摘要: 砷化镓解理加工是通过解理划片产生初始损伤,然后经过解理裂片获得解理面,因此不同的解理划片工艺参数对后续的解理裂片起到至关重要的作用。本文基于ABAQUS开展对砷化镓划片加工的有限元分析,分析划片损伤过程,以及不同工艺参数下划片过程中切削力的变化。结果表明:入刀时因未得到缓冲导致入刀口的损伤情况较大,划片深度增加一倍,划片力大小增幅达到100%左右,而划片速度增加一倍对划片力的大小几乎不影响,推断出划片载荷对划片损伤作用较大;从仿真结果来看在3 um、60 mm/s工艺参数下划片效果最佳。
Abstract:
GaAs cleavage processing produces initial damage through cleavage slicing, and then obtains cleavage surface through cleavage slicing. Therefore, different cleavage slicing process parameters play a crucial role in subsequent cleavage slicing. Based on ABAQUS, the finite element analysis of gallium arsenide scribing is carried out to analyze the scribing damage process and the change of cutting force in the scribing process under different process parameters. The results show that the damage of the knife edge is relatively large due to the lack of buffer when entering the knife, the scoring depth is doubled, and the scoring force is increased by about 100%, while the doubling of the scoring speed has little effect on the scoring force. It is concluded that the scoring load plays a greater role in the scoring damage; From the simulation results, the scribing effect is the best under the process parameters of 3 um and 60 mm/s.
1. 引言
近年来,随着社会的发展和科技的进步,相关行业对半导体激光器的需求与日俱增,因此人们逐渐重视半导体激光器的应用 [1] 。半导体激光器在激光领域具有许多优点,如结构简单、输出功率高、成形性能优异、尺寸小、易于集成、阈值电流低、可选择波长宽和电光转换效率高 [2] 。随着半导体激光器在全球激光市场的兴起,半导体激光器作为激光领域的核心部件,也成为科学家们的研究重点 [3] 。现有的划片工艺方法所产生的损伤对后续裂片获得的解理面造成大量波纹裂纹,因此研究划片的损伤过程机理至关重要,ABAQUS是最先进的大型通用非线性有限元软件之一,可以用来模拟非常庞大复杂的模型,解决工程实际中大型模型的高度非线性问题 [4] [5] [6] [7] [8] 。因此本研究采用ABAQUS进行砷化镓划片的有限元仿真模型的建立,分析不同工艺参数下砷化镓划片的损伤情况及划片力的波动情况,探究划片损伤机理。
2. 仿真模型的建立
2.1. 砷化镓划片力数学模型
如图1所示四棱刀头划刻过程中的法向切削力
和切向切削力
的切削力模型:
其中A为刀头与工件的接触面积,H为维氏硬度,
为砷化镓变形所产生的阻力,
为四棱刀头中心线与端面间夹角。
2.2. 砷化镓划片有限元仿真模型建立
首先打开ABAQUS软件,进入部件创建模块,通过绘制草图、设定尺寸,完成金刚石刀头和砷化镓工件两个部件的创建。打开材料属性模块,创建砷化镓材料的属性,本模型划片为{100}晶面的<110>晶向,因此将砷化镓材料属性简化为各向同性,在材料属性中定义材料的方向,输入弹性模量、泊松比、剪切模量、屈服应力、剪切损伤等相关参数,见表1,创建截面特性,分配给砷化镓工件,金刚石刀头材料的创建与之相同。打开装配模块,通过平移、旋转等操作,将砷化镓工件与金刚石刀头进行装配。打开相互作用模块,进行刀头与工件的接触设置,设定表面与表面接触,选取对应集。设定边界条件及约束,由于分析结果主要考虑工件的划刻情况,因此设定金刚石刀头为解析刚体,边界条件设定砷化镓工件完全固定,刀头设定位移–幅值控制速度。进行网格划分,金刚石刀头通过种子布局即可划分,砷化镓工件需要对划刻区域进行加密处理。设定分析步,通过对时间的设定即可控制刀头的运动速度,进行多核计算等相关设置,完成对仿真模型的建立,如图2所示。
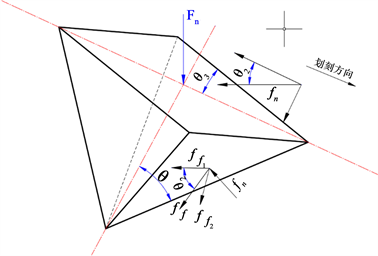
Figure 1. Schematic diagram of scribing force
图1. 划片力示意图
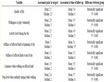
Table 1. <110> crystal orientation material parameters of gallium arsenide {100}
表1. 砷化镓{100}的<110>晶向材料参数
3. 仿真结果及分析
3.1. 划刻过程分析
划刻仿真过程中,我们可以看到首先是刀头与砷化镓晶片产生接触,由于砷化镓晶片的硬度高,而在初始接触时砷化镓晶片变形较小,因此在入刀口时应力瞬间提升,而入刀口接触时相邻的区域应力也瞬间提升到很高,瞬间超越微裂纹扩展的临界值,砷化镓晶片内部的微裂纹开始在入刀口接触时失稳扩展。由图3(a)可以看出应力集中在拉应力所集中的刃前裂纹区域,而与刀头的磨粒刃倒棱面接触的高应力区域则集中于后刀面接触区域。随着刀头的运动,如图3(b)所示砷化镓晶片在含有微裂纹区域产生了局部的断裂,刀头的刃前端下方的拉应力区域(刃前裂纹区域)是砷化镓晶片材料断裂主要区域,而与前刀面接触的压应力区域,是产生切屑的主要区域,由于模型设置的是剪切失效准则,因此与刀刃前端倒棱面接触的区域,产生加压破碎,这一部分区域材料是将来构成切屑的主体部分,因此对加工表面质量影响不大,对切削力的影响很大。如图3显示了划刻的形成过程和等效应力分布。
3.2. 划片力分析
划刻切削加工过程中由于切削力在不断的波动,很难维持稳定且持续的切削力,对加工表面质量的影响极大,并不可消除,因此研究由不同划片工艺参数下引起的切削力波动对实际划片切削加工具有重要的指导意义,划刻切削力对划片加工的机理描述有重要的作用,通过对其不同划刻速度,不同划片的切削深度仿真,研究由不同划片工艺参数下的切削力波动规律,建立划刻切削力与划刻参数之间的关系,可以更加详细的对划片加工过程进行描述(图4)。
在划刻速度为60 mm/s下,划刻深度为2.5 um,3 um,3.5 um,4 um,4.5 um,5 um下,划片力大小平均增幅为25%左右,由此可知划刻深度对划刻切削力有着非常明显的影响。对于脆性材料砷化镓划片过程是一个压碎去除的过程,随着划片深度的增加,刀头的划片力增加,刀头与材料的接触面积增大,划片损伤变大,压碎后的单元无法及时的沿着刀面排出,导致损伤累积有限单元发生网格畸变,最终导致划片力波动幅度较大。
在切削深度为5 um下,划刻速度为10 mm/s,20 mm/s,30 mm/s,40 mm/s,50 mm/s,60 mm/s下,通过对仿真过程的观察可以发现,由图5可知,刀头与工件之间摩擦作用和切屑的变形都使得磨粒产生法向划刻切削力。当划刻进行到一定阶段,划片加工中的法向磨削力变化幅度不大,开始趋于稳定。随着速度的增加,其对法向磨削力的影响不大,不同运动速度下磨粒所受的切向磨削力大小波动很小,切向磨削力便趋于相对稳定,总体上来看,速度的波动对于切向磨削力和法向磨削力的影响不大。因此通过改变磨削线速度来改善磨粒与工件相接触的摩擦情况并不会产生很大的影响。可知在进行划片加工时,通过增大划刻速度只对工件材料产生微弱的影响,并没有使得划刻切削力发生很大的变化。
4. 结论
本文建立四棱刀头划片的物理运动模型确定砷化镓划片加工过程中物理损伤过程,通过abaqus建立砷化镓划片有限元仿真模型,进行计算分析得到整个划片过程,以及划片中切削力的变化过程,得到不同工艺参数下对划刻切削力的影响,结果表明入刀时因未得到缓冲导致入刀口的损伤情况较大,划片深度增加一倍,划片力大小增幅达到100%左右,而划片速度增加一倍对划片力的大小几乎不影响,推断出划片载荷对划片损伤作用较大;从仿真结果来看在3 um、60 mm/s工艺参数下划片效果最佳。