1. 引言
据统计,中国油田采出水总量在几亿立方米以上,常规油田采出水温度为38℃~43℃,稠油油田采出水温度为60℃~65℃,蕴藏着大量的热能资源 [1] 。油田生产过程消耗大量煤炭、石油、天然气化石能源,是高产能、高耗能的大型企业,随着节能减排工作的持续推进,人们开始注意到油田采油污水中储存着巨大的余热能源。赵达等人研究了地源热泵技术在油田中的应用,采用地源热泵替代原油加热锅炉,通过试验系统运行,节约的能源费用可在4.82年收回地源热泵系统投资,具有较好的经济效益和环保效益 [2] 。耿建安等人利用蒸汽作为驱动热源,采用吸收式热泵系统提取采油污水中的余热,制取80℃的热水为居民供暖,系统性能系数可达到1.77,年可降低消耗一次能源54% [3] 。
本文主要引入了蓄能式热泵系统,通过与热泵系统、吸收式热泵系统及锅炉系统的对比分析,认为蓄能式热泵系统比其他三个系统运行成本更低,节能效果更加明显。
2. 余热利用技术介绍
2.1. 常规热泵加热系统介绍
目前,油田的加热系统主要是采用燃油、燃气、燃煤锅炉,用于加热原油、脱水、伴热及居民供暖,许多研究人员也尝试使用常规热泵系统或吸收式热泵系统替代锅炉系统,流程图如图1所示。污水经过板式换热器为热泵机组提供热源,在热泵机组中通过循环工质的相变换热,将污水中的热量提取出来,制造高温热水,加热需要被加热的介质。
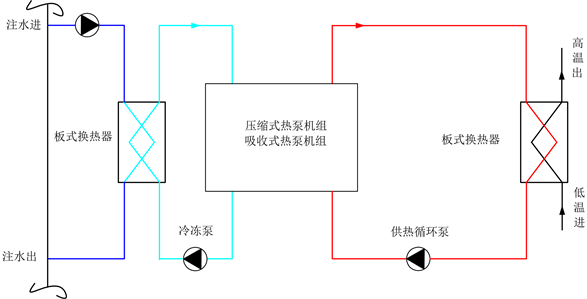
Figure 1. Flow chart of conventional heat pump heating system
图1. 常规热泵加热系统流程图
压缩式热泵主要由蒸发器、冷凝器、压缩机、膨胀阀组成,通过制冷剂的压缩、冷凝、节流、膨胀四个过程,将污水中的热量源源不断的向高温侧转移。压缩式热泵靠电能驱动,制冷工质一般为有机工质,其经济性指标为性能系数COP [4] 。
(1)
Qh——热泵机组供出的热量,kW;W——输入的能量,kW。
吸收式热泵机组主要由蒸发器、冷凝器、发生器、吸收器、溶液循环泵等组成,该机组的制冷剂为二元溶液,常用的是溴化锂和氨水溶液,沸点低的为制冷剂,沸点高的为吸收剂。它的驱动热源主要有高温热水、蒸汽、化石能源等,其经济性指标为热力系数ξ [5] 。
(2)
ϕk——机组提供的热量,kW;ϕg——机组消耗的热量,kW。
2.2. 蓄能式热泵系统介绍
蓄能式热泵系统主要是基于峰谷电价政策,利用压缩式热泵提取采油污水中的热能,在电价谷电时段热泵全开,边供热边蓄能,在电价峰值阶段,热泵主机关闭,利用所储蓄的能量向用热单位持续供热。系统流程如图2所示。
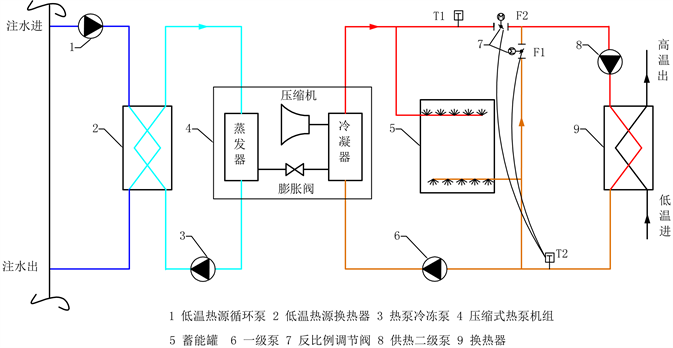
Figure 2. Flow chart of heat storage heat pump heating system
图2. 蓄能式热泵加热系统流程图
注水经低温热源循环泵1加压,经钛板板式换热器换热后重新回到注水管线,做到只取热不取水,另一侧得到热量的软化水经热泵冷冻泵3进入热泵机组4,热泵机组通过制冷剂的蒸发、压缩、冷凝、节流等环节,将热量传递到冷凝器侧的软化水,制取高温热水。夜间谷电时段内,热泵机组开启,一级泵6、供热二级泵8同时开启,一方面通过换热器9向被加热介质供热,另一方面向蓄能罐5内充水蓄能。白天峰电和尖峰电价时段,低温热源循环泵、热泵机组、热泵冷冻泵、一级泵停止运行,供热二级泵继续运行,利用蓄能罐的水继续提供热量。
3. 案例分析
3.1. 基本情况介绍
以河南省某油田联合站为分析对象,对比不同方案的投资、运行费用、经济效益和减排效益。联合站原加热系统采用天然气加热锅炉,每年消耗天然气约275万立方米,天然气价格2.9元/立方米。污水温度为40℃,污水流量约13,000立方米/天。具体参数如表1:
表2为河南省峰谷电价时刻表,每天8个小时的谷电时段,电价为0.33917元/kWh,尖峰电价为1.07585元/kWh,尖峰电价为谷电电价的3倍多,因此可以利用这个特点,利用蓄能技术在谷电时刻蓄能,用于峰电和尖峰时刻的负荷加热,可大大的降低运行成本。
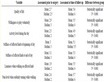
Table 2. Peak and valley electricity price in Henan province
表2. 河南省峰谷电价表
3.2. 经济效益分析
经过计算3种方案的投资、运行支出,与现有系统的运行费用作为收入计算出个系统的年收益,从而计算出各方案的静态投资回收期,系统计算期为15年。
从表3可以看出,蓄能式热泵投资最高,吸收式热泵系统投资最低,一方面增加了蓄能罐的设备投资,另一方面生产负荷为连续的,蓄能过程中的负荷为基本加热负荷与蓄能负荷之和,增大了热泵设备的选型。热泵系统和蓄能式热泵系统主要是依靠电能驱动,年运行电费分别为473.9万元和289.8万元,分别比锅炉系统运行费用降低40.6%和63.7%。蓄能式热泵系统的热泵设备基本都是在谷电运行,在蓄热负荷不足的情况下在平电时段开启,完全避开了峰电和尖峰电价时段,可以大幅的减低运行成本,缩短项目的投资回收期。吸收式热泵系统的运行费用最高,运行性能系数在1.5左右,年需天然气184万立方米,节约天然气91万立方米,比锅炉系统节约运行费用146.7万元。投资回收期蓄能式热泵系统为4.7年,吸收式热泵系统为7.6年。可看出,蓄能式热泵系统虽然增加了投资,但运行费用最低,经济效益最为明显。
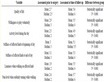
Table 3. Three kinds of scheme investment and investment payback period
表3. 3种方案投资及投资回收期
3.3. 节能效益分析
将3个系统所消耗能量折合成标煤,再进行减排二氧化碳进行计算,其中电煤转化量按0.36 kg/kWh,天然气热值为8500大卡/立方米。从表4中可以看出,替代系统都可以取得较好的减排效果,蓄能式热泵系统的减排效果最为显著,相比原来的系统年可减排二氧化碳2219吨/年,吸收式热泵系统次之,热泵系统最差。
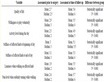
Table 4. Carbon dioxide reduction
表4. 3种方案二氧化碳减排情况
4. 结论
热泵系统、蓄能式热泵系统、吸收式热泵系统与天然气锅炉系统相比,都可以取得较好的经济效益和减排效益,蓄能式热泵系统的经济效益和节能效益最高。热泵系统的性能系数可达到3以上,吸收式热泵系统的热力系数在1.5左右,都能很好地利用油田采油污水余热,替代现有的燃油、燃煤、燃气锅炉,可成为油田企业降本增效的重要措施。