1. 引言
装配式建筑作为建筑工业化的一种形式,已在许多国家和地区得到广泛推广及应用 [1]。与传统的建筑模式相比,装配式建筑具有施工效率高、节约资源、改善施工现场条件、减少建筑垃圾等优点 [2] [3]。但是,当预制构件的供应链管理不当时,预制构件容易出现提前或延迟交付的问题,使得装配式建筑不能发挥其全部优势 [4]。除此之外,由于目前预制构件的生产过程存在标准化程度不高、构件信息提取不准确、设计和生产脱节等问题,预制构件的质量较差,返工现象十分严重 [5]。预制构件供应链管理呈现出与快速增长的装配式建筑市场完全不协调的发展态势,制约着企业和相关技术的进一步发展,引起大量学者的关注和研究 [6]。预制构件的生产调度就是其中最为关键的决策之一 [7]。为此,一些学者从算法优化和模型改进方面对上述问题开展了研究。
在算法优化方面,Chan等 [8] 提出了预制构件生产的流水作业排序模型,并使用遗传算法进行求解。Chan等 [9] 优化了文献 [8] 中提出的流水作业排序模型,并使用改进的归一化的加权遗传算法对模型进行求解。Li等 [10] 建立了以优化预制构件总生产成本为目标的生产调度模型并结合分支定界法和遗传算法进行求解,该模型中考虑了模具数量、工时、工作空间等的影响。Yang等 [11] 研究了多条生产线下的预制构件生产调度问题,并提出改进的遗传算法对所建立的优化模型进行求解。Kong等 [12] 研究了预制构件的生产、运输和组装的集成调度问题,并开发了一种动态编程算法对问题进行求解。
在模型改进方面,Leu等 [13] 系统梳理了预制构件的生产过程,研究了带有资源限制的混合生产流水车间调度系统。Khalili等 [14] 开发了一个混合整数线性规划模型以采用合适的模具并创建最佳生产调度计划,该模型可有效降低预制构件生产总成本。Liu等 [15] 研究了预制构件生产和运输的集成调度问题,并具体讨论了时间窗、车队规模等因素对集成调度的影响。Wang等 [16] 从整个预制构件供应链的角度出发,改进了传统的生产调度模型,新的模型中考虑了模具制造、构件存储以及运输对构件生产调度的影响。Wang等 [17] 系统地考虑了人为因素对预制构件生产计划安排的影响,填补了人为因素对生产影响方面的研究空白。Ma等 [18] 研究了多生产线环境中预制构件的生产调度问题并建立对应的流水车间排序模型,该模型可避免大量物料的重新分配。Kim等 [19] 研究了施工进度不确定情况下的构件生产调度问题,建立了构件生产调度的动态规划模型,模型中采用离散时间仿真方法来模拟构件交付日期的变化。Jiang等 [20] 研究了生产能力有限情况下预制构件订单的接受和调度问题,建立以利润最大化为目标函数的随机多订单调度模型,并提出启发式算法对模型进行求解。Du等 [21] 研究了需求动态波动情况下预制构件的多目标调度问题,针对该问题所建立的模型中考虑了交付日期提前、订单取消以及紧急订单插队等需求波动的情况,并提出遗传算法对问题进行求解。
综上所述,已有文献对预制构件生产调度的研究存在以下不足:1) 针对预制构件生产调度的研究没有考虑构件返工的影响,造成计算的生产完成时间比实际情况要少,生产计划的准确性大大下降;2) 针对预制构件生产调度问题的研究大多集中于单个订单、单条生产线的生产计划排布,很少有针对多订单、多生产线的预制构件的调度问题开展的研究,导致相关研究在理论意义和现实应用中都存在较大局限;3) 针对预制构件生产调度的研究通常未考虑BIM的影响,而BIM正逐渐广泛应用于预制构件的生产中并对预制构件的生产调度产生复杂影响。针对以上不足,本文系统梳理了预制构件的生产调度过程和特点,以多订单、多生产线为基本预设生产场景,同时考虑预制构件生产过程中深化设计、信息提取等非生产步骤对直接生产过程的影响以及运输过程中的多种运输方式,引入延期或提早交付罚款,对构件返工和BIM的影响下预制构件的生产调度问题展开研究,为构件生产商在复杂形势下制定更为精确的生产计划、降低供应链总成本以及促进构件的准时交付提供理论支持。
2. 理论基础与模型假设
2.1. 构件返工对构件生产的影响
区别于一般流水线产品,预制构件有其独特的生产流程。预制构件厂接到生产订单后,需要根据每个订单的要求,经过深化设计、构件信息提取、模具制造、模具组装、钢筋设置、混凝土浇筑、养护、脱模、表面处理、自然养护、质检、入库存储、运输一系列步骤,最终完成订单的交付。在以往的研究中,预制构件的生产过程一般不包括深化设计和构件信息提取阶段。然而,深化设计的时间及合理性、构件信息提取的时间及准确性将在很大程度上决定构件的质量进而影响构件的生产调度。当构件通过质检时,将返回之前的某一生产步骤进行修复或重新生产,这将增加构件的生产成本和延长构件的生产时间,进而影响到构件的运输和准时交付,产生额外的运输成本和延期交付成本。同时,随着预制构件工业化生产水平逐渐提高,在实际的构件生产环境中,传统的单生产线、串联生产的生产方式正逐渐被淘汰,多生产线、多订单并行生产逐渐成为主要的生产方式。
2.2. BIM对构件生产的影响
当BIM应用于构件的生产时,其对各步骤的影响如图1所示。在深化设计阶段,利用BIM开发面向构件生产的参数化设计系统,可以在各关键利益相关方之间进行及时的信息交换,增强不同领域设计者之间的沟通效率 [22],在设计阶段即可同步考虑构件的生产要求,使构件具有良好的可制造性,减少后续生产过程中因构件拆分不合理而造成构件难以生产、进而导致构件生产时间增加以及构件质量降低的问题 [23];在构件信息提取阶段,通过BIM建设数据平台,可将承接项目合同、客户、构件信息、模具信息统一到生产平台上,构件信息可通过3D-BIM模型直接传递至生产阶段,准确无误生成物料清单,各部门可通过平台提取所需信息,安排后续工作。模型的导入,降低了传统模式下技术人员通过二维图纸提取构件信息产生错误的概率,既节省了大量的时间,又提高了构件生产的精度,降低了构件返工的概率;在构件的后续生产及运输阶段,通过BIM平台可实现构件质检的信息化,由此可对构件的质量进行全周期可追溯性管理,有利于提高构件的质量并减少返工;除此之外,使用BIM时,由于生产阶段时间缩短,构件厂将能够灵活选择构件的运输方式,如可以选择运输时间较长但费用更低的运输方式来运输构件,降低物流成本。同时,使用BIM会增加一部分成本,该成本可分为固定成本和可变成本,其中可变成本随构件复杂度、数量等的变化而变化。

Figure 1. The influence of building information model on the production of components
图1. BIM对构件生产的影响
2.3. 模型假设
建立模型之前,不失一般性,给出如下合理假设:
1) 构件生产时原材料供应充足,不存在短缺情况。
2) 运输工作由第三方物流公司承担(简称3PL公司),3PL公司有足够的运输能力完成给定的运输工作。
3) 构件在达到可付运条件后,可随时运输,且构件不存在二次返工。
4) 生产调度计划开始时刻设为0时刻,预制构件厂构件堆放场地足够大,不存在堆放场地容量不足限制生产的情况。
3. 问题描述与建模
3.1. 问题描述
基于上文,本文所研究的问题可描述为:构件厂从服务范围内的诸多客户中接受构件生产订单,并按照客户的要求在指定时间将订单中所包含的构件运送到指定位置,如果构件厂提前或延期交付构件,构件厂将按约定数额向客户支付提前或延期交付罚款。每个客户一次可下达一个订单,该订单中包含若干类构件,每类构件称作一个子订单,如第 个订单中的第 类构件称作子订单 。由于各类构件的尺寸、生产工艺、数量不同,因此,其生产时间和生产成本可能不同。
构件厂有若干条生产线生产订单中包含的各类构件,在生产开始前,构件厂会根据子订单的生产工艺为子订单生产安排合适的生产线。构件厂在构件的生产过程中使用BIM,其生产方式为多生产线多订单并行生产,即在生产阶段,所有订单可同时并行生产,但在某一订单中,只有前一个子订单完成生产后,才能开始下一个子订单的生产,任何一个子订单只在某一条生产线上生产。如果某子订单的构件在生产过程中未能通过质检,构件厂将重新生产该构件,这将增加构件的生产成本和生产时间。在运输阶段,构件的运输工作由第三方物流公司完成,有多种运输方式可供选择,不同的运输方式运输时间和运输成本不同,多个订单的预制构件可并行运输。
构件厂需要决定每个子订单在生产线上的生产顺序和生产开始时间,在订单生产完毕并达到付运条件后,构件厂需要决定每个订单的运输时间及运输方式,使预制构件供应链总成本最低。
3.2. 参数与变量定义
决策变量
:子订单ik的生产开始时间;
:订单i的付运时间;
:其值为1表示订单i采用运输方式j进行运输,否则为0。
中间变量
、
、
、
、
、
:分别表示订单i的生产成本(包括构件返工的成本)、储存成本、运输成本、提前交付罚款、延期交付罚款以及使用BIM的成本,其他参数定义如下:
:子订单ik包含的构件数量
:订单i的指定交付日期
:订单i提前交付的日罚款额
:订单i延期交付的日罚款额
I:订单的集合,
J:运输方式的集合,
K:子订单集合,
:构件厂生产子订单ik所需时间
:订单i采用第j种运输方式的运输时间
:子订单ik采用第j种运输方式的单位运输成本
:子订单ik中构件的单位存储成本
:子订单ik的单位生产成本
:子订单ik中构件返工的平均单位修复或重新生产成本
:订单ik中构件返工的平均单位成本/时间与正常生产单位成本/时间的比例系数
:订单i使用BIM时降低构件返工概率的比例系数
f:使用BIM的固定成本
:订单i使用BIM时的单位可变成本,与构件复杂度、体积等有关
:子订单ik的前序子订单
:不使用BIM时预制构件出现返工现象的概率
:使用BIM时预制构件出现返工现象的概率
:子订单ik的生产结束时间
:订单i的可付运时间
:订单i的运输时间
:订单i实际交付日期
:其值为1表示子订单ik的可付运时间未超过指定交货日期,否则为0
:其值为1表示订单i使用了BIM,否则为0
3.3. 数学模型
(1)
(2)
(3)
(4)
(5)
(6)
(7)
(8)
(9)
(10)
(11)
(12)
(13)
(14)
目标函数式(1)为最小化供应链总成本,包括订单的生产成本、储存成本、运输成本、提前交付罚款、延期交付罚款以及使用BIM的成本。式(2)表示订单生产成本的计算,在该式中通过引入构件返工的成本以及使用BIM时构件返工概率的改变来描述构件返工和BIM对构件生产过程的影响。式(3) (4) (5) (6)分别表示订单储存成本、运输成本、提前交付罚款、延期交付罚款的计算,同生产成本的计算类似,在上述成本的计算中也考虑了构件返工和BIM的影响。式(7)表示使用BIM成本的计算,该成本包括固定成本和可变成本。式(8)表示子订单生产完成时间的计算,在该完成时间的计算中同样考虑了构件返工和BIM的影响。式(9) (10)分别表示订单运输时间、实际交付日期的计算。式(11) (12)分别表示订单中构件修复或重新生产的成本、使用BIM时构件返工概率的计算。式(13)保证一个订单只通过一种方式运输。式(14)为各变量的取值属性。
4. 算法的设计及实现
本文中的多生产线多订单生产排序问题是一个NP难问题,涉及大量复杂计算,常规精确算法不能在有效时间内完成求解,因此一般采用GA、SA、PSO等智能算法进行求解。相关研究表明,相比于SA、PSO,遗传算法在求解此类问题方面更具优势 [24],因此本文采用遗传算法求解本文中的构件生产调度问题。
遗传算法设计:
1) 编码:本文中的遗传算法采用基于子订单在生产线上的生产顺序进行编码,每一条染色体中包含n × m个代表子订单生产顺序的基因序列,是一个包含所有子订单生产顺序的某一种排列。采用上述编码方式的好处在于任意基因序列的排列所表示的调度都是可行的,在算法执行过程中不必考虑出现无效调度的问题,可以提高算法运行效率。对于一个n个订单在m条生产线上生产的调度问题,在编码时,一条染色体将由n × m个基因组成,每个订单序号最多在染色体中出现m次,从左到右遍历整个染色体,当订单序号第i次出现时,表示该订单中第i个子订单在对应生产线上的生产顺序。以m = 3,n = 4,每个订单包含3个子订单的情况进行说明。如下图2所示,在上述预制构件订单中,每个预制构件子订单所对应的生产线为[1, 2, 3; 3, 2, 1; 3, 1, 2;3, 2, 1],某一条染色体为[1, 2, 3, 4, 2, 1, 3, 4, 4, 1, 3, 2],则其对应的生产线为[1, 3, 3, 3, 2, 2, 1, 2, 1, 3, 2, 1],在各生产线上,各子订单对应的生产顺序为[1, 3, 4, 2;2, 1, 4, 3;2, 3, 4, 1]。
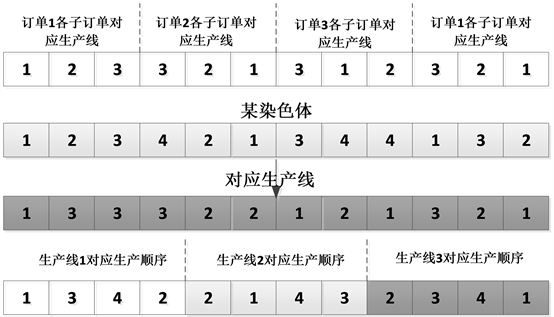
Figure 2. The coding process of the genetic algorithm
图2. 遗传算法编码图示
2) 适应度函数:采用目标函数的倒数作为适应度函数。在本例中,目标函数为成本,故适应度函数为成本倒数,设S为个体 i对应的调度策略,则
。
3) 选择:在进行选择操作时,采用精英保留策略。采用精英保留策略的好处在于在遗传算法的进化过程中,出现的最优个体不会被选择、交叉和变异操作所丢失和破坏,从而增强了遗传算法的全局收敛能力。精英保留策略具体操作为首先将适应函数值最高的个体直接复制纳入交叉配对的父代群体中. 当所有父代个体执行完交叉操作后,再次沿用精英保留策略,用交叉前的精英个体替换交叉后群体中适应函数值最差的个体,淘汰质量低的个体,使得精英个体得以保留。
4) 交叉:本文遗传算法所使用的交叉算子为基于子订单在生产线上的生产顺序编码的POX交叉算子。在本文问题交叉算子的设计标准中,子代的可行性以及对父代优良特性的继承性是最重要的。相对于PPX,SXX等交叉算子而言,基于子订单生产顺序编码的POX交叉算子能够保证子代总是可行的同时能够很好地继承父代的优良特性,能够有效避免遗传算法的早熟收敛,增强了遗传算法的全局搜索能力。
设两条父代染色体
和
采用POX交叉算子交叉生成两个子代
和
,
、
分别为[1, 2, 3, 4, 2, 1, 3, 4, 4, 1, 3, 2]、[1, 3, 2, 3, 1, 3, 2, 4, 4, 1, 4, 2],交叉过程如下:
a) 随机把订单集合
划分为两个非空订单子集,此处划分为
,
;
b) 将父代
中属于订单子集
中订单的子订单复制到子代
,将父代
中属于订单子集
中订单的子订单复制到子代
,固定子订单位置不变;同理,将父代
中属于订单子集
中订单的子订单复制到子代
,将父代
中属于订单子集
中订单的子订单复制到子代
,保持子订单顺序不变。
c) POX交叉操作完成,得到的两个子代
和
分别为[1, 2, 3, 2, 4, 1, 3, 4, 4, 1, 3, 2],[1, 3, 2, 3, 1, 3, 4, 2, 4, 1, 4, 2]。
具体情况如下图3所示:
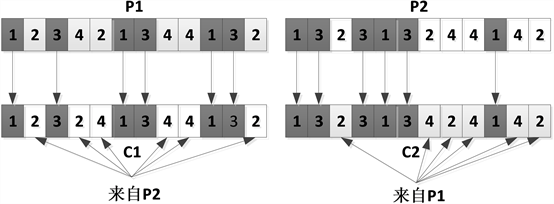
Figure 3. POX crossover process of the genetic algorithm
图3. 遗传算法POX交叉图示
5) 变异:针对单个染色体的不同基因序号进行交换。即从染色体中随机选择某个基因,然后将之随机插到同一条染色体的某个位置,完成变异操作。由于本文算法基于子订单生产顺序编码,故可确保变异后得到的解仍是可行解。
5. 算例测试
5.1. 算例生成
某构件厂在某时刻收到来自客户的的A、B、C、D、E、F共计6个订单,各订单提前交付罚款(元/天)、延期交付罚款(元/天)、指定交付日期(天)以及构件存储成本(元/件*天)分别为[50,000, 47,000, 45,000, 48,000, 40,000, 50,000]、[35,000, 40,000, 40,000, 38,000, 50,000, 45,000]、[44, 49, 45, 50, 48, 65]、[5, 6, 2.5, 7, 4, 3],订单其余相关信息如表1所示,各订单中的子订单接续生产。根据生产资料,该构件厂共计有6条生产线,用于生产各种不同类型的预制构件,该厂每个订单使用BIM的固定成本为10000元,可变成本为平均25元/件,各订单均使用BIM。该厂可选择E、F、G三种运输方式运送构件,订单[A, B, C, D, E, F]使用E/F/G三种运输方式的成本(元/件)分别为[50/75/100, 40/60/80, 65/75/90, 100/150/190, 100/150/200, 50/75/100],对应的时间(天)分别为[1/0.75/0.5, 1/0.75/0.5, 1.25/1/0.75, 2/1.5/1, 2/1.5/1, 1/0.75/0.5]。如不使用BIM,该构件厂生产的构件返工的概率
为0.2,使用BIM时可使构件返工的概率
降低一半,为0.1;订单中构件返工的平均单位成本、时间与正常生产单位成本、时间的比例系数为0.7。遗传算法的参数中,经过反复试验,选择种群规模为100,交叉概率为0.85,变异概率为0.05,终止条件为最大迭代代数200。
5.2. 结果分析
从图4可以看出,计算结果在39代已经收敛,最优值为2,323,700元,订单[A, B, C, D, E, F]对应生产完工日期分别[41.73, 43.87, 42.80, 46.01, 46.01, 66.34],到达交付点的时间分别为[44, 49, 45, 50, 48, 66.84];各条生产线上各子订单的生产顺序、生产开始时间如图5所示,除订单F延期交付1.84天之外,无订单出现延迟或提早交付情况,延期交付罚款为82,800元,占供应链总成本的3.56%;与不存在返工、不使用BIM的情况相比,因为构件返工所增加的供应链总成本为302,793元,其中生产成本增加141463元、延期交付罚款增加82,800元,分别占供应链总成本增量的70.58%、27.35%。
此外,为了比对改进的遗传算法与一般遗传算法的优越性,本文分别对基于改进的遗传算法和一般遗传算法的收敛特性进行了比较,为了比较同等参数下的优化特性,一般遗传算法的最大迭代次数也设置为200,种群规模为100,交叉概率为0.85,变异概率为0.05,选择方法为轮盘赌选择法,比较结果最终如图6所示。
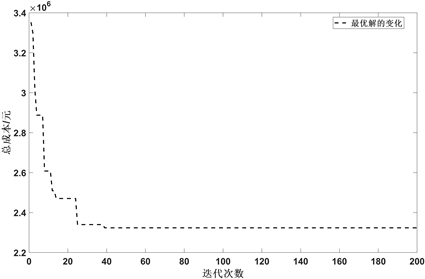
Figure 4. Calculation results of production scheduling
图4. 生产调度计算结果
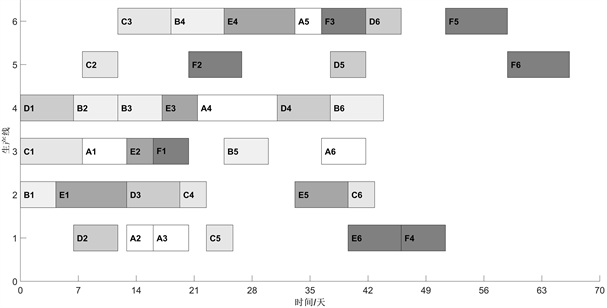
Figure 5. The result of the production scheduling of components
图5. 构件生产调度结果
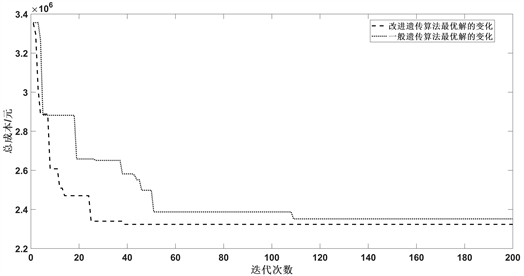
Figure 6. Comparison of convergence characteristics of general genetic Algorithm and improved genetic algorithm
图6. 一般遗传算法与改进遗传算法收敛特性比较
图6的结果表明,改进的遗传算法在收敛速度和寻优特性上均高于一般遗传算法,可以以更快速度找到更接近全局最优解,证明了改进遗传算法的优越性。
5.3. 模型参数及敏感度分析
基于算例,本文进一步讨论了模型中构件返工、BIM对预制构件生产调度的影响。
5.3.1. 构件返工对预制构件生产调度的影响
表2是考虑构件返工与不考虑构件返工两种情况下供应链总成本、延期交付成本、运输成本的对比。在保持其他条件不变(为更直观、更明显地展现构件返工的影响,此处考虑不使用BIM的情况)的情况下,以0.05为步长,让构件返工概率在[0, 0.5]之间变动,以探究返工现象的影响。在实际情况中,过高或过低的返工概率并不一定存在,本文仅是通过该概率的大幅改变,更好的说明返工现象对构件生产调度的影响。
从表2和图7可以看出,随着构件返工概率增大,预制构件供应链总成本、生产成本以及延期交付罚款也随之增大,产生该结果的原因是因为随着构件返工概率的增大,构件厂将花费更多时间和物料来生产足量满足交付条件的预制构件,直接导致生产成本和延期交付罚款增加,最终导致供应链总成本增加。在预制构件返工概率超过0.2之前,生产成本是增量成本的主要组成部分;在预制构件返工概率超过0.2之后,由于生产时间的大幅增加导致某些订单长时间延期交付,延期交付罚款成为增量成本的主要组成部分,若构件返工概率达到0.45,延期交付罚款占增量成本的比例将高达76.28%。同时,由于返工概率增大导致构件生产时间延长,为了尽量减少延期交付的损失,在构件的运输阶段构件厂不得不选用更贵但更快的运输方式,导致运输成本的增加;但在所有订单的生产时间都超过预定交付日期后,为减少延期交付罚款,构件厂将选择最贵但最快的运输方式,此时运输成本将保持稳定。提前交付罚款一直为0,这是因为提前交付构件所要支付的单位成本远远高于存储构件的单位成本,所以构件厂在构件生产完毕后将选择存储而不是提前交付构件。
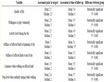
Table 2. The impact of component rework
表2. 构件返工的影响
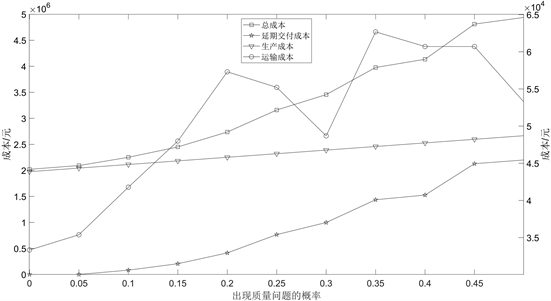
Figure 7. The impact of component rework on costs
图7. 构件返工对各类成本的影响
综上可见,当构件返工概率较小时,相对于构件没有返工的情况,供应链总成本、运输成本会小幅增加,增量成本的主要组成部分是生产成本;当构件返工概率较大且突破某一节点后,供应链总成本、延期交付罚款会大幅增加,同时延期交付罚款成为增量成本的主要组成部分。当所有订单中预制构件的生产时间超过预定交付日期后,构件厂将不得不选择最快但最贵的运输方式,此时运输成本将保持不变。
5.3.2. BIM对预制构件生产调度的影响
表3是使用BIM与不使用BIM两种情况下供应链总成本、延期交付成本、运输成本的对比。在保持其他条件不变(为更直观、更明显地展现BIM的影响,选定构件返工概率为0.3)的情况下,以0.05为步长,让BIM降低返工的概率系数在[0, 1]之间变动,以探究BIM对构件生产调度的影响。在实际情况中,BIM降低构件返工的作用区间是有限的,本文仅是通过该系数的大幅改变,更好的说明BIM对构件生产调度的影响。
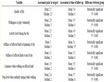
Table 3. The impact of BIM on production scheduling
表3. BIM对生产调度的影响
从表3可以看出,随着BIM降低构件返工的作用逐渐降低,预制构件供应链总成本、延期交付罚款也随之增大,产生该结果的原因在于随着BIM降低构件返工的作用降低,预制构件返工的概率逐渐增大,进而导致了上述情况的出现。BIM通过影响构件返工概率进而影响构件的生产调度,因此对其影响的分析与上文中对构件返工的分析是类似的。同时,BIM对于提升构件质量的作用越大,使用BIM的经济效益越高,但值得注意的是,当BIM降低构件返工的概率系数处于0.9~1.0之间时,仅从经济效益来说,使用BIM可能是无益的,其原因在于BIM在降低构件返工方面作用有限,所带来的效益低于使用BIM的固定成本和可变成本之和。
综上可见,BIM对于预制构件生产调度的影响和构件返工对预制构件生产调度的影响是类似的。一般情况下,BIM对降低构件返工的作用越大,使用BIM的经济效益越高,当使用BIM对于降低构件返工的作用有限时,由于使用BIM带来的效益低于使用BIM的成本,使用BIM可能会造成经济效益下降。
5.3.3. 订单交付日期变化对构件生产调度的影响
表4体现了订单交付日期变化时订单中子订单生产顺序、供应链总成本、延期交付成本、运输成本的变化情况。在保持其他条件不变(为更直观、更明显地展现构件返工的影响,此处考虑不使用BIM的情况)的情况下,以5为步长,让订单A的交付日期在[20, 65]之间变动,以探究订单交付日期变动的影响。在实际情况中,订单交付日期大幅改变的情况并不一定存在,本文仅是通过该指定日期的大幅改变,更好的说明交付日期变动对构件生产调度的影响。
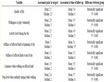
Table 4. Impact of order delivery date changes
表4. 订单交付日期变化的影响
从表4可以看出,当订单A的交付日期从20天逐渐增长到65天时,供应链总成本、延期交付成本以及运输成本基本呈下降趋势,尤其是延期交付成本下降趋势非常明显:交付日期为60天时的延期交付成本仅为交付日期为20天时的延期交付成本的12.19%。这是因为随着交付时间的延长,构件厂将有更多时间生产订单以及选择更经济的运输方式,从而降低了延期交付成本和运输成本。值得注意的是,在交付日期为20和25时,构件的生产调度方案保持不变;在交付日期为30、35、40、45时,构件的生产调度方案也保持稳定,仅有延期交付成本因交付日期变化从而发生改变。
综上可见,订单交付日期的改变对构件生产调度的影响非常显著。订单交付日期的提前可能会大幅增加构件的延期交付成本以及运输成本,从而增加供应链总成本。同时,在某订单交付日期发生改变时,可能存在一个或多个区间,当订单交付日期处于该区间时,总体订单的生产调度方案保持稳定,仅有延期交付成本随交付日期的改变而变化。
6. 结论
本文所建立的模型基于预制构件的生产特点,综合考虑了预制构件的返工现象、准时交付以及BIM的影响,以多生产线、多订单并行生产调度为基本设置,以供应链总成本最低为目标函数并建立交付时间约束。本模型不仅考虑了预制构件深化设计、提取信息的步骤和时间,还考虑了预制构件生产中经常出现的返工现象,并通过分析BIM对预制构件生产中每一环节的影响,定量描述了BIM的综合影响;同时多生产线、多订单并行生产的设置更加贴合预制构件生产的现实状况,有利于现实中构件生产商合理安排预制构件的生产事项,促进现实中预制构件的准时交付并节约供应链总成本。
在预制构件的生产调度模型中考虑返工和BIM的影响是必要的。由于根据模型得到的调度计划已预先考虑了构件返工并留足缓冲时间,当在实际生产中出现返工时,原有的生产计划不会被打乱,保证了生产的稳定性和连续性,促进构件的准时交付;反之,如果调度计划没有预先考虑而实际生产中出现返工时,构件的实际生产时间及成本将大于预计生产时间和成本,由此可能造成构件的延期交付并产生大量延期交付罚款,给构件生产商造成大量损失。同时,在BIM逐步成为建筑业重要发展方向的今天,有必要阐明BIM在预制构件生产调度中所起的作用并计算其经济效益,以便为相关决策提供理论支撑和参考。
从上文的分析可知,当返工过于严重或订单交付日期大幅提前时,构件生产成本和延期交付成本将大幅增加,因此在实际生产中应采取有效手段避免大量返工以及订单交付日期的突然改变。如可应用BIM技术减少构件的返工,同时与客户签订协议,避免订单交付日期的改变或在客户主动改变订单交付日期时获得一定的工时或经济补偿。订单交付日期的改变对客户和构件生产厂都有着巨大影响,研究多订单交付日期波动情况下预制构件的生产调度以及构件厂的对策是进一步的工作方向。