1. 引言
装配式建筑的连接方法,从施工方法角度大致可分为干式连接和湿式连接两类 [1] 。螺栓连接属于干式连接,是一种通过螺栓杆件及螺母将上下层预制构件连接为整体的连接技术 [2] ,具有施工便捷、安装效率高等优势,在装配式墙板的连接安装中经常被使用。作为整个墙板的薄弱处,连接处的锚固破坏是外墙板破坏的主要形式之一,因此连接的可靠锚固是其安全使用的前提 [3] [4] [5] 。陆春阳等 [6] 对陶粒混凝土与钢筋粘结锚固性能进行了抗拉试验研究,张玉等 [7] 建立了轻质混凝土与钢筋粘结强度概率模型。轻质混凝土中预埋螺栓套筒采用螺栓连接的锚固拉拔性能,还未见相关文献资料研究。
本文对一种新型陶粒发泡混凝土材料的力学性能进行了研究,并设计了8个锚固拉拔试件,对该混凝土材料的锚固拉拔性能进行了综合评估分析,为之后该类型混凝土及锚固方法应用于装配式外墙提供了相关的锚固理论依据。
2. 材料性能试验
本试验研究采用新型陶粒发泡混凝土(下文简称混凝土),该材料是一种使用闭孔发泡技术,将水泥胶凝材料、陶粒骨料、外加剂和水按一定比例均匀混合并搅拌发泡,经浇筑成型、振动密实、养护制成的轻质混凝土。
材性试验采用与锚固试件制作同批次的混凝土,共制作3组9块边长为150 mm的标准立方体试件和5组15块尺寸为150 mm × 150 mm × 300 mm的标准棱柱体试件。试验采用20吨多功能试验机,在同济大学土木工程防灾国家重点试验室进行。
2.1. 立方体材性试验
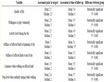
Table 1. Test results of cube specimens
表1. 立方体试块试验结果
立方体试件分为A、B、C三组,分别编号为A1~A3、B1~B3、C1~C3。在试验前使用电子称对立方体试件进行称重,以获取混凝土的容重。试验过程中,随着压力的逐渐增加,试件表面在高度中央出现了竖向并沿斜向往上、下端发展的裂缝,裂缝逐渐发展到承压面,转向试件角部,继续施加荷载,裂缝由表层逐渐向内部发展,表层混凝土开始向外鼓凸、剥落,试件破坏。经试验研究,该种类混凝土的平均立方体抗压强度为7.13 MPa,容重为907.26 kg/m³,主要试验结果详见表1。
2.2. 棱柱体材性试验
棱柱体试件分为A、B、C、D、E共5组,每组各三块,D、E组试块测试弹性模量。对A、B组三块试件进行棱柱体抗压强度试验后,以该组棱柱体强度试验结果的平均值的1/3作为弹性模量试验的试验加荷标准。弹性模量试验采用混凝土弹模测定仪进行,棱柱体的弹模平均值为4.57 × 103 MPa,平均棱柱体抗压强度为5.36 MPa,主要试验结果详见表2。
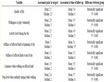
Table 2. Test results of compressive strength of prism specimens
表2. 棱柱体试块抗压强度试验结果
3. 锚固拉拔试验
3.1. 试件制作
试验共制作了8块新型陶粒发泡混凝土锚固试件,JD1~JD8。锚固试件连接组成主要包括四部分:① 双层双向钢筋网:采用HRB400钢筋,钢筋直径为8 mm;② 龙骨钢架:龙骨钢架的钢材选用厚度为1.5 mm的Q235B钢板制成,龙骨钢架之间进行焊接连接;③ 挂点套筒:连接螺栓采用高强螺栓8.8级,套筒采用M20的配套产品;④ 套筒固定钢板:钢板采用与龙骨钢架同级别钢材,厚度为4 mm,钢板通过焊接方式与龙骨钢架和挂点套筒连接。厚度为120 mm和150 mm的锚固试件对应的双层双向钢筋网的间距分别为84 mm和114 mm,对应的龙骨钢架宽度分别为60 mm和90 mm。锚固试件的参数设计表详见表3,试件构造详图如图1所示。
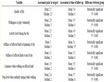
Table 3. Parameter design table of specimens
表3. 试件参数设计表
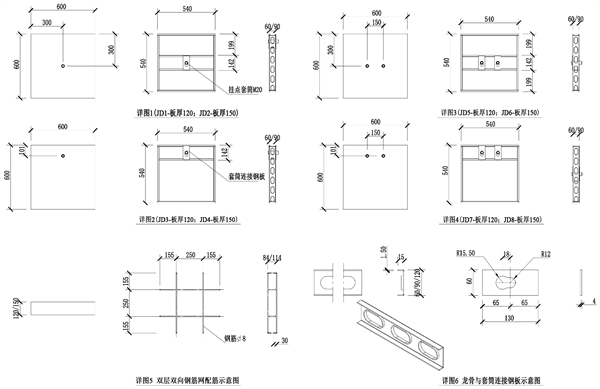
Figure 1. Detailed drawing of anchorage pullout specimens
图1. 锚固拉拔试件详图
3.2. 试验方案
试验对锚固试件的厚度、挂点套筒数量、挂点套筒位置三方面因素对连接的锚固拉拔性能影响进行了研究。试验开始前先对试件进行0.5 kN的预加载,减少连接装置的间隙带来的位移误差。预加载完成后,采用位移控制加载,加载速度为1 mm/min,每级加载1 mm,5 mm后连续加载,加载速度为2 mm/min,直至锚固试件发生明显破坏或拉力下降到峰值拉力的85%以下,停止加载,试验结束。加载过程中仔细观察并记录试件裂缝出现及发展规律。
试验通过两根截面边长为10 cm的高强钢压梁对试件进行固定,钢梁通过地锚固定,试件通过螺杆与定制的连接装置连接后与作动器相接(见图2)。为准确测得挂点套筒和锚固试件表面的变形位移,在定制连接件和试件表面放置了位移计,并以该数据对试件的荷载–位移曲线进行修正。
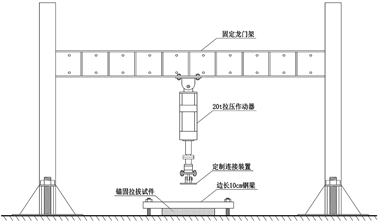
Figure 2. Installation diagram of test device
图2. 试验装置安装示意图
4. 试验结果及分析
4.1. 试验现象
锚固拉拔试件在试验过程中的试验现象基本接近,在加载的前期,曲线处于弹性阶段,荷载位移曲线基本呈现线性增长。荷载达到线性阶段的峰值后,试件开始发生塑性变形,试件承载力逐渐增加,继续延性变形。随着位移不断增大,板面整体被拉起,拉拔产生的裂缝明显,试件破坏,各试件最终破坏形态如图3所示。

Figure 3. Failure mode diagrams of JD1~JD8 specimens
图3. JD1~JD8试件破坏形态图
在极限承载力方面,JD6试件的极限荷载最大为124.53 kN,JD3试件的极限荷载最小为40.66 kN。在试件延性方面,JD4试件的延性表现较差,其余试件的破坏变形均在15 mm~20 mm之间,拉拔承载力和延性变形能力表现较好。在破坏形态方面,8个锚固试件均发生了延性破坏,破坏时试件表面裂缝开展明显,形态均为从连接套筒向试件板边开展。试验结束后将锚固试件表面混凝土除去,连接龙骨钢架和钢筋变形明显(见图4),底层混凝土与连接部分脱离,表明该连接整体与混凝土锚固较为可靠,未发生整体拔出的破坏形式。
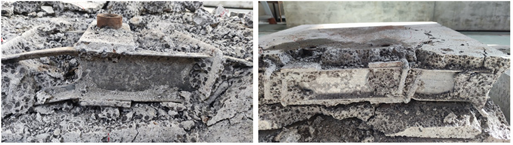
Figure 4. Keel steel frame and steel reinforcement deformation of typical specimens
图4. 典型试件龙骨钢架和钢筋变形
以JD1试件为例定量说明单个试件的具体破坏情况。预加载0.5 kN,加载试件进入弹性阶段,当荷载达到27.13 kN时,作动器位移为2 mm,此时裂缝出现从板边向连接位置发展,裂缝宽度约0.06 mm。当作动器位移为4 mm时试件表面裂缝明显增多,此时裂缝宽度为0.2 mm,试件塑性变形明显,继续加载,试件承载力缓慢增加,裂缝大量出现且宽度不断加宽,出现破坏趋势。最后试件混凝土表面隆起,表层混凝土碎裂,试件破坏,试件的最大荷载为46.58 kN。
4.2. 荷载–位移曲线
以挂点套筒的位置变化作为控制变量,保证其他构造相同,将荷载–位移曲线进行对比(见图5)。在初始加载线性阶段,连接套筒的位置改变对曲线斜率几乎没有影响,说明此时连接部分的龙骨钢架与套筒能够较好地协同工作。荷载继续增加,曲线进入弹塑性阶段,在构造情况相同的情况下,连接套筒居中可显著提高试件的极限承载力,极限拉拔承载力提升10~20 kN。在变形能力方面,当试件板厚为120 mm时,连接套筒对试件变形能力的影响并不明显,随着板厚的增加,挂点套筒的居中放置能够有效改善试件的延性,提高锚固试件的拉拔变形能力。
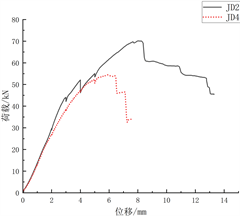
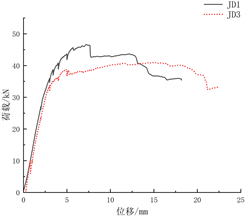
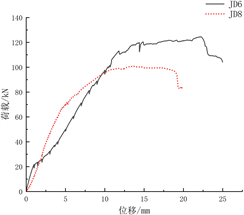
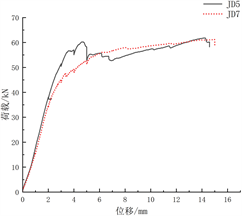
Figure 5. Comparison of load-displacement curves at sleeve position
图5. 套筒位置荷载–位移曲线对比
以挂点套筒数量作为控制变量,保证试件其他构造相同,将荷载–位移曲线进行对比(见图6)。通过曲线对比可以看到,增加锚固拉拔试件中连接套筒的数量改善了试件连接位置的受力模式,从而能显著提高试件的拉拔承载力,最大的试件承载力提升在60 kN左右,拉拔性能提升近一倍。由此可知,挂点套筒数量是锚固试件拉拔承载力提高的关键。通过曲线比对,挂点套筒的数量也会对锚固试件的延性产生一定的影响。当板厚为120 mm时,试件拉拔塑性变形阶段的延性随着连接套筒数量的增加而稍微降低;当试件板厚为150 mm时,连接套筒数量的增加会显著提高锚固试件塑性变形阶段的延性和变形能力,有效改善了试件的拉拔锚固性能。
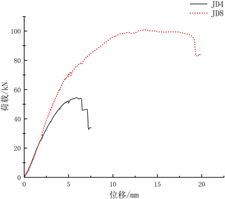
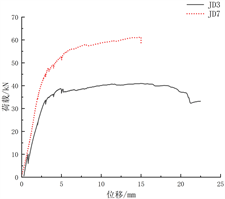
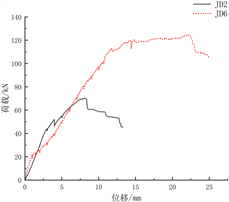
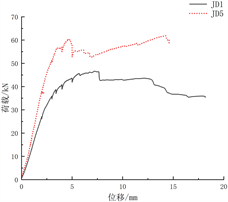
Figure 6. Comparison of load-displacement curves at sleeve number
图6. 套筒数量荷载–位移曲线对比
以厚度作为控制变量,在其他构造相同的情况下,将荷载–位移曲线进行对比(见图7)。通过增加连接龙骨钢架宽度和锚固试件板厚可以有效提高试件的拉拔承载力。对于JD1~JD4试件,由于预埋连接套筒数量为一个,拉拔时连接集中力较大,厚度的增加会使得锚固试件的延性和变形能力降低,降低连接节点处的锚固拉拔性能。对于JD5~JD8试件,预埋的连接套筒数量为两个,锚固试件板厚和连接龙骨宽度的增加能使试件的拉拔承载力、延性和变形能力有较大提升。
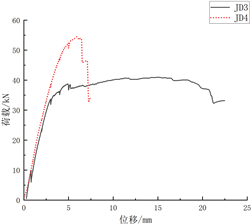
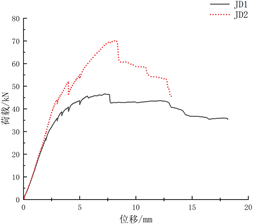
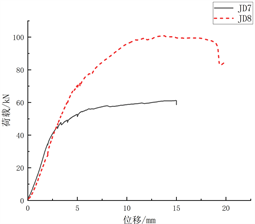
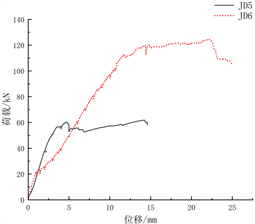
Figure 7. Comparison of load-displacement curves at anchor specimen thickness
图7. 锚固试件厚度荷载–位移曲线对比
5. 锚固拉拔承载力分析
采用《装配式混凝土结构技术规程》(JGJ 1-2014) [8] 中给出的荷载组合效应公式对持久设计状况和地震设计状况两种工况进行拉拔承载力分析。选取处于较不利应用环境下的预制外墙板进行计算,尺寸4.2 m × 3.3 m × 0.2 m。假定墙板处于8度区,基本风压0.7 kN/m2,地面粗糙度A类,每块墙板由两个支承预埋件和四个调节标高用预埋件组成,构件竖向自重主要由支承预埋件承担,风荷载和地震荷载作用下产生的水平力主要由调节标高用预埋件承担。
1) 地震作用
水平地震作用标准值时,可采用等效侧力法,根据文献 [8] 规定,按下式进行计算:
(1)
基材容重按照试验结果取9.0 kN/m3,单块墙板受到的地震力FEhk = 20.0 kN。
2) 风荷载作用
根据《建筑结构荷载规范》(GB 50009-2012) [9] 规定,外墙板的风荷载标准值
按下式计算:
(2)
风荷载标准值按照基本风压0.7 kN/m2、粗糙度类别A、离地面高度80 m的条件估算,
,墙板所受的风荷载作用力为60.5 kN。
3) 预埋螺栓拉力设计值
按照每块墙板所受的水平力仅由限位预埋螺栓承担计算,地震作用及风荷载作用下,其受力分别为5.0 kN和15.1 kN。持久设计状况和地震设计状况下,根据文献 [8] 规定,单个预埋螺栓所受的拉力设计值分别按照下式计算:
(3)
(4)
持久设计状况拉力设计值Sd = 22.7 kN、地震设计状况拉力设计值SEh = 11.5 kN。
综上,预制外墙板位于8度区、基本风压0.7 kN/m2、地面粗糙度A类时,新型陶粒发泡混凝土基材中预埋的螺栓抗拉承载力大于22.7 kN时,可以满足抗拔承载力的需求。根据试验结果,试验所有连接节点的弹性变形阶段最大荷载基本均大于该水平力,可满足实际工程使用要求。
6. 试验结论
本文通过开展新型陶粒发泡混凝土材料性能试验和锚固拉拔试验研究,得出以下主要结论:
1) 采用试验提出的锚固连接构造做法,试件均发生延性破坏,拉拔承载力和变形能力表现较好,破坏时连接的龙骨钢架和钢筋变形明显,共同参与受力。
2) 连接套筒居中布置可提高试件的极限承载力,随着板厚的增加,能够有效改善试件的延性,提高拉拔变形能力;连接套筒数量的增加能显著提高试件的拉拔承载力,随着板厚的增加,会显著提高锚固试件的延性和变形能力;增加锚固试件厚度可以有效提高试件的拉拔承载力,连接套筒数量变化对锚固试件的延性和变形能力影响不一致。
3) 根据试验研究与锚固拉拔承载力分析结果,证实了该种连接装置的新型陶粒发泡混凝土的锚固拉拔性能能够满足实际的装配式墙板工程应用。