1. 引言
SiC在加工制造中面临诸多挑战:SiC的硬度很大,莫氏硬度为9.5级,其化学性质稳定,不与大多数酸碱反应。因此,在SiC超精密加工中去除效率较低 [1]。为了提高加工效率并获得无损伤的表面,SiC晶片的加工制造过程需分为切割、研磨、抛光三个工艺步骤完成。研磨步骤的主要目的是去除切割的产生的刀痕及加工变质层,降低表面起伏低,改善表面粗糙度。然而,研磨后SiC表面依然存在划伤、微裂纹等缺陷,这些缺陷需要通过化学机械抛光 [1]、磁流变抛光 [2]、电化学抛光 [3] 等方法去除。
作为一种非接触式加工方式,激光加工可以有效地避免机械加工产生的划痕、应力、损伤等缺陷。目前激光抛光常见于金属材料的精密加工领域,激光束产生的能量可以使金属材料熔化,表面凸起处的熔融物向凹陷部分流动,最终达到消除表面缺陷,降低粗糙度目的 [4]。激光加工在半导体领域的应用主要集中于半导体材料的切割、开槽、光刻等,在半导体材料的抛光方面目前处于起步阶段 [5]。
Tomitaa等研究了表面粗糙度对4H-SiC飞秒激光诱导条纹结构形成的影响,在定性的基础上,对表面形貌对细条纹形成的具体影响作了简要的解释 [6]。Wang等揭示了飞秒激光工艺参数对4H-SiC硅面形貌、结构、成分的影响机理,但并未给出激光抛光后表面粗糙度结果 [7] [8]。此外,Wang等还对激光抛光后的4H-SiC进行了化学机械抛光处理 [7],考察了飞秒激光抛光后SiC的表面形貌结构对化学机械抛光的影响,研究结果表明:激光抛光后的4H-SiC碳面的化学机械抛光去除速率提升了3倍 [9]。
本研究提出采用激光抛光切割后的6H-SiC硅面,考察激光重复频率、扫描间距、脉冲能量、扫描速度、离焦距离等参数对抛光表面质量的影响,通过工艺条件的优化,获得表面平整、无划伤、无崩裂等缺陷的精细表面。
2. 实验装置与方法
本实验使用的激光抛光设备是由深圳市海目星激光智能装备股份有限公司生产的飞秒激光加工系统。该系统由立陶宛LIGHT CONVERSION公司生产的PHAROS型固体激光器(最大重复频率为75 kHz,最大功率为7.2 W)、德国SCANLAB高速扫描振镜系统、美国AEROTECH精密运动平台系统、光学系统和计算机控制系统等组成。
抛光过程使用的固定参数为:波长515 nm,脉宽290 fs,激光焦斑直径25 μm。该系统中激光器输出能量、频率可调,并可通过衰减片进一步精确控制输出能量,激光束通过远心透镜聚焦以0˚入射角垂直照射到放置于三维精密运动平台上的SiC单晶片表面。在加工过程中工作平台保持固定,通过扫描振镜实现二维平面上不同图案和路径的加工。
实验中使用的6H-SiC单晶片购买于北京天科合达半导体股份有限公司,实验之前使用酒精将碳化硅单晶片超声清洗2分钟,激光抛光后,将碳化硅在酒精溶液中超声清洗5分钟,然后利用激光共聚焦显微镜、SEM、EDX对加工后表面形貌、粗糙度、成分等进行表征。
3. 结果与讨论
3.1. SiC初始表面缺陷对抛光后表面质量的影响
激光抛光过程可归结为材料对激光的吸收和转化过程。当激光束聚焦到材料表面时,部分光能被材料吸收,其余部分被透射或反射损失。SiC表面初始状况对能量的吸收率和反射率都有影响,从而对抛光效果也有着重要影响。实验中对比了表面缺陷较多的SiC切割片及表面几乎无缺陷的SiC抛光片两种不同表面在相同激光抛光后差别。首先考察了脉冲打点的方式下两者的区别,结果如图1所示。

Figure 1. Comparison of the surface changes of cutted SiC and polished SiC after laser treatment
图1. 点扫描方式对比碳化硅切割片与抛光片激光作用后表面变化
SiC抛光片在激光作用后,中间出现熔融物(图1(a1)),烧蚀点边上均匀分布飞溅颗粒(图1(a2))。切割后的SiC在激光作用下表面颗粒较少(图1(b1)),烧蚀点上出现的不均匀凹坑及炸裂产生的缺陷。这说明,材料表面的缺陷会造成材料对激光吸收不均匀,碳化硅表面的凹坑、晶格缺陷进一步阻碍了热量的传导,加之表面晶格位错存在,最终导致原始缺陷被放大出现空洞,或者晶体表面产生崩裂。由此可见,飞秒激光抛光SiC切割片依然面临较大挑战,需对激光工艺参数进行优化以获得较高的表面质量。
3.2. 脉冲能量对抛光后表面质量的影响
研究采用面扫描的方式,设定扫描速度为235 mm/s、重复频率为15 kHz、扫描间距为20 μm,分别利用功率为15%、30%、50%、100% (激光能量分别为5.6 μJ、19.6 μJ、63.1 μJ、89.3 μJ)对SiC硅面进行面抛光,通过SEM观察抛光后表面形貌,结果如图2所示。在设定的实验条件下,抛光后表面相对较为平整,未出现严重凹坑、崩裂等缺陷。但是当能量大于19.6 μJ,表面开始出现条纹。当能量达到63.1 μJ,表面出现沟槽,条纹明显加深。面扫描加工是以线扫描搭接的方式完成的,在激光的扫描路径上由于高斯光斑能量分布由中心能量向边缘逐级递减,不可避免地会形成微沟槽。当能量较低时,激光辐照下材料发生弱烧蚀,激光对材料仅产生纳米级的影响,如熔融形成纳米颗粒,所以激光扫描区域几乎看不到沟槽起伏形貌;而当能量增加时,激光辐照下,材料会逐渐发生强烧蚀,并伴随材料飞溅,此时激光辐照引起的材料去除量增加,但由于能量处于高斯分布,使得扫描路径的光斑中心位置材料去除较多,逐步形成越来越明显的沟槽起伏形貌,即波纹结构;当能量很大时,材料气化重凝及相爆炸飞溅的颗粒较多,并会覆盖在表面,部分陷入沟槽的凹陷处,使得表面粗糙度加剧程度减缓。对四种脉冲能量下抛光后的SiC表面采用激光共聚焦显微镜测量(图3(a)),结果发现脉冲能量在19.6~63.1 μJ范围内表面粗糙度及表面起伏均缓慢增加,这与表面形貌变化一致。但是当脉冲能量从63.1 μJ增加到89.3 μJ,表面起伏突然增加,表面粗糙度变化较为温和。为了分析原因,实验中对抛光后表面形成氧化物含量进行了测定(以氧元素含量表示),结果如图3(b)所示。研究表明,能量从5.6 μJ增加到89.3 μJ过程中,氧元素含量均缓慢增加,增加率未出现明显突变现象,这说明脉冲能量从63.1 μJ增加到89.3 μJ时,突然增加的表面起伏主要是由于条纹加深引起。由此说明,表面起伏对条纹深度增加值较为敏感。
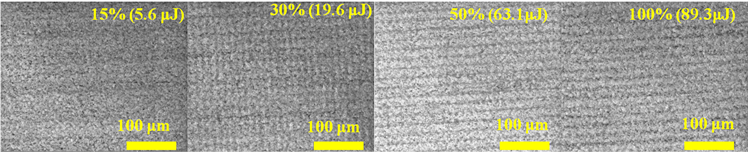
Figure 2. Surface morphology of SiC polished with different pulse energy
图2. 不同脉冲能量抛光后碳化硅表面形貌图
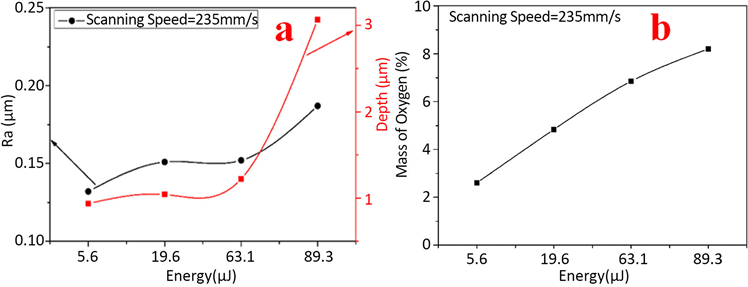
Figure 3. Ra/depth (a) and oxygen element (b) changes of SiC after polishing under different pulse energy
图3. 不同脉冲能量条件抛光后SiC表面粗糙度/起伏(a)及氧元素(b)变化
3.3. 重复频率对抛光后表面质量的影响
激光抛光过程是多脉冲作用的过程,通过研究不同重复频率等效脉冲数对烧蚀速率的影响,可反映出多脉冲累积效应对激光抛光的影响。实验采用面扫描的方式,设定扫描速度为235 mm/s、扫描间距为20 μm,分别利用功率为15%、30%、50%、100% (激光能量分别为5.6 μJ、19.6 μJ、63.1 μJ、89.3 μJ)对SiC硅面进行面抛光,考察重复频率分别为15 kHz及37.5 kHz抛光后表面缺陷情况。匹配激光的重复频率和扫描速度的方法转化为等效脉冲数用公式(1)表示为:
(1)
其中,r为焦斑半径,f为脉冲激光重复频率,v为扫描速度。本实验中,在其他参数一定的条件下,重复频率改变的实际上是等效脉冲数。37.5 kHz对应的等效脉冲数较大,在该频率下抛光后表面形貌(图4)、粗糙度(图5(a))及起伏(图5(b))明显较差。相较于重复频率15 kHz,重复频率为37.5 kHz时能量从63.1 μJ增加到89.3 μJ过程中,表面粗糙度增加明显,而表面起伏略微增加。在此能量区间,EDX分析发现重复频率为37.5 kHz抛光后氧元素含量比重复频率15 kHz抛光后氧元素含量大(图5(c)),说明有可能是表面生成的不规则氧化物,表面发生剧烈变化导致表面粗糙度增加,表明生成的不均匀氧化物对表面粗糙度影响较大。因此,重复频率15 kHz时,抛光后表面质量较高。
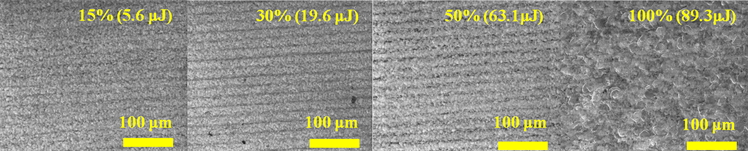
Figure 4. Surface morphology of SiC polished at 37.5 kHz with different energy
图4. 频率为37.5 kHz不同能量抛光后碳化硅表面形貌图
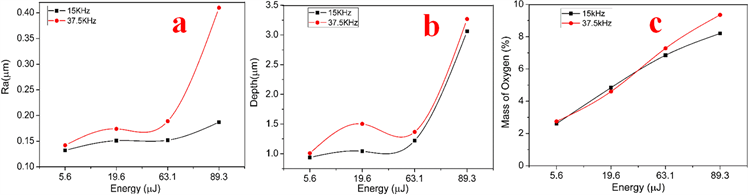
Figure 5. Ra (a), depth (b) and oxygen element change (c) of SiC after polishing with different pulse frequency
图5. 不同脉冲频率抛光后SiC表面粗糙度(a)、表面起伏(b)及氧元素度变化(c)情况
3.4. 扫描间距对抛光后表面质量的影响
采用面扫描的方式,设定扫描速度为235 mm/s、重复频率为15 kHz,功率为100% (激光能量为89.3 μJ)对SiC硅面进行面抛光,考察扫描间距分别为5 μm、10 μm、15 μm、20 μm、25 μm抛光后表面缺陷情况。从图6可以看出,随着扫描间距的降低抛光后表面条纹逐渐减少,当扫描间距小于15 μm时,表面出现块状熔融物。当扫描间距为5 μm表面条纹消失,表面出现块状熔融物。这是因为扫描间距影响了激光加工中纵向(即扫描搭接方向)的光斑重叠率,重叠率越高,SiC表面单位面积作用的能量叠加越多。而由脉冲“孵化效应”,无论是一次作用或是多次叠加,在单位面积作用的能量越大,SiC材料受激光辐照影响发生的熔融、气化、飞溅等现象程度越强。所以可以看到随着扫描间距的减少,抛光表面的熔融物逐渐增多,并由颗粒向块状转变。熔融物在表面的重凝程度主导了表面粗糙度的变化。而表面由于大量熔融物的流动、重凝堆积,使得扫描路径引起的波纹减少。此外,扫描间距越小,扫描路径搭接位置处于沟槽的波谷较低点,减弱了搭接的波纹起伏高度,融凝物更容易填满波谷,波纹减少。图7为不同扫描间距下表面粗糙度及表面起伏变化。图7表明扫描间距为15 μm时表面条纹及生成的熔融物最少,此时表面粗糙度及表面起伏最小。说明激光抛光中为提高表面质量应尽量避免条纹及熔融物的出现。扫描间距为20 μm时表面条纹明显、表面起伏最大,扫描间距为5 μm时表面生成熔融物最多、表面粗糙度最大,这些结论都与图3及图5的研究结论一致。

Figure 6. Surface morphology of SiC after polishing with different scanning intervals
图6. 不同扫描间距抛光后SiC表面形貌图
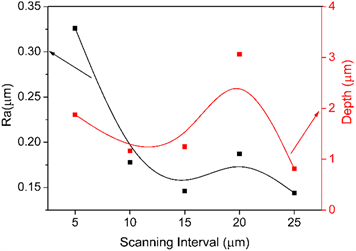
Figure 7. Ra and depth of SiC after polishing with different scanning interval
图7. 不同扫描间距抛光后SiC表面粗糙度及表面起伏变化
3.5. 扫描方式对抛光后表面质量的影响
激光扫描方式改变的是激光能量的堆叠方式。采用面扫描的方式,设定扫描速度为235 mm/s、重复频率为15 kHz,功率为100% (激光能量为89.3 μJ),扫描间距为15 μm对SiC硅面进行面抛光。研究中考察了三种扫描方式下的表面质量变化,图8所示为不同的激光扫描路径示意图及其抛光后表面形貌变化。图8(a)为激光单方向扫描,图8(b)和图8(c)分别为90˚和45˚的多方向交叉扫描。由图可以看出单方向扫描的抛光方式表面质量最好(图8(a1)),90˚的多方向交叉扫描后表面出现片状熔融物(图8(b1)),45˚的多方向交叉扫描后表面布满片状熔融物,表面质量最差(图8(c1))。多方向交叉扫描后表面片状熔融物,推测是由于两种(多种)扫描方式的交叉点多重加工导致(红色圆圈处)。扫描路径在不同方向的叠加从理论上来说虽然可以一定程度降低激光加工表面的起伏程度,但实际上仍然是使单位面积的激光能量等量多次叠加。此外,基于“孵化效应”的影响,激光辐照对材料的影响更强。多方向的扫描后,SiC表面的熔融物逐渐增多,并由颗粒熔融物的堆积逐渐变化为片状、块状熔融物,由于SiC表面几乎被熔融物完全覆盖,熔融物的分布情况从根本上影响了加工表面的粗糙度。
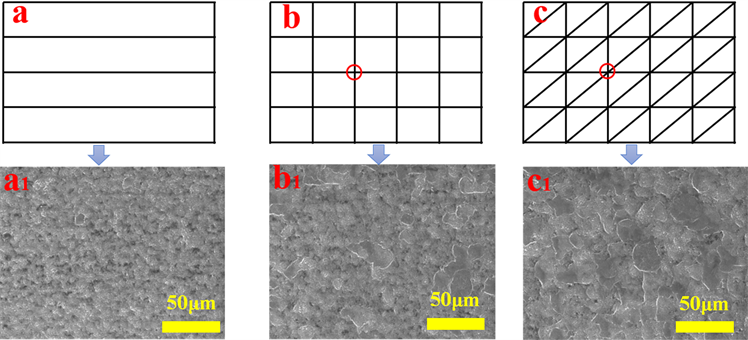
Figure 8. Surface morphology of SiC after different scanning methods
图8. 不同扫描方式及其抛光后SiC表面形貌图
3.6. 扫描速度对抛光后表面质量的影响
实验中考察了扫描速度分别为235 mm/s,118 mm/s,47.5 mm/s,23.5 mm/s抛光后SiC表面形貌(图9)、表面粗糙度/起伏(图10)的变化情况。较大的扫描速度下(235 mm/s),激光光斑重叠率小,激光在SiC
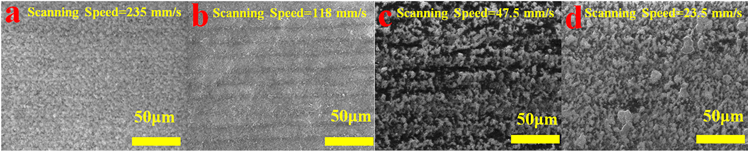
Figure 9. Surface morphology of SiC polished at different scanning speeds
图9. 不同扫描速度抛光后SiC表面形貌图
表面停留时间短,抛光后表面粗糙度及表面起伏较小,表面相对较均匀(图9(a))。当扫描速度降低到118 mm/s,光斑重叠率增大,激光在SiC表面作用时间增加,导致激光烧蚀深度增加、抛光后表面产生条纹(图9(b)),引起表面粗糙度大幅增加。继续降低扫描速度(47.5 mm/s),表面抛光过度,出现深条纹(图9(c)),表面粗糙度及起伏均相对较大。当扫描速度达到23.5 mm/s,SiC表面烧蚀严重,产生过烧起球等表面严重缺陷(图9(d))。图11(a)、图11(b)分别为图9(a)、图9(b)表面形貌放大图。从图11(a)看出,由于扫描速度过大,在单位面积作用的总能量较小,激光辐照下材料仅发生较弱的烧蚀,材料的去除量很小,由于SiC表面缺陷在表面的不同位置存在的深度不一致,激光辐照在缺陷位置的“陷光效应”也各不相同,引起缺陷位置在加工后存在差异,使得SiC表面缺陷未完全去除。118 mm/s扫描速度下抛光后SiC表面均匀覆盖生成物,未发现切割后残留缺陷,因此选择扫描速度为118 mm/s较为合适。
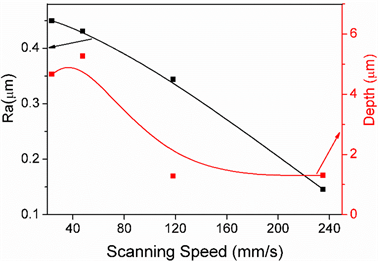
Figure 10. Ra and depth of SiC after polishing at different scanning speeds
图10. 不同扫描速度抛光后SiC表面粗糙度及表面起伏
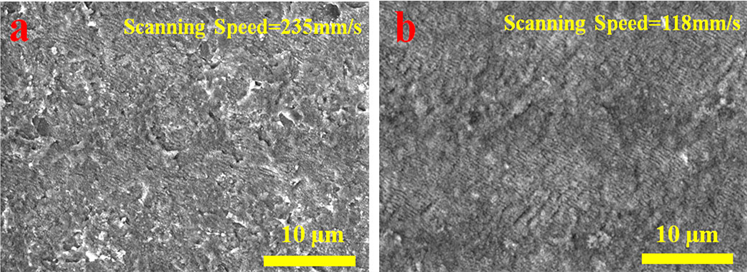
Figure 11. Surface morphology of SiC polished at scanning speeds of 235 mm/s (a) and 118 mm/s (b)
图11. 扫描速度分别为235 mm/s (a)、118 mm/s (b)抛光后SiC表面形貌图
3.7. 离焦量对抛光后表面质量的影响
由于光束为高斯光束,只有在束腰处理论光斑达到最小,光束能量也最集中,但从激光抛光来说,如何高效地达到平整表面才是关键。研究中对比了将激光聚焦在单晶SiC表面、表面正上方1 mm和表面正下方1 mm的不同抛光效果,分别称为焦点、离焦 + 1 mm、离焦 − 1 mm位置抛光效果。图12为正负离焦1 mm条件下抛光后SiC表面形貌图,在相同条件下,相对于焦点处抛光后表面(图11(b)),将样品在距焦点 ± 1 mm处抛光后表面一致性明显改善。在离焦 + 1 mm处,抛光后表面形成均一结构,表面起伏较小,粗糙度低至0.116 μm (图12(b))。这是由于在离焦的位置,光斑直径会更大,能量较为分散,单个光斑的能量分布在单位面积更为平均,更不容易引起深坑或深沟槽的问题。而在离焦 − 1 mm处,虽然相对焦点位置和离焦 + 1 mm处于对称位置,且在该平面位置的光斑直径也增大,但此时激光焦点聚焦在材料表面下方,激光在离焦 − 1 mm处的能量也更大。相对于图12(a)表面,图12(b)表面也均匀分布周期性条纹结构,但因为能量较大,条纹进一步被烧蚀,气化、熔融形成凹坑。图13为焦点位置及正负离焦1 mm条件下抛光后表面粗糙度及起伏对比,可以看出离焦 + 1 mm表面粗糙度均较小。因此,离焦 + 1 mm较为适合作为飞秒激光抛光SiC的工艺条件。
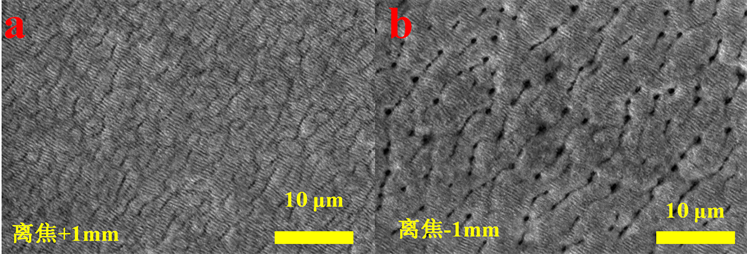
Figure 12. Surface morphology of SiC after defocusing + 1 mm (a) and defocusing − 1 mm (b) polishing
图12. 离焦 + 1 mm (a)及离焦 − 1 mm (b) 抛光后SiC表面形貌图
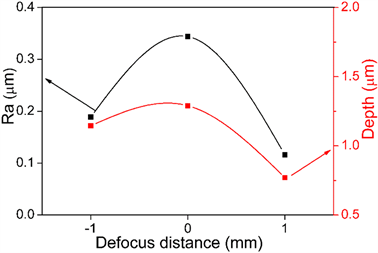
Figure 13. Ra and depth of SiC after polishing with different defocusing distance
图13. 不同离焦距离抛光后SiC表面粗糙度及起伏变化
4. 结论
本文采用激光对6H SiC切割片硅面进行抛光,通过对激光重复频率、扫描间距、脉冲能量、扫描速度、离焦距离等参数优化。在最优条件下,抛光后6H SiC硅面表面平整,线切割残留的缺陷完全去除,粗糙度低至0.116 μm,表面起伏低至0.77 μm。研究发现:表面条纹及生成物对抛光后表面质量(粗糙度/起伏)有较大影响。其中,表面起伏对条纹的变化较为敏感,生成物则对表面粗糙度影响较大。激光过度烧蚀会造成表面形貌急剧变差,严重影响表面质量。本研究揭示了激光工艺条件与抛光后表面质量对应关系,为激光抛光工艺用于6H SiC硅面制造提供理论及实验支持,具有较高的参考价值。
基金项目
本论文得到国家重点研发计划(No. 2018YFB1107700)、深圳市科技计划(No. JCYJ20170817153703060)资助。
NOTES
*通讯作者。