1. 引言
铁路货物列车作为大型物流运输的工具,对我国经济发展有着重要的影响 [1] [2]。货物列车的速度,是制约运输效率的关键因素。但随着速度的提高,会极大地影响列车运行平稳性与稳定性,给行车安全带来一定的隐患。对于货物列车提速对车辆结构及动力学性能的影响,有关学者做了一定的研究。刘转华 [3] 分析了现行的转8AG、转8G、转K2、摆动式转向架的结构和性能及运用中存在的问题。邬平波等 [4] 建立了货车非线性系统动力学模型和转K2转向架侧架有限元模型,并研究了转K2转向架侧架的疲劳寿命。陈雷等 [5] 基于贝叶斯方法的车辆运行状态地面评估技术,运用可靠性分析方法,对环行线货车可靠性试验中提速货车的横向动力学性能进行了系统研究。龚凯等 [6] 根据重载铁路货物列车–轨道系统横向振动稳定性分析方法,提出基于货物列车抗脱轨安全度的重载铁路轨道结构强化措施评价方法,并分析了轨道强化措施对货物列车抗脱轨安全度的影响。陈雷等 [7] 开展了120 km/h货车综合提速试验,并对比分析了近年来我国提速综合试验的测试线路、试验车辆、运行特点和测试数据。詹宏亮等 [8] 对铁路货车在检修过程中发现的各部位问题进行了统计和分析,归纳了货车提速对车辆的影响,并提出在检修过程中应注意的各种事项。秦忠义 [9] 阐述了提速对铁路货车的影响,并对其产生的原因进行了分析,最后提出了针对性的检修建议。在我国客货运大提速背景下,吴怀念 [10] 指出了我国铁路货车提速改造及发展方向。上述成果为研究空重混编货物列车提速对动力学性能的影响奠定了重要的基础,但以往研究大多割裂了货车提速理论与试验,且偏向于货车提速对车辆结构的影响,而现实中货物列车常常空重混合编组,将空重混编货物列车提速动力学理论计算和试验验证进行结合的研究较少,因此有必要对此问题进行研究。
为提高货物运输能力,释放货物列车运输组织压力,本文以某区段线路及空重混编货物列车为研究对象,并基于循环变量的模块化方法,建立长大编组货物列车系统动力学模型,对货物列车提速的动力学性能进行了仿真分析,并在理论研究的指导下,完成了该区段货物列车提速试验研究。
2. 理论研究
2.1. 数学建模
货物列车至少由几十辆车组成,如果1列车包含n辆车,而每辆车有m个自由度,则整列车系统就有m×n个自由度,列车系统的运动方程表达式为:
(1)
其中,[M]为列车系统的质量矩阵,[C]为列车系统的阻尼矩阵,[K]为列车系统的刚度矩阵,Y为列车的自由度变量,{P}为列车的外部作用力,{F}为列车之间的相互作用力。
由于货物列车编组较长,依据传统的多刚体动力学建模方式处理模型,会导致“自由度爆炸”而给计算分析带来很大困难。因此,开发长大编组列车动力学建模及求解方法—基于循环变量的模块化方法 [11],因此,可将式(1)分解为n个子方程:
(2)
其中,
为第i辆车所有自由度的集合,
为第i辆车的质量矩阵,
为第i辆车的阻尼矩阵,
为第i辆车的刚度矩阵,
为作用在第i辆车的外部作用力,
为车辆之间的相互作用力。
根据公式(2),可将一辆车看成一个基本的积分单元,把列车系统庞大的计算问题划分为n个基本积分单元分别进行计算,并且每辆车的计算循环使用同一组自由度变量。每辆车计算完成后,把计算结果存入中转变量,然后释放自由度变量为下一辆车计算所用,直到列车中所有的车辆都完成计算后,再进入下一个积分步。下一积分步仍按上一积分步的模式进行,直到完成所有的积分计算。在整个列车的积分计算中,使用的自由度变量不会随着列车编组的增加而增加,因而可以解决长大列车“自由度爆炸”给计算带来的难题。这种方法即为“循环变量法”。
由于循环变量法只善于解决只含一种车型的长大列车的建模,但难于处理车型众多的混编列车。而实际的运营列车,特别是货物列车,经常出现混合编组。为此,建立了一个机车车辆模型库(可包含所有型号的机车车辆),在计算时只需根据列车的编组情况设置相应车型的顺序号即可进行全列车的动态仿真计算。当列车编组发生改变时,不需要重新建模和修改程序,只需修改编组的定义即可,从而大大方便了混编列车的建模。这种方法即为“模块化建模”。
基于循环变量的模块化建模方法,采用TPLtrain多体动力学软件进行建模,其中空车转向架选用了线路工况最差的转K2转向架。
2.2. 仿真分析
采用美国五级谱进行激励,仿真了不同编组列车以80 km/h、85 km/h、90 km/h通过直线及曲线时的牵引工况、常用制动及紧急制动情况下的动力学性能,对提速过程中列车的平稳性及稳定性进行了全面分析,并统计了各编组在不同运行条件和线路工况下评定指标的最大值。列车编组情况如下所示:
编组2:机车 + 16重车 + 5空车 + 23重车 + 5空车 + 16重车;
编组3:机车 + 5空车 + 55重车 + 5空车;
编组4:机车 + 55重车 + 10空车;
编组5:机车 + 27重车 + 10空车 + 28重车。
以机车为起始位对整列车进行编号,即机车编号为0,尾车编号为65。
平稳性计算时,采用直线线路。各编组在三种通过模式(牵引工况、常用制动、紧急制动)中分别以80 km/h、85 km/h、90 km/h的速度通过,得到不同速度等级下横向平稳性和垂向平稳性。将不同速度等级下的平稳性指标进行对比,发现随着速度的提高,振动加速度变大,横向平稳性和垂向平稳性均变大,故取各编组横向平稳性和垂向平稳性的最大值,分别如图1和图2所示。图中数值为3.5的红色直线表示货车平稳性指标等级为“优”。

Figure 2. Maximum vertical stationarity
图2. 垂向平稳性最大值
由图1可知,牵引工况下,对于空车处于中间位置,编组2在空车编号部分(17~21、45~49)时横向平稳性减小,编组5在空车编号前半部分(28~32)时横向平稳性减小,在空车编号后半部分(33~38)时横向平稳性增大;而对空车处于首尾两端位置,编组3、编组4在各自空车编号部分时横向平稳性均增大。在牵引工况下,尽可能将空车置于中间位置,且连续空车数量不宜过多,可有效降低横向平稳性。在常用制动和紧急制动时,各编组横向平稳性在各自空车编号部分增大。常用制动时,由于速度降低较慢,空车部分受到振动较均衡,故各编组空车部分的横向平衡性相差不大;但在紧急制动时,由于后部车辆挤压前车,造成后部车辆空车部分的挤压力变大,引起编号靠后空车的横向平稳性相对于编号靠前空车的横向平稳性更大。各编组横向平稳性最大值指标均未超过规定的限度值3.5,达到“优”级标准。
由图2可知,对于空车编号处于首尾两端的编组3和编组4,由于端部的空车重量较轻,在空车两端无重车连挂的情况下,受到垂向振动变大;牵引工况、常用制动、紧急制动下,编组3和编组4的垂向平稳性依次降低,且垂向平稳性开始增大时的列车编号逐渐靠后。对于空车两端在重车连挂的情况下,会抑制空车的垂向振动,故编组2和编组5的垂向平稳性较小。各编组垂向平稳性最大值指标均未超过规定的限度值3.5,达到“优”级标准。
轮轴横向力计算时,分为直线和曲线工况,曲线半径R = 600 m,缓和曲线长110 m。常用制动时减压量为70 kPa。各编组在三种通过模式(牵引工况、常用制动、紧急制动)下以80 km/h、85 km/h、90 km/h的速度下通过模式的轮轴横向力。统计后发现,在相同速度下,由于过曲线时,速度越高,受到外轨挤压越明显,因此,三种通过模式下轮轴横向力在曲线和90 km/h时取得最大值,故取此种状态表示轮轴横向力的最大值,如图3所示。图中数值为26.4的红色直线表示计算出的货车轮轴横向力为“优”的上限值。

Figure 3. Maximum transverse force of axle
图3. 轮轴横向力最大值
由图3可知,三种通过模式中,各编组在空车编号部分轮轴横向力减小。无制动通过曲线时,由于速度较高,车轮通过曲线时受到外侧钢轨的挤压最明显;而对常规制动和紧急制动,由于过曲线时速度逐渐减低,车辆编号靠后的车辆轮轴横向力明显降低。各编组在无制动时轮轴横向力最大值接近26.4,其余情况均未超过规定的限度值26.4,达到“优”级标准。
轮重减载率计算时,分为直线和曲线工况,曲线半径R = 600 m,缓和曲线长110 m。常用制动时减压量为70 kPa。各编组在三种通过模式(牵引工况、常用制动、紧急制动)下以80 km/h、85 km/h、90 km/h的速度通过直线和曲线,分别得到直线和曲线下三种通过模式的轮重减载率。统计后发现,在相同速度下,过曲线时的轮重减载率较大。速度越高,轮重减载率越大。三种通过模式下轮重减载率在曲线和90 km/h时取得最大值,故取此种状态表示轮重减值率的最大值,如图4所示。图中数值为0.64的红色直线表示货车轮重减载率为“第一限度”。

Figure 4. Maximum wheel weight reduction rate
图4. 轮重减载率最大值
由图4可知,在三种通过模式下,由于空车处质量较轻,各编组在各自的空车编号部分轮重减载率均增大。在牵引工况下,速度保持不变,各编组重车编号部分轮重减载率基本保持不变;在常用制动和紧急制动下,由于速度降低,各编组重车编号靠后部分轮重减载率逐渐降低。各编组在空车编号部分轮重减载率最大值接近0.64,其余情况均未超过规定的限度值0.64,达到“第一限度”标准。
脱轨系数计算时,分为直线和曲线工况,曲线半径R = 600 m,缓和曲线长110 m。常用制动时减压量为70 kPa。各编组在三种通过模式(牵引工况、常用制动、紧急制动)下以80 km/h、85 km/h、90 km/h的速度通通过模式的脱轨系数。以90 km/h的速度通过曲线时的脱轨系数为三种通过模式下的最大值,如图5所示。图中数值为1.2的红色直线表示计算出的脱轨系数为“第一限度”。

Figure 5. Curve: system result of standard experiment
图5. 脱轨系数最大值
由图5可知,牵引工况下,货车以90 km/h的速度全速通过曲线,各编组在空车部分的脱轨系数均变大;对常用制动和紧急制动,过曲线时速度开始降低,所以空车编号靠后的部分快速减小,最后与重车部分的脱轨系数接近。各编组的脱轨系数最大值均未超过规定的限度值1.2,达到“第一限度”标准。
3. 试验研究
3.1. 数据测量
车辆动力学测试是指采用测力轮对,依据《GB/T 5599-1985铁道车辆动力学性能评定和试验鉴定规范》测得的数据,计算脱轨系数等动力学性能指标。图6为试验现场测力轮对和数据采集设备图。
(a) 测力轮对
(b) 数据采集设备
Figure 6. Vehicle dynamics test site
图6. 车辆动力学测试现场图
轮轨横向力Q和轮轨垂向力P采用测力轮测量 [12] [13] [14]。测力轮对选择4条,其踏面磨耗状态为2条新旋,2条磨耗3 mm。垂向力和横向力测量贴片布置如图7所示。
(a) 垂向力测量
(b) 横向力测量
Figure 7. The patch location
图7. 贴片位置
图8给出了加速度传感安装示意图。测定货车车体垂直和横向加速度的加速度传感器安装在1或2位心盘内侧距心盘中心线小于1000 mm的车底架中梁下盖板上,其中1为中梁,2、3为垂直、横向加速度传感器,4为安装铁。

Figure 8. Acceleration sensor installation diagram
图8. 加速度传感器安装示意图
测得数据后,可由式3~6求得垂向力和横向力的比例系数
、
及其相互间的影响因素
、
。
垂向力比例系数
(3)
横向力比例系数
(4)
垂向力对横向力桥路的影响系数
(5)
横向力对垂向力桥路的影响系数
(6)
得到系数矩阵
,并计算其逆矩阵
。以右轮的第1组应变为例,其垂向力P和横向力Q计算公式如下:
(7)
(8)
式中,矩阵
为右轮的第1组垂向应变,
为右轮的第1组横向应变。求得垂向力P和横向力Q后,可根据相关公式求得脱轨系数等参数。
3.2. 数据分析
图9、图10分别给出紧急制动下通过直线区段和弯道区段的脱轨系数。相同速度下,通过直线区段时的脱轨系数比通过曲线区段的小,且速度越高,通过曲线区段的脱轨系数越大,其原因为在相同的较高速度下,在紧急制动后前后车辆挤压力更大,故而脱轨系数也较大。通过直线区段时,编组2、编组3在80 km/h至90 km/h的速度范围内不敏感,脱轨系数相差不大;但通过弯道时,速度越高,脱轨系数越大。直线工况下,编组2 (空车处于中间)的脱轨系数比编组3 (空车处于两端)受速度的影响更大;曲线区段部分,紧急制动下虽然速度逐渐降低,但编组2和编组3均在各自空车编号部分的脱轨系数增大。

Figure 9. Derailment coefficient under the straight line condition of emergency brake
图9. 紧急制动直线工况下的脱轨系数

Figure 10. Derailment coefficient under the curve of emergency brake
图10. 紧急制动弯道工况下的脱轨系数
图11、图12分别给出紧急制动下通过直线区段和弯道区段的轮重减载率。相同速度下,通过直线区段时的轮重减载率比通过曲线区段的小,且速度越高,通过曲线区段的轮重减载率越大。通过直线区段和曲线区段时,编组2 (空车处于中间)的轮重减载率比编组3 (空车处于两端)在80 km/h至90 km/h的变化更大。通过直线区段时,编组2和编组3的轮重减载率在各速度等级下变化平缓;但通过曲线区段时,速度在紧急制动下逐渐降低,编组2和编组3的轮重减载率在总体上逐渐减小,但会在各自的空车编号部分(特别是处于紧急制动后时间较短的部分)有显著增大。

Figure 11. Wheel weight reduction rate under the straight line condition of emergency brake
图11. 紧急制动直线工况下的轮重减载率

Figure 12. Wheel weight reduction rate under the curve of emergency brake
图12. 紧急制动弯道工况下的轮重减载率
图13、图14分别给出紧急制动下通过直线区段和弯道区段的轮轴横向力。相同速度下,通过直线区段时的轮轴横向力比通过曲线区段的小,且速度越高,通过曲线区段的轮轴横向力越大,其原因为通过曲线时离心力产生的较大的横向分力。通过直线区段时,编组2、编组3对在80 km/h至90 km/h的速度不敏感,轮轴横向力变化较小;通过弯道时,随着紧急制动的进行,编组2和编组3的轮轴横向力总体上逐渐减小,但会在各自的空车编号部分增大。

Figure 13. Lateral axle force under the straight line condition of emergency brake
图13. 紧急制动直线工况下的轮轴横向力

Figure 14. Lateral axle force rate under the curve of emergency brake
图14. 紧急制动弯道工况下的轮轴横向力
对全列空载进行全线拉通试验,采集列车行驶中车轮的垂向力、横向力等情况,为后续进行车辆局部线路往复行驶试验选出最危险的试验路段。对编组2、3、4、5进行了车辆动力学测试,对测得结果取平均值,并将该组数据中的最大值作为误差棒的上限值,其结果如图16。图中2、3、4、5分别表示编组2、编组3、编组4、编组5;NB、CN、EB分别表示牵引工况、常用制动、紧急制动;CT4、CT5分别表示对编组4、编组5进行全程拉通试验。
图15、图16分别给出了编组2、编组3、编组4、编组5通过直线和曲线的轮轴横向力,图中数值为26.4的红色直线表示计算出的货车轮轴横向力的上限值。相同条件下,曲线处轮轴横向力更大,其原因为离心力产生的横向分力变大。直线通过时,编组3和编组4在牵引工况下轮轴横向力相对较小,其原因为前后编组车辆无挤压,车辆运行平稳;在常用制动下,由于后车会挤压前车,导致轮轴横向力变大;紧急制动模式下,在没有出现后车制动相对不足的情况下,其特征与常用制动相似,但是在出现后车制动相对不足的情况下,测试车辆后轮会受到挤压,轮轴横向力会变大。曲线通过时,常用制动下轮轴横向力较小,其原因为速度降低,车轮受到钢轨力减小。由于编组4、5进行全程拉通试验,其线路包含直线部分和曲线部分,其最大值出现在曲线段,故其脱轨系数较大。各编组车辆在不同速度等级下运行各测试参数未见明显规律,可能是车辆运行速度等级接近,且在实际运行中速度存在一定误差,即80 km/h为79~82 km/h之间,85 km/h为83~87 km/h之间,90 km/h为88~90 km/h之间。各编组轮轴横向力最大值均未超过26.4,达到“优”级标准。
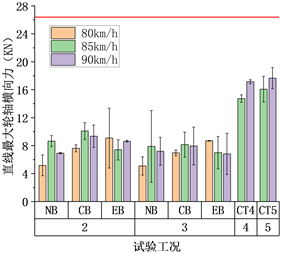
Figure 15. Maximum axle lateral force (straight line)
图15. 最大轮轴横向力(直线)

Figure 16. Maximum axle lateral force (curve)
图16. 最大轮轴横向力(曲线)
图17、图18分别给出了编组2、编组3、编组4、编组5通过直线和曲线的轮重减载率,图中数值为0.64的红色直线表示货车轮重减载率的“第一限度”值。相同情况下,由于通过曲线时车轮会受到外轨更大的作用,引起车轮与钢轨沿垂向分力变大,进而车辆轮重变化较大。直线通过时,牵引工况下轮重减载率较小,这是因为在无制动的情况下,车辆各编组前后车辆挤压力较小;在常用制动和紧急制动

Figure 17. Maximum wheel weight reduction rate (straight line)
图17. 最大轮重减值率(直线)

Figure 18. Maximum wheel weight reduction rate (curve)
图18. 最大轮重减值率(曲线)
时,后面车辆挤压前面车辆,导致轮重减载率变大。各编组车辆随着速度的提高,其轮重减载率变大。曲线通过时,速度越高,轮重减载率越大;相同速度下,牵引工况比制动工况的轮重减载率更大,这是因为车辆以较高速度通过,受到的轮对减载力比因制动引起前后车辆挤压产生的轮对减载力大。由于编组4、5进行全程拉通试验,其线路包含直线部分和曲线部分,其最大值出现在曲线段,故而通过直线和通过曲线时都取得是最大值。各编组的轮重减载率均不超过0.64,达到“第一限度”要求。
图19、图20分别给出了编组2、编组3、编组4、编组5的脱轨系数,图中数值为1.2的红色实线表示脱轨系数为“第一限度”值。相同情况下,通过曲线时脱轨系数比通过直线时大。通过直线时,在相同编组模式下,各编组车辆在不同速度等级下运行各测试参数未见明显规律。通过曲线时,与牵引工况相比,常用制动的速度逐渐降低,因此脱轨系数较低;而与紧急制动相比,常用制动下前后车辆挤压力较小,故而脱轨系数也较小。编组4、5进行全程拉通试验,其线路包含直线部分和曲线部分,其最大值出现在曲线段,故而通过直线和通过曲线时都取得是最大值(即曲线段),故图19、图20中值相同。各编组脱轨系数均未超过规定的限度值1.2,达到“第一限度”标准。

Figure 19. Maximum derailment coefficient (straight line)
图19. 最大脱轨系数(直线)

Figure 20. Maximum derailment coefficient (curve)
图20. 最大脱轨系数(曲线)
4. 结论
1) 在相同编组模式下,三种通过模式中(无制动、常规制动、紧急制动),常规制动模式各项指标相对较好,其原因为运行过程中随着运行速度降低,各项指标趋好,与理论分析相符;紧急制动模式下,在没有出现后车制动相对不足的情况下,其特征与常规制动相似,但是在出现后车制动相对不足的情况下,测试车辆后轮外轨会受到挤压;无制动通过时,各项测试指标理论上与运行速度和曲线半径相关,测试时出现与轮轨接触状态相关的特征。
2) 各编组车辆随着速度等级的提高,各测试参数一般会增大,但有些参数在80 km/h至90 km/h的速度范围内无明显变化,其原因为该参数是通过在不同的路段取平均值得到的,可能是不同的路段得到的值差距较大,而且曲线工况下的制动试验,尤其是紧急制动试验,很难保证所测试的车辆紧急制动的试验处于曲线上。
3) 不同编组情况下,测试结果未见明显规律。但是在各自编组中,测试参数在空车编号部分会发生显著变化,并在某些情况下接近安全值。
4) 仿真结果和试验结果下的各编组车辆运行安全性指标满足《GB 5599-85》要求。
基金项目
国家自然科学基金(No. 2021YJ0026)资助项目。