1. 引言
河曲电厂一期采用BBD3854双进双出正压直吹式钢球磨煤机,#1、#2机组磨煤机差压料位计共10套,差压料位自投入使用9年来,取样管路经常出现堵塞,尤其是磨煤机末端部分。在疏通时,需将磨煤机中煤粉吹空,而运行一段时间后,又出现堵塞。磨煤机料位计使用年数长,取样管路已经严重磨损,无法提供准确的测量数据,无法自动投入,严重影响磨煤机的出力及自动运行,进而影响到机组协调系统、AGC的投入质量[1] 。本方案通过对差压料位检测装置系统进行升级换代,在原控制柜基础上进行软件和硬件改造,将原系统升级为YCCH旋转容器智能化压差测厚系统,并利用新系统对装置进行测试与调整[2] 。
2. 差压料位测量原理及精确测量的前提条件
在正常运行中,磨煤机内的一次风流量和吹出的煤粉量之间存在着一定的比例关系,为保证负荷控制回路得到平衡,必须维持风煤比例的恒定。磨煤机内的含煤量很大程度上决定了这种风煤比。所以必须保持磨煤机内的煤粉层恒定。料位侧量系统将煤粉的厚度转换为差压值和对应的4~20 mA的信号。通过DCS参与到给煤机的给煤控制,实现磨煤机的煤粉层厚度的恒定[3] -[6] 。
料位测量的基本原理是利用低速喷射气流在容器中测量压力,流量调节装置使测量管子中的空气流保持低速稳流,管子中的气源在罐内喷射时所受的阻力与罐内的介质物位有关,介质物位低时,阻力小;介质物位高时,阻力大。阻力的大小反应了物位的变化。
YCCH新型旋转容器智能化压差测厚系统通过伸到旋转的、有压力变化的容器内部上、下两个探针进行测量,料位测量系统由两个功能相同、互为独立的驱动侧和非驱动侧单元组成,因为两侧相同简单论述为一侧。其中一侧的下端测量管路在进入磨煤机罐内前分成两路,悬臂支承深入到旋转的磨煤机筒内的中空管,保护着由密封风箱进入到磨煤机筒体内的检测气流管路,在下端连接着一组由两个下探针及保护套组成的下检测端口,下探针共两个高、低探针,两个探针高度之间的差距约有46 mm,分别用于测量高料位和低料位,下探针尾端埋在被测量物流下边,向下伸入煤中为正压侧;首段端连接着一个上探针,上探头设置在被测量物料的上方,煤粉上方空气中为负压侧。料位测量系统存在两个压力差,小压力差是测量气源与磨煤机大罐内的压差,另一个压力差是罐内上、下压差。系统测量时利用通过管路的两个探头输入恒定、微量的气流,再用压差变送器测量两个探头之间的压力差值。将压力差值通过换算,可测得容器内部物料的厚度。测量系统原理如图1所示。
磨煤机中煤粉层不是处于大气压下,而是在压力变化的、动态的、密闭的容器内。压力的影响因素包括进入煤仓内的煤粉量、一次风量等。料位适合采用压差测量法来测量煤粉厚度。磨煤机罐内上、下
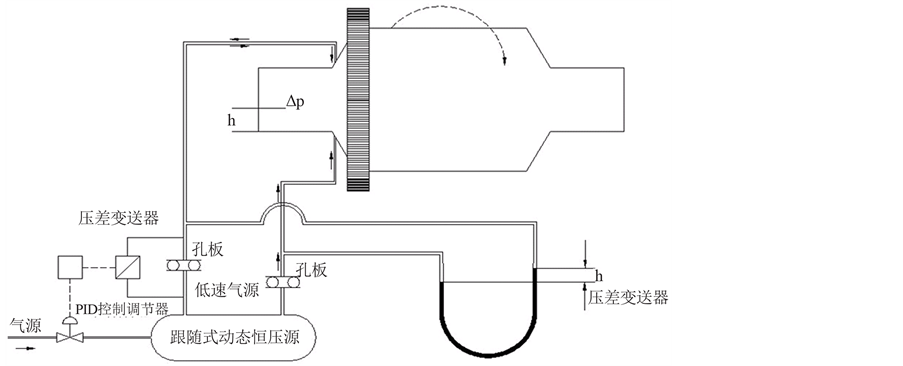
Figure 1. YCCH rotating vessel of intelligent differential thickness measurement system diagram
图1. YCCH新型旋转容器智能化压差测厚系统示意图
的两个探头,连续输入恒定低速喷射气流,两根导管之间的压差读数与上下探头间煤粉厚度存在比例关系,进行换算就可测出磨煤机中煤粉层厚度。
压差测量的基准值是低速、恒流气源,如果气源发生变化,其后测量的数据皆无意义。为保持气源恒定,料位测量系统上、下测量管路上各设有一个孔板,上管路的孔板测量的压力差作为气动调节机构的被调量,当罐内压力变化时,孔板测量得到的压差数值随之变化。为保持压缩空气罐与磨煤机罐内的压力恒定,调节仪表实际值与设定值进行比较,经PID控制器输出后,传递至气动执行机构动作,使缓冲罐内压力对磨煤机罐内形成正压。缓冲罐中的气源经过孔板限流,形成不受磨煤机内压力不断变化影响的恒定气源。
3. 磨煤机料位测量系统的改造及调试
2013年9月份开始利用1、2号机组D级检修机会分别对#1、#2号机组磨煤机差压料位测量系统进行升级改造,对控制柜及控制柜内所有管路及阀门控制设备全部更换并重新铺设电缆及接线,对测量外管路、磨煤机内软管及取样管路、探针口保护套进行检查并对存在的问题进行更换。从控制柜到探针全部系统气源管路小通径部分及小通径手动针形阀门统一更换为Ф22的球阀,气源管路的软管部分、检测探针全部更换。并用变送器、触摸屏、PLC与专用软件进行泄漏检测。在检查安装设备无误的情况下,送电并进行了静态调试。
首先是测量管路泄漏检测。压差柜与磨煤机连接共四根管路,为防止现场安装施工后管道耐压过程中出现遗漏和跳跃现象,压差柜设有现场管路连接后进行管路泄漏检测的步进式画面、操控阀门提示画面、泄漏检测特性曲线显示画面。测试管路泄漏前需用堵头将探针口密封,再按照画面操作步序提示对相关阀门进行正确控制,然后将选择开关指向“管路充气”,当管路充气压力稳定后,选择“测试开始”,系统首先将压缩空气值存到初始值中,计时同步开始,出厂预设检测时间10分钟,压降小于0.02 MPa,当测试时间满足要求时,管内压降小于0.02 MPa,测试结果合格。依次进行其它管路泄漏检测程序。小流量、稳气压的气源是磨煤机料位测量的基础,所以磨煤机罐内探针至压差料位控制柜之间连接管流向通畅、不堵、不漏是正常运行的关键,安装调试及正常维护时都要十分重视。
然后检测各管路特性,每台压差控制柜与磨煤机连接共有四根管路、四个探针,每条管路到探针口有自身的特性,系统对管路特性级别分等级。系统安装完成后,对管路进行测试得到基础数据,根据级别在系统运行前对每一条管路进行特性识别、注册。
4. 磨煤机料位测量系统改造后存在的问题、分析及优化方案
1) 磨煤机运行料位低。改造前由于料位不准确,运行人员把磨煤机料位控制始终在低料位运行,低时200~300 Pa,高时500~600 Pa,改造后的磨煤机料位投运后,灵敏度、精确度有了很大的提高。为了实现进一步的节能减排,需要将差压料位提高到1100 Pa以上,料位提高后煤粉细度、浓度将会提高,AGC响应进一步提高,降低容量风、衬板、钢球的消耗,机组发电煤耗量也相应减少。通过对几台正常的磨煤机可以进行提高料位试验和对煤粉的取样工作,寻找最佳料位值。若要单炉达到最佳运行值,五台磨煤机料位均需正常运行,但1号机组的B、D磨煤机存在问题:容量风门开关大于60%后,磨煤机料位出现频繁大幅度波动,最大波动幅度由300 Pa涨至1100 Pa。D磨煤机料位波动曲线如图2所示。
第一条趋势线(由上至下排列、蓝色)代表D磨煤机驱动端分离器出口压力;第二条趋势线(由上至下排列)代表D磨煤机非驱动端分离器出口压力。两压力值均正常时(趋势曲线后段),差压料位平稳,工作正常;两压力值相反,大幅度震荡时(趋势曲线前段),差压料位随之震荡。若单台磨两侧料位曲线同时波动,则排除单侧测量管路的问题,调节压差柜内压差变送器气动执行机构,保持压缩气罐的气源出口压力一直高于磨煤机罐内压力。针对料位波动,检查恒压气源,取出气源管路上的调压阀上端阀的弹簧、堵头,若上端阀内无油,则气源管路正常,调节器输出指令在170~190 Pa之间,恒压气源无异常。经过半个多月的连续观察、分析研究,发现磨两侧容量风出口压力曲线震荡峰值相反,两侧的一次风由中空管进入到大罐时,对冲点被转移到一侧,对冲点偏离中心,容量风高侧将容量风低侧压到最低,筒体压力震荡变化引起料位剧烈波动。两侧容量风开度大时,均会产生这种震荡现场。我厂磨煤机罐内无压力测点,采用磨煤机出口压力值代替。
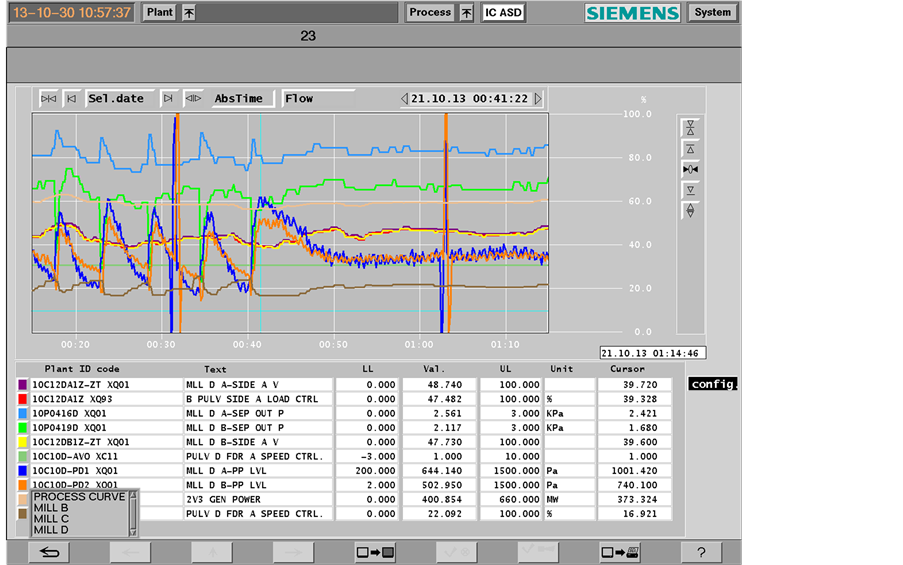
Figure 2. Material level fluctuation curve of D coal grinding
图2. D磨料位波动曲线
优化方案:磨正常运行时,磨煤机两侧的一次风通过各自的中心管进入磨煤机的筒体,在筒体内对冲后裹挟着筒体内悬浮煤粉通过绞笼与中心管间的环形通道分离器接管。在分离器接管中容量风、旁路风和密封风汇合,以风粉混合物状态进入分离器。磨煤机的容量风挡板的开度控制在60%以下,调门开度线性区是一个范围,超过60%后,挡板的线性差,影响机组燃烧的自动控制。进入到磨煤机内的两侧风量对冲中心不能偏离大罐中心,否则两侧携带煤粉能力不一致。可通过设定容量风两侧的偏置,使两侧容量风量相同、对中,消除筒体压力震荡现象。
2) 密封风箱压力取点、压力值偏高。磨煤机运行时密封风压力与筒体压力设计差值为2~3.5 KPa,此时不会漏粉,还会减少密封风圈的磨损和消耗。现取一端在一次风关断门后,一端在密封风门后,数值在5~6 KPa左右,此方案远高于密封风压力与通体压力设计差值。为解决这一问题应将密封风机出口调节挡板开度适当减小。密封风系统如图3所示。
5. 磨煤机料位改造后的效果
1) 磨煤机料位改造后,锁气器动作次数有了明显的降低。锁气器位于分离器的回粉管路上,使不合格的粗煤粉回到磨煤机大罐内,同时锁断气流,防止煤粉或灰粉在某一压力范围时,发生空气窜流现象,保证粉粒的顺利流通。本厂每台磨的单侧装有2个重锤锁气器,分别是位于外部回粉管路上的锁气器和内部回粉管路上的锁气器。锁气器结构参数如图4。
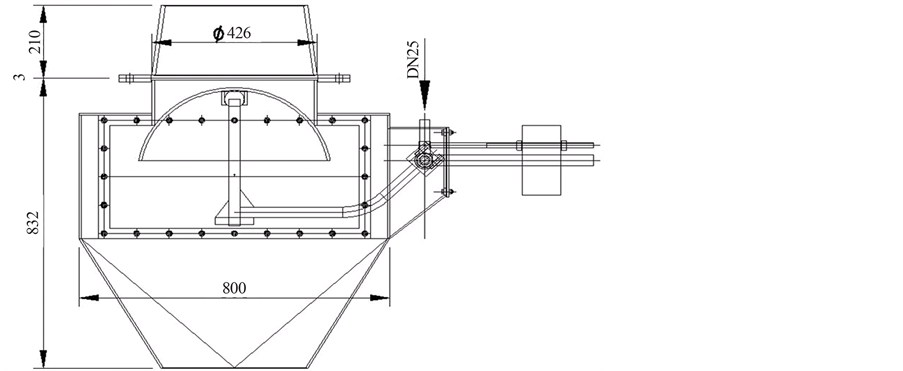
Figure 4. Structure parameters of air lock device
图4. 锁气器结构参数
锁气器关闭时,管道常闭。当分离器回落下不合格的煤粉落在锁气器的伞形阀体上,随着煤粉的重量增加,磨煤机至出口压力增大,积累至大于外部重锤的力量时,阀体向下动作打开缝隙,煤粉回落到磨煤机大罐内,同时有效地阻止空气通过。
压差料位值与分离器回粉管中锁气器的值:500 Pa料位设定值,锁气器重锤向磨煤机释放粗颗粒煤粉周期为11~12 s;1100 Pa料位设定值,锁气器重锤向磨煤机释放粗颗粒煤粉周期为24~25 s;料位改造后,测量值准确、真实,磨煤机料位提高时,粗煤粉颗粒减少一半,由之前11 s动作一次提至20~24 s动作一次。回粉管出口压力降低,降低了磨煤机出力,电流降低,一次风压也随之降低,减少了一次风机、磨煤机的消耗。改造前后参数如表1所示。
2) 磨煤机料位改造后,系统运行状态很好,料位系统无故障运行,大大降低了炉控检修人员的维护量。改造前的料位系统包括就地PLC控制、气源管路、料位测量系统,磨煤机料位检测装置属于开放式运行,管路泄漏无检测与报警装置,正常运行时经常出现测量管路泄漏造成料位测量不准。此情况下检修人员采用肥皂水对管路上存在的泄漏点进行一一涂抹测漏,工作量大且效率低,控制柜出口接头泄漏,由于地方狭小,接口在弯头弧部,不易对正,强行紧固容易把接头损坏。磨煤机本体入口阀门及接头存在泄漏,一是接头本身未密封好,二是阀门(普通阀门)接口也易漏。再者阀体也有漏的可能,改造后的料位系统增加了管路泄漏自动检测功能,停磨后,进入磨煤机大罐内将上、下探针用堵头封住,利用控制柜上的触摸屏进行检漏操作,这种操作方式对泄漏管路定位精确,很大程度上节省了人力,提高了维护人员的工作效率。
3) 新的料位测量系统采用“吹气测量”,测量回路的气压始终比大罐内的压力高1.8 kPa,上、下探针的气压比罐内的气压大,不容易堵塞探针。改造前的料位系统是微压测量装置,控制料位测量气源的执行机构是通过就地PLC控制,执行机构采用比例换向阀,在控制精度、响应时间上不能满足现场需求,罐内压力增大时,开门不及时导致探针端口堵塞的现场时有发生。虽有吹扫功能,但因是微压,不足以吹扫净死沉积和固化沉积,也会造成测量系统探针端口堵塞,严重时煤粉进入到测量管路。检修人员只能在设备停运时进行堵塞管路的疏通工作,影响制粉系统的控制和发电效益。测量管路的堵塞及泄漏促使料位测量值严重失真造成堵磨或空磨故障发生。在机组升降负荷时无法提供燃料的及时供给,造成机组调系统、AGC的投入指标不能满足电网要求。改造后的调节仪采用恒和调节仪,执行机构是微量调节阀,气源回路控制稳定,吹扫时间由以前的15分钟延长到20分钟与120分钟范围之间。
新的料位测量系统在安装过程中将控制柜及其内部的设备全部更换,之前的管路也进行了更换,发现在中空管的下方存在磨损的测量管路,进行了更换,上、下探针加装了保护套,增强了测量装置的耐磨性。每台磨的测量装置加装了汽水分离器,保证了气源品质,且方便检查。
4) 差压料位系统与给煤机给煤存在对应关系,当手动改变给煤量时,压差料位值趋势曲线在延迟一段时间后应该产生波浪式响应。在磨煤机自动运行时,可以自动跟踪负荷改变给煤机给煤量。之前存在料位波动大,给煤量变化后,压差料位无对应变化趋势的问题,磨的料位自动只能在手动方式。改造后
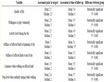
Table 1. Effect of contrast for before and after the transformation
表1. 改造前后效果对比
的磨煤机差压料位系统的检测装置属于全闭环运行系统,使运行状态可视化监测和故障预防报警。并加强前馈测量系统功能,将磨煤机筒体压力变化参数引入到PID控制调节子系统,提高动态跟踪衡压差源同步速度和精确度,实现精准检测,在磨煤机正常运行中,能够快速、准确的测量出磨煤机内部的煤粉料位,保证自动的投入率,减少故障的发生,为高料位运行提供了先决条件,进而能发挥双进双出钢球磨的特有优势,为节能、降耗、减排做出贡献,并保证了机组的安全稳定运行。
6. 结论
通过对河曲电厂磨煤机料位测量方式的介绍,提出在运行过程中出现的问题,并针对以上问题进行改造,改造后锁气器动作次数减少,系统运行良好,降低了炉控检修的工作量,并增加了测量回路气压,探针不易发生堵塞,能够准确测量煤粉料位,为机组安全运行提供了保障。