1. 引言
近些年来由于天然陶瓷原料的枯竭,中国已经禁止开采天然黏土用来制备烧结砖 [1]。我国是建筑陶瓷的生产大国和出口大国,产量多年位居世界首位。2015年陶瓷砖产量已超过百亿平方米,2016年达110.76亿平方米,较上年增长1.81% [2]。因此寻找陶瓷天然原料的代替物是近些年来研究的重点领域。我国虽然是资源大国,但是由于我国矿产资源品位较低,因此冶金过程中会产生大量的尾矿和尾渣,但由于处理技术落后,大量的冶金固废未能得到及时和有效的回收处理,而造成土壤、重金属水污染等环保问题 [3] [4]。如果能够将冶金固废利用在建筑陶瓷上,不但能够解决天然资源日益枯竭的问题,还能够为冶金固废提供一条很好的利用途径 [5]。许多研究人员开始将一些二次资源(钢渣、赤泥、尾矿)利用在建筑陶瓷上 [5]。赵、裴、艾等对高钙陶瓷体系的深入研究,提出了新的SiO2-Al2O3-CaO-MgO-Fe2O3系陶瓷,辉石、钙长石作为主晶相 [6] [7]。新的体系可以使用一些劣质陶瓷原料,尤为关键的是冶金渣可以作为资源利用在陶瓷原料中。然而虽然经过了多年的研究,在实验室取得了一些成就,但是目前尚未见到工业化生产的报道。其中一个很重要的原因是,碱性原料在球磨过程中难以解胶 [8]。水分在泥浆制造过程中主要具有使物料粒子均匀分散、溶解电解质,使泥浆具有流动性等作用 [9]。陶瓷产业的高能耗主要体现在排水过程,而其总能耗的80%以上用于干燥和烧成 [10]。因此,泥浆中的水分应在满足工艺要求的前提下越少越好。为了使含碱原料能够解胶,或增加泥浆的含水率或使用减水剂,而这些都将增加能耗增加成本。而冶金渣都具有较高的碱度,这就限制了其在传统陶瓷湿法中的利用。因此将干法路线应用在冶金固废、在陶瓷应用上具有很多优点。
多孔陶瓷是一种经过高温烧成,具有三维立体网络骨架结构的陶瓷体,内部分布着大量三维彼此贯通的孔道 [11]。由于具有透过性高、比表面积大、低密度、低热传导率以及耐高温、耐腐蚀等优点而被应用于过滤分离、工业污水处理、熔融金属过滤、催化剂载体、隔热隔音材料等 [12] [13] [14] ;近年来,多孔陶瓷的应用领域又扩展到航空领域、电子领域、医用材料领域及生物化学领域等。多孔陶瓷的广泛应用已引起了全球材料界的高度重视,并得到了较快的发展。为了得到不同性能的多孔陶瓷,各种制备方法被相继提出,如添加造孔剂法、有机泡沫浸渍法、溶胶凝胶法、热压法、离子交换法等 [15] [16] [17]。
在本文中结合干法造粒技术提出了一种新的多孔陶瓷制备方法:将配好的原料制粉与混合造粒,将原料制备成0.6~0.9 mm的颗粒,再利用颗粒堆积法压制成型,并将成型生坯经过高温烧制,获得多孔陶瓷。进一步通过XRD、SEM、显微分析和物理性能测试,对多孔陶瓷的烧结过程和成孔机理进行了初步探讨。本研究除了为冶金固废提供一种新的利用途径外,还为多孔陶瓷的制备提供了一种新的思路。通过控制孔径的大小还可以进一步将其制备成透水材料或者过滤材料,为固废高值化利用提供一条有效的途径。
2. 实验
2.1. 原料
实验所用全部原料均来自山东地区,其中钢渣来自山东某钢铁厂,铝土矿尾矿、滑石、黏土均来自淄博地区某陶瓷厂。所用到的主要原料成分的XRF (XRF, XRF-1800, Shimadzu, Japan)成份分析见表1,部分原料物相分析见图4。
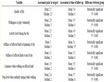
Table 1. Chemical compositions (wt%) of raw materials
表1. 原料的化学成份(wt%)
2.2. 试样制备
试样采用混合造粒工艺与压制烧结工艺进行制备,具体操作步骤见图1:原料烘干后按预设配方称50 kg,将配方置于球磨机中,球磨时间24 h;粉料过200目筛,筛余量小于1%;所得粉料取30 kg放入干法造粒机中喷水进行造粒,总共加入8%~12%左右的水分得陶瓷原料颗粒;通过筛分选择0.6~0.9 mm的颗粒,并阴凉密封陈腐12 h,确保水分均匀;陈腐后的粉料置于磨具中,压制20 × 50 mm长条状试样,置于烘干箱内,烘干至含水量 < 1%。烘干后的试样置于梯度析晶炉(GR1300/13S, Nabertherm, Germany)内进行烧结,升温制度以5℃/min升至最高温度(1100℃、1120℃、1130℃、1140℃和1150℃)并保温0.5 h,10℃/min降至1000℃以下后随炉冷却至室温。
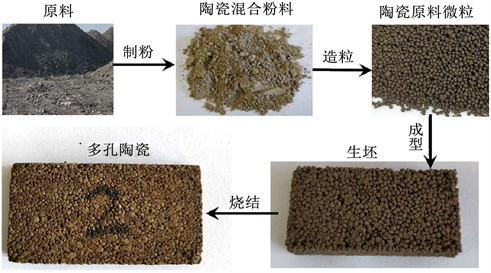
Figure 1. Preparation process for porous ceramic
图1. 多孔陶瓷制备过程
2.3. 材料性能测试
烧结后的试样进行基础性能测试包括收缩率、抗折强度和显气孔率。通过数显游标卡尺测量烧结前后的试样长度
与
,并按照公式(1)进行计算:
1)通过用宁夏机械研究院生产的数显陶瓷砖抗折测试仪(TZS-6000)进行抗折强度测试,并利用数显游标卡尺测量试样的断面高度h、宽度b、支点间距l,并按照公式(2)进行计算:
;2)通过陶瓷吸水率真空装置(CXX-A)对试样进行显气孔率测试。利用精确天平测量吸水前后和水中的试样质量M1,M2与M3,并按照公式(3)进行计算:
;3) 通过X射线衍射和扫描电镜等手段分析样品的物相组成和微观特征,将烧结后的试样干燥粉碎后过200目筛,采用X射线衍射仪(M21X, MAC Science Co. Ltd., Japan)分析陶瓷材料的物相组成,测试方式为:连续扫描,步长为0.02˚,采用Cu靶,扫描速度10˚∙min−1,扫描范围10˚~70˚;对烧结后的试样用金相制样机进行研磨抛光,研磨后的样品置于体积分数为5%的HF中腐蚀90 s,腐蚀后立即将样品放入超声波清洗仪中清洗60 s,清洗介质为蒸馏水,清洗完毕后置于105℃恒温干燥箱中干燥;对样品观察表面喷Au以使其导电,随后进行扫描电镜测试试(MLA-250, Carl Zeiss, Germany)。
3. 结果与分析
3.1. 样品的物理性能
样品的抗折强度和显气孔率如图2所示。从图2中可以看到随着温度的升高抗折强度显著升高,同时随着温度升高显气孔率随之降低。在烧结温度为1100℃时样品的抗折强度只有0.72 MPa,当烧结温度提高到1120℃时,样品的抗折强度缓慢提高,此时抗折强度为2.81 MPa。当烧结温度升高到1130℃时,此时抗折明显提高,达到了9.73 MPa;当烧结温度继续提高样品的抗折强度增速下降,在烧结温度为1140℃和1150℃时抗折强度分别为12.86 MPa和13.67 MPa。相反的样品的显气孔率随着温度的升高而降低。当烧结温度为1100℃时样品的显气孔率为28.89%,当烧结温度升高到1120℃时样品的显气孔率降低到25.54%。当烧结温度为1130℃时样品的显气孔率明显下降此时的显气孔率为21.48%,当烧结温度升高到1140℃时显气孔率吧略微有所降低此时的显气孔率为21.14%。当烧结温度提高到1150℃时显气孔率再次剧烈下降此时的显气孔率为11.97%。
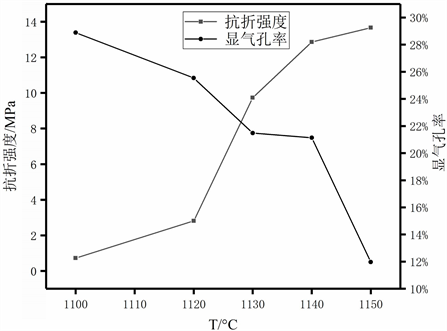
Figure 2. Bending strength and apparent porosity of samples sintered at different temperatures
图2. 样品的抗折强度和显气孔率
从图3中能够明显看到样品在不同温度下收缩率的变化情况,当烧结温度为1100℃时样品的收缩率为9.95%,随着烧结温度的提高样品的收缩率继续增加,当烧结温度为1120℃和1130℃时样品的收缩率分别为10.39%和10.64%。当烧结温度继续升高样品的收缩率增速降低,烧结温度为1140℃和1150℃时样品的收缩率分别为10.82%和10.97%。从图中可以看出随着温度的升高样品的收缩率增加但是其增速放缓。收缩率的增加提高了样品的致密化程度,这也是影响多孔陶瓷显气孔率的另一个重要的因素。
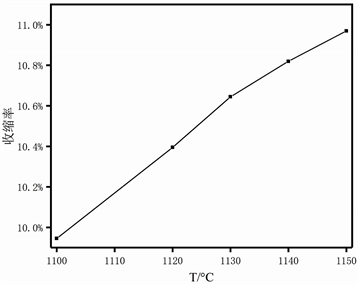
Figure 3. Linear shrinkage of porous ceramics sintered at different temperatures
图3. 不同温度下样品的收缩率
3.2. 样品的矿相转变分析
对图4(a)、(b)显示了主要原料的物相,其中铝土矿尾矿的主要物相有石英(SiO2)、白云母(KAl3Si3O10(OH)2)、赤铁矿(Fe2O3)和一些黏土矿物,如:伊利石((K,H3O)Al2Si3AlO10(OH)2)还有高岭土(Al2(Si2O5)(OH)4)。钢渣则由硅酸二钙(Ca2SiO4)、RO相(MgO,FeO)、f-CaO和黑钙铁矿(Ca2Fe2O5)组成。从图4(c)中可以看到样品不同温度烧结后的XRD图谱,当烧结温度为1100℃时,样品的晶相主要有石英(SiO2)、钙长石(Ca,Na)(Si,Al)4O8、钠长石(Na,Ca)(Si,Al)4O8、辉石(Ca(Mg,Fe)Si2O6)、赤铁矿(Fe2O3)。将样品烧结温度为1130℃时与烧结温度1100℃对比可以明显的看到石英特征峰降低,辉石、钙长石特征峰升高,辉石特征峰有着显著的增加。同时在14˚附近的钠长石峰消失,这可能是因为其转化为了钙长石,33˚附近的赤铁矿峰有着略微的增加,这可能是因为钢渣的RO相分解而导致的。
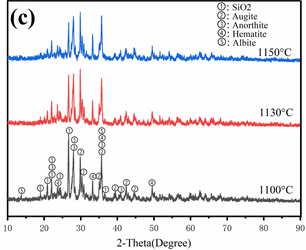
Figure 4. XRD patterns of simples: (a) bauxite tailings, (b) steel slag, and (c) porous ceramics sintered at different temperatures
图4. 样品的XRD图谱,(a)铝土矿尾矿,(b)钢渣,(c)不同温度的多孔陶瓷
3.3. 样品的显微形貌分析
从图5中可以到样品在1100℃~1120℃时样品表面粗糙颗粒之间没有明显粘结现象。当温度升高到1130℃时样品表面开始出现光滑的瓷化现象,同时颗粒之间开始粘结。随着烧结温度的继续升高瓷化现象开始显著,颗粒之间的粘结性增大,所以样品的整体强度有着显著的提高。当烧结温度升高到1150℃时,此时样品的瓷化效果显著,但是由于产生了过量的液相,其扩散能力增强,除了将较小的气孔排除而粘结颗粒外,还进一步堵塞了颗粒之间更大的孔隙,这导致了样品显气孔率的降低。因此,随着烧结温度的提高,样品的收缩率提高和与之相应的陶瓷原料颗粒更大孔隙进一步被填充,是样品显气孔率降低的重要因素。
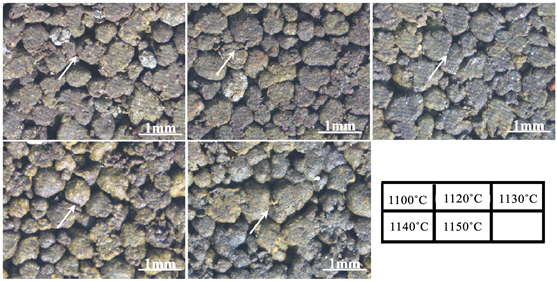
Figure 5. Metallographic microscope images of sample sintered at different temperatures with 25× magnification
图5. 25×放大倍数样品不同温度下的显微镜形貌图
从图6中可以看出在1100℃的时候颗粒之间贴合在一起,但是没有粘结的现象,而在1130℃时可以明显的看出烧结反应后的结果,使得颗粒之间紧密的粘结成为一个整体。这也正好对应图5中现象,在1100℃时只有极少数的颗粒相互粘结所以此时的强度较低,而当温度升高到1130℃时随着反应程度的加大颗粒之间粘结作用显著提高,所以1120℃~1130℃时抗折强度增长率最大。
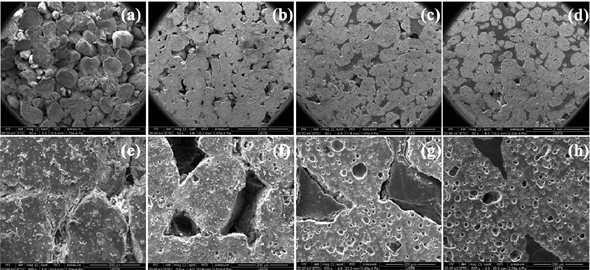
Figure 6. SEM images of samples with different magnification and different sintering temperatures, 50×, (a) 1100, (b) 1130, (c) 1140, (d) 1150; 500×, (e)1100, (f) 1130, (g) 1140, (h) 1150
图6. 样品不同放大倍数不同温度下的SEM形貌图,50×,(a) 1100,(b) 1130,(c) 1140,(d) 1150;500×,(e) 1100,(f) 1130,(g) 1140,(h) 1150
由图3可知,1130℃至1150℃区间样品的收缩率增加值小于1120℃和1130℃时样品的收缩率增加值,这与图5和图6的烧结过程变化规律一致,即在1100℃~1130℃期间是颗粒致密化最显著的区间,此区间内的较小细孔都因为致密化过程而被离子扩散填充,因此形成了多个颗粒之间的粘接。随着温度进一步升高,虽然离子扩散能力增强,但是前期致密化过程已经排除了大量的微小气孔,此时排除的气孔主要是因扩散能力提高而增加的更大一些的气孔,其数量小于原来所有的更小的气孔,其收缩率增加值因此有所下降。
结合图4可知,随着温度的升高,辉石、钙长石增加逐渐成为主晶相,颗粒之间通过进一步反应粘结成为一个整体,从而提高多孔陶瓷的整体强度。
图7显示了多孔陶瓷及其成孔方式。综合以上分析可知,在本实验中三维贯通孔洞的形成主要是通过生坯制备过程中陶瓷原料颗粒不完全贴合而形成的较大空隙。随着温度的升高,颗粒表面反应生成玻璃相将颗粒中形成的较小微气孔排除而相互粘结,使得多孔陶瓷整体上具有一定的强度;而未能排除的较大孔隙测保留形成了多孔通道。
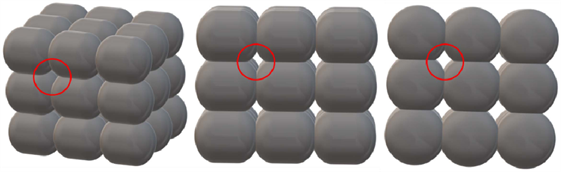
Figure 7. Model of porous ceramic green body
图7. 多孔陶瓷生坯模型图
4. 结论
以转炉钢渣、铝土矿尾矿为主要原料,采用混合造粒方式制备了陶瓷原料颗粒,进一步经压制和烧结制备出了多孔陶瓷材料。陶瓷生坯制备过程中,其颗粒原料不完全贴合而形成大小不一的空隙。烧结温度的升高有利于陶瓷中辉石、钙长石和液相的形成,促进了材料的致密化,使得形成较小孔隙的颗粒之间发生连接,导致了多孔陶瓷显气孔率降低和抗折强度升高;同时,而未能排除的较大孔隙则保留形成了三维多孔贯通结构。当烧结温度继续升高,液相增多,更大孔隙的陶粒颗粒之间连接和致密化,其抗折强度继续升高,但是由于过量的液相堵塞了颗粒之间的孔隙,导致了其显气孔率的显著降低。合适的烧结温度是制备钢渣多孔陶瓷的关键。本实验条件下,当烧结温度为1140℃时,样品表现出了优秀的力学性能(抗折强度12.86 MPa)和显气孔率(21.48%)。本研究为多孔陶瓷的制备提供了一种新的思路,并且为固废高值化利用提供一条有效的途径。
致谢
感谢国家重点研发计划资助(课题编号:2016YFB0601304)。