1. 前言
高炉冶炼是在炉料下降和煤气上升还原过程中进行的,要想实现高炉稳定、顺行、高产、长寿,则必须保证高炉料层具有良好的透气性。烧结矿作为现代高炉冶炼最主要的含铁原料,其粒度分布对煤气流的分布和料层透气性具有较大影响[1] -[3] 。而烧结矿在高炉上部低温区发生的还原粉化会使料层的空隙度降低,透气性下降,此外,低温还原粉化率过高会使炉内矿石粉末被较多地带出炉外,增加炉尘量。生产实践表明 [4] [5] ,炉料低温还原粉化率RDI-3.15每增加5%,生铁产量下降1.5%~5%,焦比上升3 kg。另外,低温还原粉化对高炉炉龄、炉壁和热损失都有较大影响,国内烧结矿的RDI-3.15一般要求控制在30%以内 [6] 。
关于烧结矿低温还原粉化的原因,一般认为是因为Fe2O3还原为Fe3O4时由三晶系六方晶格转变为等轴系四方晶格,体积膨胀约25%,产生极大的内应力,导致烧结矿发生严重的破裂 [7] [8] 。但还有一些不同的观点:Ishikaw等人通过实验发现,烧结矿的低温还原粉化率与骸晶状再生赤铁矿的数量有非常好的对应关系 [9] [10] ;Sakamoto等利用X射线衍射分析发现,固溶了Al2O3的多组分赤铁矿的晶格面间距随Al2O3的增大而减小,他认为这一现象是引起RDI-3.15增大的原因 [11] 。本文利用显微镜观察烧结矿在低温还原20、40、60 min后的显微结构,并分别测量其显气孔率和体积的变化,对高碱度烧结矿还原粉化的机理进行探究。
2. 实验
2.1. 实验原料
实验用高碱度烧结矿为马钢现场高炉所用的高碱度烧结矿,其主要化学成分如表1所示。
2.2. 实验设备与方法
低温还原实验在铁矿石冶金性能综合测定仪上进行,其实验装置如图1所示。其主体主要包括还原反应管、加热炉、气体流量控制系统和数据采集系统四个部分。
低温还原实验方法:将高碱度烧结矿破碎、筛分后,取10~12.5 mm粒级的在105℃ ± 5℃下烘干2小时,取500 g放入还原管内,将其表面铺平。封闭还原管的顶部,将惰性气体N2通入还原管,流量为5 L/min,然后把还原管插入加热电炉中开始加热,升温速度不得大于10℃/min。当试样接近500℃时增大惰性气体流量到15 L/min。在500℃恒温30分钟,使温度恒定在500℃ ± 10℃之间。然后通入流量为
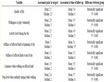
Table 1. Main chemical composition of high basicity sinter (w%)
表1. 高碱度烧结矿主要化学成分(w%)
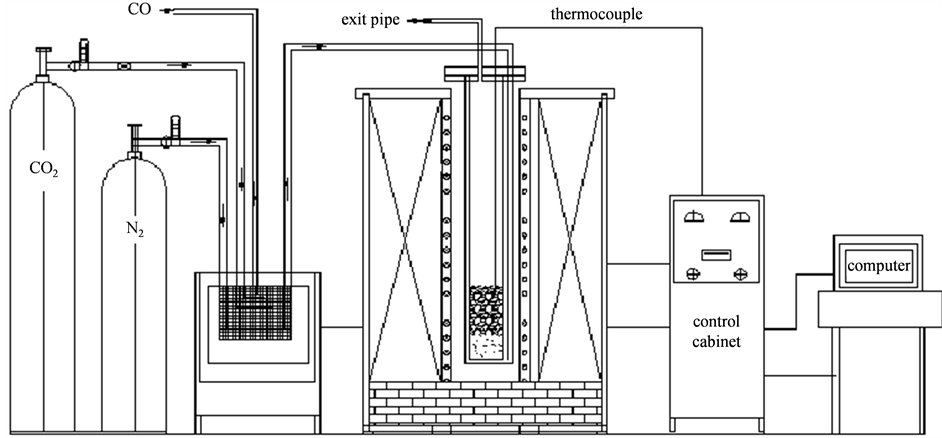
Figure 1. Schematic diagram of the experimental setup
图1. 实验装置示意图
15 L/min的还原气体,代替惰性气体,还原气体组成:CO 20%,N2 60%,CO2 20%。当还原时间分别到达20、40、60 min后停止还原气体,并向还原管中通入惰性气体N2,流量为5 L/min,然后将还原管提出炉外进行冷却,将试样冷却到100℃以下,取还原后的试样在光学显微镜下观察其显微结构。本实验过程在无荷重情况下进行。
3. 实验结果与分析
3.1. 烧结矿低温还原过程显微结构的变化
1) 还原前烧结矿的显微结构
在还原前的烧结矿显微结构中,可见到大量的铁酸钙和磁铁矿的交织熔蚀结构及骸晶状的赤铁矿。此时烧结矿中的赤铁矿多为再氧化次生赤铁矿,分布于孔洞周围或结构疏松区域,如图2(a)所示。
2) 低温还原20 min后的烧结矿的显微结构
此时,烧结矿边沿的赤铁矿开始被还原为磁铁矿,新生成的磁铁矿数量很少,但在气孔的周围,有相当多的磁铁矿生成,如图2(b)所示。
3) 低温还原40 min后的烧结矿的显微结构
此时,烧结矿的边沿有大量的赤铁矿生成,但在烧结矿边沿新生成的磁铁矿仍然很少,与低温还原20 min后的烧结矿边沿相比,磁铁矿数量几无增加,而在烧结矿气孔处,磁铁矿继续增多。如图2(c)所示。
4) 低温还原60 min后的烧结矿的显微结构
此时,烧结矿边沿磁铁矿数量明显增多,新生成的赤铁矿被迅速还原为磁铁矿,但是相对于其他矿相,磁铁矿所占比例仍然很少,如图2(d)所示。
H—hematite; F—calcium ferrite; M—magnetite
Figure 2. Microstructure of the sinter; f: 200×
图2. 烧结矿显微结构;f: 200×
综上分析,发现在500℃时的确存在赤铁矿还原为磁铁矿的反应,且此反应在气孔处进行的程度比烧结矿边沿处更多,但是程度也不是很剧烈。所以如此少的还原反应不可能造成如此多的粉化,必然还有其他的原因造成烧结矿低温还原粉化。
3.2. 烧结矿低温还原过程内部气孔结构的变化
于50倍显微镜下观察低温还原20、40、60 min后烧结矿内部气孔结构,如图3所示。从图中可以看出,还原20 min时烧结矿内部气孔在变大,并和相邻的气孔合并,此时烧结矿内还是以小气孔为主,如图3(a)所示。还原40 min后烧结矿内形成大气孔,从气孔形状可知是几个小气孔合并后形成的,大气孔通过裂纹与相邻的气孔相连,随着还原的进行,裂纹扩大,两个气孔最终会合并成一个更大的气孔,如图3(b)所示。还原60 min后烧结矿内的气孔已大到无法在50倍显微镜下完全显示了,如图3(c)所示。
通过对烧结矿低温还原过程内部气孔结构的分析,可知低温还原时烧结矿气孔不断变大,烧结矿强度变差,可知烧结矿内部气孔的变大是造成烧结矿低温粉化的一个重要原因。
从图4(b)可以看出,在两个气孔的中间处,大部分铁酸钙分解为赤铁矿和氧化钙,氧化钙进入渣相中,新生成的骸晶状赤铁矿形状规则,这部分烧结矿矿相从原先铁酸钙交织赤铁矿的致密结构变成骸晶状赤铁矿、渣相、少量未还原的铁酸钙的疏松结构。因新生成的赤铁矿形状规则,赤铁矿相互之间生成气孔,图4(b)中的Q即为骸晶状赤铁矿之间新生成的小气孔,随着反应的进行,不断有小气孔生成,新生成的小气孔不断变大,最终导致相邻两个气孔连接到一起。
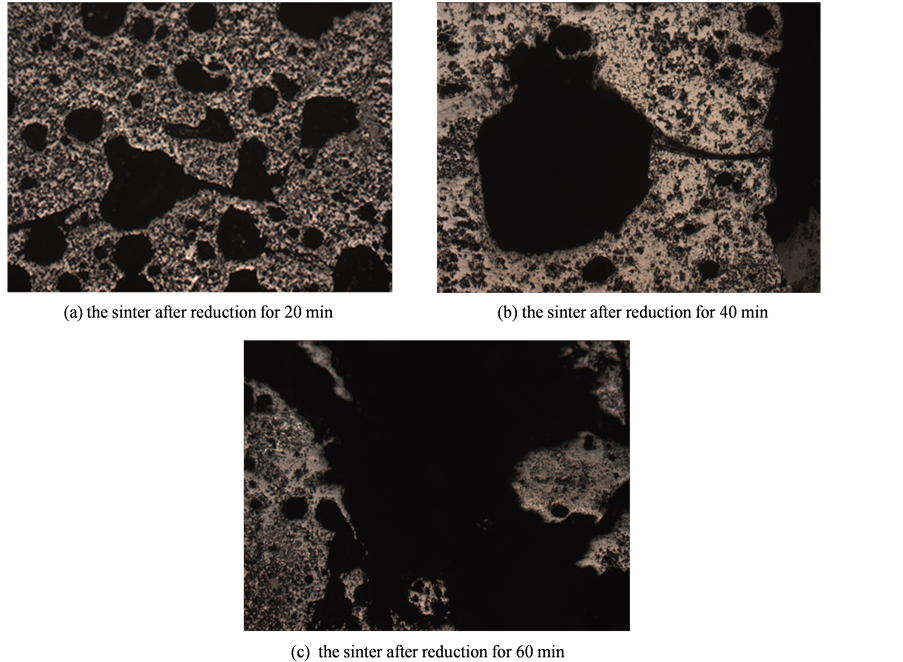
Figure 3. Porosity structure of the sinter; f: 50×
图3. 烧结矿气孔结构;f: 50×
(a) (b)H—hematite; F—calcium ferrite; M—magnetite; Q—pore
Figure 4. Porosity structure of the sinter; f: 200×
图4. 烧结矿气孔结构;f: 200×
综上所诉,铁酸钙分解为赤铁矿和氧化钙时,新生成的骸晶状赤铁矿之间生成小气孔。随着反应的进行,不断有小气孔生成,新生成的小气孔不断变大,最终导致两相邻气孔合并,随着气孔的生成和合并,烧结矿由原先铁酸钙交织赤铁矿的致密结构变成疏松大气孔结构,导致烧结矿强度不断变差,这即是导致烧结矿低温还原粉化的一个重要原因。
4. 结论
1) 烧结矿低温还原时,赤铁矿还原为磁铁矿的反应进行的很少,且还原反应多发生在气孔周围而非烧结矿边沿。
2) 烧结矿低温还原时显气孔率和体积几乎不变。烧结矿气孔的变化主要体现在烧结矿内部相邻气孔的合并和变大。
3) 烧结矿低温还原时铁酸钙分解为赤铁矿,新生成的骸晶状赤铁矿之间生成气孔,随反应的进行,新的气孔不断生成、长大,最终造成相邻气孔不断合并,使烧结矿由原先铁酸钙交织赤铁矿的致密结构变成疏松大气孔结构,从而强度不断下降,这是造成烧结矿低温粉化的一个重要原因。