1. 引言
连铸过程钢水经过浸入式水口进入结晶器,钢水中的Al2O3、高熔点的铝酸钙等夹杂物会在水口内壁粘结堆积,造成水口部分或完全堵塞[1] -[3] 。中间包水口堵塞是影响连铸生产的一个重要问题,首先,由于堵塞不得不更换水口从而影响生产的连续性甚至造成停浇,使得成本增加、生产率降低以及质量下降;堵塞改变钢水在水口及水口出口的流动形态,造成由浸入式水口流出的钢水偏流,从而影响钢水在结晶器内的流动,导致产生铸坯表面质量缺陷,严重时会造成漏钢;脱落的堵塞物不仅干扰流动,还容易被凝固前沿捕捉成为铸坯中的大型夹杂物,或进入结晶器保护渣中改变渣的成分,亦可造成铸坯缺陷;由于水口堵塞,节流装置必须进行补偿(开口度增大),造成结晶器液面波动,也容易产生铸坯缺陷。
浇铸不经过钙处理的铝镇静钢水时,水口堵塞主要是由于钢水中的Al2O3夹杂物粒子在水口壁面上的沉积造成的[4] [5] ,影响沉积的因素比较多,钢水流速、钢水中的Al2O3夹杂物浓度、吹Ar气量[6] -[10] 以及水口结构均为影响沉积的重要因素。本文采用数值模拟方法,研究了水口吹氩量以及水口开度对水口内壁夹杂物沉积的速率问题。
2. 水口沉积数学模型
2.1. 假设条件
在水口吹入氩气的情况下,钢水中的Al2O3夹杂物在水口内表面上的沉积是一个气液两相共存、并涉及夹杂物颗粒在钢水中运动的复杂过程,为了建立沉积模型,有关钢液、气泡和夹杂物的假设如下:
1) 认为钢液为粘性不可压缩的牛顿液体;2) 不考虑水口内自然对流对钢液流动的影响;3) 认为水口内钢液流动为湍流流动;4) 由于钢水通过水口的时间极短,忽略钢水流经水口时的温降,即将水口壁设为绝热。5) 假定氩气进入钢液后形成的气泡尺寸相同;6) 假定生成的气泡呈球形和刚性的;7) 忽略气泡之间的相互作用。8) 假定夹杂物呈球形,并且在钢液中均匀分布;9) 与钢液总的体积相比,夹杂物的体积很小,故忽略其对总体积和各相体积分数的影响;10) 忽略夹杂物对钢液流动的影响。
2.2. 控制方程
基于上述假设,描述水口内氩气与钢液两相流流动过程的控制方程如下:
1) 连续性方程;2) 动量守恒方程;3) 湍流方程(k-ε方程);
以上方程中的经验常数C1,C2,Cμ,σε,σk目前通常采用Launder和Spalding的推荐值[11] ,C1 = 1.44,C2 = 1.92,Cm = 0.09,sk = 1.00 and se = 1.30。
Al2O3夹杂物粒子在水口壁面上的沉积过程实质上是夹杂物粒子在钢水中以及在边界层内的传质、在壁面上的吸附过程,夹杂物粒子在壁面上的沉积速率取决于夹杂物在这一过程的传质速率。因此研究这一过程必须考虑夹杂物粒子在钢水中的传输速度。
结合粒子相和钢水连续方程,可以推导出粒子相的传输速度。两相的动量方程分别为:
(1)
(2)
其中,
表示相间的动量传递。上两个方程消去压力梯度后,得到:
(3)
作如下假设:
1) 离散相(即夹杂物粒子)瞬时达到最终速度,因此瞬态项可以忽略;
2) 作以下近似: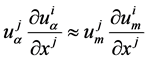
3) 粘性力和宏观扩散力忽略不计。
根据以上假设,方程(3)可以简化为:
(4)
此外,再假设相间动量传递仅由拖曳力引起,以及假设颗粒均为球形:
(5)
由此可以导出以下关于粒子相对钢水的传输速度的关系式:
(6)
式(6)中,拖曳力CD根据Schiller Naumann模型计算得出。
2.3. 求解过程
计算模型中的流体控制域包括水口座砖、上水口砖、滑动水口、下水口砖以及浸入式水口共同组成的钢水通道区域,如图1所示。入口速度根据浇铸速度来确定,采用无滑移边界条件,侧孔出口设定压力条件,钢水中的Al2O3夹杂物质量分数通过钢液中的T[Al]和SO[Al]计算得出。计算模型中的物性参数见表1,计算域几何模型见图1。
3. 结果及分析
3.1. 水口内沉积模拟结果
图2为钢水中的Al2O3夹杂物粒子在水口内沉积的模拟结果。左图显示在上水口砖和浸入式水口内壁面上、滑动水口处的滑板上下表面以及孔内均出现沉积现象,滑板处的沉积比较明显,而内壁面上只出现比较薄的一层沉积。同样,右图显示在水口底部出现较为明显的沉积,而在内壁面以及出口内壁面的沉积层比较薄。
结合水口内钢水流场特征可知,出现明显沉积的部位为钢水冲击处以及回旋区域,在这些地方钢水流速变化较大,方向急剧改变。从动力学角度分析,在这些区域紊流程度大,速度边界层和浓度边界层比较薄,有利于夹杂物粒子向沉积界面的传输。
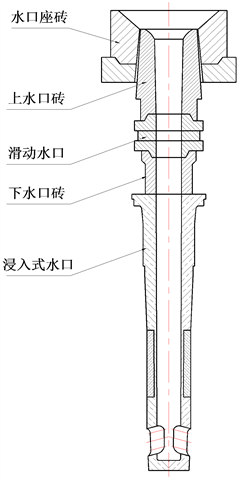
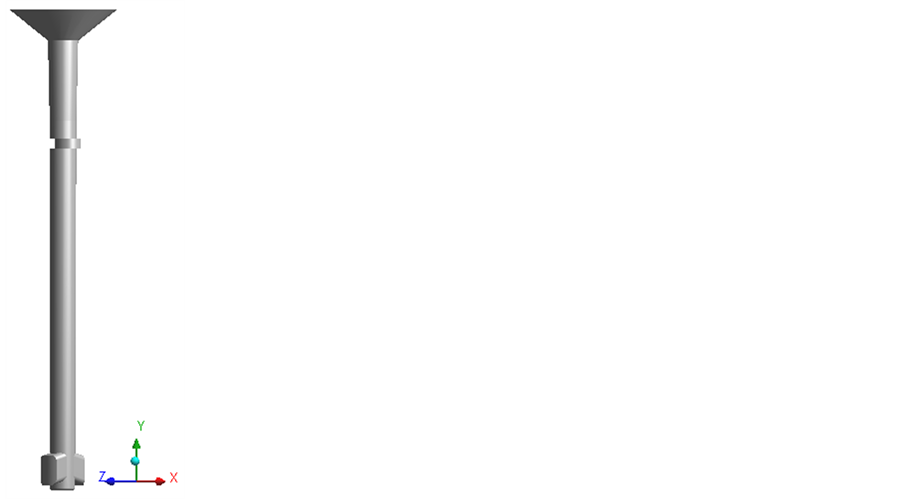
Figure 1. Nozzle structure diagram and computational flow model
图1. 水口结构示意图及计算域几何模型
表1. 模拟计算中的物性参数
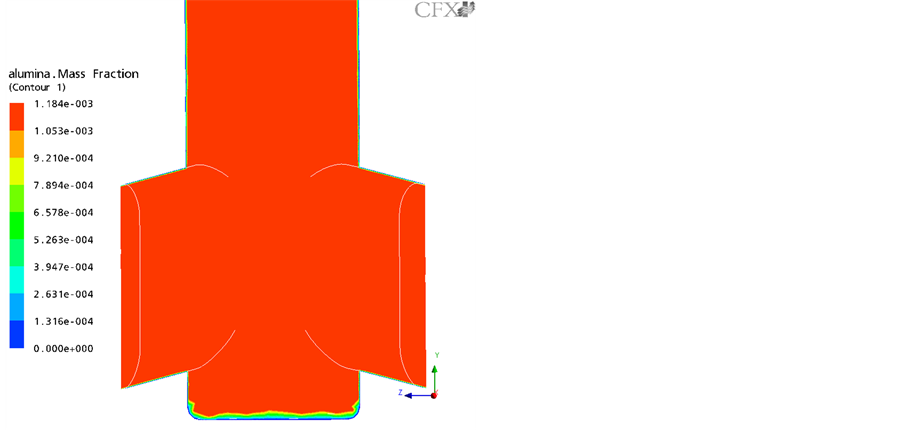
Figure 2. Simulation results of alumina deposition
图2. 水口Al2O3沉积模拟结果
3.2. 氩气吹入量和水口内压力的关系
钢水流经滑动水口后产生较大的负压,极易造成空气吸入。如果空气进入水口,氧气将和钢水中的[Al]反应生成氧化铝夹杂。吸入空气造成二次氧化,是水口堵塞的一个原因[4] [16] 。目前防止或减轻吸气的方法主要有两种,一是加强水口接缝处的密封,二是吹入氩气以增加水口内的压力。
图3表示在整个水口高度方向上,不同的水口开度下不同氩气流量时水口内压力分布的模拟计算结果。图中纵坐标零点为水口座砖上表面的中心点。吹氩量对水口内的压力分布存在较大的影响,不吹氩气时,水口内压力最低,随着吹氩量增大,水口内压力随着升高,整个压力曲线向增大的方向移动。在整个水口内部,钢水经过滑板后,压力在滑动水口处存在突降,压力最低值出现在下滑板下方,因此如果滑动水口处密封不好,极易造成吸气。
图3(a)水口开度K = 66.45%,不吹氩时,压力最低值约为0.831 × 105 Pa。当吹氩量低于10 L∙min−1时,水口内大部分区域尤其是滑板处的压力低于1.013 × 105 Pa,由于水口内压力低于1.013 × 105 Pa时,容易造成吸气,要防止吸气,水口开度K = 66.45%的情况下最小吹氩量约为10 L∙min−1。
图3(b)-(d)分别为水口开度K = 58.36%、K = 50.46%和K = 42.82%时的水口内部压力分布曲线。随着开度减小,不吹氩气时,滑动水口处的压力突降更为明显,吸气趋势增大,并且使水口尤其是滑动水口处保持正压的吹氩量相应增大,当K=58.36%时,使滑板处保持正压的吹氩量约为15 L∙min−1,K = 50.46%时,吹氩量大于20 L∙min−1才能使滑板处的压力大于1.013 × 105 Pa,K = 42.82%时,这一值增大到25~30 L∙min−1。
以上3种开度的计算是在铸坯拉速为1.2 m∙min−1的情况下取得的,随着拉速的提高,使水口滑板处保持正压的吹氩量需要相应增加。
3.3. 水口吹氩量对沉积速率的影响
图4为不同浇铸速度时吹入的氩气流量对沉积速率的影响模拟计算结果。吹氩量对沉积速率的影响同样存在明显的规律,而且开度不同时,存在不同的规律。
由图4(a)可见,在较大开度下,吹氩量较小时,沉积速率显著降低,并存在一个最低点,随着吹氩
量增大,沉积速率上升,达到最大值后,随着吹氩量进一步增大,沉积速率又减小。对低于1.4 m∙min−1的较低浇铸速度,使沉积速率最小的吹氩量范围为5 L∙min−1左右,吹氩量为10 L∙min−1左右时沉积速率最大,拉速增大至1.5 m∙min−1以上时,沉积速率最低值对应的吹氩量右移,为10 L∙min−1左右,最高值对应的吹氩量为12.5 L∙min−1。氩气吹入钢液后对钢液流场的影响是产生上述结果的原因。低吹氩量时,
(a)(b)
(c)(d)
Figure 3.
图3. 不同开度时吹氩量对水口内压力分布的影响。(a) 66.45%; (b) 58.36%; (c) 50.46%; (d) 42.82%
(a)(b)
(c)
Figure 4.
图4. 不同水口开度氩气流量对沉积速率的影响。(a) 66.45%; (c) 50.46%; (d) 42.82%
气泡进入钢液时的流速低,贴着壁面上浮并与钢液混合,氩气的体积分率在临近壁面的区域较高,影响了Al2O3粒子向沉积边界的传递,降低了沉积速率。吹氩量增加时,气泡逐渐远离壁面,氩气的体积分数在中心区域较高,相当于把钢水向壁面挤压,此时不仅不能降低沉积速率,反而会使沉积加快。但随着吹氩量进一步增加,氩气和钢液剧烈混合,氩气体积分数趋于一致,气泡严重阻碍了夹杂物粒子的传输过程,导致沉积速率重新开始下降。
图4(b)和图4(c)开度减小,吹氩量对沉积速率的影响规律则与大开度时的规律不完全一致,沉积速率随着吹氩量的增加始终呈下降趋势。主要原因仍然是水口内钢水流场特性造成的,开度越小,钢水流经滑板后紊流程度越大,与氩气的混合更为充分,因此未出现大开度时的影响规律。从图4(b)和图4(c)可以看出,对于同一拉速来说,吹氩量在大于15 L∙min−1后,再增加吹氩量对降低沉积速率没有明显效果,而大吹氩量会造成结晶器液面的波动加剧,铸坯表面夹渣、皮下气泡的缺陷数量会大大增加。
结合图3所示的吹气量对水口内压力影响的计算结果,大开度(>60%)时,要防止吸气,最小吹氩量约为10 L∙min−1 (开度越大此值越小),而使沉积速率最小的吹气量为5~10 L∙min−1 (拉速越高此值越大),综合考虑,大开度下(>60%)合适的吹气量应为10 L∙min−1。
小开度时(<60%),要防止吸气,最小吹氩量约为15 L∙min−1以上(开度越小此值越大),而沉积速率随着吹气量的增加而降低,但吹气量为15~20 L∙min−1以后下降幅度很小。考虑大吹气量带来的危害,小开度下(<60%)合适的吹气量应为15~20 L∙min−1。
4. 结论
1) 在水口内所有壁面均出现沉积现象,滑板附近处以及水口底部的沉积比其他壁面更为明显。
2) 吹氩量对水口内的压力存在较大的影响,不吹氩气时,水口内压力最低,随着吹氩量增大,水口内压力随着升高,整个压力曲线向增大的方向移动,压力在滑动水口处存在突降。
3) 使水口滑板处保持正压的吹氩量随着开度的减小而增大。
4) 吹氩量对水口内沉积速率的影响规律与滑板开度有关。大开度时,较小吹氩量5~10 L∙min−1可以使沉积速率降至最低,但随着吹氩量进一步增大时,沉积速率反而增加,至最大值后再次下降。小开度时,随着吹氩量的增加,沉积速率均为下降趋势,但吹氩量大于15~20 L∙min−1以后,增大吹氩量对降低沉积速率的效果并不明显。
5) 综合考虑吹气量对水口内压力和对沉积速率的影响,大开度下(>60%)合适的吹气量应为10 L∙min−1。考虑大吹气量带来的危害,小开度下(<60%)合适的吹气量应为15~20 L∙min−1。