1. 引言
感存算一体化芯片晶圆级集成主要包括混合键合技术、表面平坦化技术和晶圆级减薄技术等关键工艺模块。定制化的混合键合技术,对于高密度垂直互联的技术要求,主要优化铜表面平坦化及键合工艺环节,其中,铜CMP平坦化技术工艺能否在较短的研磨时间取得较高的平整度控制决定了键合缺陷的水平及研磨效率 [1] 。
传统铜CMP采用两步研磨法,第一步用铜研磨来磨掉晶圆表面的大部分铜;第二步用较低的研磨速率精磨与阻挡层接触的铜,并通过终点侦测技术使研磨停在介质层上。由于第二步精细研磨需要很好的控制沟槽内和氧化层上面的金属,所以研磨时间较久,效率较低,且较容易形成蝶形和侵蚀缺陷,导致晶圆表面的不平整。
本文在传统铜CMP两步研磨工艺的基础上对工艺方法进行优化,提出三步研磨工艺方法,通过前两步研磨以去除晶圆沟槽上的金属铜,并在此基础上进行特定条件的过抛处理,以确保残余铜完全去除。同时,增加第三道研磨工序,对沟槽和旁边的氧化层进行减薄到工艺需求的厚度。
结果显示,采用三步研磨法后,通过优化第二步残留铜研磨工艺,调整研磨液流量,设定不同研磨工艺压力参数等措施,不仅能够使氧化层减薄到和金属铜相同的厚度水平,形成较好的表面形貌和最小的蝶形缺陷,同时研磨时间与传统两步研磨工艺相当,不会因为增加工序而影响整体工艺的研磨效率。
目前国内外有学者研究了CMP工艺参数如抛光头压力、抛光头和抛盘的转速、抛光液的体积流量等对抛光效果的影响,并取得了一定的研究成果。2013年,张宏远等人 [2] 通过改变抛光压力、抛光液体积流量等工艺条件得到了最佳铜膜抛光去除速率和高抛光后表面质量。2014年,孙薇等人 [3] 通过优化多层铜布线CMP抛光工艺参数(抛光压力、抛光液体积流量等)有效地解决了划伤、蚀坑等表面缺陷问题。同年,袁浩博等人 [4] 通过实验表明在1.5 psi抛光压力、抛头和抛盘的转速分别为87和93 r/min、抛光液体积流量300 mL/min的工艺条件下,可以得到良好的平坦化效果。2021年,栾晓东等人 [5] 同样研究了中心压力、抛头和抛盘的转速以及抛光液体积流量对铜互连阻挡层去除速率一致性的影响。由此,在通过优化工艺方法、控制研磨液流量、调节研磨压力上等措施的研究却鲜有报道。
2. 工艺实施细节与工艺参数设计
本文在传统铜CMP两步研磨工艺的基础上,设计了铜CMP三步研磨工艺,并对关键工序的工艺参数进行了详细分析。
2.1. 工艺实施细节
铜CMP三步研磨工艺具体实施细节如图1所示。
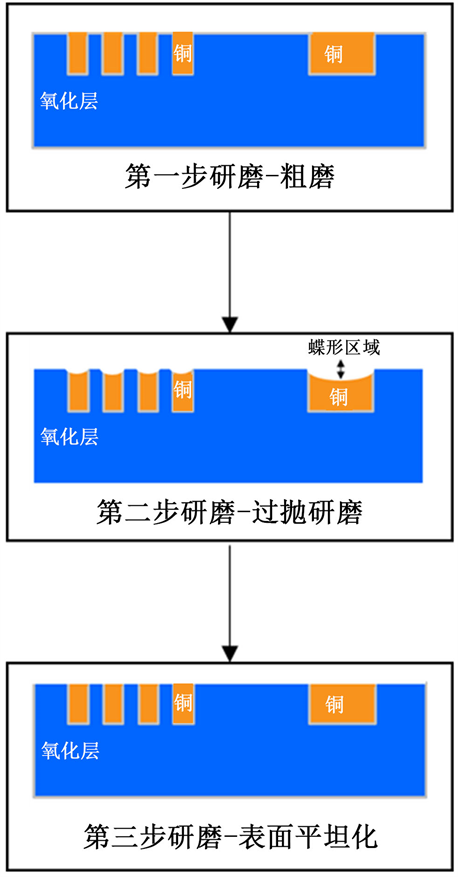
Figure 1. Flow chart of CMP by three steps
图1. 铜CMP三步研磨工艺
第一步研磨:CMP三步研磨法中第一步研磨工艺基本沿用了两步法研磨工艺中第一步研磨工艺,通过研磨盘进行大压力铜的去除,对晶圆表面进行粗磨,去除沟槽上方大部分的铜。主要的区别在于两步法研磨工艺因为没有氧化层研磨,所以在第一研磨盘一般都设置残留相对较多的铜,一般会有500 A左右的铜安排在第二研磨盘;三步研磨工艺相较于二步研磨法可以设置较薄厚度铜层的研磨停止点,第一步研磨量较多,所以该工序的时间要略多于两步法研磨,但由于第一研磨盘的研磨速度最快,效率最高,可以有效减轻第二道研磨工序的压力,提高效率。
第二步研磨:CMP三步研磨法中第二步研磨工艺在原有两步法研磨工艺中第二步研磨工艺的基础上,分别从调整研磨压力和研磨液流量、减少研磨时间上进行了优化。
在调整研磨压力和研磨液流量方面,由于两步法研磨工艺中,第二步研磨时一般用最小的压力和研磨速率最小的研磨液流量控制去除沟槽上方剩余的金属铜,精细控制沟槽上方剩余的金属铜去除的同时又不产生较大的蝶形缺陷。三步研磨工艺有第三步氧化层研磨,所以相较于二步研磨法蝶形缺陷的接受度较高,可以设置一个较短时间,较快速度的工艺参数,实现第二研磨盘快速高效研磨。也可以减少二步研磨法研磨时间久而产生的缺陷以及研磨终点设置太小而导致的研磨终点侦测不到的机台故障。
改善研磨时间方面,由于两步法研磨工艺中,第二研磨盘通常将氧化层上方的金属铜全部研磨完作为研磨探测终点,在探测到研磨终点时仍然继续研磨,探测到研磨终点后的研磨时间一般称为过抛时间 [3] 。为确保完全去除沟槽上方剩余的金属铜,过抛过程中会设定一个较长的过抛时间,在过抛过程中会形成具有铜凹陷的蝶形结构,而且过抛时间越长蝶形的深度越大,铜线宽越大蝶形的深度越大 [6] 。采用三步研磨后,因为还有第三步介质层研磨,会对平坦化质量和蝶形缺陷做最终的优化处理,所以对蝶形缺陷的接受度较高,第二研磨盘可以设置较短的过抛时间和较快的研磨速度。这样可以减轻第二道研磨工序的压力,提高效率。
第三步研磨:CMP三步研磨法相较于两步法研磨工艺增加了第三道研磨工序,主要因为要实现高平坦度和低蝶形缺陷的晶圆表面,二步研磨法有着研磨终点较难侦测,研磨时间较久,较大蝶形缺陷的局限。增加第三研磨盘的作用是去除剩余少量凹凸不平的介质层,使留下的介质层的厚度满足制程要求,最终全局平坦化要求达到最佳效果。
研磨时间方面,根据第二步研磨剩下的蝶形深度估算需要研磨的介质层厚度,通过设定研磨时间实现凹凸不平介质层的全部去除。
研磨压力和研磨液流量方面,通过选择对金属和氧化层选择比较高的含二氧化硅研磨液,主要对晶圆表面的沟槽旁边的氧化层进行化学机械研磨,同时增加适当浓度的氧化剂抑制铜的去除速率,主要使得凹凸不平突出的介质层移除,实现最佳的研磨平坦化质量。氧化剂H2O2加入后能迅速将凹处铜膜氧化成不溶于水的Cu2O、CuO和Cu(OH)2产物,在铜膜表面形成钝化膜,氧化剂浓度的增加,形成的钝化膜越致密,对铜膜的钝化作用越强,机械去除的难度增加,铜膜去除速率也就下降。在氧化剂含量较少时,凹处铜膜的钝化作用不强,因此凹凸处速率差不是很明显,难以实现平坦化,当氧化剂含量很大时,铜膜钝化作用加强,凹凸速率差增加,平坦化性能大大提高。
2.2. 工艺参数设计
本文工艺方案所选用设备及器件型号等信息如下:
1) 化学机械研磨机台选用国产天津华海清科公司Universal-300E型;
2) 抛光垫选用美国杜邦IC1000标准型。
本文工艺方案所选试验材料规格等信息如下:
1) 抛光材料选用12英寸铜布线晶圆片;
2) 抛光液第一和第二研磨盘选用国产安集科技生产的U3100抛光液,第三研磨盘选用国产安集科技生产的H6T抛光液。
根据化学机械抛光材料去除速率Preston公式 [7] 如下:
RR = K * P * V。
其中,RR代表材料去除速率,K代表比例常数通常由经验和材料的种类决定,P代表硅晶圆在化学机械抛光中的下压力,V则代表硅晶圆在抛光过程中硅晶圆相对于抛光垫的速度。
从公式中来看,硅晶圆相对于抛光垫的速度越快,材料去除速率越大。在实际生产中,化学机械抛光从来不是一个单纯的机械作用,化学反应作用在化学机械抛光中起了非常重要的作用,尤其是在铜和钨等金属材料的化学机械抛光过程中。而铜金属的化学反应中研磨液流量又是决定化学反应的关键因素,所以本文从晶圆在化学机械抛光中的下压力以及研磨液流量对化学机械抛光材料去除速率及非均匀性影响进行讨论。
2.2.1. 工艺压力对研磨效率影响分析
通过金属铜在国产铜研磨液不同压力条件下的研磨速率的DOE实验,工艺条件:研磨头转速/研磨垫转速 = 75/70rpm,研磨液流量 = 300 ml/min,通过设置不同的工艺压力可以得到如下数据,据此得到研磨速率与工艺压力的关系曲线图,如图2所示。
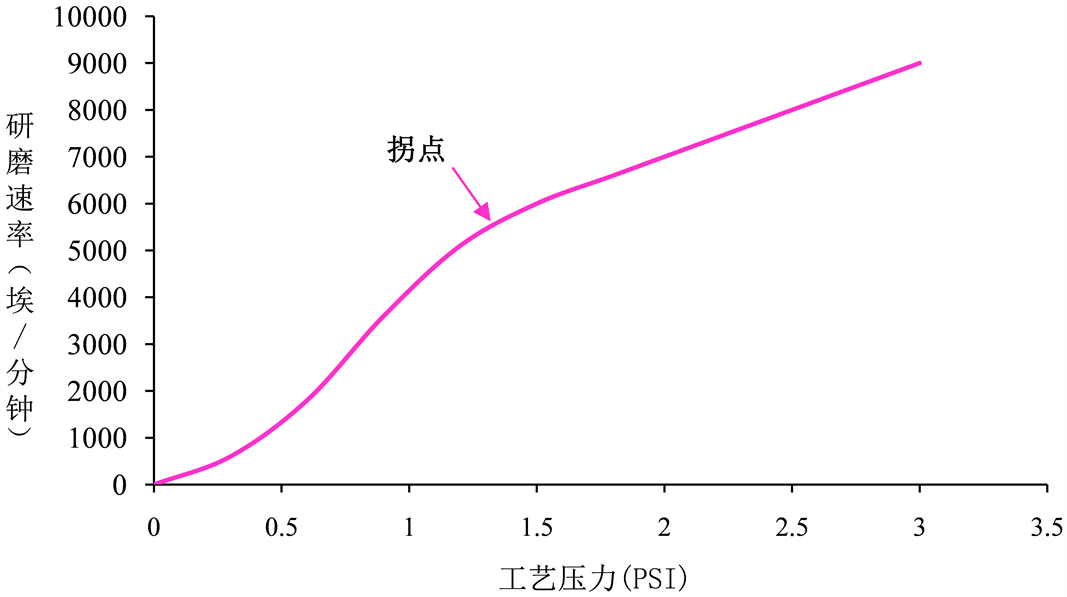
Figure 2. The relationship between grinding rate and process pressure
图2. 研磨速率与工艺压力关系曲线
图中可以看出,曲线存在一个压力拐点,当压力大于拐点时,研磨速率线性增加;当压力小于拐点时,研磨速率显著下降。压力从1.5 psi到3 psi过程中,铜的去除速率变化很大,呈直线增加。当研磨压力很小时,铜的去除速率很小,这是因为没有机械力的去除,只有研磨液和铜的化学反应;当压力逐渐增加时,可以将研磨液与铜离子发生络合反应产生的络合物和氧化铜移除掉,不断暴露出新的铜表面,避免过多化合态的铜在表面堆积;随着压力机械作用增加到一定大小,越容易克服化学反应所需的势垒,此时研磨速度基本是稳定随着压力线性增加的,因为研磨液的氧化剂是一定的,被氧化的铜离子数是一定的,铜的去除速率主要依靠研磨压力去除化合态的铜速率。但是研磨压力也会对表面形貌和表面缺陷产生较大影响,特别当表面大部分铜已经去除阻挡层和氧化介质层露出的时候,所以针对第二研磨盘,会在研磨速度最佳的时候选择最小的压力。
基于上述分析过程,第一研磨盘的工艺压力都会在条件允许的情况下尽量选择大的工艺压力,在实验要求的范围内从图中可知当压力为3 psi时最佳。从而增加研磨速率,避开工艺拐点,增加机台产能。第二研磨盘的工艺压力尽量选择线性条件下较小的工艺压力,从图中可以看到当压力为1.5 psi时最佳,从而尽量避开氧化层缺陷及沟槽铜过度研磨导致的缺陷增多和蝶形缺陷超过工艺规格。但是三步研磨法对沟槽铜过度研磨有更大的工艺窗口,因此可以设置2 psi作为工艺压力实现。
2.2.2. 抛光液流量对研磨效率影响分析
通过对金属铜在不同研磨液流量条件下研磨速率的DOE实验,工艺条件:平均研磨压力 = 2 psi,研磨头转速/研磨盘转速 = 75/70rpm,通过设置不同的抛光液流量可以得到如下数据,据此得到研磨速率与抛光液流量的关系曲线图,如图3所示。
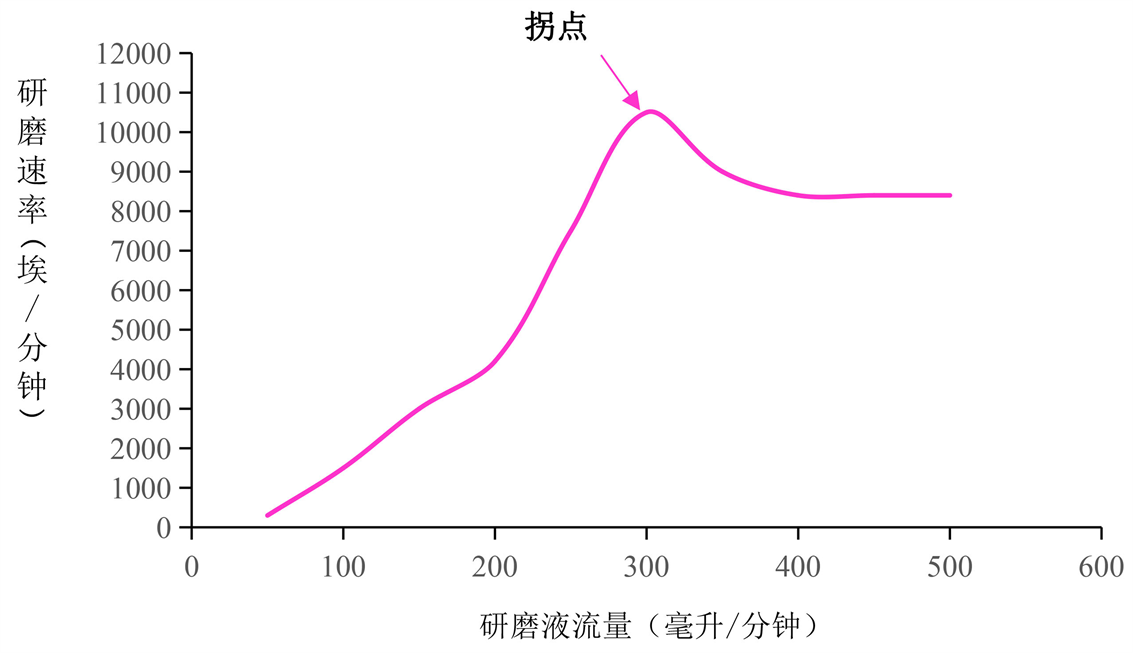
Figure 3. The relationship between grinding rate and polishing fluid flow
图3. 研磨速率与抛光液流量关系曲线
图中可以看出,当随着抛光液流量增加,晶圆表面的研磨颗粒增多,研磨速率随之增加;当流量增加到时350 mL/min研磨颗粒和抑制剂达到平衡并开始由抑制剂占主导,研磨速率随之下降;当流量增加到450 mL/min时,抑制剂趋于饱和,此时研磨速率保持稳定,继续增加抛光液流速则提升了研磨成本,这是因为抛光液流量逐渐增加,传递到抛光垫上的反应物增加,反应产物也能迅速带离抛光垫表面,促进反应加快,抛光速率略有提高。在350 ml/min时,速率达到最快。但是当流量过快时,抛光液将不能在抛光垫上均匀的分布,抛光液流动性过大造成反应不充分,另外,流量过大也会在抛光垫与抛光材料之间形成的钝化膜变厚,机械研磨作用相对下降,最终造成速率略有下降,因此与其他工艺参数相比流量对速率的影响作用不是很大。
基于上述分析过程,第一研磨盘和第二研磨盘都选择流量为350 ml/min时作为铜的CMP的工艺条件。
经过第一研磨盘和第二研磨盘研磨后的剩余蝶形缺陷高度约为200 A左右,第三研磨盘采用国产安集科技生产的H6T抛光液,是一款对金属和氧化层选择比较高的含较高浓度氧化剂及二氧化硅研磨液,因为介质层的研磨的主要靠机械力去除的特性,本文采用介质层常规压力和流量设置,选取工艺压力1 psi,研磨液流量300 ml/min作为工艺参数。
2.2.3. 三步研磨法工艺参数设计
综上,优化后的CMP三步研磨法工艺参数如表1所示:
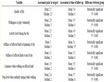
Table 1. The parameters of CMP by three-step
表1. 三步研磨工艺参数
3. 实施效果
基于上述工艺参数,选取10片12英寸铜布线晶圆片样本进行测试,其中,1#~5#样本采用三步研磨法工艺,5#~10#样本采用两步研磨法工艺,分别对其对成品蝶形缺陷深度、均匀度、研磨时间等指标进行测量,测量结果如表2所示。
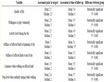
Table 2. The measurement results of water uniformity
表2. 晶圆均匀度测量结果
测量结果显示,通过上述控制过抛处理环节的抛光液流速和施加压力,通过三步研磨法实验的平均均匀度是1.27%,优于二步研磨法的平均均匀度2.05%,能够将金属铜的蝶形缺陷深度减小至10 nm以下,均匀度小于2%。
为能了解CMP三步研磨法对抛光效率的影响,对CMP三步研磨法和两步研磨法工艺过程的不同工序的主要研磨时间进行了整理,测量结果如表3所示。
测量结果显示,通过上述三步研磨法工艺路线设置及对应的抛光液流速和施加压力等工艺参数设定,三步研磨法实验的平均主要研磨时间是130.4 s,优于二步研磨法的平均主要研磨时间142.8 s,实现了降低工艺缺陷的同时,对整体加工时间也不会有太多增加。
综上,通过优化第二步残留铜研磨工艺,设定不同研磨工艺压力等措施,增加第三步氧化层研磨工艺,不仅能够使氧化层减薄到和金属铜相同的厚度水平,形成较好的表面形貌和最小的蝶形缺陷,同时研磨时间与传统两步研磨工艺相当,不会因为增加工序而影响整体工艺的研磨效率。
4. 结语
本文提出用于一体化芯片晶圆集成的铜孔表面平坦化的三步研磨工艺,通过优化工艺方法、设定研磨液流量研磨压力等关键工艺参数等措施,将金属铜的蝶形缺陷深度减小至10 nm以下,均匀度小于2%,最终实现被抛光的晶圆表面达到高度平坦化、极小的铜通孔度凹陷度(纳米级),低表面粗糙度和低缺陷的要求,同时也保证一定的工艺成本控制,为定制化混合键合技术提供保障。