1. 引言
微注塑模具型腔几何尺寸微小,使得注入微型腔的聚合物熔体体积量及携带的热量都很少,但微型腔的表面积与体积比却成倍增大。这使型腔内熔体与型腔壁面的接触面积迅速增大,散热速度加快。从而导致熔体黏度升高,流动阻力增大;使熔体流动时的黏性耗散效应和对流换热行为随之增强,进而影响熔体的平稳填充和微制件的质量。对此,国内外学者已进行了较多的研究 [1] [2] [3] 。Liu Y等 [4] [5] [6] 模拟研究了LDPE熔体在型腔中流动时的对流换热系数,结果表明,对流换热系数随熔体与型腔壁面接触面积的增加而增大;同时熔体温度和型腔壁面粗糙度对对流换热系数也有显著影响。田兴旺 [7] 等对幂律型非牛顿流体在多孔介质通道内作充分发展流动时与壁面间的对流换热系数进行了数值模拟。结果显示,Nu数与速度分布密切相关,且布林克曼数Br、达西数Da和幂律指数n等,都对Nu数有较大影响。刘焕玲等 [8] 利用数值求解方法,研究了圆形截面微通道内流体的强迫对流问题,结果表明,微通道直径越小,平均对流换热系数越大。李烨等 [9] 在H11模具钢通道中,实验研究了水流与通道间的对流换热系数,结果发现对流换热系数与水流量和热流密度成正比,与通道直径成反比。侯亚丽 [10] 采用不同直径的石英玻璃微管,进行了去离子水流动时的对流换热特性实验。结果表明,当Re较大时,对流换热强度随管径的减小而增强,但管径越小,黏性耗散效应的影响越明显;尹玉真 [11] 采用Fluent软件,对聚丙烯酰胺溶液通过多孔介质通道时的对流换热行为进行了模拟,结果表明,对流换热系数随流速和幂律指数n的增大而增大。殷素峰 [12] 等对PC和PS在不同注射速度下,流过带有不同截面尺寸口模的狭缝流变仪时的对流传热系数进行了实验和数值模拟。结果显示,熔体与型腔壁面间的传热系数与注射速度成正比,与口模截面尺寸成反比。
由于对流换热作用的复杂性,目前国内外学者大多是通过数值模拟,或利用牛顿流体来进行实验研究的,而对非牛顿流体的研究较少,对注塑成型过程中,熔体在型腔内流动时的热量交换过程的研究更为少见,更缺少不同工艺参数对熔体对流换热系数影响规律的研究。而成型过程中熔体内部的热量变化过程会直接影响熔体分子链的聚集形态,直接决定制件内部的凝聚态结构及最终的力学性能。对此,本文通过自行构建的微注塑成型实验平台,对两种不同牌号的POM熔体填充微型腔时,微型腔壁面不同位置处的温度进行了测量,并根据傅里叶定律与牛顿冷却定律计算求得了熔体与型腔壁面间的对流换热系数。同时在型腔深度为510 μm,表面粗糙度为0.062 μm条件下,对POM (M90-44)熔体填充型腔时的对流换热系数进行了数值模拟。结果发现,模拟值与实验值十分接近。
2. 实验原理与测量
2.1. 实验原理
依据传热学理论,微注塑成型流动过程中,高温熔体是通过对流换热作用,将熔体热量通过型腔壁面向外传递的,故理论上熔体与型腔壁面间的热流密度等于型腔镶块中的热流密度 [13] [14] 。而镶块中的热流密度可通过测量其温度分布来求得;另据牛顿冷却定律可知,熔体与型腔壁面间的热流密度是由对流换热系数决定的。因此只要测得模具型腔壁面的温度分布,便可利用傅里叶定律和牛顿冷却定律求得熔体与型腔壁面之间的对流换热系数。
由傅里叶定律可知,模具中的热流密度可表示为
(1)
其中,k为型腔导热系数,为 29 W∙m−1∙K−1。T1、T2分别为测得的距型腔底面0.5 mm和1 mm处的温度,l为两个温度传感器的距离,为0.5 mm。
当型腔中聚合物熔体的流动处于热未充分发展状态时,熔体与型腔壁面间的对流换热行为可用牛顿冷却定律表示,即
(2)
其中,Tm、Tw分别为熔体温度和型腔壁面温度,h为对流换热系数。
为测型腔壁面温度,应用两支温度传感器,将其等距分布安装于型腔底面,所测得的型腔壁面温度可表示为
(3)
令q1 = q2,即可求得其对流换热系数为
(4)
2.2. 实验设备及材料
实验在德国BOY 12A型微注塑机上进行,模具结构如图1所示。实验采用的微型腔深度分别为0.510 mm、0.420 mm和0.325 mm,型腔表面粗糙度分别为0.062 µm、0.393 µm和0.695 µm。使用6支K型热电偶温度传感器测量型腔壁面温度,在熔体充模流动方向距离浇口分别为6 mm、9 mm、16 mm的截面处各安装2支,同一截面上的2支温度传感器的测量端,距型腔底面的距离分别为0.5 mm和1 mm,如图2所示(图1中的A-A剖面)。温度数据采集使用瑞士Kistler公司生产的CoMo Injection 2869B型数据采集系统。实验使用的POM材料主要参数见表1。
2.3. 测量方法
待模温升至设定值后开始实验,合模后进行注射操作,同时打开数据采集仪记录温度数据,达到设定的采集时间后,一个注塑成型周期内的模具温度分布便被记录下来。为减小测量误差,每组参数条件下均重复测量五次,取其平均值作为最终结果。
2.4. 实验工艺参数
实验基准工艺参数如表2所示。
1—油孔;2—冷却水孔;3—电热棒孔;4—石棉板;5—定位环绝缘套;6—喷嘴绝缘垫;7—定模型腔镶块;8—微型腔;9—储料槽;10—动模型腔镶块; 11—温度传感器
Figure 1. Schematic of micro-injection mold
图1. 微注塑模具结构图
1—顶丝;2—顶柱;3—型腔;4—温度传感器;5—镶块a;6—镶块b;7—垫片
Figure 2. Schematic of temperature sensor installation
图2. 温度传感器安装示意图
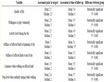
Table 1. The main parameters of experimental materials
表1. 实验材料的主要参数
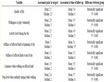
Table 2. The reference process parameters of experiment
表2. 实验基准工艺参数
3. 数值模拟
为了与实验得到的对流换热系数进行对比分析,采用Fluent软件,对POM (M90-44)熔体以不同注射速度填充深度为0.51 mm、表面粗糙度值为0.062 μm的微型腔时,熔体与型腔壁面间的对流换热系数进行了数值模拟。
模拟时假设型腔内的熔体作一维单向流动,且熔体在型腔内壁处无壁面滑移,同时忽略熔体流动时的惯性力和重力,并假设材料的导热系数λ和比热容cp为定值。采用Cross粘度模型计算熔体粘度,其表达式如式5所示,模型参数 [15] 见表3。
(5)
4. 实验测量结果及分析
4.1. 聚合物材料不同时的对流换热系数
在不同注射速度条件下,当两种POM熔体填充深度为0.51 mm,表面粗糙度为0.062 μm的微型腔时,距浇口6 mm处,得到的对流换热系数如图3所示。
由图3可见,不同注射速度下,两种牌号的POM熔体与型腔壁面间的对流换热系数变化趋势完全一致,均随注射速度的增加而近似线性增大;但两者的对流换热系数值却明显不同。其中POM (M90-44)熔体的对流换热系数比POM (M25-44)熔体平均高出321.57 W∙m−2∙K−1。这是由于POM (M90-44)材料的比热容及导热系数较大,因而熔体携带的热量多,熔体内部及其与型腔壁面间的热量传递能力较强,充模流动时的对流换热作用随之增强,因而POM (M90-44)材料的对流换热系数明显大于POM (M25-44)。
4.2. 不同型腔深度时的对流换热系数
不同注射速度条件下,当两种POM熔体填充表面粗糙度为0.062 μm,而深度不同的微型腔时,距浇口6 mm处,得到的熔体与型腔壁面间的对流换热系数如图4所示。
壁面粗糙度一定时,型腔深度尺寸的减小,意味着填充型腔的熔体体积量及其所携带的热量在减少,但型腔的面体比却成倍增加,熔体流动时的散热面积也增大,热量损失速度加快;熔体黏度升高,流动阻力增大。因此,对流换热系数随型腔深度的减小而明显增大。例如,当型腔深度从0.510 mm减小到0.420 mm和0.325 mm时,POM (M90-44)熔体在不同注射速度下的平均对流换热系数从3199.57 W∙m−2∙K−1分别增大到4545.43 W∙m−2∙K−1和7529.14 W∙m−2∙K−1。这是由于当注射速度一定时,型腔深度越小,熔体流动通道的截面尺寸就越小,充模流动时的阻力及剪切速率都增大。高剪切速率使无规缠结的聚合物分子间产生的解缠滑脱及相互摩擦作用加剧,摩擦热量增多,黏性耗散效应增强,从而引起熔
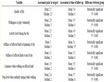
Table 3. Viscosity model parameters
表3. 粘度模型参数
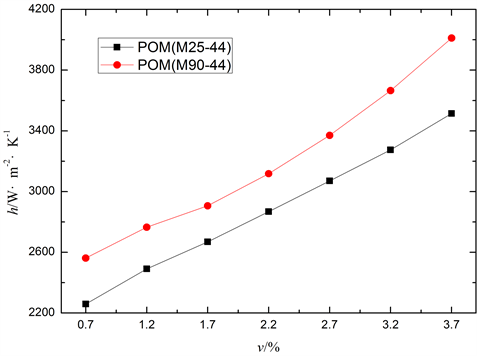
Figure 3. Variation of HTC with injection speed at different polymer materials
图3. 不同材料的对流换热系数随注射速度的变化情况
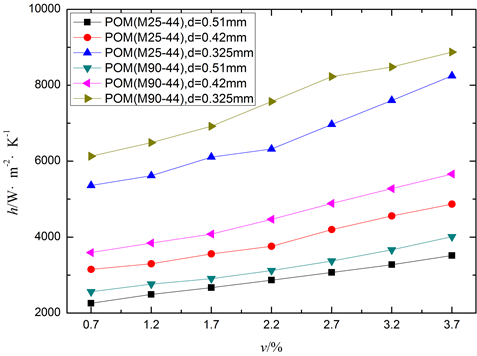
Figure 4. Variation of HTC with the injection speed at different cavity thickness
图4. 不同深度型腔的对流换热系数随注射速度变化曲线
体与型腔壁面间的温度梯度增大,对流换热作用增强。同时,型腔深度减小,型腔壁面的相对表面粗糙度就增大,而粗糙的型腔壁面会使靠近壁面层的熔体流动时产生微观不稳定流动,加快对流换热作用,从而使其对流换热系数迅速上升。
4.3. 不同型腔表面粗糙度时的对流换热系数
不同注射速度条件下,两种POM熔体填充深度为0.51 mm,而表面粗糙度不同的微型腔时,距浇口6 mm处,得到的熔体与型腔壁面间的对流换热系数如图5所示。
由图5可见,两种POM熔体的对流换热系数均随型腔表面粗糙度值的增加而近似线性增大。例如,当型腔表面粗糙度值由0.062 µm增大到0.393 µm和0.695 µm时,POM (M90-44)熔体在不同注射速度下的平均对流换热系数从3199.57 W∙m−2∙K−1增加到3901.14 W∙m−2∙K−1和4530.57 W∙m−2∙K−1。且表面粗糙度越大,对流换热系增加的越多。这是由于表面粗糙度的增大,意味着型腔壁面上的微观峰谷的峰高和谷深均加大,这会导致熔体流动的阻力增加,并使熔体在壁面处产生紊流,甚至在局部区域产生逆流,从而扰乱了熔体的平稳流态。这一方面会加速熔体内部的热量交换;另一方面也会加剧熔体流动时的剪切摩擦,导致熔体与型腔壁面间的温度梯度升高,从而使对流换热作用增强。同时,表面粗糙度值的增大还意味着熔体与型腔壁面的接触面积增大,散热速度加快,这也促进了对流换热作用的增强。
4.4. 熔体流动距离不同时,对流换热系数的实验与模拟
当两种POM熔体以不同注射速度填充深度和表面粗糙度值分别为0.51 mm和0.062 μm的微型腔时,测得不同流动距离处,熔体与型腔壁面间的对流换热系数如图6所示。
由图6可见,熔体与型腔壁面间的对流换热系数均随注射速度的提高而增大,随流动距离的增大而减小。例如,在距浇口6 mm截面处,当注射速度从0.7%增加到3.7%时,POM (M90-44)熔体与型腔壁面间的对流换热系数从2562 W∙m−2∙K−1增大到了4011 W∙m−2∙K−1,增幅达56.56%。而注射速度一定时,流动距离越小,对流换热系数越大。例如,当流动距离由6 mm增大到9 mm和16 mm时,POM (M90-44)熔体与型腔壁面间的平均对流换热系数从3199.57 W∙m−2∙K−1分别减小到2845.14 W∙m−2∙K−1和2409 W∙m−2∙K−1。这是由于充模流动的熔体与型腔壁面间的热量交换与传递是一个循序渐进和不断发展的过程,在熔体刚进入型腔时,因熔体温度远高于型腔壁面温度,熔体与壁面间的温度梯度增大,对流换热作用强烈,因而对流换热系数较大;但随熔体流动距离的增长,熔体自身热量以及流动时的黏性耗散热量不断传递给型腔壁面,使熔体温度降低,壁面温度升高,导致熔体与型腔壁面间的温度梯度下降,对流换热作用减弱,因此熔体流动距离越远,对流换热系数越小。
当POM (M90-44)熔体填充深度和表面粗糙度分别为510 μm和0.062 μm的型腔时,数值模拟与实验得到的对流换热系数如图7所示。
由图7可见,两者的对流换热系数值均随注射速度的提高而增大,随熔体流动距离的增长而减小;例如,在距浇口6 mm、9 mm和16 mm的型腔截面处,不同注射速度下模拟得到的对流换热系数平均值分别为3005.05 W∙m−2∙K−1、2680.68 W∙m−2∙K−1和2271.42 W∙m−2∙K−1,实验测量求得的平均值分别为3199.57 W∙m−2∙K−1、2846.14 W∙m−2∙K−1、2409 W∙m−2∙K−1,模拟值比实验值平均减小了6.33%、6.23%和6.09%,可见两者十分接近。模拟值与实验值之间存在误差是由于在模拟时为了简化模型和加速运算,对初始条件和边界条件进行了必要的简化和假设所导致的。
5. 不同参数耦合作用对对流换热系数的影响
分析型腔表面粗糙度ε、熔体流动距离x和型腔深度d三个参数作用的实验测量结果发现,不同参数
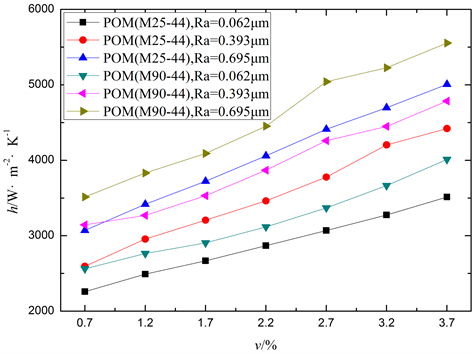
Figure 5. Variation of HTC with the injection speed at different cavity surface roughness
图5. 不同表面粗糙度型腔的对流换热系数随注射速度变化曲线
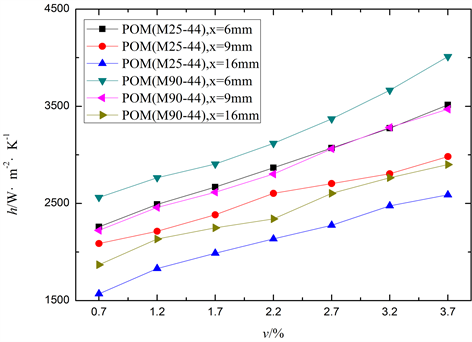
Figure 6. Variation of HTC with injection speed at different measuring positions
图6. 不同测量位置的对流换热系数随注射速度变化曲线
间的耦合作用,对对流换热系数的影响也较为明显。
5.1. x和ε变化对对流换热系数的影响
在注射速度为2.2%时,以POM (M25-44)熔体填充深度为0.420 mm的型腔,测得不同型腔表面粗糙度和熔体流动距离下,熔体与型腔壁面间的对流换热系数如图8所示。
由图8可见,流动距离一定时,随型腔表面粗糙度增大,熔体与型腔壁面间的对流换热系数呈快速增大趋势。例如,在熔体流动距离最小,表面粗糙度值最大时,对流换热系数快速增大到5660 W∙m−2∙K−1。
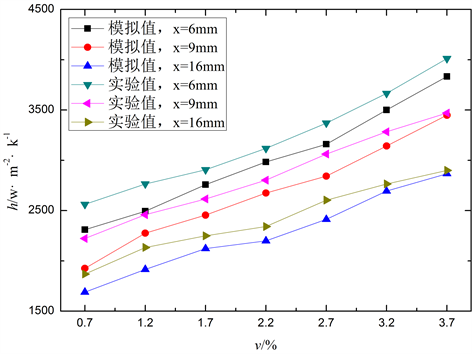
Figure 7. The simulated values and experiment values of HTC at different positions
图7. 不同测量位置的对流换热系数模拟与实验值
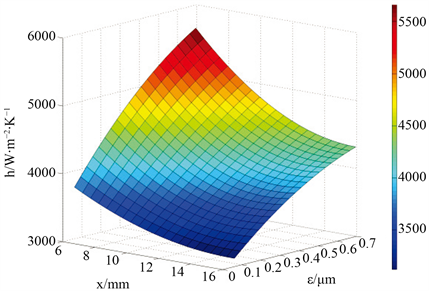
Figure 8. Variation of HTC with x and ε
图8. 对流换热系数随x和ε的变化
但当熔体流动距离与表面粗糙度值都增大时,对流换热系数的变化趋势减缓。例如,当表面粗糙度分别为0.062 μm,0.393 μm和0.695 μm时,随熔体流动距离的增大,对流换热系数的降幅分别为16.97%、21.37%和23.67%。而当熔体流动距离分别为6 mm,9 mm和16 mm时,随表面粗糙度值的增加,对流换热系数的增幅分别为50.53%、36.49%、38.37%。这是由于熔体填充微模具型腔时,对流换热系数随熔体流动距离增大而减小,随型腔表面粗糙度增大而增大,两个变量对对流换热系数起到相反的作用趋势,因此流动距离与型腔表面粗糙度之间存在相互影响的动态竞争关系。
5.2. d和ε变化对对流换热系数的影响
在注射速度为2.2%时,以POM (M25-44)熔体填充不同深度和表面粗糙度型腔的型腔,测得6 mm流动距离处,熔体与型腔壁面间的对流换热系数如图9所示。
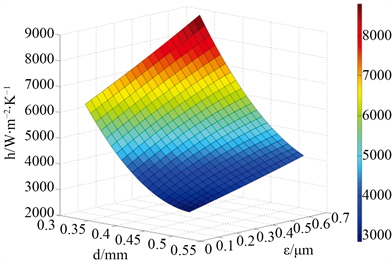
Figure 9. Variation of HTC with d and ε
图9. 对流换热系数随d和ε的变化
由图9可见,型腔表面粗糙度一定时,随型腔深度增加,熔体与型腔壁面间的对流换热系数呈快速下降趋势,尤其在表面粗糙度最小,而型腔深度最大时,对流换热系数迅速下降到最低值2868 W∙m−2∙K−1。当型腔深度和表面粗糙度都增大到最大值时,对流换热系数为4060 W∙m−2∙K−1;比型腔深度最小,表面粗糙度值最大时的对流换热系数减小了4718 W∙m−2∙K−1,其减小的幅度达53.75%。这是由于对流换热系数随型腔深度增大而减小,随型腔表面粗糙度增大而增大,两个变量对对流换热系数起到相反的作用趋势,型腔深度与表面粗糙度之间同样存在相互竞争的影响关系,两者耦合作用的结果会直接影响对流换热系数的变化。
5.3. d和x的变化对对流换热系数的影响
在注射速度为2.2%时,POM (M25-44)熔体填充表面粗糙度为0.062 μm的型腔,测得不同型腔和不同流动距离时,熔体与型腔壁面间的对流换热系数如图10所示。
图10显示,填充距离一定时,增加型腔深度,会使熔体与型腔壁面间的对流换热系数呈快速下降变化趋势,尤其在型腔深度和填充流动距离都增大到最大值时,对流换热系数迅速下降到最小值2135 W∙m−2∙K−1,下降幅度达61.34%。相对于型腔深度最大而熔体流动距离最小时的对流换热系数2868 W∙m−2∙K−1,其下降幅度为25.56%。显然,这是由于对流换热系数随型腔深度和熔体流动距离增大而减小,这两个变量的改变会对对流换热系数起到相同的作用趋势,两者的相互耦合作用,使熔体与型腔壁面间的对流换热系数下降得较为缓慢。
6. 结论
对两种牌号的POM熔体在不同注射速度下,填充不同深度和不同表面粗糙度微模具型腔以及熔体填充距离不同时,微型腔中熔体流动时的对流换热行为研究,可得到以下结论。
1) 同样工艺参数和型腔尺寸条件下,聚合物材料自身的导热系数和比热容等热物性参数越大,成型流动时的对流换热系数越大。
2) 聚合物熔体填充微型腔时,增大型腔表面粗糙度以及减小熔体流动距离均会使熔体与型腔壁面间的对流换热系数增大;而增大注射速度使分子链间产生剪切摩擦热,使熔体与壁面间温度梯度增大,是导致熔体流动时的对流换热行为明显增强的主要因素。
3) 改变微型腔深度,对熔体流动时的对流换热行为影响,比改变型腔表面粗糙度和熔体填充流动距离更为明显,尤其是在型腔深度尺寸较小时。
4) 微型腔的深度、表面粗糙度和熔体填充距离之间的相互耦合作用,对熔体流动时的对流换热系数大小及变化趋势也有明显的影响。
基金项目
感谢国家自然科学基金(NO. 51175060, 51575080)资助课题。