1. 引言
随着我国经济的快速发展,人民追求高质量生活水平的需求不断提高,汽车的保有量也逐年增长,同时汽车行驶中的安全问题也备受关注 [1] 。在车辆发生的碰撞事故中,经常发生车辆因失控撞上电线杆、树木这类事故,相对于其他形式的碰撞,此类型的碰撞因为缓冲区域较小,侵入量较大,会对乘员舱造成较大的侵入,导致门框变形较大,造成事故后车门打不开的风险。针对此问题,本文对某款新能源商用车进行中心柱碰工况仿真来模拟此类型的事故,并通过实车试验分析其安全性。
早期的碰撞试验都是去碰撞试验室完成的,这会消耗大量的人力物力财力。随着计算机技术的蓬勃发展,有限元法逐渐被应用到了汽车碰撞中,此方法在保证计算精度的同时,节省了大量成本,缩短了研发周期 [2] 。
2. 整车有限元模型的建立
本文研究的正面中心柱碰,在试验场试验时,如图1所示,车辆在牵引绳的作用下,加速到30 Km/h,并撞击在刚性柱上。在仿真实验时,为了更贴近现实,被测车辆同样以30 Km/h的瞬时速度撞击到刚性柱上,如图2所示。
首先对数模进行几何清理,删去不必要的倒角、圆角、工艺孔,尽可能的简化模型 [3] 。
第二步划分网格。汽车主要由钣金件构成,所以对其进行抽中面处理,在其中面划分网格。对于那些不易变形的部件,例如:发动机、泵等则在其表面画一层网格,并设置为刚体 [4] 。
第三步检查网格质量。好的网格质量不仅可以减少大量的计算时间,还可以使结果更加精确。本文中2D网格尺寸设置为10 mm,翘曲度(Warpage)小于5度,长宽比(aspect)小于5,扭曲度(skew)小于60度,雅克比(jacobian)大于0.7。
整车网格如图3所示,共2,655,487个单元,其中2D单元2,077,203个,影响计算精度的三角形单元58,371个,远远小于5%符合精度要求 [5] 。
3. 30FCP整车碰撞模型
此工况目的是为了模拟日常生活中车辆碰撞电线杆、树木等柱状物的情况,针对这种场景,本文车辆速度设置为30 Km/h。考虑到现实生活中碰撞时间较短,本文碰撞时间设置为120 ms。在碰撞模拟中,会涉及到各个部件之间的接触,当中的摩擦系数尤为重要,本文动摩擦系数设置为0.2 [6] ,静摩擦系数设置为0.2 [7] 。针对刚性柱的尺寸问题,因为没有对应的法规,所以各个厂家设置的不同,本次试验采用的是半径310 mm的刚性柱。最终的30FCP整车碰撞模型如图4所示。
4. 仿真结果可信度分析
正面中心柱碰模拟属于非线性有限元分析,它包含几何非线性、材料非线性和接触非线性,此次仿真所用的LS-DYNA求解器特别适合处理碰撞模拟的非线性问题 [8] 。将模型保存为K文件,提交到LS-DYNA中计算,当仿真计算完成后,为了判断模型的可信度,应着重关注模型碰撞过程中的能量变化和质量缩放。
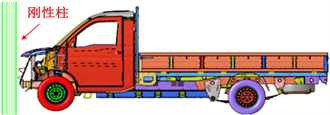
Figure 4. 30FCP vehicle crash model
图4. 30FCP整车碰撞模型
4.1. 能量变化
在计算过程中,由于积分点的不足,会产生沙漏现象,此现象会严重影响计算结果的精度,当沙漏能超过总能量的10%,则认为计算得出的结果是无效的,所以在计算模型的时候,应尽可能降低沙漏能的数值,提高计算精度,通常控制其小于5%。此外,由于网格的初始穿透,会产生负的界面滑移能,对结果产生影响,所以为了结果的准确,也应控制其小于5% [9] 。
图5为碰撞中,各能量的变化曲线,碰撞结束时,总能量为70,372 J,沙漏能为1658 J,占总能量的2.36%,界面滑移能为1986 J,占总能量的2.82%,由此可见沙漏能和界面滑移能均小于5%,在合理的变化范围之内,说明模型建立可靠。
4.2. 质量缩放
除了要检查能量变化曲线,同时也需要关注质量缩放。质量缩放通过*CONTROL_TIMESTEP中的DT2MS控制,当值小于0时,表示质量缩放仅加到计算时间步长小于TSSFAC*︱DT2MS︱的单元上;当值等于0时,表示没有缩放;当值大于0时,表示质量缩放加到所有单元上。以壳单元为例,其时间步长公式如下:
(1)
(2)
四边形单元
(3)
三角形单元
(4)
式中,LS为单元特征长度,A为单元面积,Li (i = 1, 2, 3, 4)为单元长度,c为波的传播速度,E为弹性模量,
为密度,v为泊松比。在动态分析中,特征长度跟划分的网格尺寸有关,修改起来较为繁琐;弹性模量与泊松比和材料有关,不能随意改变。所以只能选择增加非物理的质量来改变密度,从而增大时间步长。但这种方法会对结果产生影响,所以为了同时保证计算速度和计算准确性,需要控制增加的质量小于总质量的5% [10] 。图6为碰撞过程中质量增加图,质量增加最大为69 kg,整车总质量1941 kg,占总质量的3.55%,小于5%,符合要求。
5. 变形分析
本文正面中心柱碰时间设置为120 ms,模型在碰撞过程中的变形云图,如图7所示。在100 ms之后,车辆的变形就基本没有变化了。从图7可知,整个碰撞过程中,并没有零部件飞出,也没有网格发生爆炸的情况,基本实现了车辆对刚性柱的正常碰撞。图8为门框变形量,在60 ms之前,因为车辆前舱变形吸能,门框并没有太大的变形。在60 ms~100 ms,在刚性壁障的连续作用下,前舱吸能能力减弱,随即门框开始受压变形。在100 ms~120 ms,进入门框回弹阶段,车辆动能明显减弱,变形基本消失。同时门框的最大变形量仅为6.1 mm,车门打不开的风险较小,也说明了本车具有很高的安全性能。
6. 实车试验
本次试验车辆,整备质量为1680 Kg,考虑到中心柱碰并没有相应的法规,不采集假人数据,为避免假人损伤,则采用配重160 Kg的方式模拟主驾和副驾的假人,同时再配重136 Kg,模拟货物重量。最终试验质量为1976 Kg。
(a) 门框测量点
(b) 门框变形量
Figure 8. Deformation of doorframe
图8. 门框变形量
车辆在牵引绳的作用下,以30 Km/h的速度撞击刚性柱,造成车辆前舱巨大变形,如图9所示。
7. 试验结果分析
正面中心柱碰,主要模拟汽车在行驶过程中因失控撞向电线杆、树木等柱状物的情况,相对于整车正面100%碰撞,正面中心柱碰缓冲和吸能的空间有限,所以侵入量较大。针对此款新能源商用车,不仅要关注碰撞过程中各零部件的变形量,还要着重关注碰撞过程中电池包的安全。
实车试验结果表明:
1) 试验后通过三坐标仪测得主驾门框的侵入量为6.3 mm,与仿真数据测得的6.1 mm数值上相近,也进一步说明了仿真分析的准确性。
2) 车辆A、B柱在碰撞后,没有明显折弯,表现出优秀的耐撞性(图10)。
3) 气囊正常点爆,保护了乘员安全(图10)。
4) 试验后主、副驾门正常打开,保证了乘员在发生事故后,能快速离开车辆(图10)。
5) 车辆仪表板常亮,且“Ready”灯熄灭,说明车辆蓄电池完好且车辆下电,防止乘客存在触电风险(图11)。
6) 底部电池包并未受到挤压,试验过程中也未发生起火爆炸等现象(图12)。
8. 总结
1) 本文通过HyperMesh联合LS-DYNA建立了某款新能源商用车正面中心柱碰工况的仿真模型,仿真分析结果显示:在正面中心柱碰工况下,车辆前舱受冲击区域虽然存在较大变形,但是吸能充分,所以门框并没有发生较大侵入量,车门打不开的风险较小。
2) 通过实车试验测得门框的侵入量与仿真数据大致相似,且碰撞后车门能够正常打开,同时底部电池包状态良好,表明车辆具有很高的安全性能。
基金项目
广西自然科学基金项目(2013GXNSFAA019319);广西科技计划项目(桂科攻1348005-12);2020年度湖南省高新技术产业科技创新引领计划项目:封闭特定场景无人驾驶通用底盘平台开发关键共性技术研究与应用(2020GK4010);2021年度湖南省创新型省份建设专项项目:湖南省智能线控底盘工程技术研究中心(2022TP2006)。
NOTES
*第一作者。
#通讯作者。