1. 引言
工业革命为人类带来技术发展的同时,大量消耗煤炭,石油等化石燃料,产生了大量二氧化碳、甲烷、臭氧等温室气体,使得全球温室效应日益严重。国际能源机构指出,制造业碳排放已达全球碳排放占比30%以上 [1] 。我国是制造大国,目前制造业的地位越来越突出,其制造能耗大,是温室气体排放的主要源头 [2] 。因此,为了实现低碳制造,如何描述制造生产过程排放状况,并分析制造过程碳排放特性以及碳源分布流量、碳排放全过程变化规律,是当前迫切需要解决的科学问题之一 [3] 。
针对低碳制造过程中碳排放研究,Narita等 [4] 结合生命周期理论分析机加工过程的环境影响预测系统,通过计算切削工具状态、冷却液量以及金属切屑量等各加工组成部分在机加工过程中的电能消耗量来探究其对环境的影响情况。Branker等 [5] 为优化能源和环境成本加工工艺参数共同提出加工过程的微观经济模型,并在此基础上结合生命周期评估法利用实验就该模型对碳排放和成本的作用展开深入的探究。李先广等 [6] 以干式切削齿轮为实验对象,探究其碳排放特性并在此基础上构建齿轮加工核算模型核算碳排放量。
在低碳加工参数优化方面,Bhushan等 [7] 通过在数控机床上的实验探究以最低能耗和刀具最大寿命为优化目标的基于铝合金SiC颗粒复合材料的加工过程。Yi等 [8] 以碳排放和加工时间为最优目的,探究机器加工过程中切削参数以最大程度减少碳排放的潜力。李聪波等 [9] 为实现数控加工低碳化,建立高效低碳多目标优化模型,并在此基础上使用复合型法对此求解,最后通过具体实例证明分析。刘琼等 [10] 提出以完工时间最少、车间设备利用率最高为最优目的,建立优化调度模型,使用NSGA-II为其求解。以上研究大多是针对切削,铣削加工进行参数优化,目前针对低碳磨削加工方面的研究较少。在轴类零件的加工工艺流程中,磨削加工也是非常重要的一环,为达到轴的表面精度要求,往往要对轴类零件进行粗磨和精磨加工,而目前针对轴类零件低碳磨削方面的研究也比较有限。
针对上述问题,本文综合考虑磨床、磨具性能约束,建立了轴类零件磨削加工过程中以低碳、低成本为目标的工艺参数优化模型,最后使用改进粒子群算法(Bird Swarm Algorithm, BSA)对所建模型进行求解,并结合实例验证所建模型的有效性。
2. 轴类零件磨削加工工艺参数优化模型建立
2.1. 优化变量确定
在磨削加工过程中,影响碳排放和加工成本的主要工艺参数为工作台进给速度
,工件转速
和磨削深度
。因此,本文选择以上3种铣削工艺参数作为优化变量。
2.2. 优化目标函数
目标函数在体现优化目标的同时,必须以反映客观问题为前提。在国家发布3060双碳目标的背景下,磨削加工过程中的碳排放和生产成本是我们亟待改善的方面。因此,本文选取碳排放量和加工成本作为优化目标函数。
2.2.1. 磨削加工过程碳排放函数
磨削加工过程中碳排放源主要包括磨床运转耗能碳排放,轴材料制备碳排放,废屑回收处理碳排放,砂轮磨损碳排放以及磨削液消耗和废液处理碳排放。由于被磨除材料体积与轴类零件尺寸参数紧密相关,与磨削用量参数并无直接关系,因此被磨除材料消耗和废屑回收处理产生的碳排放并不随着磨削用量的改变而发生变化,故在轴类零件磨削加工碳排放函数中不考虑其原材料消耗因素。基于以上分析,轴类零件磨削加工碳排放只需考虑:1) 磨床能耗、2) 砂轮磨损和3) 磨削液消耗三个因素。
1) 磨床能耗碳排放
轴类零件磨削过程能耗核算主要是考虑其加工过程中磨床因消耗的电能产生的碳排放量,其计算公式如下:
(1)
式中,
为轴类零件磨削加工过程磨床因电能消耗产生的碳排放,
为电能碳排放系数,
为轴类零件磨削加工过程磨床总能耗。
磨床在运行时有加工和空载两种状态,当磨床处于空载时产生空载功率。当磨床处于负载状态时,除了产生切削功率以外,还会产生附加载荷损耗功率,因此磨床总输入功率由空载功率、切削功率以及附加载荷损耗功率组成 [11] 。空载功率是与转速近似成二次函数关系,附加载荷损耗与载荷成一个线性的比例关系,具体公式如下所示:
(2)
式中,
为空载功率,n为转速,
和
为系数。
(3)
式中,
为附加载荷损耗功率,
为负载载荷损耗系数,取值范围为0.15~0.25的常数,实际应用中凭经验取值,本文取值0.2。
切削功率计算公式如下所示:
(4)
式中,
为切削功率。
由于磨床的变速、负载变化以及其他一些原因,磨床运转是动态的,但是在允许范围内,其状态可以被看成是稳态的,稳态下机床功率平衡方程公式如下:
(5)
式中,
为机床总输入功率,磨床总输入功率
和空载功率
近似看成固定不变。
由于能量的流动过程包括输入、损耗、存储和输出,遵守能量守恒原理,刘飞等 [12] 根据机床功率平衡方程导出了其能量近似平衡方程,公式如下:
(6)
式中,
为空载时间,
为磨削加工时间。
根据公式(1)和公式(6),轴类零件磨削加工过程中的碳排放核算模型可以表示为:
(7)
2) 砂轮磨损消耗碳排放
轴类零件磨削加工过程中砂轮磨损消耗碳排放是指因砂轮损耗而产生的碳排放。轴类零件磨削加工过程砂轮磨损消耗碳排放计算公式如下:
(8)
式中,
为轴类零件磨削加工过程中砂轮磨损碳排放,
为砂轮材料碳排放因子,
为砂轮磨损质量。
其中,量化砂轮损耗的方法有很多,如直接测量等方法,但因操作复杂不易使用,研究表明 [13] ,磨削比是指工件被去除材料的体积与砂轮损耗体积之比,该值近似一个常数。目前通常利用磨削比的换算获得砂轮磨损量,其计算公式如下:
(9)
式中,G为磨削比,近似一个常量,
为工件磨除体积,
为砂轮损耗体积。
磨削比与机械加工工艺和加工条件相关,比如对于平面磨削和外圆磨削而言,两者的磨削比是不同的,外圆磨削的磨削比计算公式如下:
(10)
式中,
为工件磨削长度,
为原始工件外圆直径,
为最终工件外圆直径,
为砂轮宽度,
为原始砂轮直径,
为最终砂轮外圆直径。
因此,根据外圆磨削比的公式可得砂轮磨损量计算公式如下:
(11)
式中,
为砂轮质量,
为砂轮的可用体积。
基于轴类零件磨削加工过程中砂轮磨损消耗碳排放计算公式(8)并且结合砂轮磨损量计算公式(11)可得轴类零件磨削加工过程中砂轮磨损消耗碳排放模型为:
(12)
3) 磨削液消耗碳排放
核算磨削液消耗碳排放主要考虑因磨削液制备以及废液回收处理而消耗能源产生的碳排放。磨削液更换周期较长,对于磨削加工过程而言,采用时间折算方法 [12] ,则轴类零件磨削加工过程磨削液消耗碳排放核算模型为:
(13)
式中,
为磨削液更换周期,
为配置磨削液碳排放因子,
为废液处理碳排放因子,
为循环周期磨削液使用量,
为循环周期废磨削液量。
根据上述轴类零件磨削加工能耗和物料消耗分析,轴类零件磨削加工碳排放
包括磨床运转耗能碳排放,砂轮磨损碳排放以及磨削液消耗碳排放,因此轴类零件磨削加工碳排放核算模型为:
(14)
2.2.2. 磨削加工过程成本函数
除了考虑低碳因素以外,加工成本因素也是建立优化模型中值得考虑的重要部分,磨削加工成本主要分为加工费用和损耗费用两个方面 [14] 。磨床加工体系能耗主要由各个耗能部件的能量消耗组成,忽略人力等其他成本因素,其加工费用主要是由磨床整个系统运转消耗的电能成本构成,而损耗费用包含砂轮损耗和磨削液消耗,因此轴类零件外圆精磨加工阶段加工成本模型主要有磨床运转耗能、砂轮损耗和磨削液消耗成本组成。磨床运转耗能成本为:
(15)
式中,
为轴类零件外圆精磨加工磨床电能消耗成本,
为轴类零件精磨加工过程磨床整个系统运转总耗电量,
为当前地区电能单价。
砂轮磨具损耗成本为:
(16)
式中,
为轴类零件外圆精磨加工砂轮磨损成本,
为砂轮费用。
磨削液消耗成本为:
(17)
式中,
为轴类零件外圆精磨加工圆磨削液消耗成本,
为轴类零件外圆精磨加工所用时间,
为磨削液循环使用周期,
为磨削液的循环使用量,
为磨削液单价。
综合考虑磨床加工耗能成本、砂轮磨损成本和磨削液消耗成本因素,轴类零件外圆精磨加工阶段加工成本模型为:
(18)
2.3. 约束条件
磨削加工工艺参数的选择须符合机械加工系统各种限制条件。根据实际加工情况,将约束调节分为表面粗糙度约束、磨床功率约束、头架主轴转速约束、工作台纵向进给量约束。
1) 表面粗糙度约束
轴类零件对表面粗糙度有着较高的要求,保证表面质量是核算磨削碳排放的前提,影响其表面粗糙度的要素有很多,如工件材料的化学部分、磨削深度以及磨削液等 [1] 。加工表面粗糙度应满足:
(19)
式中,Ra为表面粗糙度,
是与被磨材料物理力学性能相关系数,
是砂轮宽度,
是与砂轮粒度相关系数,
是与无火花磨削次数相关系数,
是与磨削液相关系数。
2) 磨床功率约束
由轴类零件外圆精磨加工碳排放核算结果分析不同的工作台进给速度和工件圆周速度都会导致碳排放量不同,并且通过切向磨削力经验计算公式可知切向磨削力的大小与磨削深度、工件圆周速度、工作台进给量等工艺参数相关,增加工作台进给速度和工件圆周速度会导致其切向磨削力增加,其有效切削功率也会提高,但是如果磨削功率超过磨床额定功率,对磨床造成损坏,因此探究磨削过程碳排放的同时需要考虑磨床功率因素。切向磨削力产生的切削功率应满足低于磨床功率的条件,即:
(20)
式中,
是磨床主电动机的额定功率,
是磨床传动效率。
3) 头架主轴转速约束
磨床头架主轴转速都有明确的转速范围,以型号为M1432A磨床为例,该磨床头架主轴由双速电动机驱动,轴I和轴II之间有3级的V带塔轮变速 [15] ,所以工件可获得6级转速。其最高最低转速参考M1432A磨床头架主轴转速表1,因此M1432A头架主轴转速应满足:
(21)
式中,n为头架主轴转速,
为头架主轴转速范围内最小值,
为头架主轴范围内最大值。
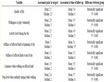
Table 1. M1432A basic technical parameter data of grinding machine
表1. M1432A磨床基本技术参数数据
4) 工作台纵向进给量约束
由轴类零件外圆精磨加工碳排放核算结果可知不同工作台进给速度也会影响着其产生的碳排放量。除此之外,工作台进给量也直接影响着磨削效率和表面质量。选择较低进给量时,其磨削效率较低,选择较大进给速度时会加剧磨削热对表面质量的影响,因此根据实际轴类零件加工零件的基本数据信息结合机械切削使用手册选择合适的进给量,进给量应满足:
(22)
式中,f为工作台纵向进给量,
为最小进给量,
为最大进给量。
3. 改进粒子群算法
3.1. 粒子群算法
粒子群算法(Particle Swarm Optimization, PSO)是由J. Kennedy和R. C. Eberhart等于1995年提出的,该算法起初是受到了鸟群觅食行为的启发,后发展成了一种基于简单社会模型的智能算法。PSO算法由系统随机初始化一组粒子,通过不断迭代搜索出最优解,迭代公式如下:
(23)
(24)
式中,
,
,k表示粒子当前迭代的次数,
表示在第k次迭代时第i个粒子的第d维速度;
表示在第k次迭代时第i个粒子在第d维的个体极值的坐标;
表示在第k次迭代时第i个粒子的第d维位置分量;
表示在k次迭代时粒子的最优解向量中的第d维分量;
表示速度的惯性权重;c1,c2表示学习因子;r1,r2为(0, 1)之间随机的实数。粒子群算法简单、计算方便、求解速度快,但由于在运行的过程中种群粒子的多样性损失比较严重,所以易陷入局部最优解,产生早熟。
3.2. 改进粒子群算法
由3.1结论可知,由于PSO算法容易产生早熟现象,这可能就会使得计算结果并不是局部最优解,为了防止此类现象发生,这里提出了改进粒子群算法:把遗传算法中的交叉和变异操作引入到传统粒子群算法中,通过改变种群的分割策略来使粒子群算法摆脱局部最优解,并且提高算法搜索精确度的能力。
交叉操作就是把两个父类个体的部分用重组和替换的方式组成新的个体。假设对第k代两个个体
,
(
)进行交叉,交叉后第
代产生的两个新个体为:
(25)
(26)
其中,
为一个既可以是常数也可以是变量的参数:当
为常数时,交叉为均匀算数交叉;当
为变量时,交叉为非均匀算数交叉。
变异方面本文使用
代替
,使用历史最优个体
代替
,使用历史最优种群
代替
,使用
的累差
代替
,其中
由式(27)求得
(27)
将上述公式带入式(23)和式(24),得到改进粒子群算法的速度和位置的更新公式:
(28)
(29)
根据以上对传统粒子群算法公式的改进使得改进后的粒子群具备了学习能力,同时也提高了粒子群的局部和全局搜索能力。
改进粒子群算法解决问题的基本步骤如下:
1) 选取一定数量的个体作为初始化粒子群;
2) 使用适应度函数计算得出粒子的适应度值;
3) 将步骤2)结果中适应度值最大的粒子记为全局最优解;
4) 不断搜索新粒子并计算器适应度值,若结果大于步骤3)中适应度值最大的粒子,那么这个粒子被记为新的全局最优解;
5) 对粒子进行交叉操作和变异操作,并记录两个操作后的粒子的全局最优解;
6) 所得结果与终止条件对比,若满足,则终止迭代,输出最优解,结束计算;若不满足,返回步骤4)继续计算,且迭代次数加1,直到满足条件,输出最优解,结束计算。
流程图如图1所示。
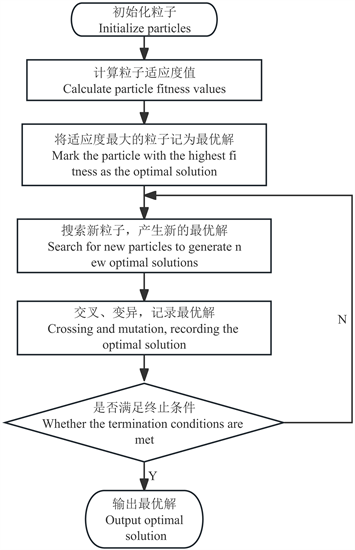
Figure 1. Improved particle swarm optimization algorithm flowchart
图1. 改进粒子群算法流程图
4. 实例分析
4.1. 模型参数设置
本文基于典型的轴工艺设计,通过优化轴的工艺参数为例进行仿真优化,轴零件图如图2所示。磨床型号选择M1432A磨床,其基本技术参数数据见表1,砂轮规格为WA60KV400 × 40 × 203。磨削液选择2%~5%的普通乳化液磨削液。
4.1.1. 工件圆周速度
外圆精磨时工件速度的选取与工件磨削表面直径和加工材料有关,具体信息见表2。
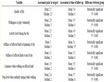
Table 2. Table for selecting the speed of cylindrical precision grinding workpieces
表2. 外圆精磨工件速度选择表
实际生产中,往往先选定工件速度,再计算工件转速,以此调整机床转速。被加工工件材料为45钢,加工表面直径45 mm,需要经过淬火热处理,属于淬火钢。工件速度取值范围接近25~40 m/min。使用常用的精磨工艺参数,选取工件速度为25 m/min和30 m/min。工件圆周速度计算公式如下:
(30)
式中,
为工件转速。
因此可知工件转速计算公式为:
(31)
通过上述工件精磨时磨削表面直径以及选取的工件速度,可以得到相应的工件转速,最终结合M1432A磨床的头架主轴参数,见表3。当工件速度为25 m/min时,工件计算转速为176.6 r/min,当工件速度为30 m/min时,工件计算转速为212 r/min。一般取接近的较小一级转速,因此当工件速度为25 m/min时,选择头架主轴转速为140 r/min,当工件速度为30 m/min时,选择头架主轴转速为200 r/min。
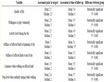
Table 3. Parameter table for the headrest spindle of M1432A grinder
表3. M1432A磨床的头架主轴参数表
4.1.2. 工作台纵向进给速度
一般而言,纵向进给量受到砂轮宽度的限制,当表面粗糙度处于0.2 μm和0.4 μm之间时,纵向进给量可按下列公式选择:
(32)
式中,B为砂轮宽度,
为工作台纵向进给量。
由于砂轮宽度为40 mm,因此纵向进给量的取值范围为8~16 mm/r之间,当工件速度为25 m/min时,纵向进给量取12 mm/r,当工件速度为30 m/min时,纵向进给量取14 mm/r。
工作台进击速度公式:
(33)
结合之前选取的工件转速最终确定当工件转速为140 r/min时,工作台进给速度为1.7 m/min,当工件转速为200 r/min时,工作台进给速度为2.8 m/min。
4.1.3. 磨削深度
磨削深度也称为横向进给量。上述确定的工件速度和工作台进给量,结合机械切削手册精磨时常用的磨削参数,最终确定磨削深度为0.005 mm。
综上所述,通过上述对磨削参数的分析和实际加工经验的参考,最终确定本文以外圆精磨加工过程的磨削用量参数见表4。
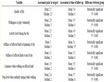
Table 4. Grinding parameters for precision grinding of outer circles of shaft parts
表4. 轴类零件外圆精磨加工过程磨削用量参数
4.2. 碳排放核算结果分析
根据第2章不同磨削用量参数下轴类零件外圆精磨过程中碳排放的主要来源,结合各部分计算公式总结得出不同磨削用量参数下轴类零件外圆磨削加工过程中总碳排放见表5。
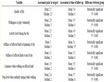
Table 5. Total carbon emissions during precision grinding of shaft outer circle under different grinding parameters
表5. 不同磨削用量参数下轴外圆精磨加工过程总碳排放
根据不同磨削用量参数下轴类零件外圆精磨加工过程总碳排放表5可知,不同磨削用量参数下的材料消耗碳排放和废屑消耗碳排放是固定不变的,这主要是由于尺寸参数的确定,去除材料的体积一定,相对应的材料消耗和废屑处理碳排放并不受磨削用量参数的影响,因此排除材料消耗和废屑处理对总碳排放的影响,在方案一和方案二的情况下,其余电能和物料消耗碳排放如图3所示。
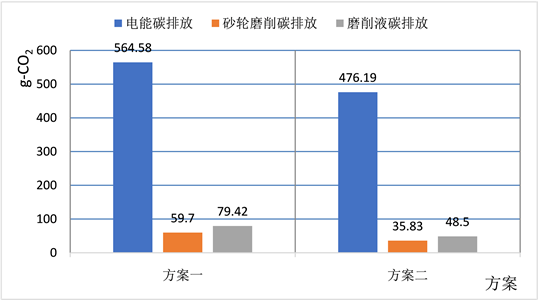
Figure 3. Carbon emission composition diagram of shaft outer circle precision grinding
图3. 轴外圆精磨碳排放构成图
由图3可知,电能排放量占主要占比,工作台纵向进给速度提高会导致加工时长大幅度下降,因此方案二的电能碳排放与方案一相比较少。从图3整体分析,方案二的碳排放量明显是低于方案一的碳排放量,选择不同的磨削用量参数,其精磨碳排放量也会有很大的差异,因此可以通过优化磨削用量参数降低主轴类零件外圆精磨过程总碳排放量,实现磨削加工的低碳制造。
4.3. 磨削参数优化
本文使用线性组合法将第2章中建立的磨削加工过程中的碳排放函数和成本函数结合得到新的同一目标函数,因此轴类零件外圆精磨加工优化模型适应度函数为
(34)
式中,
为轴类零件外圆精磨加工碳排放量函数,
为轴类零件外圆精磨加工成本函数,
为轴类零件外圆精磨加工碳排放量函数的加权因子,
为轴类零件外圆精磨加工成本函数的加权因子,F为适应度函数。
线性组合法中的加权因子
需要由实际情况而定,仅仅通过减少碳排放和加工成本两个角度出发考虑,其两者处于同等程度,故两者在整个统一目标函数中的重要程度相同,其加权因子值均为0.5,但是考虑实际加工情况,加工成本和碳排放量两者数值存在相当大的差异,需要加大加工成本因素在整个适应度函数的重要性,根据历史加工经验需要将加工成本因素的加权因子扩大100倍,基于上述各个分目标函数的加权因子的分析,最终的轴类零件外圆精磨加工优化模型适应度函数为:
(35)
根据前文M1432A磨床基本数据信息,待磨削轴类零件的尺寸参数等信息并参考磨削加工手册确定头架主轴转速范围为28~280 r/min,纵向进给量范围为8~16 mm/r,M1432A磨床额定功率为6.77 kW,工件刚度在精磨加工下最大挠度不得超过加工公差的1/5。针对轴类零件外圆精磨过程加工成本方面,基于该加工场景所在地区、外圆精磨加工过程涉及到的磨床、砂轮磨具、磨削液等实际情况确定电能单价为0.6444元/kWh,砂轮磨损成本为6.75元/mm3,磨削液单价为25.2元/L。基于上述磨削加工约束条件确定粒子群算法中的适应度函数以头架主轴转速和纵向进给量为优化变量,其余为约束条件,并结合上述砂轮磨损成本、磨削液成本等加工成本信息以及前文涉及的物料碳排放因子和电能碳排放因子等,通过线性组合法建立轴类零件精磨加工碳排放量和加工成本的适应度函数,依据粒子群算法使用Matlab建立粒子数目为20,迭代次数为150的轴类零件精磨过程碳排放和加工成本多目标优化模型进行求解优化参数,优化结果如图4所示。
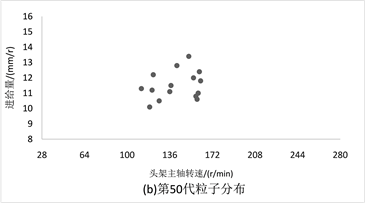
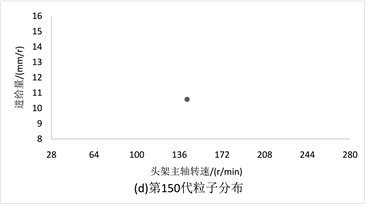
Figure 4. Particle swarm optimization process diagram
图4. 粒子群优化过程图
根据上述各图中所有粒子每次迭代的分布变化可知,所有粒子随着迭代次数的增加整体会趋向于一个最优解。当粒子达到迭代次数为150,头架主轴转速为142.5 r/min,进给量为10.58 mm/r时,轴类零件精磨加工多目标优化模型适应度函数取到最小值。综合考虑磨床头架主轴转速和进给量实际取值范围,最终确定轴类零件精磨加工最优磨削参数为:头架主轴转速140 r/min,进给量10.58 mm/r,磨削深度0.005 mm。在最优磨削参数下轴类零件精磨加工碳排放量约为685.39 g-CO2,与经验精磨加工产生的总碳排放量约792.41 g-CO2相比,碳排放量降低了17.3%。使用优化后的磨削用量加工产生的加工成本约为0.609元,与经验精磨加工成本约为0.879元相比,加工成本降低了30.7%。
5. 结论
本文在分析了影响轴类零件磨削加工工艺参数的基础上,结合加工成本函数和约束条件,建立了轴类零件磨削加工工艺参数模型。在经过传统磨削加工碳排放核算比较后,得出可以通过优化磨削用量参数降低主轴类零件外圆精磨过程总碳排放量的结论。通过线性组合法建立轴类零件精磨加工碳排放量和加工成本的适应度函数,再依据改进粒子群算法求得最优解参数。实现了加工过程中的低碳排放目标。
针对目前对轴类零件的磨削加工工艺过程中低碳制造研究较少的情况,本文为企业轴类零件磨削加工阶段实现低碳制造提供了一种可行方案。
基金项目
浙江省2023年度“尖兵”“领雁”研发攻关计划(2022C01SA111123);国家自然科学基金资助项目(51475434)。
参考文献