1. 引言
随着节能减排逐渐成为工业社会发展的大势所趋,汽车由于其结构重量对燃油经济性的影响,其轻量化研究得到了广泛重视和发展。重型牵引车作为一种重要的生产资料,每年消耗大量能源,因此重型牵引车的轻量化研究意义重大,不仅提升了燃油经济性和产品竞争力,更为重要的是减少了排放和能源消耗 [1]。
目前,国内外众多单位和学者针对重型牵引车开展了一系列研究,并取得了一定的可借鉴成果。Dannbauer H [2] 对轻型车车身、车架上的焊接点数量、尺寸等采用有限元手段,不仅提升疲劳可靠性,还有效实现了轻量化。L Gui、CA Zhou [3] 对某工程车车架进行有限元建模和分析,结合分析结果并提出了轻量化设计方案,并通过有限元分析证明轻量化车架结构强度满足设计要求。江西五十铃汽车公司邓斌 [4] 等采用ABAQUS软件,对某商用轻卡玻璃纤维板簧方案进行了结构优化设计,同时对轻量化后的板簧方案进行有限元强度分析,轻量化效果显著。陕汽公司张婷婷 [5] 等从重型商用车轻量化概念以及方法,并以整车各系统为例,阐述了轻量化在重型商用车上的发展与应用,为整车轻量化方案提供了一些参考。合肥工业大学柏林 [6] 利用HyperWorks软件有限元分析手段,对某载货车车架进行静态分析,并进行拓扑优化设计研究,有效地改进了车架结构。湖南大学刘威 [7] 对华菱公司某载货车车架进行分析研究,首先收集总结车架典型受力情况,进行有限元模型强度分析,完成设计方案改进,然后通过实车试验,验证了整车可靠性,同时充分验证了车架结构的可靠性和耐久性。合肥工业大学王启栋 [8] 提出一种考虑疲劳性能要求的集拓扑优化与尺寸优化于一体的车架轻量化设计方案,在满足疲劳性能要求、保证车架安全性能的同时,减轻了车架的重量。南京航空航天大学张凯成 [9] 等对商用车车架进行多工况轻量化优化设计,建立有限元模型并进行自由模态分析和4种典型工况的静态分析,并对4种典型工况下的车架同时进行尺寸和材料的优化。
本文主要针对某6X4重型牵引车轻量化车型开展轻量化设计研究,对整车状态下,车身、动力总成、车架等底盘系统进行详细研究,形成整车轻量化方案,通过CAE以及道路行驶可靠性试验等手段验证轻量化方案的可行性。
2. 某重型牵引车车架几何模型及有限元模型建立
2.1. 牵引车车架几何模型
本文的研究车型是高速物流用牵引车,作为主流的重型牵引车,其车架采用前宽后窄的梯形结构,包括第一横梁、变速箱后横梁、几型横梁、鞍座连接板、后悬架横梁、后横梁等,其几何模型如图1所示,相关尺寸参数如表1所示。
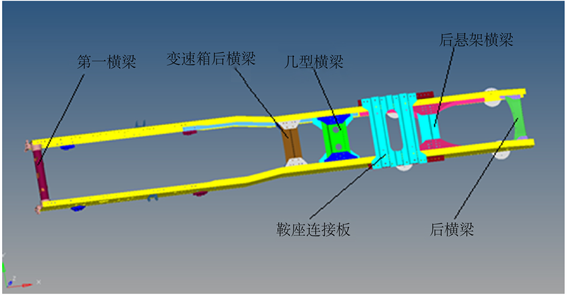
Figure 1. Geometric model of tractor frame
图1. 牵引车车架几何模型
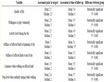
Table 1. Frame related dimension parameters
表1. 车架相关尺寸参数
2.2. 牵引车车架有限元模型
将车架CAD模型转化成IGS格式,由有限元软件HyperWorks/HyperMesh直接调用,进行车架的中面抽取和网格划分。车架结构采用壳单元模拟,各悬置、悬架块状支架采用四面体单元模拟,所有焊接、铆接和螺栓连接采用刚性体单元及梁单元模拟。同时,为模拟整车状态下车架受力的更真实情况,将与车架连接的受力较大的各系统支架附件进行有限元建模,以便于后续强度、刚度分析时在支架上加载。处理完成后的有限元模型如图2所示,网格单元平均尺寸为40。
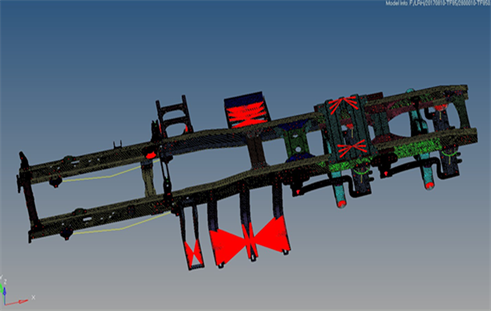
Figure 2. Finite element model of frame with bracket attachment
图2. 带支架附件的车架有限元模型
3. 基于OptiStruct的车架拓扑优化设计
3.1. 拓扑优化基模型设定
本文采用HyperWorks/OptiStruct优化模块对车架结构进行拓扑优化,不同的基模型与优化设计区域划分,都会造成拓扑优化结果的较大差异,一般情况下,要经过不同的尝试,才能得到比较合理的拓扑优化结果。重型牵引车车架的作用是支撑整车底盘以及加载在鞍座上的挂车鞍载,其承载能力主要取决于纵梁腹高等纵梁截面参数,作为主要承载部分,车架纵梁及纵梁加强梁作为非优化设计区域。另外,重型牵引车匹配大马力发动机和变速箱,其一般布置在车架总成前端内部,具体在第一横梁后至第二横梁中间,故布置发动机和变速箱动力总成的区域也作为非设计区域。两纵梁内部的其他大部分区域作为设计区域。经过大量的拓扑优化尝试,以及对产生的不同结果进行比较,最终基模型与优化设计区域划分如图3所示。
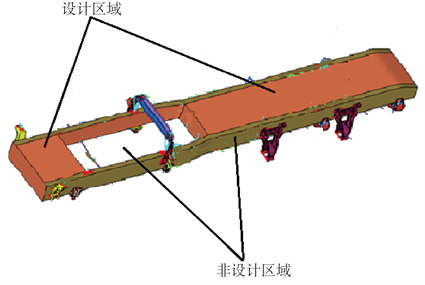
Figure 3. Topology optimization base model and design area division
图3. 拓扑优化基模型及设计区域划分
3.2. 拓扑优化模型边界约束条件设定
根据重型牵引车复杂的实际使用工况和车架受力状况,设置拓扑优化工况约束、工艺约束以及载荷约束。
(1) 工况约束。即创建典型工况下的车辆约束情况,重型牵引车的车架受载工况一般可简化包括:弯曲工况、弯扭工况、弯扭加转弯工况、制动工况等四种工况,其中以汽车在凹凸不平路面行驶时的弯扭工况以及在弯道上行驶受到离心力作用时的弯扭加转弯工况对车架的载荷冲击最恶劣。具体的工况约束情况如图4所示,弯曲工况:约束一二三轴轮心位置;弯扭工况:约束一二三轴轮心位置,在一轴两侧加强制位移约束,模拟扭转状态;弯扭加转弯工况:约束情况同弯扭工况,增加了侧向载荷;制动工况:在弯曲工况约束的基础上,约束一二三轴前后方向位移。
(2) 工艺约束。不能加工制造成为实物的设计,就不能为人类所用于生产生活,也就没有任何实际意义。为提高拓扑后车架制造工艺性,本文分别设置成员尺寸控制和对称约束两项制造工艺约束。为了保证传递路径上不出现微小结构,无法满足最小材料选用,设置最小成员尺寸将其定义为120 (网格单元平均尺寸的3倍),如图5(a)所示;车架左右两侧受力基本均衡,两侧安装和结构差异不大,故车架纵梁和横梁采用对称结构。为提高制造生产效率,简化生产模具,降低工艺成本,设置对称约束如图5(b)所示。
(a) 弯曲、弯扭、弯扭加转弯工况约束
(b) 制动工况约束
Figure 4. Working condition of constraint
图4. 工况约束
(a) 最小成员尺寸控制
(b) 对称约束
Figure 5. Process constraint
图5. 工艺约束
(3) 荷约束。整车状态下,驾驶室、动力总成重心和重量、附件系统重量以及鞍载重量如表2所示。驾驶室、发动机和变速箱等重量按照其重心位置,分配到驾驶室悬置和动力总成悬置上。底盘附件,包括油箱、尿素罐、电瓶框、EGP、储气筒等重量直接加载在其相应的支架上。
设置拓扑优化工况约束、工艺约束以及载荷约束等边界条件后,得到的拓扑优化加载模型如图6所示。
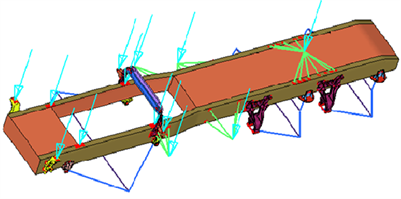
Figure 6. Topology optimization loading model
图6. 拓扑优化加载模型
3.3. 拓扑优化要素设定
拓扑优化设计的要素主要有:1) 设计变量:单元的材料密度,即设计区域内各单元的材料密度;2) 约束函数:体积分数为0.3,即保留材料为拓扑优化基模型的30%;3) 目标函数:多工况下应变能最小,应变能与刚度成反比;4) 响应:体积分数和多工况应变能,即其分别对应约束函数和目标函数。
4. 拓扑优化计算结果及分析
设置工况、工艺及载荷约束,并定义拓扑优化设计要素后,利用OptiStruct进行优化计算,经过28次迭代后收敛,得到拓扑优化结果云图如图7所示。蓝色区域的材料密度值接近0,表示可除大部分材料;红色区域的材料密度值接近1,表示结构需保留区域;其它颜色区域为中间区域,表示可去除部分材料。
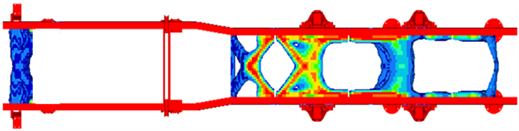
Figure 7. Cloud map of topology optimization results (Isosurface map)
图7. 拓扑优化结果云图(等值面图)
车架在弯曲工况和扭转工况以及匝道工况等典型工况下的综合受力状态和力的传递路径在拓扑结果上比较明显,根据受力路径,结合车架设计经验和制造工艺,避开车架常见的危险部位,优化车架结构。本文中将作为主要承载部分的纵梁区域设定为非拓扑优化设计区域,即原车架纵梁部分保留只对其中间多个横梁进行优化。
根据拓扑优化结果云图:1) 车架第一横梁云图虽然以蓝色为主,但拓扑保留的材料面积较大,故本设计选择第一横梁保持原有扭转刚度较大的圆管梁,保持不变;2) 车架上变速箱后横梁和几型横梁区域内,材料红色区域比较集中。在扭转工况和扭转+转弯工况下,车架中部承受扭转角较大。对于变速箱后横梁,传统设计认为该横梁必须是强度较大结构,但该处蓝色区域较多,结合实际生产工艺考虑,该处选择单片槽型梁。对于几型横梁,拓扑云图所示为“X”型横梁结构,但是因车型布置原因,几型横梁上不仅要布置管线、阀体支架等,且“X”型横梁制造困难不利于工艺降本,还影响几型横梁附件储气筒的布置和其下方传动轴的通过性,故几型横梁选择沿用原横梁结构形式,其横梁本体和连接板尺寸上减小进行优化;3) 后悬架横梁云图以蓝色为主,结合实际使用情况,该处受到较大扭转力,且该处受到鞍载集中载荷的作用,故该处横梁采用原结构形式、连接板尺寸减小;4) 后横梁云图为蓝色,区域面积较小,车架尾部受力较小,此部位安装部件较少,局部刚度要求不高,初步判断后横梁采用铝合金材料代替,以实现减重目标。如图8所示为车架轻量化设计前后的几何模型。
(a) 原车架几何模型
(b) 车架轻量化设计后几何模型
Figure 8. Frame lightweight design before and after geometric model
图8. 车架轻量化设计前后几何模型
结构和尺寸具体优化设计如表3所示。
5. 有限元强度对比分析
强度是权衡车架性能的重要指标,对拓扑优化设计后的车架进行强度分析,如发现不满足设计要求的薄弱部位,通过结构调整或材料提升等方式加强,使车架本身坚实可靠。首先,最大应力应小于材料的屈服强度,并预留一定的安全系数,对于车架通常下预留1.5的安全系数。其次,对于应力值接近1.5倍安全系数限值的部位,要和现有结构相应部位比较,应力不得超出现有成熟结构中应力的20%,以排除后续风险。其中,纵梁材料为DL750,屈服强度为700 MPa;各横梁和连接板材料为DL600,屈服强度为455 MPa,铝合金6061-T6材料屈服强度为245 MPa。
对原车架和拓扑优化轻量化后的车架进行有限元强度分析是考验新车架优化效果的第一步。在分析过程中采用相同载荷以及约束情况,如图9所示,得到的车架应力情况整理如表4所示。
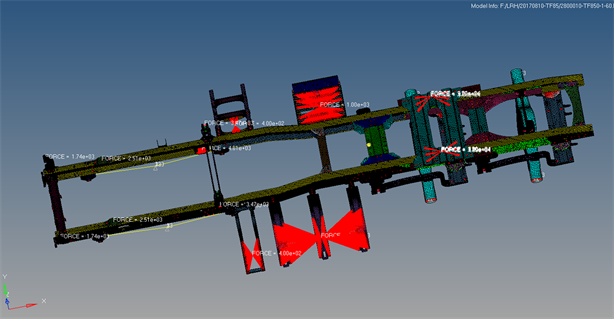
Figure 9. Frame finite element loading diagram with bracket attachment
图9. 带支架附件的车架有限元加载图
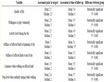
Table 4. Distribution of the maximum stress (MPa) of the frame
表4. 车架最大应力(MPa)分布情况
1) 纵梁:轻量化设计前后的车架纵梁在弯扭、弯扭加转弯两种较恶劣工况下的应力云图如图10、图11所示。弯扭和弯扭加转弯工况下车架轻量化更改前后右纵梁应力增大明显,变化率分别为21%和30%,但是其应力绝对值327.8 MPa和311.2 MPa小于DL750考虑1.5倍安全系数后的许用限值466 MPa,较为安全。
(a) 原车架
(b) 轻量化后车架
Figure 10. Frame rail stress cloud diagram under bending-torsion condition
图10. 弯扭工况下车架纵梁应力云图
(a) 原车架
(b) 轻量化后车架
Figure 11. Frame rail stress cloud diagram under bending, twisting and turning conditions
图11. 弯扭加转弯工况下车架纵梁应力云图
2) 横梁和连接板:第一横梁、后悬架横梁、后横梁,其横梁和连接板在车架轻量化前后,应力变化幅度较小,说明轻量化方案对第一横梁、后悬架横梁、尾横梁强度影响较小。从表中分析,此三根横梁在弯扭工况下表现出应力最大状态,以下列出该三根横梁弯扭工况下车架优化设计前后应力云图对比情况,如图12~图14所示。从强度分析结果看,改进前后变速箱后横梁连接板应力值均偏大,且A车架(原车架)变速箱后横梁连接板强度方面存在较大风险。变速箱后横梁连接板在轻量化设计后,弯扭和弯扭+转弯工况下应力显著下降,但其应力绝对值372 MPa仍较大。根据轻量化设计后应力情况,改用DL750材料,安全系数可达到1.88,改进了原设计的缺陷。
3) 几型横梁:几型横梁优化设计,是将横梁和连接板的翼面宽度同时减小80 mm。在四种工况下,几型横梁本身应力有所下降而横梁连接板应力有不同程度上升,应力云图如图15、图16所示,说明横梁和连接板翼面减小相同幅度时,横梁较连接板受力更为敏感,应力峰值迅速转移到连接板上。
(a) 原车架 (b) 轻量化后车架
Figure 12. Stress cloud diagram of frame first beam under bending-torsion condition
图12. 弯扭工况下车架第一横梁应力云图
(a) 原车架 (b) 轻量化后车架
Figure 13. Stress cloud diagram of rear suspension beam under bending-torsion condition
图13. 弯扭工况下车架后悬架横梁应力云图
(a) 原车架 (b) 轻量化后车架
Figure 14. Stress cloud diagram of rear beam of frame under bending-torsion condition
图14. 弯扭工况下车架后横梁应力云图
(a) 原车架 (b) 轻量化后车架
Figure 15. Body stress cloud images of several frame beams under four working conditions
图15. 四种工况下车架几型横梁本体应力云图
(a) 原车架 (b) 轻量化后车架
Figure 16. Stress cloud diagram of several beam connecting plates of the frame under four working conditions
图16. 四种工况下车架几型横梁连接板应力云图
6. 整车道路可靠性试验
汽车道路可靠性试验是通过整车道路试验来诱发产品的故障和缺陷,并在这个过程中找出产品的薄弱环节进行加强和改进。为了提高研发效率缩短试验周期,道路可靠性试验中选择的路况都是集中的各典型路面,如山区路、卵石路、搓板路、高速环道等。根据轻量化设计方案试制完成三台样车,进行全程34000 km的可靠性试验,考核在原车型基础上重新设计零部件以及轻量化设计的车架总成、发动机变速箱及其他系统轻量化零部件的可靠性和耐久性。制定试验方案如下:
本车型全面轻量化优化改进后,结合本车型自身特点,考虑市场上主流牵引车耐久性里程,以及所选试车场内各种路况和试验资源,制定该车型试验大纲,其中包括高速环道、山区公路、环路工况、工况行驶。主要项目和行驶里程如表5所示,各试验项目道路情况示意如图17所示。
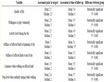
Table 5. Road reliability test project
表5. 道路可靠性试验项目
(a) 高速环道
(b) 山区公路
(c) 坏路工况
(d) 常用工况
Figure 17. Schematic diagram of road condition of test project
图17. 试验项目道路情况示意图
1) 高速环道:路面平整,水泥混泥土铺装,试验中以100~110 km/h车速验证,考察高速时连续运转的可靠性。发动机、变速箱、传动轴等高速旋转件,是否存在渗漏和异响等,高温条件下发动机冷却、润滑剂的可靠性。
2) 山区公路:水泥混泥土和砂石铺装路面,考核整车的制动系统,验证制动系统匹配是否合理性、是否存在疲软,制动器摩擦片及制动鼓的耐磨性能、制动器抗热衰退性。
3) 坏路工况:按各种凹凸不平的特征强化后的路面组合的路面,主要针对整车承载系统、行驶系、传动系在极端工况下的可靠性,验证其强度和刚度。
4) 工况行驶:国道省道等等级公路路面,试验中以50~60 km/h车速验证,考察行驶的平顺性、燃油经济性、操控稳定性。
试验评价是整车试验的重要的一环,整车可靠性试验评价,一般按照平均故障间隔里程(MTBF)和可靠性试验综合扣分数(Q)两个指标来评价。可靠性故障分类及扣分标准如表6所示,试验项目数据统计结果,如表7,表8所示。
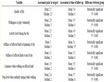
Table 6. Deduction standard for reliability fault classification
表6. 可靠性故障分类扣分标准
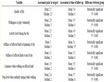
Table 8. Total mileage and time of test sample vehicles
表8. 试验样车总里程及时间
根据经验标准指标,其中MTBF指标为大于400 km,Q指标为小于950。
MTBF = t/r (1)
式中,t为试验样车行驶总里程,km;r为故障次数(不含二次故障和四类故障)。
(2)
式中,Q为综合评定扣分数;n为试验样车数量,3;rj为发生第类故障数;qkj为每个第类故障的扣分数,如表6所示。
由表7、表8可得:
样车1:t = 34512,r = 66,MTBF = 522 km;
样车2:t = 34515,r = 63,MTBF = 548 km;
样车3:t = 34530,r = 73,MTBF = 473 km。
由表6可得:
样车1:Q1 = 925;样车2:Q2 = 810;样车3:Q3 = 875。
根据以上两项分析三台试验样车,平均故障间隔里程(MTBF)和可靠性试验综合扣分数(Q)两个指标均满足试验标准,整车可靠性通过。同时,对试验过程中产生的螺栓故障进行了分析并采取对应的加强措施,形成了量产的永久方案。
7. 结论
本文基于生产实际与拓扑优化的理论,采用结构优化、尺寸优化以及高应力部位改用高强度材料局部加强的方法,形成了车架轻量化方案。并对轻量化前后车架有限元强度分析对比、轻量化后车架进行多工况道路试验,验证了车架轻量化方案的可行性。车架轻量化方案实现降重65 Kg,较原方案减重7.7%,减重效果显著。本文轻量化设计研究分析方法为后续轻量化新车型的开发提供了借鉴。