1. 引言
随着科技的发展和社会的进步,制造业之间的竞争力日益激烈。为了在竞争中立于不败之地,各个企业都在想方设法提高生产率并且降低消耗,而减少和消除不必要的作业是最有效的方法之一。只有缩短生产周期,减少空地,减少物料的停留、搬运和库存,才能保证投资最少、生产成本最低。
某汽车电机公司的转子生产车间M面积为1259 m2,有操作工52名,共生产53个系列转子产品。为了节约物流成本,有效利用车间空间,使得物流更加便捷,空间得到更加充分利用,提高生产效率,现对M车间的布局进行优化。基于鱼骨图 [1],对其工艺流程与车间现状分析得出如下问题:车间物流路径多有回流且移动距离过长,产品工序又较多,各产品路径混杂不清晰;暂存区较多,且每个暂存区内都堆积很多产品,搬运不及时,导致通道拥挤;车间内有许多废弃设备未及时清走,占用较多面积,问题设备未及时修理。
针对以上问题,利用SLP方法对现有M车间的布局进行改善。系统布置设计方法(SLP) [2] 是工艺专业化布局时常用的方法。缪瑟 [3] 提出系统布置设计(SLP),车间布局规划正式成为一门具有学科方向和技术体系的学科。如今,SLP由当初的按经验做事到定量分析再到有自己专门的知识体系和特有符号再到如今和建模仿真和算法 [4] 联系到一块,发展的越来越好。布局优化也不只应用在制造业 [5]、学校 [6]、超市 [7] 以及物流电商 [8] [9] 都可以应用到。
2. 基本要素分析
2.1. 产品(P)-产量(Q)分析
为了更加合理的对转子生产车间进行布局优化,对M车间的转子产品进行了P-Q分析,M车间的转子系列产品中,主要生产ZD094 (ZD044)、ZD028、ZD035三种产品,且三种产品适合采用流水线型方式。根据二八原则,以这三种产品的生产设施为主进行车间布局优化。
2.2. 工艺流程分析
根据P-Q分析的结果,以ZD094 (ZD044)、ZD028、ZD035这三种产品作为切入点进行工艺流程的分析。具体情况如图1所示。
从图1中可以看出,这三种产品的加工工艺相似,均有压铁芯片穿绝缘纸、压入换向器、点焊、浸漆、精车换向器、换向器下刻、宝石刀精车、动平衡测试、短路检测和压轴承这几项工艺。在进行作业单位划分以及设施布局时可从相同工艺部分入手进行优化,可将三种产品的相同工艺部分进行合并优化。
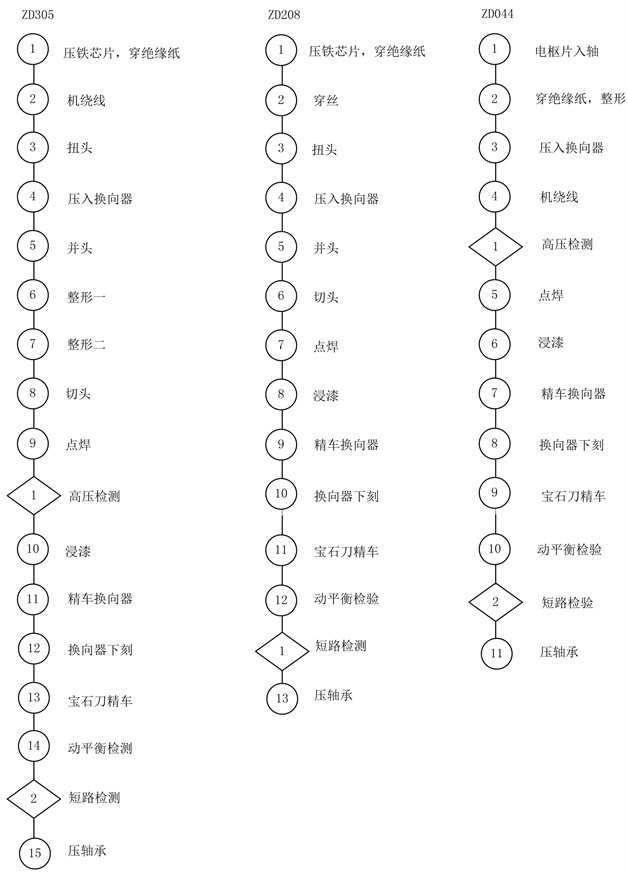
Figure 1. Process flow chart of ZD 035/ZD 028/ZD 044
图1. ZD035/ZD028/ZD044三种产品的工艺流程图
2.3. 车间作业单位的划分
在进行作业单位划分之前,对车间进行了产线平衡,并根据产品的生产工艺,将车间划分为15个作业单位,依次为周转区、转子028穿轴成型区、转子028穿丝区、转子028整型半成品区等。这15个作业单位的具体用途如表1所示。
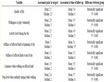
Table 1. Summary table of M workshop operation units
表1. M车间作业单位汇总表
3. 作业单位关系分析
3.1. 物流关系分析
分析不同功能区之间的物流强度关系,在SLP中,用等级划分来表示他们的密切程度,具体划分为:A:绝对重要、E:特别重要、I:重要、O:一般密切程度、U:不重要,其划分可根据承担物流量的比例来确定。该生产车间的各作业对之间的物流强度如表2所示:
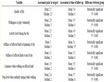
Table 2. Summary table of logistics relationship level among each operation unit
表2. 各个作业单位之间的物流关系等级汇总
注:表2中的作业单位对并不完整,除表2中所描述的,其余作业单位对的物流关系等级均为U。
根据表2中的物流关系等级,可以绘制出相应的物流相关图,如图2所示。

Figure 2. Logistics correlation diagram of operation unit
图2. 作业单位物流相关关系图
从图2中可以看出,作业单位对10~11、11~12、12~13物流关系等级最高,在进行布局改善时应将他们的位置安排在一起。
3.2. 非物流关系分析
确定各作业单位之间非物流关系的主要影响因素有以下几个方面:安全污染、工艺流程、相同的公共设施、监督和管理方便、噪声、服务的频繁和紧急程度等。作业单位的非物流等级划分及含义为,A:绝对重要、E:特别重要、I:重要、O:一般密切程度、U:不重要、X:负密切程度。非物流等级评级理由见表3。
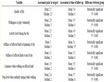
Table 3. Reasons for non-logistics relationship level of operation unit
表3. 作业单位非物流关系等级的理由
基于表3,可以对M车间各个作业单位之间的非物流关系进行评价,得出如图3所示的作业单位非物流相关关系图:
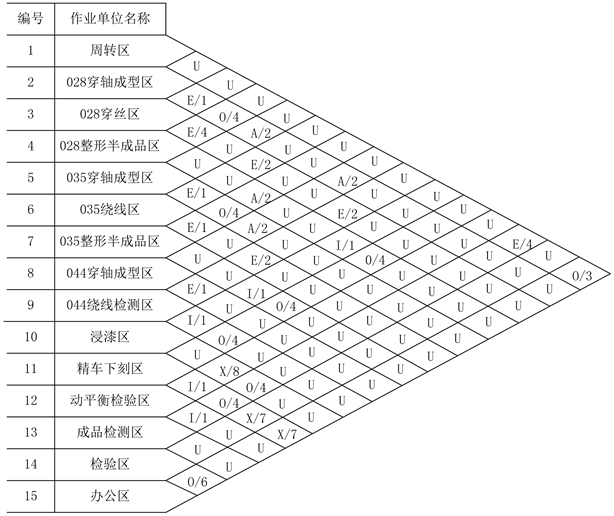
Figure 3. Non-logistics correlation diagram of operation unit
图3. 作业单位非物流相关关系图
3.3. 作业单位综合相互关系分析
对于M车间来说,物流因素的影响并没有明显大于非物流因素的影响,因此在计算综合关系时取加权值m:n = 1:1。通过计算,按照A、E、I、O、U、X确定各作业单位密切程度等级,绘制综合相关图, 如图4所示。
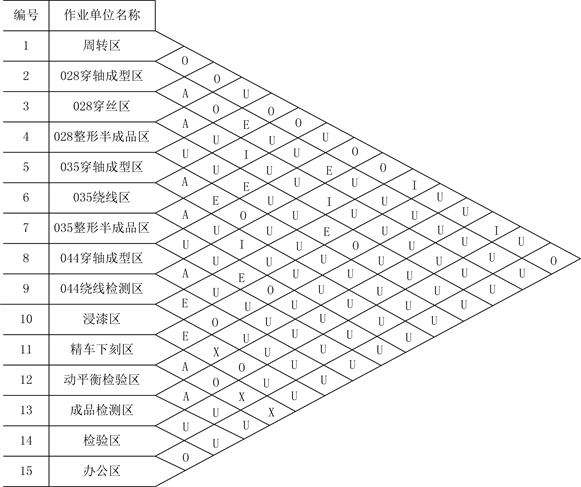
Figure 4. Comprehensive relationship diagram of operation units
图4. 作业单位综合相互关系图
3.4. 作业单位位置相关图
根据作业单位的综合相互关系,可以绘制出作业单位得综合接近程度排序图。某一作业单位的综合接近程度等于该作业单位与其他作业单位之间量化后的关系密切等级的总和。具体情况见图5。
依据SLP的思想,首先根据综合相互关系等级高低按照A、E、I、O、U、X的顺序确定不同级别作业单位的位置,而同一级别的作业单位则按照综合接近程度分值的高低来进行布置。
按照上面的布置方法,可以得到如下的转子车间作业单位位置相关图,如图6所示。
注:图6中四条黑色实线代表作业单位综合之间关系为A等级,三条黑色实线为E等级,两条黑色实线为I等级,一条黑色实线为O等级,黑色虚线为X等级。结合各个作业单位的面积以及物料搬运等其他因素,可画出转子生产车间的平面布置图,如图7所示。
4. 改善前后对比分析
4.1. Flexsim建模仿真分析
为了验证改善后的布局有利于提高生产效率、减少库存堆积、降低生产成本,建立一个仿真模型,并将改善前后的生产节拍等数据输入Flexsim仿真系统 [10] [11] 中,得到以下对比数据。模型如图8所示,对比数据如表5、表6所示。
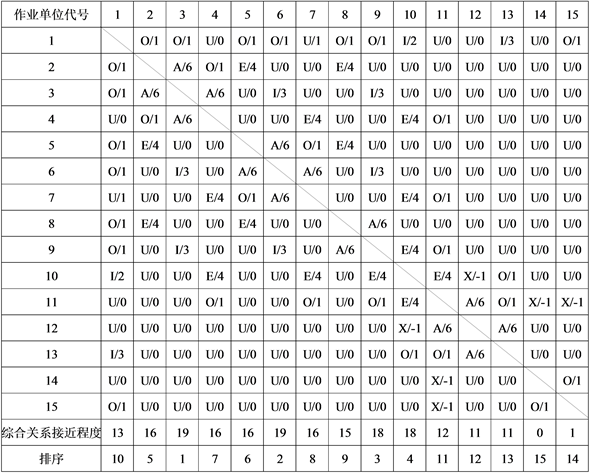
Figure 5. Comprehensive approach diagram of working units in rotor workshop
图5. 转子车间作业单位综合接近图
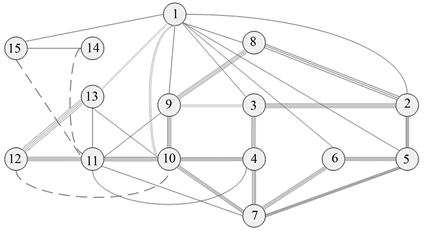
Figure 6. Location correlation diagram of operation unit
图6. 作业单位位置相关图
4.2. 改善数据对比分析
(1) 产量对比分析
以上表中的第一列表示建模仿真中的工位名,改善前有18个工位,最终产量不足500件;而改善后工位减少至15个且最终产品产量由不足500件提升至将近1000件,产量增长将近一倍,产能有较大提升。
(2) 产线平衡对比分析
改善前,存在等待的工位有5个,平均等待时间在4000 S左右,改善后产线中存在等待的工位仅有2个且平均等待时间在3400 S左右,改善后的产线较之前产线更加平衡。
注:表中数字单位为mm,车间区域为79000 × 40000,作业单位3面积为1000 × 1000。
Figure 7. M layout of workshop operation unit
图7. M车间作业单位布局图
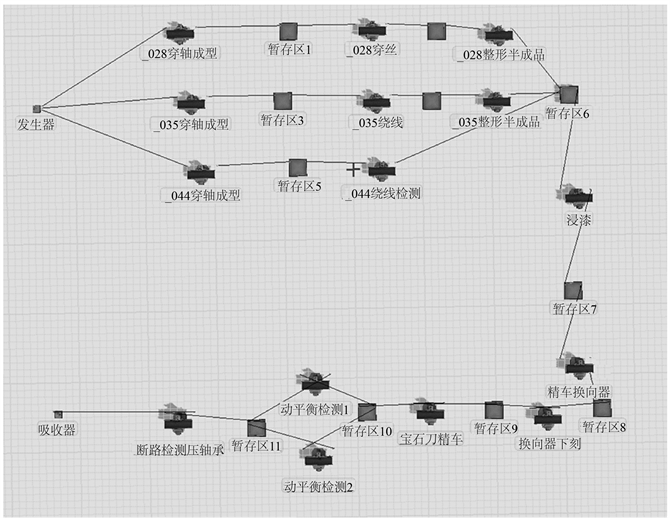
Figure 8. Rotor workshop simulation model
图8. 转子车间仿真模型
(3) 机器效率对比分析
改善前,12个机器存在闲置且半数机器闲置率在20%以上,最大闲置率达76.7%;改善后虽然仍有11台机器存在闲置,但10台闲置率在20%以下,另一台闲置率为20.3%加工率得到有效提高,改善效果显著。
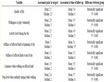
Table 5. Relevant data of each station in the workshop before improvement
表5. 改善前车间各工位相关数据
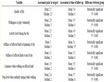
Table 6. Relevant data of each station in the workshop after improvement
表6. 改善后车间各工位相关数据
以上是改善前后产线的数据对比表。(注:以上表格中的数据都是在机器工作时间为7.5个小时的情况下进行的)。
(4) 暂存区对比分析
改善前产线暂存区库存数量最少为78件,最大为425件;改善后暂存区的库存量明显减少,最大困存仅为114件在制品。
总的来说,改善后产线的生产效率明显得到提升,一天内生产的产品数量由485件提升到897件,效率提升将近一倍,工位暂存区库存最大值由425件减至114件。
5. 结论
新的布局方案将车间的加工区更加聚集分布,有效的减少了M车间的在制品堆积问题并提高了车间生产效率。
布局优化的本质是现场物理空间的调整,更重要的现场管理流程、工艺流程的管理重组,它是现场管理的载体与体现,当现场管理层混乱不畅时,往往会体现在物理空间的布局中,但是仅仅调整布局不能解决管理不善带来的问题,需要从本质上解决管理问题,布局优化才能发挥重要作用。
NOTES
1刘俊艳,1980.11-,博士,硕导,研究方向:工业工程,人因工程,数字化工厂。
2李栋,1997.6-,实验员,研究方向:工业工程。