1. 引言
根据相关的统计数据,在世界范围内,平均每分钟有一人因交通事故死亡 [1]。面对严峻的交通安全形势,政府管理者和汽车消费者对汽车安全性的期望越来越高。汽车制动性能和汽车操纵稳定性能方面发生故障时能造成巨大危害,而在汽车操纵稳定系统中,汽车转向节臂具有重要作用。转向节臂发生故障将会导致汽车无法转向,造成严重的事故,甚至会威胁司机及乘客的生命安全。因此,对转向节臂进行分析和优化,对于保障汽车的行驶安全和人们的生命安全具有十分重大的意义。
当前,国内针对转向节臂的研究主要集中体现在以下方面:胡艳连等 [2] 将有限元分析软件和理论计算融合,研究转向节臂的强度,验证有限元分析软件的准确性;元涛等 [3] 通过仿真软件和改善加工工艺、热处理方法,针对转向节臂的疲劳耐久性、失效和强度问题,提出优化方向,提高疲劳耐久性和强度;王延强等 [4] 运用仿真软件对转向节臂的刚度、强度及疲劳耐久性进行模拟分析。
2. 有限元模型建立
转向节臂又叫梯形臂,是转向传动装置中最后一级传力零件。转向节臂不但承受来自地面的冲击力和车身的部分重力,还在车辆制动过程中承受扭转力的作用。
2.1. 建模
转向节臂的三维模型通过UG软件建立。为了减少仿真计算时间,除了保留转向节臂原来的机械性能与结构特征,将连接螺纹简化成直通孔,并且也不考虑加工过程中出现的拔模角度和圆角等结构特征,但保留减小应力集中的圆角 [5]。最后转向节臂零件图如图1所示。
2.2. 材料属性及单位制
该转向节臂选用40Cr作为加工材料,各物理属性及单位如下表1所示。
2.3. 网格划分
将模型导入Workbench后,进行网格划分,网格大小为2 mm,转向节臂模型网格化后的节点数为664,596,单元数为473,957。转向节臂有限元模型如图2所示。
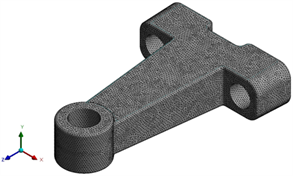
Figure 2. Finite element model of steering arm
图2. 转向节臂有限元模型
3. 转向节臂的模态分析
振动问题引起的机械设备故障率可高达60%~70% [6],转向节臂作为汽车转向系统的重要组成部分,发生超出标准的振动不但会对转向节臂的性能产生重大影响,而且会缩短使用寿命,一旦长时间发生共振,更是会对转向节臂造成恶性破坏甚至失效。
转向节臂研究目的就是在保证功能要求的前提下,使其具有合理的结构、良好的动态性能及经济性,工作过程可靠平稳,工作效率高。为实现上述目标,从本质上改进转向节臂的设计,需从总体上把握结构的阻尼、振型及固有频率等特征。因此,可通过模态分析来实现研究目的。
模态分析是动力学频域分析的基础分析类型,主要用于计算模型的振动频率和振型。将动力学控制方程单元的各个矩阵进行组装,表示为系统的整体有限元方程:
(1)
其中:
,
,
,
,
(2)
式中,M叫做单元的质量矩阵;C为结构阻尼矩阵;K为刚度矩阵;Ft为随时间变化的外部载荷;
为节点加速度矢量;
为节点速度矢量;
为节点位移矢量。
静力情况下,考虑与时间的无关性,即结构静力分析的整体刚度方程为:
(3)
理想状态下,结构振动不考虑约束和阻尼情况,此时v = 0,Ft = 0,表现为无阻尼自由振动情形,其振动形式叫自由振动,此时的自由模态方程为:
(4)
其方程有解的形式为简谐振动形式:
(5)
式中:i为虚数;
为自然圆频率,也叫圆频率,rad/s;t为时间变量;
为
对应的特征向量。将式(5)代回式(4)得到:
(6)
消掉
后,有
(7)
该方程有非零解的条件,即特征方程为:
(8)
自然圆频率对应的频率
,求得自然圆频率
后,代入方程(7),求得
对应的特征向量
,
这就是对应与振动频率
的振型或模态。
3.1. 转向节臂有限元模态分析
在汽车各种运行工况下转向节臂的约束条件较为复杂,而模态是结构的固有特性,它与模型是否受到外界载荷无关,不合理的约束对仿真分析结果的影响较大,因此采用自由模态分析可以在很大程度上更有效地反映转向节臂自身的固有特性。
通过Workbench对转向节臂进行模态分析,提取前十二阶的振型,自由模态下,转向节臂前6阶模态为刚体模态,主要表现形式为模型在空间内的转动和平动,不产生弹性形变,求解的固有模态为0或趋近于0,可忽略刚体模态 [7]。因此将第七阶模态,即弹性模态的第一阶开始,选取前6阶弹性模态进行分析,有限元模态仿真分析结果如图3所示,模态分析结果见表2。
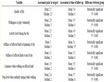
Table 2. Results of steering arm modal analysis
表2. 转向节臂模态分析结果
3.2. 结果分析
第一二阶振型主要表现为转向节臂与转向拉杆接触圆孔的弯曲模态;第三阶振型主要表现为转向节臂与转向拉杆接触圆孔的扭转模态;第四阶振型主要表现为转向节臂与转向节连接凸台的弯曲模态;第五阶振型主要表现为转向节臂与转向拉杆接触圆孔的弯曲模态;第六阶振型主要表现为转向节臂与转向节连接凸台的弯曲模态和扭转模态。前六阶固有频率都较小,第一阶至第三阶频率在3~6 Hz,第四阶至第六阶频率集中表现在7~8 Hz之间。综上所述,在不同的振型下转向节臂表现出的模态不同。随着各阶模态的增加,转向节臂在共振形态下的变形区域和变形程度增加,变形形式也更为复杂。
一般情况下,汽车的外在激励频率主要分布在20~80 Hz频带内 [8]。从上述数据可以得知,转向节臂的固有频率远小于外在因素的激励频率,由此可以判断很难发生内外共振,可以保障汽车在正常行驶时的稳定性,安全性较强。通过模态分析,可在转向节臂设计阶段掌握结构的振动特点,采取相应措施,有效防止共振的产生,确保转向节臂的稳定性和持续性,了解结构的共振变形区域,为结构设计提供指导,为动态特性研究提供理论依据,为结构动力特性优化以及振动故障的预防诊断提供依据。
4. 转向节臂的拓扑优化
拓扑优化是将材料布置在既定的可设计区域内,建立算法和规则分析材料最优分布,在分析过程中持续修改优化区域的单元材料性质,通过从模型中移走或增加单元来有效地获得某项性能最优的结构模型,最终得到最优的设计目标。
4.1. 工况设计
汽车转向节臂有三种典型工况,即越过不平路面,转向和紧急制动。转向节臂在典型工况中,转向拉杆受X轴方向的力较大,Y轴方向和Z轴方向的力较小,将各方向中最大载荷同时作用于该模型 [9],转向拉杆受力见表3。
将转向节臂有限元模型进行强度分析。约束条件见图4(a),图4(b)所示。优化前转向节臂的最大应力为350.88 MPa,最大应力位于转向节臂与转向节连接凸台处,结果如图5(a)所示;最大位移为0.33653 mm,最大位移位于转向拉杆圆孔上端处,结果如图5(b)所示。
4.2. 拓扑优化模型建立
利用Workbench对转向节臂进行拓扑优化。首先建立优化任务;其次建立应变能的设计响应;再次选择优化区域,本研究中转向节臂拓扑优化区域选定为除受力面的所有表面,即除去连接圆孔表面和转向拉杆连接孔表面,如图6所示;再次建立最小应变能目标函数和响应约束为50%质量优化目标,其中,最小应变能是指最大化全局刚度,在模型初始计算强度结果条件下,刚度基本保持不变;最后,创建优化进程并提交分析。
(a)
(b)
Figure 4. (a) Fixed constraint; (b) steering tie rod force constraint
图4. (a) 固定约束;(b) 转向拉杆受力约束
(a)
(b)
Figure 5. (a) Stress cloud of steering arm before optimization; (b) displacement cloud of steering arm before optimization
图5. (a) 优化前转向节臂应力云图;(b) 优化前转向节臂位移云图

Figure 6. Optimized area of steering arm
图6. 转向节臂优化区域
经过21次迭代得到拓扑优化结果如图7所示。对模型进行重构,对转向节臂模型下部及中部进行材料去除,在应力集中处采用圆角过渡的方法对模型进行修正,优化后转向节臂模型图如图8所示。
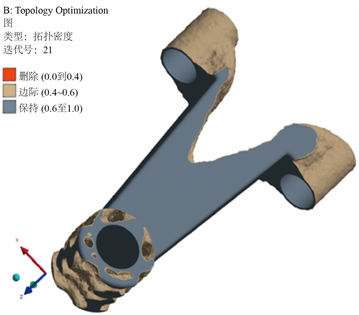
Figure 7. Topological optimization model diagram
图7. 拓扑优化后模型图
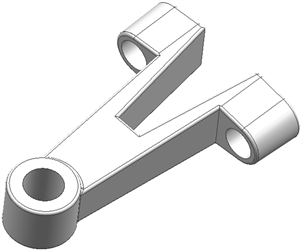
Figure 8. Reconstruction model of steering arm
图8. 转向节臂重构模型图
为了验证优化设计的可靠性,对优化后的转向节臂重构模型重新划分网格,进行静力分析,最大应力为406.77 MPa,位于转向节臂与转向节连接凸台处,结果如图9(a)所示;最大位移为0.42181 mm,最大位移位于转向拉杆圆孔处上端,结果如图9(b)所示。优化前后最大应力和最大位移对比见表4。
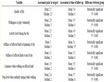
Table 4. Comparison of optimization results of steering arm
表4. 转向节臂优化结果对比
(a)
(b)
Figure 9. (a) Optimized back steering arm stress cloud diagram; (b) optimized rear steering arm displacement cloud diagram
图9. (a) 优化后转向节臂应力云图;(b) 优化后转向节臂位移云图
4.3. 结果分析
通过图5和图9可知,转向节臂的最大应力和最大位移出现位置基本不变,由表4可知,优化后的转向节臂模型的最大应力和最大位移分别增大15.92%和25.34%,质量减小48.18%。在同种工况下,转向节臂质量减少48.18%,最大应力变为406.77MPa,不仅有效的实现轻量化设计目的,且优化后的最大应力还远小于其材料的屈服强度750MPa,保证轻量化设计后转向节臂的可靠性。
通过对该转向节臂的拓扑优化分析,在满足使用要求和安全要求的前提下,完成减轻转向节臂质量的设计任务,不仅实现将产品设计优化过程从传统的经验设计优化向现代数字设计发展,而且对汽车转向节臂设计优化理论进行了拓宽和深化,对实现汽车轻量化具有十分重要的现实意义,可有效缩短车用转向节臂设计周期,对今后的车用转向节臂设计工作有指导性作用。