1. 引言
多孔焊接件作为手动搬运车的重要组成部件,是连接车架与油泵的动力传输纽带,其加工质量直接决定整车的工作过程中的空间稳定性,在整车的运动过程中具有承上启下的作用 [1]。
图1为某工厂系列多孔焊接件,由两块筋板、一根中心圆管以及两个封套构成,均采用普通碳钢材质,需要在两块筋板的两臂端分别加工两个的圆孔。使用传统方法在普通钻床上加工定位装夹困难,导致生产效率和加工质量都无法满足要求 [2] [3]。为此本文根据多孔焊接件形状结构特点,进行详实的工艺分析,综合分析同系列不同型号多孔焊接件关键部位尺寸要求,设计了一种适用系列多孔焊接件四孔同步加工的专用夹具,并利用Solidworks软件对其进行仿真优化以提高设备的可靠性。
2. 工艺分析
图1为系列多孔焊接件和钻床加工坐标示意图,可以看出,该系列工件形状复杂呈对称树枝状,需要加工的四个φ18孔对称分布在两块筋板的两个臂端。结合表1可知,该系列工件左筋板和右筋板长臂端X轴方向位置距离为固定值,而不同型号工件筋板折弯程度不同,使不同型号工件中心圆管长度(L2)随两块筋板和封套沿圆管轴线方向距离(L1和L3)的变化而变化。因此在设计时考虑工件以图1所示卧式L形姿态进行定位装夹,使待加工四孔与四头钻床上的钻头一一对应,从而满足四孔同步加工的需求。特别说明,下文中X轴方向统称为轴向。
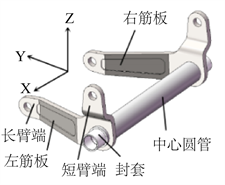
Figure 1. Schematic diagram of machining coordinate system of series porous weldment and drilling machine
图1. 系列多孔焊接件和钻床加工坐标系示意图
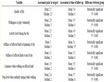
Table 1. Dimension table of porous weldment series
表1. 多孔焊接件系列尺寸表
由于焊接产生的应力变形导致单个筋板发生侧弯以及两块筋板长臂端位置偏差,如图2,且筋板臂薄,在普通钻床上采用通用夹具夹紧侧弯的筋板时发现,夹紧力会在筋板长臂端上形成一个力偶矩,使筋板长臂端发生扭转变形,导致孔加工质量难以保证 [4] [5] [6]。
3. 夹具设计思路分析
3.1. 定位方案分析
由于筋板为铸造件精度差,筋板待加工孔与封套中心距为固定尺寸,且封套内孔已完成精加工,故以封套内孔为基准定位,使工序基准与定位基准重合。并结合六点定位原理,对封套外端面和筋板长臂端进行定位,限制工件在空间的六个自由度 [7]。确定定位基准后,还需确定定位元件并对定位误差进行计算校核,以确保定位准确。
3.2. 夹紧方案分析
由于封套与中心圆管同轴且轴向刚性较好,故采用组合连杆对向式夹紧方法沿轴向对两封套外端面进行夹紧固定,使夹紧力方向可适应不同型号尺寸变化始终与钻削力方向保持重合,从而降低所需夹紧力并满足夹具通用性装夹需求。由于常规夹紧方式夹紧筋板前端产生的力偶矩导致工件夹紧变形,故沿钻床Z轴方向对筋板长臂端侧端面进行夹紧,使夹紧力反向共线贯穿筋板长臂端进而避免力偶矩的产生。由于不同工件两块筋板长臂端可能存在的不同的位置偏差,新颖性采用虎口压力钳自适应调整的夹紧方法,使下钳体可根据上钳体施加的夹紧力进行自适应转动微调,从而实现对存在不同位置偏差的两块筋板长臂端的装夹。夹紧方案如图3。
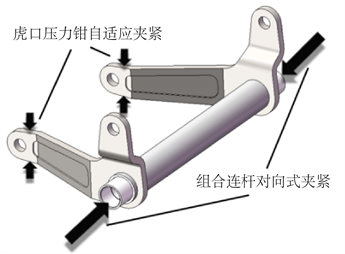
Figure 3. Schematic diagram of clamping scheme
图3. 夹紧方案示意图
为保证工作效率以及工件成品质量的稳定性,夹紧动作应由自动化控制完成。因此首选液压夹紧或气动夹紧,其中液压夹紧回路一般用在低速重载的场合且成本也较高,气动夹紧回路一般用在高速轻载的场合,为提高装夹效率和控制夹具成本选用气动夹紧 [6] [7]。
3.3. 夹具机械结构分析
依据专用夹具的结构应遵循力求简单、合理,便于制造、装配、调整、检验、维修的原则,且需要满足耐用性和柔性生产的现实需求 [8]。由于工件属于复杂异形件,为简化夹具结构、节约钻床有限空间采用模块化组合式设计方法 [9] [10] [11]。
3.4. 强度校核
在设计完成后还需要对工件装夹的关键部位——筋板长臂端进行强度校核,检验设计方案合理性。
4. 具体设计方案
4.1. 定位与定位误差计算
依据上文分析,图4为工件定位示意图,以封套内孔作为定位基准,限制工件Y、Z轴方向的移动自由度以及绕Y、Z轴的旋转自由度;以封套圆管右端面以及筋板长臂端下端面限制工件X轴方向的移动自由度以及绕X轴的旋转自由度,至此工件已完全定位。定位元件心轴和夹紧块如图5。
(a) 心轴
(b) 夹紧块
Figure 5. Schematic diagram of positioning element
图5. 定位元件示意图
定位误差∆D由基准位移误差∆Y和基准不重合误差∆B两部分组成。为了保证加工精度,一般限定定位
误差不超过工件加工公差T的
[8]。加工前后Z轴、Y轴方向孔位置尺寸误差要求分别在0.15 mm
和0.2 mm内,即定位误差分别在0.03~0.05 mm和0.04~0.06 mm内。
所设计定位元件心轴直径为
,心轴最大直径公差为
,封套内径为
,内孔最大直径公差为
,孔轴最小间隙为
,设计基准与定位基准重合,满足基准重合原则,即
。
Z轴方向心轴与封套为固定边接触,定位误差为
。
Y轴方向心轴与封套为任意边接触,定位误差为
。
经计算,定位误差均在允许值范围内,符合设计要求。
4.2. 夹紧装置机械结构设计
4.2.1. 组合连杆对向式夹紧装置
图6为组合连杆对向式夹紧装置爆炸图。当气缸带动左滑台组件3动作时,通过组合连杆4实现左、右滑台组件3、5对向式同步夹紧动作,满足多型号加工的通用性需求,并确保作用在封套圆管两端的夹紧力的一致性,避免工件加工过程中产生夹紧变形。
4.2.2. 虎口压力钳自适应夹紧装置
图7为虎口压力钳自使用夹紧装置三维模型图和爆炸图。当气缸2推动活塞杆3伸出时,同时推动左、右两上钳体14绕中心转轴下压,与下钳体12形成钳口,分别在筋板长臂端折弯处与待加工孔位之间的上下端面进行夹紧;当两筋板前端出现位置偏差的情况时,上钳体14首先接触筋板高的一端并施加下压夹紧力,由于工件轴向已夹紧,因此,筋板低的一端对下钳体12施加一个竖直方向的下压力,带动下钳体13绕中心转轴转动,进行自适应动态调整直至上钳体14和下钳体13与摩擦环5达到静态平衡,从而实现对筋板长臂端的自适应夹紧。
1-工件;2-三角支撑架;3-右滑台组件;4-组合连杆;5-左滑台组件;6-导轨副;7-工装底座;8-支撑转轴;9-气缸。
Figure 6. Exploded view of combined connecting rod opposite clamping device
图6. 组合连杆对向式夹紧装置爆炸图
(a) 三维模型图
(b) 爆炸视图1-后立板;2-气缸;3-活塞杆;4-加强轴;5-摩擦环;6-中心转轴;7-前立板;8-胀紧套;9-工件;10-T形柱;11-凸形板;12-平板;13-下钳体;14-上钳体;15-夹紧块。
Figure 7. Self-adaptive clamping device of vice pressure clamp
图7. 虎口压力钳自适应夹紧装置
4.3. 关键部位强度校核
由于夹具需要满足通用性需求,因此需要对抗变形能力最差的多孔焊接件关键部位进行强度校核。选用Solidworks Simulation仿真分析软件对夹紧块和685型号左筋板进行仿真分析,以检验其在夹紧力、钻削力和钻削力矩作用下的应力和变形是否在允许范围内。为此,需要对筋板长臂端所受外部载荷进行计算。
在实际生产加工过程中,主轴匀速进给,进给量f为0.03 mm/r,加工孔孔径
,
。计算得出钻削力
,钻削力矩
。
计算公式如下 [8]:
为简化计算,以筋板长臂端为质点在机床(X, Z)平面内进行受力分析,分别受到来自上钳体和下钳体的夹紧力F和F'、钻削力Ff以及静摩擦力Fƒ和
,如图8所示,其中静摩擦系数f = 0.15。由静力学原理计算出的理论夹紧力Fw,需乘以安全系数K作为实际夹紧力Fwk,其中K = 2.9。计算得出实际夹紧力
。
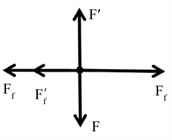
Figure 8. Stress analysis of long arm end of rib plate
图8. 筋板长臂端受力分析
计算公式如下 [8] [12]:
上述各参数数据均向上取整。
1) 材料属性
查表知 [13],普碳钢的质量密度为7.7 × 103 kg/m3,弹性模量为210 GPa,泊松比为0.28,屈服强度为235 MPa。
2) 边界条件
根据夹具工作原理,对筋板下方夹紧块以及筋板进行固定,在筋板上方夹紧块上端面添加一个与上端面垂直的夹紧力
,分别在长臂端φ18孔添加一个沿轴向的钻削力
和一个绕轴顺时针方向的钻削力矩
,如图9。

Figure 9. Schematic diagram of boundary conditions
图9. 边界条件示意图
3) 网格划分
采用三面体实体网格对夹紧块和筋板进行网格划分,完成网格划分后的仿真模型如图10。
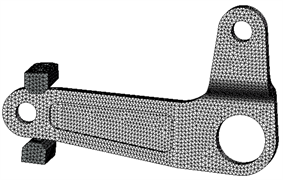
Figure 10. Finite element model after meshing
图10. 网格划分后的有限元模型
4) 计算结果分析
图11和图12分别为仿真模型的应力云图和位移云图,可知,有限元模型最大应力集中在筋板长臂端与下方夹紧块的接触面上,最大值为231.2 MPa,小于普碳钢材料的屈服强度235 MPa;最大位移发生在筋板长臂端前端,最大值为0.04933 mm,小于工件的允许位移量0.05 mm。
5. 优化分析
虽然实验结果均在允许范围内,但实验结果与实际情况存在不可避免的误差,因此需要预留允许值的5%作为实验结果参照的安全误差。意即最大应力应小于223.25 MPa,最大位移应小于0.0475 mm,而上述实验结果最大应力的安全误差仅为1.6%,最大位移的安全误差仅为1.3%,故需对上述设计方案进行优化。那么如何有效减小最大位移以及在不影响夹具夹持刚性的前提下减小夹紧筋板长臂端所需的夹紧力成为此次优化的重难点。
5.1. 解决方案
5.1.1. 思路分析
对筋板长臂端最大位移发生位置以及筋板长臂端所受外力进行分析可知,最大位移主要是由钻削力导致的。对产生原因作进一步分析,由于筋板大圆孔与中心圆管焊接固定,而筋板壁薄抗变形能力差,因此作用在筋板长臂端的钻削力以筋板长臂长度为力臂形成一个作用力矩,进而导致最大位移在筋板长臂端前端的发生,如图13。那么在力的大小方向无法改变的情况下缩短力臂长度,将有效减小力矩,进而减小最大位移。
对筋板长臂端最大应力发生位置以及筋板长臂端受力分析图研究发现,最大应力主要是由夹紧力过大导致的。对夹紧力公式作进一步分析,可知实际所需夹紧力Fwk与钻削力Ff成正比,那么在筋板长臂端施加一个与钻削力相反的补偿力,则将有效减小实际所需的夹紧力,进而降低最大应力。
为此,依据上述分析提出了一种自锁式辅撑装置,该装置可沿钻削力反方向对筋板长臂端施加辅顶支撑,将力臂缩短为支撑点与钻削力作用点的直线距离,并可凭借其自锁性进而根据夹紧力的减小实现对钻削力的反向自动补偿。
5.1.2. 自锁式辅撑装置
如图14为自锁式辅撑装置三维模型图。当气缸1收缩时,拉杆4拉动空心滑块6以前立板11侧面为轨道,杠杆5上端以圆柱销为支点随空心滑块6沿拉杆5方向的滑动末端向外侧转动,直至辅顶垫块8与筋板长臂端接触达到自锁式静态平衡,巧妙运用杠杆原理实现对筋板长臂端的辅顶支撑。
5.2. 对比分析
5.2.1. 最大位移仿真分析
在装置设计完成后,需要对分析结果进行分析验证。根据自锁式辅撑装置工作原理对辅顶垫块进行固定,其余设置条件不变对夹紧块、辅顶垫块和685型号左筋板进行仿真分析。图15和图16分别为有限元模型应力云图和位移云图。
1-气缸;2-卡板;3-长条板;4-拉杆;5-杠杆;6-空心滑块;7-筋板;8-辅顶垫块;9-限位块;10-固定板;11-前立板。
Figure 14. Three-dimensional model of self-locking auxiliary support device
图14. 自锁式辅撑装置三维模型图
将图16与图12对比分析可知,自锁式辅撑装置可有效减小筋板长臂端加工时的最大位移,减幅可达10.8%。
5.2.2. 最大应力仿真分析
对比图15和图11可知,仅引入自锁式辅撑装置而不减小夹紧力对降低最大应力效果并不明显,最大应力的安全偏差仍小于5%,因此结合5.1.1分析思路在以5.2.1设置条件不变的情况下,分别取夹紧力7000 N、6500 N、6000 N、5500 N对夹紧块、辅顶垫块和685型号左筋板进行仿真分析,如图17和图18分别为应力云图和位移云图,图19为应力和位移折线图。
(a) 7000 N
(b) 6500 N
(c) 6000 N
(d) 5500 N
Figure 17. Stress nephogram
图17. 应力云图
(a) 7000 N
(b) 6500 N
(c) 6000 N
(d) 5500 N
Figure 18. Displacement nephogram
图18. 位移云图
由图19可得结论,夹紧力与最大应力成正比,与最大位移成反比,实际所需夹紧力的合理取值范围为6500 N~7000 N,此时最大应力的安全误差为8.5%~15.3%,最大位移的安全误差为8.2%~10.1%。此结论可为实际生产过程中夹紧力调整提供理论依据,并为同类型实验研究提供借鉴。

Figure 19. Stress and displacement line diagram
图19. 应力和位移折线图
6. 夹具总体机械结构
如图20,夹具总体结构由组合连杆对向式夹紧装置模块、虎口压力钳自适应夹紧装置模块、自锁式辅撑装置模块以及工装底座模块组合装配构成,通过工装底座根据钻床加工坐标系固定安装在卧式四头钻床上。
1-自锁式辅顶装置;2-虎口压力钳自适应夹紧装置;3-组合连杆对向式夹紧装置;4-工装底座。
Figure 20. Three-dimensional model drawing of fixture overall structure
图20. 夹具总体结构三维模型图
7. 结语
本研究通过对系列多孔焊接件进行详实的工艺技术分析,设计了一种系列多孔焊接件四孔同步加工的专用夹具。并以抗变形能力最差的685型多孔焊接件左筋板长臂端为主要研究对象进行仿真分析,结论如下:
1) 最大位移发生在筋板长臂端前端,是由作用在筋板长臂端的钻削力以筋板长臂长度为力臂形成一个作用力矩导致的;
2) 最大应力集中在筋板长臂端与下方夹紧块的接触面上,主要是由夹紧块作用在工件上的夹紧力过大导致的;
3) 自锁式辅撑装置可有效减小筋板长臂端加工时的最大位移,减幅可达10.8%;可在不影响夹具夹持刚性的前提下减小夹紧筋板长臂端所需的夹紧力;
4) 夹紧力与最大应力成正比,与最大位移成反比,实际所需夹紧力的合理取值范围为6500 N~7000 N。
基金项目
浙江省科技计划项目(2022C01202)。
NOTES
*通讯作者。