1. 引言
回转体零件在切削加工中很常见,长度和直径比不小于20的轴称为细长轴。它随处可见,如海底传动轴、数控车床上的光杆、滚轴、纺织机械中的锡拉轴、机床中常用的光杆和螺杆、活塞杆和心轴 [1]。细长轴的加工尺寸误差的提高对生产设备的精度和使用效益影响重大,减少细长轴加工尺寸误差的产生有以下几个难点 [1]:
(1)、细长轴自身刚性不强,车削时引起的热和力相互作用,形成残余应力,使材料表层发生塑性形变,降低了细长轴的表面粗糙度和尺寸精度 [2]。
(2)、细长轴在加工中要求生产操作者有较高的加工技能,并能选择合适的切削参数和工艺参数,安装辅助夹具和调整机床软硬件,并且加工中经常会出现腰鼓形和竹节形,如图1中的(a)和(b)所示 [3]。
(a) 腰鼓形(b) 竹节形
Figure 1. Waist drum shape and bamboo segment shape
图1. 腰鼓形和竹节形
机床原理误差、夹具误差、残余应力引起的塑性形变,都会对细长轴尺寸精度产生影响 [4]。在机械加工中,热力耦合的作用产生残余应力,残余应力引起材料表层发生塑性形变,使细长轴产生尺寸误差 [5]。目前,普通车床自身丝杆间隙误差大,很难实现对细长轴进行误差补偿。其次,误差补偿的计算很复杂,掌握难。最后,可以通过机床结构改造实现细长轴加工精度提高,但有技术风险并会影响原有加工能力。在加工工艺、切削参数、装夹方式方面对细长轴的误差研究比较多,但对成形机理的研究不足,热力耦合下细长轴加工过程的研究很少,热力耦合形成残余应力的过程未彻底研究清楚,对残余应力引起的加工误差,大多集中于确定性质的研究缺少确定量的研究。
2. 细长轴车削热力耦合误差分析
2.1. 切削加工热力耦合理论
在刀具切除多余材料时,工件、刀具、切屑会形成能量传递和转化,当刀具对工件切削时,工件产生应变能。机械加工过程中,材料表面形成应变能,材料内部存在的弹性形变没能力抵消应变能产生的塑性形变。材料塑性形变和摩擦产生的功共同变换为热能,切削区热能的集聚和提高产生热应变,表面变软。切削力的大小随材料表面变软和变硬而变化,而刀具在切削时产生的功随加工中产生的力与热的变化而变化。切削热和切削力的变化相同,刀具温度随切削热减弱而降低,随着刀具温度降低软化作用削弱,材料硬化导致切削力有增大趋势。残余应力的控制方法是建立在热力耦合的理论基础上的,总应变量
,在不考虑蠕变时表示成:
(1)
——弹性应变增量;
——塑性应变增量;
——热应变增量。
根据Pranditl-Reuses理论,得到材料机械力的弹塑性力学本构关系 [6]:
(弹性变形区) (2)
(塑性变形区) (3)
、
——机械应力和应变;
、
——材料弹性矩阵、弹塑性矩阵。
切削热产生的热应力–应变本构关系:
(弹性变形区) (4)
(塑性变形区)(5)
、
——热应力和热应变。
(6)
(7)
——线膨胀系数;
T——温度;
H——热源距离;
——等效应力;
——等效塑性应变;
、
——弹性矩阵、弹塑性矩阵。
与温度相关的强化系数,
(8)
——温度强化系数。
机械应力和热应力叠加,材料的热–弹塑性力学本构关系:
(弹性变形区)(9)
(塑性变形区) (10)
——残余应力。
根据Prandtl-Ruess增量理论,设定材料各向应变硬化同性,塑性条件满足Von Mises屈服准则,则热–弹塑性本构方程为 [6]:
(11)
——残余应力;
——全应变增量;
——热应力;
——热应变增量;
、
——弹性矩阵、弹塑性矩阵。
应用增量变分原理,经过数值计算推导出仿真的热–弹塑性本构关系表述 [7]:
(12)
(13)
——应力;
——等效应力;
——线膨胀系数;
T——温度;
——温度强化系数;
、
——弹性矩阵、弹塑性矩阵。
2.2. 加工表面形成过程
对尺寸精度和表面质量影响最大的是第三变形区,如图2。因为实际加工时刀具有刀尖钝圆半径,刀刃和材料发生相对运动,切削层中有高度为hs的材料从刀刃O点以下,受挤压变形成为已加工表面一部分。此区域材料经过刀尖钝圆最低处B后,在VB处受力和热影响引起塑性形变,已加工表面在CD处与后刀面接触,当材料自身应力产生弹性变形产生恢复高度为∆h [8]。
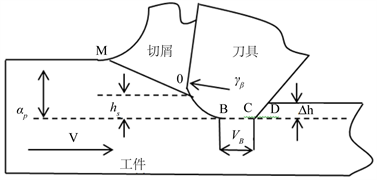
Figure 2. Formation of residual stress on machined surface
图2. 加工表面残余应力形成
因此,材料表层产生的塑性变形和热变形主要受刀刃钝圆处与后刀面力的作用,零件受到正压力和摩擦力,材料表层产生塑性变形,导致材料表层温度升高,产生热形变 [8]。加工的整个过程使切削区域产生不均匀应力场和应变场,热力耦合现象对材料原有内应力影响很大。
3. ABAQUS仿真实验
3.1. 初始网格划分及网格自适应重划分
3.1.1. 初始网格划分
在Machining模块中,选择相对网格尺寸方法直接指定生成的网格数量和网格尺寸比,程序自动确保在切削刃附近生成相对密集的网格。采用绝对网格尺寸法直接指定工件初始网格划分的最小网格尺寸和网格尺寸比,程序会在曲率较大的轮廓边缘自动生成较密集的网格。
划分网格时,选择“System Defined”系统定义方法,通过组合权重因子(Weighting Factors)和网格窗口(Mesh Window)来控制网格大小。分别设置边界曲率权重因子、温度权重因子、应变权重因子和应变率权重因子,在划分初始网格时,程序将在曲率较大的区域生成高密度网格,在自动重绘网格时,在温度、应变和应变率梯度较大的区域始终保持高密度网格。当网格窗口功能被激活时,可以使用多个网格窗口来控制局部网格密度,并使网格窗口跟随工具移动,如图3所示。
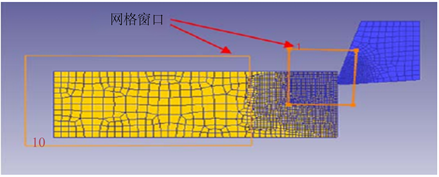
Figure 3. Weight factor and mesh window control of local mesh density
图3. 权重因子与网格窗口控制局部网格密度
3.1.2. 网格自适应重划分
金属切削是一个典型的大变形问题。随着切削的进行,与刀具接触的网格严重变形,在执行等参变换时导致雅可比行列式(Jacobian)为零或负值,使得计算难以进行 [9]。网格变形也会导致工具嵌入材料中,这与实际情况不一致,使解决方案无法实现。因此,对于复杂的大变形问题,有限元程序必须在网格变形到一定程度时停止计算,并在新网格生成后继续计算。
自适应网格重划分需要注意以下两点:
1) 对象的几何边界特征。这些问题主要表现在为了更好地实现逼近,应该在几何边界曲率较大的区域划分更多的网格。
2) 字段变量的梯度。这类问题主要表现在应力梯度、应变梯度和温度梯度等较大区域应划分更多的网格,以保证后续插值计算的准确性。
DEFROD-3D生成的单元都是具有四个节点的四面体单元,而DEFORM-2D生成的单元都是具有四个节点的四边形单元。根据干涉深度标准(包括绝对和相对标准),在切割过程中有四个标准触发网格重新划分:
1) 基于干涉深度准则(包括绝对和相对两种);
2) 基于最大行程增量准则;
3) 基于最大时间增量准则;
4) 基于最大步长增量准则,以上准则可以单独或同时使用。
本文选择了自适应网格重划分的第一和第四准则。由于局部网格重分区比全局网格重分区具有更小的插值误差和更高的求解效率,所以选择局部网格重分区。根据生成的应变钻杆测试。可以看出,该程序在高应变梯度区域自动划分精确网格。将生成的Local Remeshing文件中的以下语句进行FURTHER_IMPROVE_CONTACT_ELEMENTS的取值有0改为1即可实现接触区域扭曲网格的重划分,如图4所示。
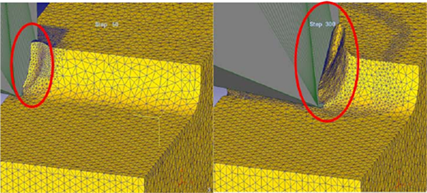
Figure 4. In the process of cutting the adaptive mesh division
图4. 切削过程中自适应网格重划分
3.2. 切削模型中的边界条件和接触定义
在切削加工仿真模型中,将未变形切屑、分离线、工件基体以及刀具按顺序位置安装。为了实现切削过程,固定工件基体x,y方向的位移和转动,同时约束未变形切屑和分离线左侧的位移以及转动,在刀具上定义参考点,将刀具的运动施加在参考点上,约束刀具垂直方向的位移和转动,定义刀具沿着x轴的反方向运动 [9]。除了位移速度边界条件外,对刀具和工件表面施加温度边界条件,使其初始温度为20℃。为了实现JC本构模型中定义的材料失效准则,需要在模型中定义三个独立的接触对,如图5所示,分别定义为分离线与工件基体之间的接触对1,未变形切屑与刀具前刀面的接触对2,已加工表面和刀具后刀面的接触对3,通过这三个接触对实现切削过程中的摩擦定义和加工中的切削热生成和耗散,如图5所示。
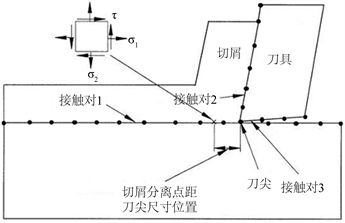
Figure 5. Definition of contact pairs in orthogonal metal cutting
图5. 金属正交切削中的接触对定义
3.3. 切削温度和切削力分布
如图6(a)、图6(b)为加工时的应力分布图,材料在第一变形区和主剪切区内受刀具的挤压,产生塑性形变。由图6(b)所示,最大压力存在刀尖位置,刀尖前部应力等值线互相平行且从剪切带开始依次降低。切削热的产生主要受材料塑性变形做功和刀屑摩擦生热的影响,刀具最高温度位于刀尖一定距离的切削刃上。
(a) 云纹图 (b) 等值线图
Figure 6. The stress distribution of cutting process
图6. 切削过程应力分布图
由图7所示的压应力分布图可以看到,主切削区中的应力主要表现为压应力即径向力,证实了切削力主要表现为径向力。
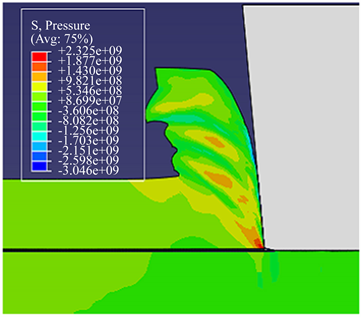
Figure 7. Turning radial force distribution
图7. 车削径向力分布图
3.4. 细长轴车削残余应力预测公式
切削细长轴时,会引起很多的热量,而一些热量将被刀具传递给工件而消失,导致接触区域温度比较高,在研究切削热问题时,可以把以刀具作为热源。细长轴在车削时受到的切削力可以分为Fp、Fc、Ff,其中径向力Fp对尺寸误差影响最大3。切削力和切削热互相影响,产生残余应力,引起材料表面塑性形变,从而导致细长轴的尺寸误差。
3.4.1. 残余应力正交实验模拟结果和分析
仿真实验选择三因素三水平的正交实验方案 [10],选择不一样的Vc、f、ap三个因素,对残余应力进行方差分析,按照回归法推导公式,继而推出了残余应力的预测公式 [10]。模拟所采用的实验方案如表1。
为了确保试验初始条件的相同,模拟结果选用了细长轴加工完成时,最外表面的残余应力有效值,具体数据表2如下:
通过三因素三水平正交实验,Vc、f、ap三个因素对刀具温度影响依次递减,对径向力影响依次递增。残余应力是受车削时的力和热互相作用产生的,径向力对残余应力的影响比刀具温度大,因此,在三因素正交实验中,径向力对残余应力的影响比较显著。
3.4.2. 残余应力误差预测公式
因为在主轴夹紧、顶针顶紧辅助跟刀架下车削时,如果刀具不变,那么可以通过调整切削参数来改变残余应力大小。假定该经验公式为:
(14)
C——固定系数;
——是
的指数。
公式(14)两边取对数得:
(15)
或者
(16)
式中,
,
,
,
,
。
可以看出式(15)可以转变为式(16),这时候,经验公式就变形为一个多元线性方程,可以通过多元方程求出
和
值,其中
。即
,因变量用y表示,总共进行了9组模拟。
建立多远线性方程如下:
(17)
上式可用矩阵表示为:
(18)
其中:
,
,
,
。
采用最小二乘法估计参数
,设
分别是参数
的最小二乘估计,则回归方程为:
(19)
其中
为统计变量。则有:
(20)
由回归参数的最小二乘法估计得:
(21)
式中,X'是X的转置矩阵,
是
的转置矩阵,其中,
。
按照最小二乘法,创建残余应力的预测公式。表2中的切削参数分别取对数建立细长轴的数学回归模型,可得,
,
。
将向量X,Y代入公式(20)可得:
。
将公式(21)带入(19)可得线性方程:
(22)
最后得到合金材料的残余应力经验公式表达如下:
(23)
残余应力
带来的径向应变为
,所以由切削时热和力变化而引起的径向位移量,
(24)
在车削时产生的力和热相互作用产生残余应力,残余应力使材料表面发生形变,影响细长轴尺寸误差。
(25)
U——泊松比;
E——弹性模量;
r——细长轴直径;
——残余应力;
ap、Vc、f——背吃刀量、切削速度、进给速度。
联立式(23)和式(24)得出式(25),推导出相关细长轴直径、泊松比、弹性模量、切削三要素的残余应力误差预测公式。
4. 搭建细长轴车削实验
(1) 机床条件:数控机床CKA 6150车床。
(2) 工件:细长轴的
,
。
(3) 刀具:硬质合金刀片,主偏角
,前角
,刃倾角
,后角
,刀具线膨胀系数为5 × 10−6,悬伸长20 mm。
(4) 测量设备:YDC三向压电测力仪,FLIRA20红外热像仪,如图8所示。
4.1. Vc对刀具温度和径向力的影响
在进给速度f、被吃刀量ap恒定的情况下,研究选用不同的切削速度Vc对实际加工中的刀具温度T和径向力Fp的影响,实验结果如表3所示。
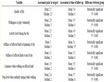
Table 3. Influence of Vc on T and Fp
表3. Vc对T和Fp的影响
注:所测是已加工表面形成瞬间的前刀面最高温度和切削力。
如图9所示,Vc的升高导致切屑变多,材料表面产生的塑性形变做功增多,塑性变形做功转化成的热量也变多,引起加工区域热量变多和刀具温度提高,加工表面软化,导致作用在材料表面的切削力下降。同时,加工速度变快之后同样也使切屑的流出速度上升,切屑吸收部分热量,引起T不会快速上升。所以,T和Vc呈线性关系,但并非成倍升高,Vc对T和Fp影响显著。
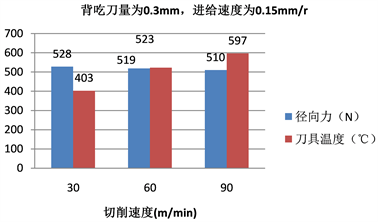
Figure 9. Relation diagram of Fp and T at constant ap and f
图9. ap、f恒定时Fp与T关系图
4.2. f对刀具温度和径向力的影响
在切削速度Vc、被吃刀量ap恒定的情况下,研究选用不同的进给速度f对实际加工中的刀具温度T和径向力Fp的影响,实验结果如表4所示。
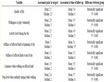
Table 4. Influence of f on T and Fp
表4. f对T和Fp的影响
如图10所示,随着f的升高,切屑增多但切屑的塑性形变变小,变形功转化的热量减少,两者综合影响,导致切削区域的T提高变慢。加工区域温度提高变慢,导致加工表面软化不明显,切削力降低不明显。因此,f对T和Fp的影响小于Vc。
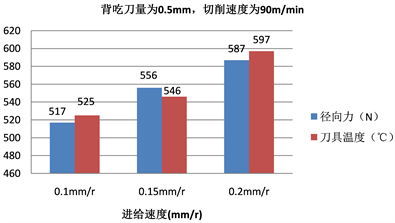
Figure 10. Relation diagram of Fp and T at constant Vc and ap
图10. Vc、ap恒定时Fp与T关系图
4.3. ap对刀具温度和径向力的影响
在切削速度Vc、进给速度f恒定的情况下,改变车床的背吃刀量ap,研究选用不同的ap对实际加工中的刀具温度T和径向力Fp的影响,实验结果如表5所示。
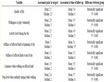
Table 5. Influence of ap on T and Fp
表5. ap对T和Fp的影响
如图11所示,随着ap的增大,切削刃参与切削的尺寸变长,更易于散热,T上升变小,加工表层硬化,切削过程进行,导致Fp增大。因此,ap对Fp的影响大于T,且和Fp变化呈正相关。
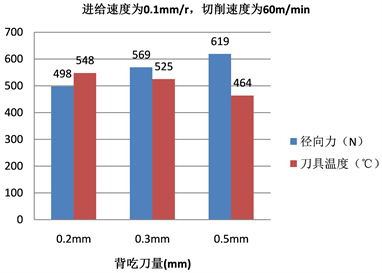
Figure 11. Relation diagram of Fp and T at constant Vc and f
图11. Vc、f恒定时Fp与T关系图
4.4. 仿真值和实验值对比分析
在切削三要素中的Vc、ap、f分别为30 m/min、0.3 mm、0.15 mm/r时,刀具温度T和径向力Fp仿真和实验值对比如表6所示。
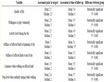
Table 6. Comparison of simulation and experimental values under the same three cutting elements
表6. 相同切削三要素下仿真和实验值对比
在切削三要素中的Vc、ap、f分别为60 m/min、0.3 mm、0.1 mm/r时,刀具温度T和径向力Fp仿真和实验值对比如表7所示。
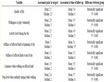
Table 7. Comparison of simulation and experimental values under the same three cutting elements
表7. 相同切削三要素下仿真和实验值对比
在切削三要素中的Vc、ap、f分别为90 m/min、0.5 mm、0.1 mm/r时,刀具温度T和径向力Fp仿真和实验值对比如表8所示。
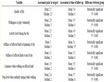
Table 8. Comparison of simulation and experimental values under the same three cutting elements
表8. 相同切削三要素下仿真和实验值对比
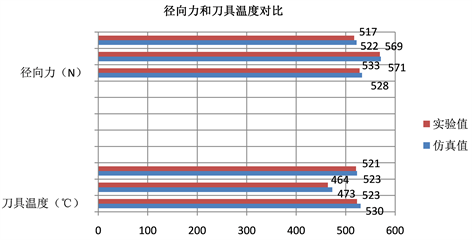
Figure 12. The experiment and the simulation of radial force and the cutting tool temperature numerical comparison
图12. 实验和仿真中径向力和刀具温度数值对比
如图12所示,在3组相同的切削参数下,仿真和实验得到的T、Fp数值基本一致。切削力和切削热的相互影响产生残余应力,通过前文分析得出,切削力主要受Fp影响,切削热主要在刀具上,因此,车削产生的力和热可以利用测力仪、热像仪分别收集径向力Fp、刀具温度T的测量数据得到,而径向力、刀具温度主要受Vc、ap、f影响。通过设置相同的切削参数,得出仿真和实验的刀具温度T、径向力Fp数值基本一致性,验证了残余应力预测公式。
5. 小结
本文从细长轴的误差来源出发,研究了热力耦合下细长轴车削产生的残余应力对尺寸误差影响。通过对国内外相关文献的分析,得出细长轴在车削时受到的热和力相互作用产生残余应力,引起零件发生塑性形变和热形变。车削时受到的力主要表现为径向力,受到的热集中在刀具上,可以把刀具作为热源。利用ABAQUS软件分析了热力耦合下车削过程,得到切削三要素中Vc、ap、f对径向力Fp和刀具温度以及残余应力的影响,推导出残余应力误差公式。进行车削实验验证残余应力误差公式,在主轴夹紧、顶针顶紧,辅助跟刀架下车削细长轴,利用YDC三向压电测力仪和FLIRA20红外热像仪采集径向力和刀具温度数据并对比分析,验证了仿真中Vc、ap、f对Fp和刀具温度的影响以及残余应力误差公式的正确性。通过本文研究,得出以下结论:
1、在主轴装夹,顶针顶紧外加跟刀架下,研究热力耦合下细长轴车削产生的误差可以简化为研究径向力Fp和刀具温度T。细长轴在主轴夹紧、顶针顶紧辅助跟刀架下车削,车削时的热和力相互作用产生残余应力引起尺寸误差。此时,切削力主要表现为径向力Fp,切削热主要集中在刀具,可以把刀具看做热源。
2、利用多元线性回归法得出细长轴残余应力预测公式
,误差公式
。径向力、刀具温度主要受Vc、ap、f影响,通过对比相同的切削参数,
得出仿真和实验的刀具温度T、径向力Fp数值基本一致性,验证了残余应力误差公式正确性。
3、T和Vc呈线性关系,但并非成倍升高,Vc对T和Fp影响显著。f对T和Fp的影响小于Vc。ap对Fp的影响大于T,且和Fp变化呈正相关。在切削三要素中,Vc、ap、f对刀具温度的影响依次递减,对Fp的影响依次递增。当Vc增加时,切屑生成量变多,塑性变形功转化的热量变多,切屑底层与前刀面摩擦生热加快,导致刀具温度提高显著。当f增加时,切屑增多,刀屑摩擦剧烈,摩擦热增多但切屑流出速度也增大,带走部分热量,导致刀具温度升高变缓慢。当ap增大时,切削刃长度增加,散热改善,刀具温度上升变少,导致加工表面硬化使得切削力增大。
参考文献