1. 引言
汽车在行驶过程中,车轮承受车体的垂直载荷和侧向载荷以及轴承传递的驱动,制动扭转力。汽车转向是通过车轮实现转向,车辆在高速行驶过程中对车轮的性能要求更高。车轮不仅影响汽车行驶性能,还影响行驶过程中的舒适性和安全性。因此对车轮在保持良好的轮廓、尺寸和形状的同时还要求具有极其高的刚性和疲劳性。常见的车轮是主要有轮辐和轮辋组成,由于轮毂模型的复杂性,简化了轮缘、槽底、偏距等。轮毂的国际性能实验主要包括轮毂的弯矩疲劳实验,径向载荷疲劳试验等,相对于传统的采用实验室实际实验来检验轮毂性能是否合格,耗费大量人力物力,周期长成本高等特点,采用有限元方法和仿真技术可以符合汽车行业快速发展的需求。通过预测结果和轮毂实验结果对比,验证仿真分析结果的正确性。进而对轮毂优化设计,大大缩短了研发周期,降低了成本。肖占龙等人 [1] 研究了钢制轮毂和铝合金轮毂的受力和模态分析并轻量化了轮毂。任山等人 [2] 通过弯曲疲劳实验和冲击试验进行考核。陆洋等人 [3] 运用ANSYS进行参数化建模和有限元分析,进行结构化设计得到轮毂的最优参数。
2. 结构形式
2.1. 轮毂结构
车轮是通过轮辋和轮辐焊接而成,如图1所示。轮辋主要用于支撑轮胎和承受轮胎内气压和来自径向的作用力,轮辐主要用于保护轮圈和加强强度的作用。气门孔用于伸出轮胎气门。一般轮毂采用辊压工艺成型,轮辐上有止口,通风孔等特征,结构较为复杂,轮辋和轮辐都属于薄壁构件,为方便后续的有限元分析,将不重要的部位进行简化。
2.2. 材料属性以及网格划分
轮辐的直径448.97 mm,轮辋厚度为10 mm。材料属性如下表1所示。
在考虑进行网格划分时,由于轮毂的结构复杂性可能会给网格划分失败,因此根据结构的特点简化了气门孔,偏距等,加快计算时间和提高结果精度,对于结构的倒角面进行处理,关闭网格的自适应,打开曲率捕捉,设置曲率角50˚,最后的网格划分如图2所示。网格划分统计:144,035个节点,90,145个单元。
轮毂的主要失效形式是疲劳破坏,国际上常用的主要指标为轮毂的弯曲疲劳寿命和径向疲劳寿命,其中弯曲疲劳实验成本高,失效率高等特点。因为在ANSYS中没有直接施加弯矩的功能,故采用节点融合来模拟螺栓孔和车轮链接,将螺栓孔和参考点(RP)进行耦合,通过对参考点施加载荷来等效替换弯矩载荷。
针对于轮毂动态弯曲疲劳分析,先将轮毂外表面进行全自由度约束,施加弯矩载荷后得到应力应变云图。为了进一步加快仿真模型计算速度,对结构进行简化做了一组对比分析,对轮辋下表面施加固定支撑约束,模拟乘用车正常形式下的静力学特性,再次得到应力应变云图,分别对比了两种常见轮毂材质下的静力学结果。
3. 轮毂弯矩载荷和径向载荷疲劳分析
3.1. 弯矩载荷静力学分析
载荷弯矩的大小如式(1)计算,具体参考GB/T 5909-2009。
(1)
式(1)中M为弯矩,单位N/m;
为轮胎和路面见的摩擦系数;R为车轮配用的最大轮胎的静态负载半径,单位m;d为车辆的内偏距,
为车轮额定负载值;S为强化实验系数。其中,
和S的取值见表2 [4]。
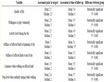
Table 2. Hub dynamic bending fatigue test requirements
表2. 轮毂动态弯曲疲劳试验要求
3.2. 约束条件以及载荷加载方式
根据某乘用车参数配置,汽车的质量为1250 kg,满载时质量2380 kg,则W = 12250 N,满载G = 23324 N,载荷影响系数则轮毂承受的最大载荷为:9032.33 N [5],故单个轮毂受到的最大载荷为2253.1 N。
根据乘用车轮毂的安装和受力情况,在对轮毂进行有限元分析时将5个螺栓孔和参考点(RP)点进行节点耦合,用等效载荷F来代替弯矩加载。分别对轮毂外侧和轮毂下侧进行全自由度约束,对载荷施加和应力、应变结果对比如图3所示。

Figure 3. Hub bending moment load deformation nephogram with different boundary conditions
图3. 轮毂弯矩载荷不同边界条件形变云图
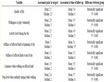
Table 3. Results of static analysis of bending moment load
表3. 弯矩载荷静力学分析结果表
从表3钢制轮毂的不同边界条件来看,对轮毂外侧施加固定支撑约束,轮毂结构的总变形主要集中在轮辐周围,其最大变形为9.9393e−6 m,在螺栓孔附近有明显的应力集中现象,最大应力为3.3105e7 Pa,说明在实验室设计轮毂结构时候需要考虑来自车身等弯矩载荷带来的应力集中问题可能会导致的疲劳问题,总变形集中于轮辐可能会导致轮毂整体性能下降。为了进一步解决这一问题,需要加强相邻螺栓孔强度和轮辋厚度,可以采用增大螺栓孔直径或者厚度的方式以及对轮辋厚度进行优化处理,使轮毂应力分布散开,结构承受弯矩载荷更加均匀合理化。
对轮毂下侧施加固定支撑约束来模拟轮毂在行驶过程中来自地面的约束以及车身自重带来的弯矩载荷,从仿真结果可以看到其最大变形为7.5597e−4 m,主要集中于接触地面时轮辋的外侧,相对于实验室理想约束条件下,工程实践中更加需要对轮辋外侧进行加强,减少由于外部约束造成的变形过大问题,轮毂最大应力为1.6794e8 Pa,主要集中在轮辋外侧和和相近螺栓孔部分,应力结果相对增加,这就要求轮毂在复杂的外部环境下更加注重对轮毂轮辋强度和刚度要求,可以合理提高轮辋厚度来改善轮毂的变形,提高结构的刚度,提高结构的使用寿命。
3.3. 径向载荷静力学分析
通过模拟乘用车在非平整路面行驶过程中受到来自车身自重和垂直于地面方向的冲击力,21世纪初,某某研究了铝合金汽车轮辋应力及其位移分布特性,将轮胎压力对轮辋的作用效果等效替换成在轮辋上径向分布力作用范围约为在40˚,径向分布力的值从轮毂中线至两侧20˚角度逐渐减小。
定义轮毂所受最大径向分布力
,则轮毂的分布力
的表达式为:
(2)
式中,
为加载偏转角;
为最大加载偏转角。
车轮所受径向力的合力
的表达式为:
(3)
式中,b为轮胎座受力宽带;
为轮胎半径。
轮胎气压作用于轮辋的常用两种方式:第一种以法向力均匀作用于轮辋;第二组以侧向力作用于轮辋两侧内环面 [6]。
轮胎气压对轮辋侧向作用力
的表达式为
(4)
式中,
为轮胎实验气压;
为轮胎冲完气后的内面半径。
一般来说,轮辋单侧受到的侧向力约为
的1/2,所受到的侧向力载荷p的表达式为
(5)
式中,s为单侧轮辋与外侧轮胎的接触面积。
本文将轮胎气压等效替换为分布载荷,作用于轮毂轮辋的外表面,将轮胎对轮辋的景象作用力采用正弦函数方式施加在轮胎圆心和轮毂圆心两侧40˚范围内,同时对5个螺栓孔进行全自由度约束,如图4所示
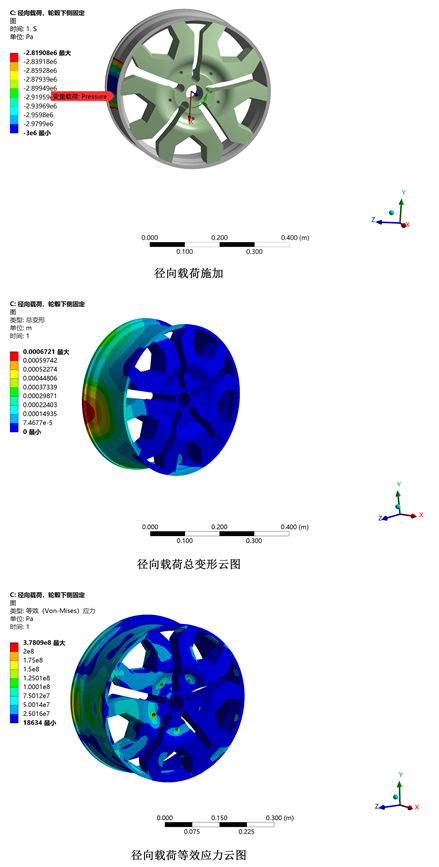
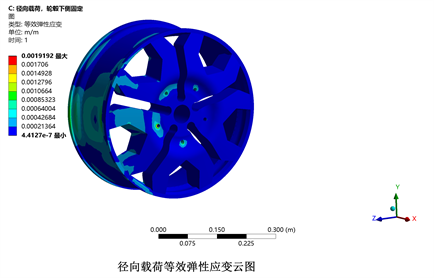
Figure 4. Deformation nephogram under radial load
图4. 径向载荷下形变云图
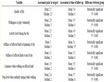
Table 4. Results of statics analysis of radial load
表4. 径向载荷静力学分析结果表
从表4轮毂静力学分析结果可以看出,在径向载荷作用下轮毂的最大变形量为6.721e−4 m,最大应力为3.7809e8 Pa,应力主要集中在轮辋外侧载荷受力区域和相邻螺栓孔附近,轮毂对称面呈现小变形量,低应力状态。对于轮胎气压加载处的应力相比较较大,后续可以通过对结构的尺寸优化来减缓疲劳问题。轮胎气压对轮毂结构性能影响比较大,在乘用车行驶在非平整路面时,轮胎的气压在过程中起到动平衡的作用,可以有效减小轮毂螺栓孔处的变形量,轮毂可以有效抵抗来自外界复杂激励。应对不同的外部环境可以采用不同的轮胎气压来缓解轮毂的受载荷作用下的刚度问题。
3.4. 疲劳分析
疲劳是指材料在循环应力和应变作用下,一处或几处产生永久性累计损伤经过一定循环次数后产生裂纹或突然发生完全断裂的过程。疲劳寿命的定义为发生疲劳破坏时候的载荷循环次数,或从开始收到载荷作用到发生断裂所经过的时间。轮毂在行驶过程中时刻收到来自外部循环动态激励或者冲击激励作用,常见的失效形式就是来自弯曲和径向载荷引起的疲劳破坏,因为对轮毂的疲劳分析也至关重要。
本文采用ANSYS疲劳模块拓展程序,采用的是基于应力疲劳理论。使用软件ANSYS workbench中Fatigue疲劳分析模块预测了轮毂疲劳寿命,绘制出疲劳寿命云图。从结果可以看出轮毂在理想状态下整体使用寿命接近无限,但是在实际工况下疲劳寿命下降,主要应力疲劳出现在螺栓孔附近,需要后期对螺栓孔直径进行优化,减少疲劳问题对轮毂性能的影响。
从图5疲劳分析结果可以看出,轮毂在弯矩载荷作用下疲劳寿命久,在模拟实际行驶过程中,轮辋外侧可能出现应力疲劳问题进而影响整体疲劳寿命;在径向载荷作用下,轮毂的疲劳出现在载荷作用区域和螺栓孔附近,这与实际工况下的情况一致,可以对结构的轮辋和螺栓孔进行优化提高整体的疲劳寿命。
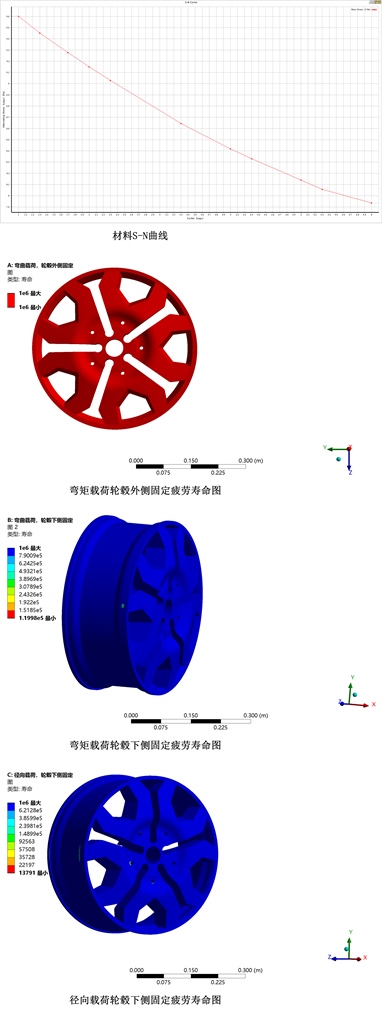
Figure 5. Cloud chart of hub fatigue life under different loads
图5. 不同载荷下轮毂疲劳寿命云图
4. 模态分析
对于轮毂的模态分析,是研究结构动力学特性的一种常用方法,主要用于工程振动问题。每一阶对应一个模态,每个阶次包括自身特定的频率,振型等信息。通过对轮毂前五阶固有频率的提取分析找到结构薄弱环节,通过后续优化设计提高结构的稳定性,使乘用车在行驶过程中减少颠簸振动,提高驾驶的舒适性。本文的模态分析主要分为自由模态和约束模态两种情况。
多自由度运动微分方程为:
(6)
式中M为广义质量矩阵;C为阻尼矩阵;K为刚度矩阵;x为位移矢量;
为激振力向量。在不考虑外激励的情况下分析系统的自由模态时,阻尼对系统产生的影响很小可以忽略不计。此时结构的无阻尼自由振动方程可以简化为:
(7)
式2的特征方程为:
(8)
此方程的特征值为
,其中
为自由振动圆频率,所对应的特征向量
为自由振动振型向量。
其结果如下图6所示。
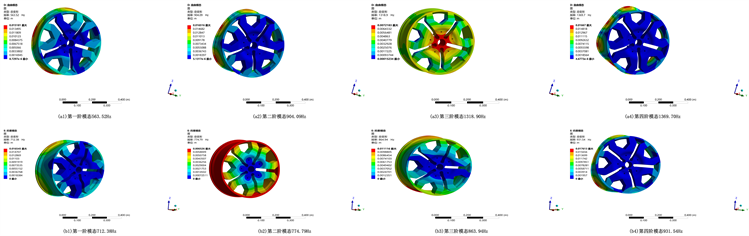
Figure 6. Hub modal shape ((a) free boundary; (b) constraint boundary)
图6. 轮毂模态振型((a)自由边界;(b)约束边界)
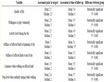
Table 5. Modal table of radial loads with different boundary conditions
表5. 径向载荷不同边界条件模态表
从图6可以分析得到在径向载荷作用下轮毂约束模态的1阶固有频率712.38 Hz,模态变形主要集中在轮辋外表面,轮毂四侧向内弯曲其最大变形量1.6545e−2 m;轮毂2阶固有频率774.79 Hz,模态变形主要集中在轮辋外表面和相连的轮辐处,轮毂变形从外侧向螺栓孔逐渐减小其最大变形量6.526e−3 m;轮毂3阶固有频率863.94 Hz,轮毂上下侧向内弯曲对折,模态变形主要集中在上下侧的轮辋表面其最大变形量为1.1116e−2 m;轮毂4阶固有频率931.54 Hz,轮毂受载荷作用下轮辋侧面向内弯曲变形明显,模态变形量大其最大变形量为1.7613e−2 m。通过对径向载荷作用下约束模态的振型的分析,表5可以进一步指导工程实践中对轮毂结构刚度的设计指导,减小对应频率下的模态振型变化量。
5. 轮毂结构优化
在保障轮毂强度和刚度的条件下,通过ANSYS对轮毂结构进行轻量化优化。本文研究了轮毂同时受到径向载荷和弯曲载荷同时作用下的结构性能,主要优化对象为螺栓孔和轮辋直径。在对轮毂重量轻量化设计理念下,轮毂的密度为常数的情况下,也就是研究对轮毂体积的轻量化目标,符合国家节能减排的指导理念。然后通过对比优化前后轮毂的模态信息的对比,得到的结果表明轮毂在体积轻量化的情况下,系统的固有频率得到了提升,减少了和外部激励发生共振的可能性,更好了满足行驶过程中的舒适感。
响应曲面法是优化随机过程的统计实验方法。目标是通过寻找实验指标和各因子之间的定量规律,从而得到最优化的参数组合。在多元回归的基础上来提取数据,以获得较好的回归方程,具备良好性质,常广泛应用于模拟和系统动力学。本文通过对轮毂在收弯矩和径向载荷同时作用下的优化设计,更加符合乘用车真实环境下的模型。
将螺栓孔直径定义为参数P9-Group1,轮辋直径为参数P10-Group2,对轮毂的质量和最大应力和最大应变设置优化目标,根据实际轮毂情况此处设定最大应力应小于300 MPa [7],结果如图7~9所示。
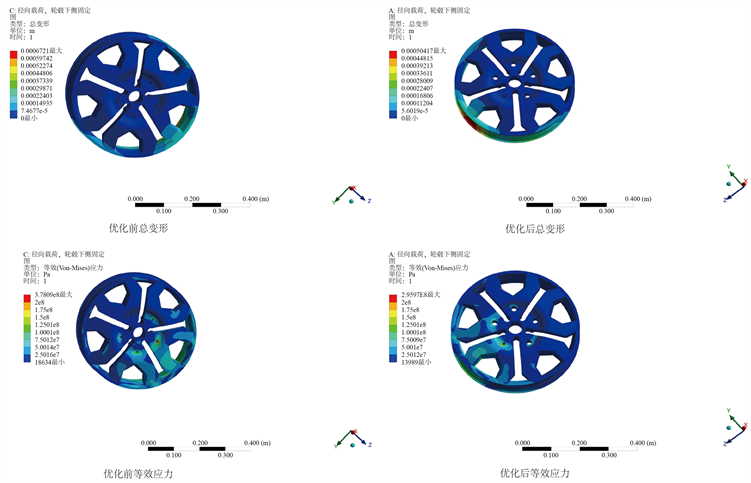
Figure 8. Cloud chart of deformation comparison before and after optimization under radial load
图8. 径向载荷下优化前后形变对比云图
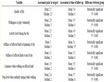
Table 6. Statics analysis results before and after optimization
表6. 优化前后静力学分析结果表
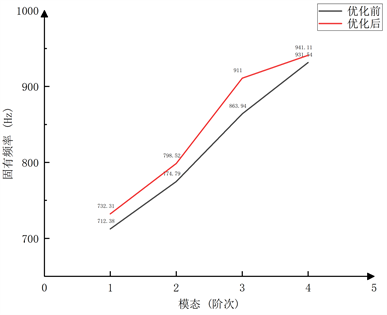
Figure 9. Natural frequency diagram before and after constrained modal optimization
图9. 约束模态优化前后固有频率图
取径向载荷作用下轮毂的优化分析结果可得,螺栓孔直径从4.5 mm优化到9.85 mm,轮辋直径从218.66 mm优化到219.28 mm,轮毂质量优化到5.6135 kg。在满足强度刚度的同时减小了轮毂的质量,符合轻量化设计要求。
从表6和图8可知轮辋的总变形量减小了,有利于减小乘用车在行驶过程中收到外部激励载荷作用下的变形量,提高了轮毂的刚度;螺栓孔附近的应力明显减小,从3.7809e8 Pa减小到2.9597e8 Pa,有利于减小应力集中带来的损伤疲劳问题,提高了轮毂的强度,可以延长轮毂的使用寿命。由图9可知轮毂的前四阶模态提高了,文献 [8] 表明轮毂的模态振型主要分布在轮辋上,轮辐刚度也会更加大些。固有频率和模态振型主要表现在轮辋上面,同时也间接地说明,在质量相差不大的部件间,刚度大的部件其固有频率较高。因此在乘用车轻量化指标的条件下,可以选择固有频率较大的钢制轮毂,来减小和外界环境频率相近共振的可能性,进而提高乘用车在行驶过程中的舒适感。
6. 总结
1) 本文通过对轮毂结构进行建模,根据结构的特点删去了轮毂上圆角、气门孔等特征,采用钢制轮毂进行了静力学分析、模态分析,通过远端点力的加载等效轮毂受到的弯矩载荷效果,分别对轮辋外侧和下表面侧进行分析,基于应力结果和结构钢材料S-N疲劳寿命曲线,采用疲劳分析插件,预测轮毂在弯矩载荷下的疲劳寿命。
2) 在对轮毂径向载荷疲劳分析时,将轮辋外表面的等效成轮辋收到轮胎气压的表面压力,在轮辋双侧40˚范围内施加余弦函数径向作用力,对五个螺栓孔进行全自由度约束,最后基于应力结果和材料的S-N疲劳寿命曲线预测了轮毂在动态载荷下的疲劳寿命。
3) 在对轮毂进行轻量化设计的同时保证轮毂强度刚度的要求,对螺栓孔和轮辋直径进行了样本点设计,从而择优出合理的轮毂参数,使得轮毂质量减少了,固有频率提升了提高了整体的稳定性。