多余物、托板螺母数量、托板螺母安装方向等。为了找出托板螺母铆接一次合格率低的原因,查阅全年托板螺母返修记录,不合格的象限有表面质量不合格、多余物问题,对问题分布情况进行分析,采用分层筛选的方法进行统计,得到各种不合格产品的统计结果,如表1所示。经统计,全年共生产支架铆接托板螺母6508件,3340件铆接后一次合格,3168件返修后合格,平均一次合格率51%;3168件返修产品中,支架表面质量问题占全部不合格品的99.5%,多余物问题占0.5%。
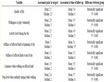
Table 1. Statistical results of non-conforming products of bracket riveting support plate nuts
表1. 支架铆接托板螺母不合格产品统计结果
对支架表面质量不合格现象进一步分析,发现表面质量不合格现象有表面划痕、铆钉孔周围压痕、装配孔周围压痕,得出托板螺母铆接一次不合格质量缺陷统计表,如表2所示。可以看出,支架表面装配孔处出现压痕的不合格现象占全部不合格品的96.7%,说明支架铆接托板螺母一次不合格的主要现象是装配孔周围压痕。
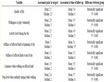
Table 2. Statistical table of surface quality non-conforming defects
表2. 表面质量不合格缺陷统计表
2.1.2. 基于鱼骨图的原因定位与分析
从人、机、料、法、环五个方面,对支架铆接托板螺母装配过程中支架表面压痕超差问题进行了分析,绘制鱼骨图,如图1所示。总结提出可能导致问题产生的5项末端原因,包括铆接水平不足、施工螺钉螺母压伤零件、支架本体装配孔周围压痕、垫纸挤压破损、铆接现场温湿度超出要求范围。
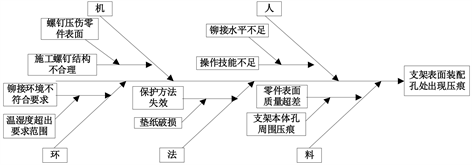
Figure 1. Cause analysis fishbone diagram
图1. 原因分析鱼骨图
针对以上5项末端因素,运用调查表逐条进行了分析以确认要因,根据每个因素特点逐个制定确认内容、确认方法及依据,分析结果见表3。经过多次分析、讨论、验证,最终确定影响托板螺母铆接一次合格率的2项要因:施工螺钉压伤零件、垫纸破损。
2.2. 对策制定及实施
根据要因按照5W1H的原则制定对策表,见表4。
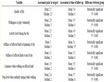
Table 4. Countermeasure implementation table
表4. 对策实施表
对策一:改进定位工具
1) 分析装配需求
支架本体上装配孔比托板螺母孔直径大,需使用定位工具保证同心,传统定位工具的螺母压在零件表面易产生压痕,需进行结构优化。
2) 自行设计制造定位工具
选择与装配孔直径相同的销钉,进一步进行适应性改造,其结构如图2所示。利用改进后的定位销钉定位托板螺母,销钉不与零件表面接触,避免了装配孔处周围压痕问题。
3) 改进定位装配方法
由于同心定位销钉无凸台,定位托板螺母时无法卡紧支架定位,故使用预制孔方式代替卡紧定位方式。预先在支架上制出托板螺母铆钉孔,再利用同心销钉保证托板螺母与支架装配孔同心,再进行铆接操作。
对策二:摸索新的保护方法
1) 制定不同保护方法试验方案
为改善垫纸保护易破损的问题,探究新的保护方法。通过调研,选取铜皮、铝垫块材料进行试验,分别制作M3、M4、M5、M6等四种保护垫,结构尺寸如图3所示。
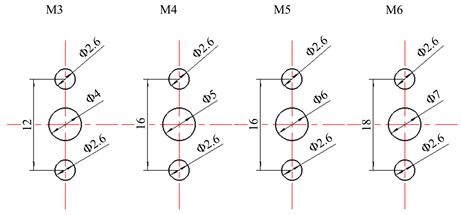
Figure 3. Protective pad structure size
图3. 保护垫结构尺寸
2) 开展铆接试验工作
分别使用铜皮、铝垫块作为保护垫,选取M3、M4、M5、M6托板螺母各10件,开展8组铆接试验,试验方案如表5所示。
3) 检查对比不同方式零件表面质量
各组铆接完成后,测量保护垫孔径,对比钻孔前后孔径变化情况,得出保护垫磨损情况;同时,检查支架表面质量是否存在压痕问题。结果如表6所示。
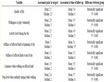
Table 6. Riveting effect inspection table
表6. 铆接效果检查表
试验结果显示,采用铜片钻孔后,铜片孔径变化范围为Φ2.60~Φ2.74,与原始孔径偏差最大达到+0.14 mm;采用铝垫钻孔后,铝垫孔径变化范围为Φ2.60~Φ2.62,与原始孔径偏差最大达到+0.02 mm。铆接后,支架表面均良好,无压痕。得出结论,铜皮较软易磨损,铆钉孔容易错位;铝垫块硬度高,便于操作,其可重复使用,故使用铝垫块保护铆接的方案。
3. 实施效果
3.1. 效果检查
对策实施后,小组成员利用同心销钉定位、铝垫片保护钻制铆钉孔定位铆接托板螺母,以验证对策的正确性及可行性。对409件支架进行了铆接托板螺母工作,检查其表面质量情况,并和活动前进行对比,如表7、图4所示。
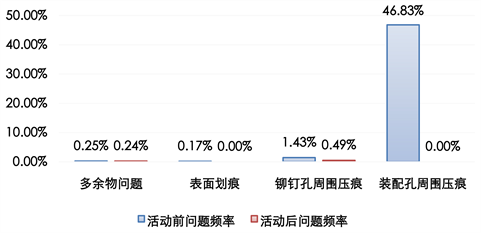
Figure 4. Diagram of the practical teaching system of automation major
图4. 自动化专业实践教学体系图
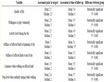
Table 7. Statistical table of quality problems of bracket riveted plate nuts
表7. 支架铆接托板螺母质量问题统计表
从表7和图4看出,对策实施后,装配孔周围压痕发生概率由46.83%下降为零,且支架表面质量问题中的表面划痕、铆钉孔周围压痕也得以大幅度下降,下降幅度分别为100%和65.78%;409件支架铆接托板螺母有质量问题有3件,问题发生率不足1%,一次合格率已达到99%,实现了目标要求。
3.2. 巩固措施
为了巩固和提高所取得的成绩,巩固期内,小组讨论并制定了以下巩固措施:
1) 同心销钉、铝垫片按自制工装管理,将使用方法落实到支架铆接托板螺母工艺规程中,提高产品质量;
2) 开展技术培训,结合实际铆接操作,使员工掌握支架铆接托板螺母工艺方法,满足车间生产需要;
3) 将措施应用到新批次支架铆接托板螺母中,充分保证产品任务节点;
4) 将此次QC小组活动经验形成纪要,可为后续QC小组活动提供参考。
通过上述巩固措施后,2023年支架铆接托板螺母9672件,其产量较2022年提升1.48倍,同时铆接质量显著提高,对比初始、目标、现状一次铆接合格率如图5所示。
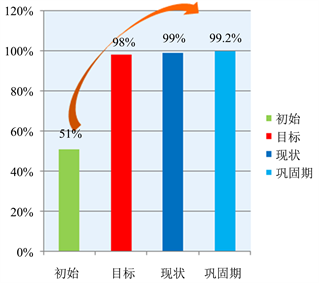
Figure 5. Comparison of pass rates during consolidation period achieved
图5. 巩固期间合格率对比实现
3.3. 效益分析
由于提高了产品的一次合格率,产品的返工、返修量明显减少,相应的费用也降低。2023年支架铆接托板螺母9672件,产品合格率从51%提升至99%,产品返修数量减少9672 × (99% − 51%) = 4642.56件,共节约返修工时约386小时。每小时工时费用150元,共减少费用57,900元。
4. 结论
在本次QC小组活动过程中,小组成员对支架铆接托板螺母过程中导致支架表面装配处压痕问题进行了调查研究,运用分层筛选、鱼骨图等质量工具分析了问题要因,制定实施了专项对策,通过应用同心销钉定位和铝垫保护的装配方案,使支架铆接托板螺母一次合格率提高到99%,有效降低了后期返修概率,节约了装配成本。QC小组在此次活动中取得了令人满意的成绩,活动成果荣获中国运载火箭技术研究院一等奖、航天质协先进QC成果,为今后同类支架的装配奠定了基础。
NOTES
*通讯作者。