1. 引言
随着纤维增强复合材料的性能被进一步发掘,应用于轨道交通装备的复合材料实现了从非承载结构到主承载结构的发展历程 [1] [2] 。主承载结构中的转向架质量通常占整车质量的1/3,用复合材料制备转向架及其部件成为了当前的研究热点。如Hou [3] 介绍了一种由玻璃纤维增强复合材料制成转向架构架的全新设计,并通过有限元分析预测了其在不同载荷条件下的性能,分析结果表明,各向应力均较低。Kim [4] 等设计了铁路转向架构架用复合侧梁,并通过静载试验确定了结构的安全性。Liu [5] 提出了在动车组转向架摇枕上使用复合材料薄层的设计策略,结果表明薄层可以有效提高复合材料结构的静强度。Zhang [6] 等提出一种搭扣式复合材料板簧总成应用于下一代高速列车,通过静态、动态弯曲试验以及相关的有限元分析,证明该搭扣式复合材料板簧总成满足设计要求。
复合材料板簧具有较为宽泛的刚度调整、极佳的强度以及优异的减振能力,应用于转向架后能达到极佳的轻量化效果。当前复合材料板簧为适应不同的服役环境,衍生出了多种类型。Ma [7] 等人设计了一款变宽度复合材料板簧,通过试验和仿真得出其弯曲刚度满足汽车行业的设计要求,各向应力也满足材料的强度要求。Ke [8] 等采用Abaqus软件建立了某轻型客车主–副簧式复合材料板簧的有限元模型,并对该复合材料板簧的刚度及模态进行了仿真分析。Shi [9] 等建立了变刚度双叶板簧的简化模型,并利用位移叠加法和材料变形的连续性推导了该模型的复合刚度计算方法,且所提出的方法可以应用于三叶板簧和多叶板簧。Kueh [10] 等利用ANSYS软件研究了金属和复合材料多叶板簧的静态和疲劳性能,发现所设计的复合材料板簧较金属板簧具有更低的弯曲应力和挠度,以及更高的疲劳寿命。为满足板簧不同应用场景下所需的特殊性能,许多学者通过改变板簧的结构形式,探索具有特殊结构的复合材料板簧的潜在优势。如Polilov [11] 认为选择合适的弹簧几何形状,可以创建具有恒定横截面积和3倍减重的树枝状的复合材料板簧,该板簧未切割纤维,并且可以通过将叶片组合成束来减小弹簧尺寸。Abu [12] 等通过有限元仿真优化了复合材料椭圆板簧的材料和几何形状,从实验和数值模拟两方面研究了椭圆率对粗纱缠绕复合材料椭圆板簧性能的影响。
为了实现动车组转向架轻量化,本文设计了适用于高速重载的转向架复合材料板簧,由两个单片簧身对扣组合而成。端部设计为高可靠性、强连接性的金属铰接式接头,建立了对扣式板簧的刚度理论模型,根据铰接结构可靠性理论,校核了铰接结构。利用有限元软件仿真分析了板簧刚度和总成结构的强度,通过Fe-safe计算了铰接结构的疲劳强度。制备样件并进行板簧台架疲劳试验。试验结果表明,铰接结构及其他连接部件未出现明显损坏,测得板簧的疲劳寿命为45.2万次,高于设计要求中30万次的疲劳寿命。理论、仿真及试验结果相吻合,验证了对扣式复合材料板簧匹配设计的正确性以及铰接结构的高可靠性。
2. 结构设计
对扣式复合材料板簧,安装空间较小、能承受较大的垂向位移。该特性适合转向架服役中频繁承受高额垂向载荷所产生的大变形工况。复合材料板簧簧身结构为等宽抛物线的等强度结构。该结构能够使板簧上下表面应力均匀分布,在满足轻量化的同时具有较高的材料利用率 [13] [14] 。为了提高板簧中部的强度,簧身设计中只保留内凸台,起到限位作用的同时增加板簧的安装面积。此外上下簧片通过铰接连接实现簧身两端的转动,并传递载荷。设计的复合材料板簧具体结构如图1所示。根据中车长春轨道客车股份有限公司提供的数据,板簧的主要设计参数如表1所示。
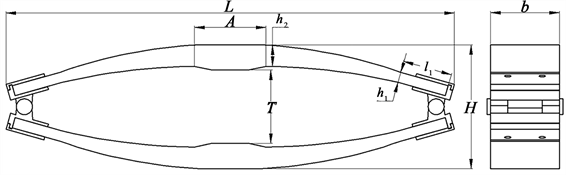
Figure 1. The diagrammatic drawing of the buckle-type composite leaf spring
图1. 对扣式板簧示意图
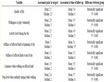
Table 1. Main design parameters of leaf spring
表1. 板簧主要设计参数
高铁运行速度快,传递到连接结构的震动密集,这对板簧接头部分连接的可靠性提出了更高的要求。采用螺栓连接和胶接连接的混合连接形式,在提高板簧连接部位的稳定性的同时减小了连接结构的整体尺寸。对扣式板簧装配图如图2所示,铰接结构由上耳板、销轴、下耳板三部分组成。中部连接结构,即夹具内表面,设计为完全包裹凸台并向外延伸一定长度的平面以保护过渡面。
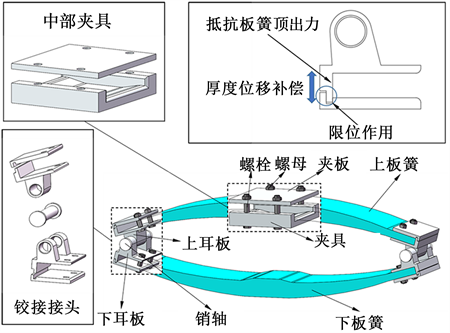
Figure 2. Three-dimensional model of the buckle-type leaf spring assembly
图2. 对扣式板簧装配体的三维模型
图2中所示,铰接接头分为上下两部分,通过铆接形式连接,防止上下部分发生相对位移,并起到限位的作用。接头厚度方向上留有一定间隙,以补偿簧身制造中产生的误差及厚度方向受力产生的变形,同时起到位移补偿作用。金属接头下夹板部分为L型结构,当板簧承受载荷时,能抵抗板簧变形时的纵向顶出力,降低板簧螺栓孔壁的应力,延长板簧的使用寿命。铰接孔两边缘倒圆角处理,以降低孔壁两侧的应力,减少光轴的磨损。
3. 理论计算
3.1. 刚度理论
对扣式板簧刚度计算问题不同于单个板簧,若板簧刚度不变,则在施加相同载荷时,对扣式板簧的位移是单独两个板簧在相同载荷条件下位移的叠加。将单个复合材料板簧等效为简支梁结构模型,则其受力情况如图3所示。
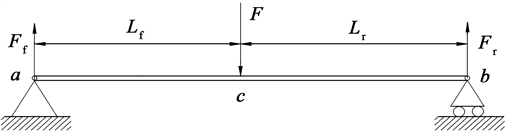
Figure 3. Force model of composite leaf spring
图3. 复合材料板簧的受力模型
设单个板簧在载荷F作用下位移为s,则对扣式复合材料板簧的刚度Ks为:
(1)
根据EN13298铁路应用–悬挂系统相关标准,设对扣式板簧刚度为1000 N/mm,单个板簧刚度为2000 N/mm。根据钱琛等人 [15] 的研究,设计的对扣式复合材料板簧尺寸参数如表2所示。此外上板簧凸台需承受垂向载荷与纵向载荷,在板簧内表面设置6 mm厚度凸台。同时为防止因纵向载荷导致的中部夹具与凸台滑移脱落的情况,凸台纵向长度A应适当增加。
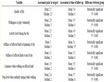
Table 2. Size parameters of the buckle-type leaf spring
表2. 对扣式板簧尺寸参数
注:h1为板簧端部的厚度,h2为板簧中部的厚度,l1为板簧端部水平段的长度。
3.2. 铰接可靠性
铰接连接一般用于承受较大载荷且往复运动的部位,通过耳板与销轴之间的接触传递载荷 [16] 。图4为销轴和耳板的示意图。针对铰接连接可能出现的破坏模式,对销轴及耳板进行计算校核 [17] [18] 。除耳板材料采用Q345钢,其余金属材料采用40Cr钢,材料参数如表3所示,表4为销轴和耳板尺寸参数。
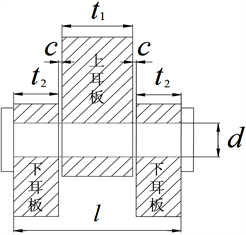
Figure 4. Diagram of the axis pin and ear plates
图4. 销轴和耳板示意图
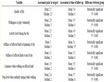
Table 3. Related performance parameters of metal materials
表3. 金属材料相关性能参数
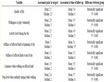
Table 4. Size parameters of pin shaft and ear plate
表4. 销轴和耳板的尺寸参数
其中耳板最小厚度不得小于销孔处净宽的1/16,即下耳板厚度应满足 [19] :
(2)
销轴孔中心需位于耳板的中心线上,且销轴孔径相差应不大于1.0 mm,即:
(3)
销轴接触面沿着耳板厚度方向存在不均匀的承压应力,导致销轴和耳板局部发生变形并使荷载向耳板边缘集中。图5为销轴弯矩计算简图 [20] 。
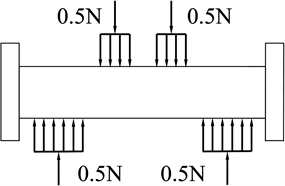
Figure 5. Axis pin bending moment calculation diagram
图5. 销轴弯矩计算简图
根据图3可得:
(4)
(5)
式中:N为杆件轴向拉力,N;Lf为板簧中心点至左端长度,mm;Lr为板簧中心点至右端长度,mm。
考虑应力分布不均的影响,销轴计算截面弯矩M可表示为 [21] :
(6)
式中:r为考虑耳板厚度方向承压应力不均匀分布的峰值系数,取值在0~1.0之间。
为了避免销轴出现弯曲破坏,对销轴抗弯强度进行验算。销轴的弯曲强度应满 [22] :
(7)
式中:σb为销轴截面弯曲应力,MPa;fb为销轴抗弯强度设计值,MPa。
为了避免销轴出现剪切破坏,对销轴抗剪强度进行校核:
(8)
式中:τb为销轴截面剪切应力,MPa;d为销轴直径,mm;nv为受剪数目,本文中nv取2;
为销轴抗剪强度设计值,MPa。
当销轴处于弯剪组合工况时,其强度可表示为:
(9)
为避免销轴、耳板出现承压破坏,对销轴、耳板的承压强度进行验算。销轴、耳板的承压强度为:
(10)
式中:σc为销轴对耳板的挤压应力,MPa;t为耳板厚度,mm;
为耳板销孔孔壁承压强度设计值,MPa。
为了避免耳板在销孔处的发生净截面拉裂破坏,耳板净截面抗拉强度与端部抗拉强度分别为 [23] :
(11)
(12)
式中:f为耳板抗拉强度设计值,MPa。
为避免耳板端部出现剪切破坏,对耳板端部的抗剪强度进行验算:
(13)
式中:τ为耳板端部截面剪切应力,MPa;fv为耳板抗剪强度设计值,MPa。
4. 可靠性有限元仿真
4.1. 仿真设置
根据表2中的设计尺寸参数,在Abaqus有限元分析软件中建立复合材料板簧分析模型,网格单元类型为C3D8R。板簧的材料为G1600/7901DNK/32%的玻璃纤维/环氧树脂,其相对碳纤维材料韧性更好、成本更低,具体的力学性能参数见表5。
簧身按照表5的材料参数进行设置。板簧的铺层设置如图6所示,绿色箭头1方向代表纤维主方向、白色箭头S方向为铺层方向,铺层角皆为0˚。
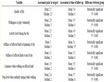
Table 5. Related parameters of unidirectional glass fiber
表5. 单向玻璃纤维相关参数
注:Ei (i = 1, 2, 3)为弹性模量,μij (i, j = 1, 2, 3; i ≠ j)为泊松比,Gij为剪切模量,Sij为剪切强度,Xt、Yt为材料的拉伸强度,Xc、Yc为材料的压缩强度。
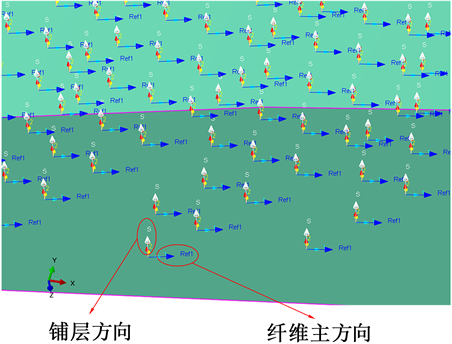
Figure 6. Given material’s properties
图6. 复合材料板簧的铺层设置
由于连接结构包含夹紧力及诸多接触对,模型的边界条件非常复杂,在静力分析模块下难以收敛,故采用动力–隐式方法对结构进行刚度和强度分析。设置2个分析步,在Step-1中,对中部螺栓施加40 kN的轴向载荷,等效拧紧力矩为110 N·m。端部螺栓施加20 kN的轴向载荷,等效拧紧力矩为50 N·m。在Step-2中对参考点RP-1施加1.5倍定员载荷,即92.1 kN的垂向载荷。RP-1为板簧中部夹具上表面集合的参考点。根据板簧的服役工况,下板簧中部设有完全固定约束。板簧模型在Abaqus中的载荷和边界条件设置如图7所示。
4.2. 结果分析
在图8中,图8(a)~(c)为施加了端部、中部螺栓预紧力与1.5倍定员载荷下复合材料板簧的应力分布图;图8(d)~(f)为仅有端部螺栓预紧力与1.5倍定员载荷下复合材料板簧的应力分布图,其中图8(a)与图8(d)为主应力云图,图8(b)与图8(e)为纵向应力云图,图8(c)和图8(f)为横向应力云图。
图8(a)~(c)中,上板簧在中部夹具夹持下,最大主应力为798.0 MPa,避开了过渡面,纵向最大拉应力为790.3 MPa,最大压应力为611.6 MPa;横向最大拉应力为42.0 MPa,最大压应力为157.0 MPa。图8(d)~(f)中,对于无中部夹具夹持的下板簧,其最大主应力为651.0 MPa,纵向最大拉应力为649.6 MPa,最大压应力为627.6 MPa;有限元仿真结果与材料许用应力对照见表6。结果表明对扣式板簧在定员载荷及1.5倍定员载荷条件下皆满足材料的强度要求。
如图8所示,板簧的抛物线结构使其上下表面在纵向方向的应力均匀分布,能有效地发挥材料的性能。随着垂向载荷的施加,板簧与中部夹具接触区域应力无明显提升,说明中部夹具对板簧的可靠性影响较低。横向最大应力均出现在孔壁边缘处,此处是板簧劈裂损伤的危险区域。
1.5倍定员载荷下金属部件应力分布如图9所示,中部夹具应力最大为777.2 MPa,耳板及销轴应力均较小,均未超过330 MPa,因此金属接头结构处于安全范围。此外中部螺栓M12及端部螺栓M10为10.9级,同样处于安全范围。
(a) 中部夹具应力云图
(b) 铰接结构应力云图
Figure 9. The stress cloud of metal parts
图9. 金属部件应力云图
如图9(a)所示,在螺栓预紧力作用下,中部夹具的变形造成螺纹孔轴线与螺栓轴线不重合,容易造成螺栓弯折,导致最大应力主要集中在螺栓侧面,可以通过加厚中部夹具或者采用更高等级的螺栓提高安全裕度。
铰接结构的应力分布如图9(b)所示,最大应力同样出现在螺栓上。销轴的应力主要集中在耳板边缘,这是因为销轴的弯曲变形和耳板的局部承压变形会使荷载向耳板的边缘集中。该结果与3.2节的销轴受力情况相吻合,从而在仿真方面验证了铰接可靠性理论的正确性。
后处理中RP-1点输出的力–位移曲线如图10所示。曲线的斜率即为板簧的刚度,即1044 N/mm,与设计刚度1000 ± 15% N/mm相匹配,满足设计的刚度要求。
4.3. 疲劳仿真
高铁是一种长时间工作的运载工具,在较短的时间或者较少的循环次数内发生破坏是不允许出现的状况。不同于公路运输交通工具,高铁运行平稳,故金属接头的工作环境具有长期性、稳定性,因此采用高周疲劳的算法,即采用S-N曲线对接头的寿命进行计算。如图11所示,一般认为循环次数低于10E+4属于低周疲劳,低周疲劳时纵坐标为应变,高周疲劳时纵坐标为应力。高周疲劳主要用全寿命法进行分析,而低周疲劳主要用初始裂纹法来进行分析。初始裂纹分析方法通常是基于应变寿命曲线(E-N曲线)理论来进行寿命分析。S-N和E-N曲线在高周区域重合,因为名义应力是线性的 [24] 。
调用Fe-safe材料库中自带的40Cr材料,采用S-N寿命曲线法。将Abaqus计算得到的61.4 kN (定员载荷)下金属接头应力数据导入到Fe-safe中,用Goodman算法对应力平均化,最终计算得出在61.4 kN循环载荷下金属接头结构均处于无限寿命区。一方面,经调质处理的40Cr,一定程度上避免了金属接头受载过程中的应力局部集中;另一方面,仿真中寿命薄弱部位出现在孔壁两侧,这与接头或光轴的变形造成的局部应力集中有关。支撑铰接孔的底座为具有高刚度的L型结构,一定程度上抑制了接头因载荷过大而变形的问题,故接头的寿命得到很大的提高。
对于螺栓等疲劳寿命计算,用局部应力应变法估算结构疲劳寿命。首先估算疲劳危险点弹塑性应力应变历程,然后对照材料的疲劳性能数据,按照疲劳累积损伤理论进行疲劳损伤的累积,最后得到构件的疲劳寿命 [25] 。采用累积损伤理论Palmgren-miner准则,对应于Fe-safe中Brown-miller算法。Brown-miller主要针对应变进行疲劳计算,对于求解低周与高周疲劳同样适用,且算出的寿命相对保守,比实际寿命更小,符合安全冗余的需要。
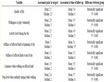
Table 7. Some parameters of bolt life calculation
表7. 螺栓寿命计算的部分参数
采用同样的方法,将Abaqus的计算结果导入Fe-safe中,采用表7材料参数。计算得到端部螺栓的疲劳寿命最小,且最小寿命出现在螺栓与接头螺纹孔相切的部位,循环次数为2.167E+8次,如图12所示。这是因为端部螺栓在板簧承受载荷时,反复承受螺栓孔的剪切作用,应力幅变化较大,故寿命相对较低。
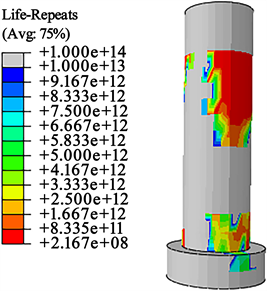
Figure 12. Fatigue life calculation results of the end bolts
图12. 端部螺栓的疲劳计算结果
5. 样件制备及性能测试
5.1. 样件制备工艺及试验细节
下面按照实际操作过程对样件制备工艺进行阐述。
(1) 样件制备前的准备工作:裁剪玻璃纤维预浸料,清洁、预热模具,设置模具温度为120˚;往模具注入树脂、固化剂和催化剂;制备金属件。
(2) 铺层:按照设计好的包夹铺层方案,按顺序依次在模腔内铺设裁切后的玻璃纤维预浸料。
(3) 合模固化:模腔烘干、加热加压等工序后进行固化。
(4) 脱模:固化完成后,开模并进行脱模操作。
(5) 金属件处理:进行粗坯清理、切割、安装金属件、接头钻孔等工序。
(6) 后固化:完成零部件的装配后,对簧身进行后固化处理,后固化温度为120℃,时间为2 h。
板簧台架试验通过1600T压机实现。分别对制备的5组复合材料板簧Ⅰ~Ⅴ在承载力44.1~81.9 kN,频率为1 Hz的试验条件下进行疲劳试验。其中样件Ⅰ和Ⅱ中部铺层数为40,外表层设有的2个加强片(S玻纤)。簧身端部开孔处理,以通过连接簧身和铰接接头的螺栓。样件Ⅲ时在样件Ⅰ的基础上铺层数增加一层,同时加强片增为4个。样件Ⅳ和Ⅴ与样件Ⅲ铺层数相同,但取消了簧身开孔。此外样件Ⅳ的后固化温度为150℃,样件Ⅴ后固化时间为2.5 h。
5.2. 结果分析
试验失效现象如图13所示。试验时样件Ⅰ由于夹具切割导致层间开裂,最终导致失效,损伤形式如图13(a)所示。样件Ⅱ由于铰链螺栓不匹配,摩擦力太大导致端头断裂,损伤形式图片见图13(b)。如图13(c)所示,在经过45.2万次循环后,试样Ⅲ由于端部打孔导致应力集中,端头沿着0˚方向开裂发生分层失效。这是因为板簧开孔会切断增强纤维并引起应力集中,即连接结构是极易发生破坏的部位,故应尽量避免簧身开孔。这与前文仿真中孔壁边缘处出现的横向应力集中,产生的危险区域相对应。对于试样Ⅳ,因螺栓在板簧端部接头外侧进行连接,一定程度上避免了开孔区域应力集中。但因更高的后固化温度会降低板簧韧性,板簧沿簧身分层开裂并最终失效,如图13(d)所示。对于试样Ⅴ,后固化时间的同加会降低板簧韧性,损伤模式表现为下板簧的层间开裂,如图13(e)所示。此外,图13(e)中端部螺栓与接头螺纹孔相切的部位有轻微弯曲。这是因为端部螺栓在板簧承受载荷时,反复承受螺栓孔的剪切作用,对螺栓有一个弯折的效果,这与仿真结果一致。铰接结构在试验中未出现疲劳失效现象。
考虑到各试样在疲劳试验中的出现损伤模式及性能表现。将试样Ⅰ和试样Ⅱ的试验刚度与仿真模拟刚度进行对比分析,如图14所示。
由图14可知,有限元仿真的板簧刚度为1044 N/mm,相较于样件Ⅰ和样件Ⅱ,仿真与试验测的刚度最大误差为12.8%。考虑到材料参数误差、建模误差及后期的制造误差,有限元仿真能够有效进行刚度匹配。
6. 结论
本文重点研究了对扣式复合材料板簧的匹配设计及其动刚度、疲劳等动态性能,以及铰接结构的可靠性。建立了对扣式复合材料板簧的刚度理论模型。针对铰接连接可能出现的破坏模式,校核了铰接接头的可靠性;通过有限元仿真对板簧总成进行刚度及强度预测;设计了板簧台架试验,用于验证相应的理论及仿真的正确性,并分析对扣式复合材料板簧重载工况下的损伤模式。结合理论、仿真、试验结果,结论如下:
(1) 建立的板簧刚度模型与试验误差满足工程应用要求,能够预测不同材料参数和结构尺寸对板簧影响下的刚度。设计的对扣式复合材料板簧的刚度和强度均满足设计要求。为研究重载对扣式复合材料板簧提供了理论支撑。
(2) 板簧总成疲劳寿命最高可达45.2万次。同时设计L型铰接结构一定程度上抑制了接头因载荷过大而变形的问题,其在台架试验中始终未出现疲劳失效现象。此外建立的可靠性理论模型可用于预测铰接结构的可靠性。
(3) 板簧的失效模式主要为沿0˚方向的分层和开裂。簧身开孔会切断增强纤维并导致孔壁边缘应力集中,加剧板簧的损伤行为。同时端部螺栓与接头螺纹孔相切的部位存在应力集中现象,易发生弯曲变形。
综上所述,设计的对扣式复合材料板簧总成在轻量化的同时在刚度、强度均满足工程应用标准,且在重载工况下的疲劳寿命远高于设计标准的30万次。其在高速动车组转向架中具有一定的应用潜力。
NOTES
*通讯作者。