1. 引言
天然气场站是上游天然气开发的要害部位,站内工艺管道是天然气处理和集输的关键设施 [1] 。对于含硫场站而言,管道在服役过程中与酸性采出气长期接触会引起化学腐蚀和电化学腐蚀,因此出现不同程度的壁厚减薄,造成金属壁强度降低,从而引发泄漏失效,极大地影响了场站的平稳运行和安全生产 [2] [3] [4] [5] 。为加强天然气处理厂和集气站安全稳定运行,需定期开展站内设备和工艺设施检修 [6] 。
目前,国内天然气场站站内压力管道的系统性检测及评价策略参照《TSG D7005-2018压力管道定期检验规则——工业管道》进行,但若完全依照该标准进行场站检测,存在检测周期长、检测成本高等问题 [7] 。本文在承压设备系统基于风险的检验(RBI)的策略上,对某油气田内具有代表性的样本平台进行缺陷统计分析,确定了适用于该油气田的站内管道缺陷快速检测作法。
2. 研究现状
目前,国内学者对压力管道检测方案的优化也进行了一定的探索和研究。
游兴越 [8] 对油气管道的腐蚀原理、腐蚀根本原因、对腐蚀检测技术性和防腐措施进行了讨论,得出了油气管道在不一样的自然环境下的最好的腐蚀检测方式和相应的安全防范措施。
张响等 [9] 通过对比分析目前常用的检测技术,提出了使用低频导波、漏磁和超声波测厚组合对站内架空管道的点蚀进行检测。
王磊等 [3] 通过分析天然气集输场站工艺管线腐蚀泄漏的原理及主要影响因素,提出采用多相流、临界流速等方法确定工艺管道中易腐蚀的管道和部位,针对不同的部位采用有针对性的检测方法的检测思路及流程。
孙亮等 [4] 针对胜利油田关键场站压力容器和附属管线腐蚀现状进行分析,并针对性地提出相应的防护措施。
王东 [10] 结合油气集输管道腐蚀检测技术的发展现状,探讨了油气集输管道腐蚀检测技术的应用方法。
3. 样本平台分析
场站缺陷历史资料分析是建立在准确、完整的腐蚀检测数据基础之上的,通过缺陷的数据分析可以了解特定系统当前状况全貌,并获得该系统当前健康状况、缺陷发生以及具体缺陷部位分布特征等关键信息。对缺陷的数据分析结果能为场站的生产控制策略的制定提供科学的依据,有助于管道的安全生产管理,同时也有助于优化后续的监督检测工作。本次研究选取了23个在生产流程、气质特征、地质特征等方面具有代表性的场站,对站内管道缺陷分布特征和类型特征进行分析。
3.1. 历史数据总结
通过对样本场站的历史定期检测报告中发现的缺陷进行归纳,统计发现管线上缺陷共计304处,统计结果见图1~3。
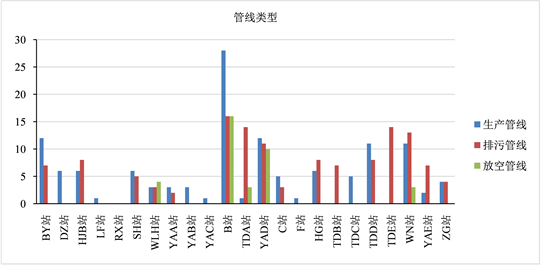
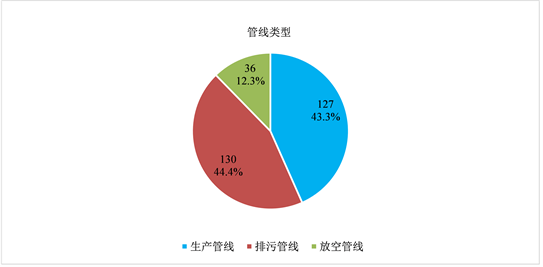
Figure 1. Statistical diagram of distribution of defects in the pipeline within the sample platforms
图1. 样本平台内缺陷在管线上的分布统计图

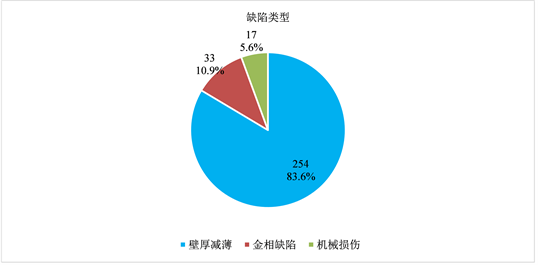
Figure 2. Statistical diagram of defect types in sample platforms
图2. 样本平台内缺陷类型统计图
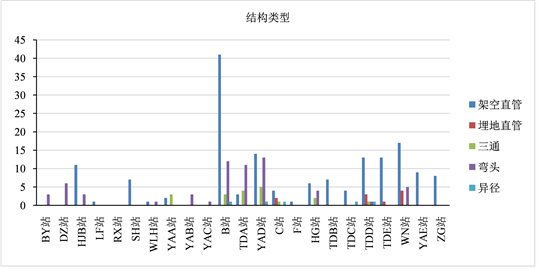
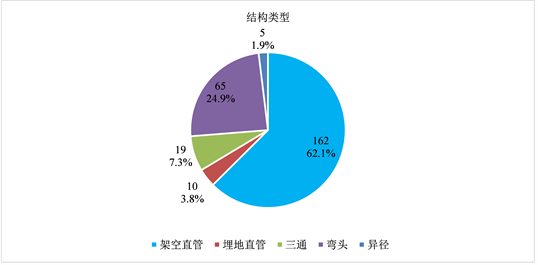
Figure 3. Statistical diagram of distribution of defects in pipeline structure in sample platforms
图3. 样本平台内缺陷在管线结构上的分布统计图
通过对23个平台定期检测报告中发现的缺陷的横向对比可以发现:
1) 站内管道缺陷主要分布于生产管线和排污管线上,放空管线上发现的缺陷相对较少。其中生产管线上共发现127处,占比43.3%;排污管线上共发现130处,占比44.4%;放空管线上共发现36处,占比12.3%。
2) 站内管道缺陷以厚度减薄为主,金相缺陷和机械损伤相对更少。其中发现厚度减薄254处,占比83.6%;发现金相缺陷33处,占比10.9%;发现机械损伤17处,占比5.6%。
3) 站内管道缺陷主要出现在架空直管上,其次是弯头上,三通、埋地直管和异径管上相对更少。其中,架空直管上共发现162处,占比62.1%;弯头上共发现65处,占比24.9%;三通上共发现19处,占比7.3%;埋地直管上共发现10处,占比3.8%;异径管上共发现5处,占比1.9%。
3.2. 不同流态管线腐蚀情况统计
按工艺流程中介质流态将管线进行划分,分为气液两相、液相和气相等三种流态的管线,逐一对上述23个平台的所有缺陷在不同流态管线上的分布数量进行统计,统计情况见图4。
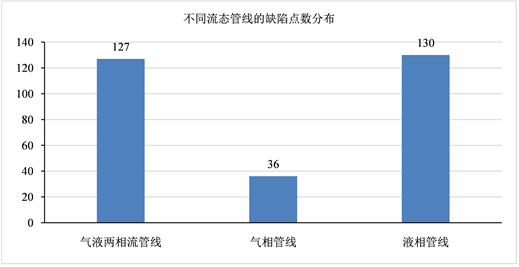
Figure 4. Distribution diagram of corrosion points of pipelines with different flow patterns in the sample platforms
图4. 样本平台中不同流态管线的腐蚀点数分布图
可见气液两相流管线腐蚀点数大于液相管线的腐蚀点数,相较于两者的绝对长度,液相管线的腐蚀点密度远大于气液两相流管线。气相管线的腐蚀点数相较于气液两相和液相管线要小得多。
3.3. 小结
1) 管道的直管段上的腐蚀点分布数量最多,其次是弯头。但相对于直管段的绝对长度,弯头处发生腐蚀的占比尤为显著,突显出弯头腐蚀的高发性。
2) 液相管线的腐蚀点密度远大于气液两相流管线。
4. 推荐作法
考虑到调研的样本平台站内管线特性、生产流程、气质条件等的具有代表性,检测发现的缺陷类型、缺陷分布应基本与某油气田内场站的站内缺陷总体情况保持一致,因此样本平台的缺陷分布及缺陷特征的分析对该油气田其余场站的检测策略与方案的制定具有较大的参照意义。
基于样本平台的缺陷统计,笔者认为,某油气田的检测策略应围绕排污管线、长直管段、弯头和厚度减薄进行制定。基于承压设备基于风险的检验(RBI)的规程,优化某油气田站内管线关键部件及位置对场站内管道缺陷检测技术,以管线和结构进行区分,调整站内管道缺陷快速检测应用的检测技术组合。
4.1. 架空管线检测
1) 长直管段上的缺陷主要表现为介质腐蚀和垢下腐蚀等因素造成的腐蚀减薄,可使用超声波C扫描和超声波B扫描检出。
2) 水平U形弯段直管的腐蚀减薄以介质腐蚀、垢下腐蚀和积液腐蚀为主,使用超声波C扫描和超声波B扫描检出这类缺陷。
3) 异形管件
① 弯头出口内弯及邻近直管以气相、气液相紊流冲刷腐蚀造成的减薄为主,使用超声波B扫描可以检出,因表面不光滑、管径过小或探头无法放置等无法使用超声类检测时,可使用DR射线检出缺陷,但无法准确判定剩余厚度。
② 弯头出口外弯及邻近直管上的腐蚀减薄可使用超声波C扫描和超声波B扫描组合检出。
③ 焊缝上的腐蚀及缺陷多由冲刷、热应力及施工等造成,使用涡流阵列探伤仪可有效检出表面裂纹,使用超声相控阵可检测内部埋藏裂纹,因表面不光滑等无法使用超声类检测的,可使用DR射线检出缺陷,但无法准确判定剩余厚度。
④ 其余可能出现冲刷腐蚀的部位可使用超声波B扫描进行检测,因表面不光滑、管径过小或探头无法放置等无法使用超声类检测时,可使用DR射线检出缺陷,但无法准确判定剩余厚度。
4) 气压机进出口管线
① 入口管线上可能因振动、应力腐蚀等形成裂纹,可使用涡流阵列探伤仪检测表面裂纹,使用超声相控阵检测内部埋藏裂纹。
② 出口管线使用涡流阵列探伤仪可有效检出表面裂纹,使用超声相控阵可检测内部埋藏裂纹。
③ 进出口弯头可能因腐蚀或管件材质本身出现分层,使用超声波B扫描可以检测出这类缺陷。
④ 管线内的腐蚀减薄可使用超声波C扫描和超声波B扫描组合检出,因表面不光滑等无法使用超声类检测的,可使用DR射线检出缺陷,但无法准确判定剩余厚度。
⑤ 压力表处可能因振动等出现泄漏,可通过宏观检查、肥皂水检漏等方法判断。
4.2. 埋地管线检测
1) 入地直管防腐层端口可能出现防腐层剥离开裂、土壤–空气界面腐蚀,这类缺陷可通过宏观目视检测发现。
2) 入地直管及弯头因雨水浸泡、土壤含碱等出现的腐蚀可通过开挖直接检测。
3) 水平段管线可能因防腐层破损、老化等造成的土壤腐蚀形成管线外腐蚀,此类腐蚀缺陷可通过开挖、剥除防腐层、宏观目视检测发现。
4) 水平段管线底部(5~7点钟)可能积液腐蚀、垢下腐蚀、细菌腐蚀等形成内部腐蚀减薄,可在开挖后使用超声波C扫描和超声波B扫描组合精确检出这类缺陷,因表面不光滑等无法使用超声类检测的,可使用DR射线检出缺陷,但无法准确判定剩余厚度。
5) 斜直管线中上部可能因气液相冲刷腐蚀、凝液腐蚀、细菌腐蚀等形成腐蚀减薄,可通过开挖后使用超声波C扫描和超声波B扫描组合精确检测,因表面不光滑等无法使用超声类检测的,可使用DR射线检出缺陷,但无法准确判定剩余厚度。
5. 现场应用
应用优化后的缺陷快速检测方案进行场站站内管道的无损检测,将检测结果与近期检测报告进行对比,对比结果见表1,发现历史资料中的缺陷均能检出,且发现管壁上的腐蚀有了一定的发展。
本轮检测剩余壁厚相对原剩余壁厚的壁厚减薄在0.12 mm~1.19 mm以内,剩余壁厚在79.76%~95.78%以内。
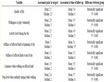
Table 1. Comparison between historical data of Q Station and field detection (Unit: mm)
表1. Q站历史资料与现场检测对比(单位:mm)
从剩余壁厚对比上一轮检测发现,对于较短的检测周期而言,即便壁厚减薄最小的部位(分离器来气至吸收塔管线)的腐蚀速率也超过了0.2 mm/a,如此大的腐蚀增长是不科学的。推测是因为扫描模式的不同,超声波B扫描排除了管道外油漆涂层的厚度,同时可能由于本轮检测与上一次超声C扫描检测的区域不同,导致取得的缺陷位置不同,从而出现不正常的腐蚀增长。
6. 结语
综上所述,通过应用实施含硫场站的缺陷快速检测作法,在实际检测中选择合适的技术手段,可以在保证检出缺陷和检测精度的同时,极大地简化作业流程,减少检测时间和资金成本,对某油气田场站站内管道缺陷的科学采集及平台的安全生产管理提供了充分的支持。
缺陷快速检测作法是基于样本平台的数据分析进行策略调整的,因此合理选择并继续增加样本平台的数量有利于完善某油气田含硫场站的缺陷快速检测作法,以增强缺陷快速检测作法的普适性。
NOTES
*通讯作者。