1. 引言
危险化学品企业储存成本比普通货物高昂这已经是行业内的共识,其中乙类化学危险品仓库的租赁价格甚至是普通的几倍。这一部分的原因是化学危险品对物理储存条件要求非常高,特别是在安全、环保这两方面,这就使得仓库的使用条件更加严格和苛刻;另一部分的原因出在处理呆滞库存成本上面,由于是化学危险品的呆滞库存,这就必需专业的具备相应资质的处理公司接手,并且一定要在当地环保部门的全面监控下完成,这就使得成本进一步的增加了,有些处理费用甚至超过了采购价格的20%。由此可见,库存控制方法的探讨对化学危险品企业具有十分重要的借鉴及实践意义。
据统计,全球范围内每年生产的化学危险品约有40亿,危化品在生产、运输、储存、消耗过程中,存在着很大的安全隐患,一旦发生危险事故,将会对社会、经济、环境带来不可磨灭的影响。在存储方面,由于危险品的特性,其存储成本和要求比普通货物的要求高得多,尤其是在安全方面。因此制定出符合危险品特性的库存管理方法对危险品企业有着重要的实际意义。然而,国内目前对危险化学品库存优化问题的研究很少,大多都是定性的分析,很少有人针对危险化学品的库存控制提出定量的模型。本文设计了一种考虑包括风险成本和过期处理成本在内的总成本的化学危险品库存控制模型。
2. 文献综述
从经济订货批量模型被提出以来,随着应用的深入,人们考虑了更多周围环境变化所产生的影响,扩充了多种类的库存控制模型。Hadley和Whitin等人假设了供应商为刺激消费者需求,对产品采取价格折扣的策略,以此建立了具有价格折扣的EOQ模型。Crowther第一次从供应商和零售商双方角度出发,分析了一种批量购买时享受价格折扣的订货模型,从而使供应商的利益最大化的同时降低零售商的成本。Banerjee则考虑了两级供应链下的库存控制策略,以供需双方的库存费用最小为目标建立数学模型,并且具体分析了产品售价与订购量对库存成本的影响。陈宪章建立了季节性需求、变化生产率最优生产存储库存策略。研究发现,在不允许缺货的条件下,为满足季节性需求,单纯追求提前存储或增加机器数量,均不一定能够取得最佳效益,要根据存储费用和启动费用以及生产周期共同确定。在有限生产率的条件下,得出一种寻求最优生产–库存策略,为此类库存系统的管理决策提供了理论依据 [1]。施文武等建立了一种多周期随机需求生产/库存模型。该模型采用(s,Q)策略,设计了一种最优生产控制算法,根据该算法可以得出系统的最优生产准备点和最优生产量。并计算验证该方法可以有效地减小系统生产和库存的平均费用 [2]。王小斌讨论了含模糊参数的不确定环境下的经济订购批量问题与经济生产批量问题,运用可信性理论、不确定过程理论以及数学规划理论,分别建立了这些不确定库存问题的数学模型,并设计了相应的算法进行求解。张广霞通过联合库存在供应链库存控制中应用的研究,找出联合库存管理法在供应链库存控制中的应用对策,为实现供应链的同步化运作、零库存、准时化采购以及精细供应链管理提供条件和保证 [3]。张广霞通过联合库存在供应链库存控制中应用的研究,找出联合库存管理法在供应链库存控制中的应用对策,为实现供应链的同步化运作、零库存、准时化采购以及精细供应链管理提供条件和保证 [4]。蒋志明等将随机提前期作为变量,建立了一种基于随机提前期的(Q,R)模型,并用实例进行验 [5]。
目前针对危险化学品的研究集中在运输管理、安全风险评估、成本构成与管理等方面,而对危险化学品库存优化问题的研究很少,大多都是定性的分析。例如,王练以深圳的危险品库的库存管理为例,提出了一些危险化学品存储的建议 [6]。柴保身具体描述了我国危险化学品仓储业发展现状与展望 [7]。蔡翔根据危化品的特性,采用分库、分类、分区储存养护的办法对危险化学品进行库存管理,从而将风险降到最低 [8]。韩学飞将危害分析与关键控制点方法的预防性管理思想应用在危险品的仓储管理中,研究在危险品仓储过程中可能发生的危害,提出可行性的危害控制方法,对此方法在未来的发展方向进行了展望 [9]。刘立祥以唐山市危险品库存管理为例,给出了一些针对性的措施和建议 [10]。这些研究都是从危险化学品的特性出发定性的进行分析,得出库存管理策略。很少有将危化品的特性进行分析量化后加入库存模型中进行分析的,而准确的模型往往在现实生活更具有指导意义。本文将危险品的事故风险成本加入到库存总成本中,以库存总成本最小化为目标,建立库存控制模型,对库存控制进行了定量计算,求得最优订货量。
3. 数学建模
本文在(Q,R)模型中加入风险成本和过期处理成本,求解使得包括风险成本和过期处理成本在内的库存总成本最小的订货批量、再订购点和安全库存。我们考虑连续盘点策略,对企业的现有库存量进行连续盘点,一旦发现库存量到达或低于再订货点R,立刻实施补货策略,补货量为Q,以保证生产的连续。本模型以订货量Q和再订购点R作为决策变量,目标函数是最小化库存总成本。
3.1. 模型假设
1) 单位时间需求量服从正态分布。
2) 每次补完货的库存水平总是高于再订货点R,也就是一个提前期内只会订一次货,同时也保证了连续订货,并且不会发生交叉订货。
3.2. 模型符号意义
Q:订购量
v:单位危化品的价值
:单位时间平均需求均值
:单位时间需求标准差
L:提前期
:提前期内需求均值,
:提前期内需求标准差,
x:提前期内的需求量
:提前期内需求量概率密度函数
:提前期内需求量概率分布函数
:单位时间内危化品发生事故的概率
:每件危化品单位时间存储费
:每次补货订购成本
:单位时间单位危化品缺货成本
:单位危化品风险成本
:单位产品过期危化品的处理费用
3.3. 模型建立
1) 存储成本HC
由以上符号可得安全库存为:
(1)
则平均存储量为:
(2)
得单位时间存储成本为:
(3)
2) 订货成本OC
单位时间订货次数(周期数)为
,可得单位时间订货成本为:
(4)
3) 缺货成本VC
如果D1为提前期的需求量,则提前期内的缺货量为
,由此可得一个周期内的期望缺货量为:
(5)
则单位时间的缺货成本为:
(6)
4) 风险成本RC
(7)
5) 过期危化品处理成本MC
危化品一旦过期只能作销毁处理,企业不但要承担由于过期所带来的损失,还要支付相应的处理费用。
(8)
6) 单位时间平均库存总成本
由以上计算步骤,可得年平均库存总成本为:
(9)
7) 再订购点,订货批量和安全库存
对(8)中的Q和R分别求一阶偏导并令其等于0得:
(10)
(11)
对(9)和(10)交替迭代求解可得最优订货批量
、再订购点
,步骤如下:
① 在式(9)中令
作为初始解,求解得
;
② 将
的值代入式(10),求解得
;
③ 将
的值代入式(5)计算
;
④ 再将
的值代入式(9)求得
;
⑤ 重复②~④步,直到
和
的值基本上不再有较大的变化为止;此时的
,
即为最优解
,
。
再由
可得到安全库存为:
(12)
4. 算例验证
本小节给出一个具体实例验证上述模型和求解算法的有效性。
已知某公司危险品每月需求量服从均值等于30,923,标准差等于6918的正态分布。此条件满足(Q,R)模型假设。已知订货提前期L平均为7.5天,即0.25个月,单位危化品的价值v为68元;单位危化品每月储存费为2元,单位危化品缺货费为10元,每次订货费为500元,单位危化品发生事故后造成的损失为3000元;单位时间内危化品发生事故的概率为0.0005;单位过期危化品的处理费用为5元。
因为该产品每月需求量的均值
,标准差
,
,所以,提前期内需求量服从均值
,标准差
的正态分布。
计算过程如表1所示。
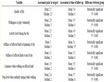
Table 1. Process of iterative calculation of B ( R i ) , Q i , R i
表1.
迭代计算过程
Continued
由上表我们得到最优订货量
,最优再订购点
,安全库存
。
5. 灵敏度分析
通过Matlab数值计算对模型中各个参数(
、
、
、
、
)进行灵敏度分析,得到了每个参数在选取不同值时库存总成本TC的变化情况,结果如下。
5.1. 存储费CH的灵敏度分析
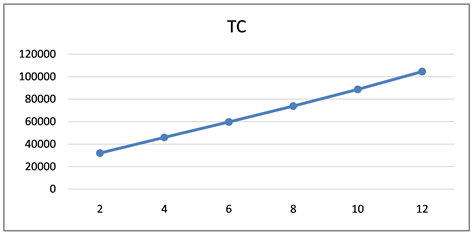
Figure 1. Sensitivity curve of total inventory cost to CH
图1. 存储费CH灵敏度曲线
图1中的曲线揭示了不同存储费CH对应的库存总费用TC。从图中我们可以看出,单位产品存储费增加时,库存总成本随之增加。且存储费增加时,企业更愿意进行小批量订货,再订购点和安全库存水平也会设置为更低水平。由于危险化学品本身的特性,其存储费会比普通货物高得多,所以企业可以通过控制平均库存量在一个较低的水平来降低库存成本。
5.2. 缺货成本CV的灵敏度分析
由图2可知,单位产品的缺货成本增加时,库存总成本随之增大,且缺货成本增加时,企业会设置较高的再订购点和安全库存水平以期降低因缺货给企业带来的损失。
5.3. 订购费CO的灵敏度分析
由图3可知,当订购费CO增加时,库存总费用随之增大。且当每次的订购费用较大时,企业不愿频繁订货,并会将再订购点和安全库存水平设置较低水平。
5.4. 风险损失Cr的灵敏度分
由图4可知,随着单位原材料风险损失Cr的增加,库存总费用相应增加。且风险损失增加时,企业更愿意订购较少的批量并设置较低的再订购点和安全库存水平。
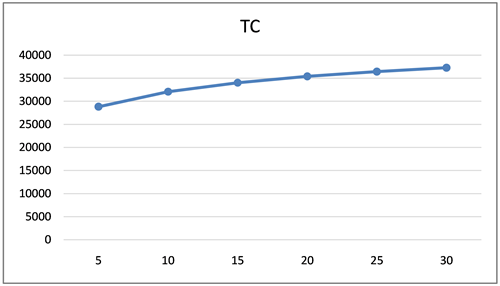
Figure 2. Sensitivity curve of total inventory cost to CV
图2. 缺货成本CV灵敏度曲线
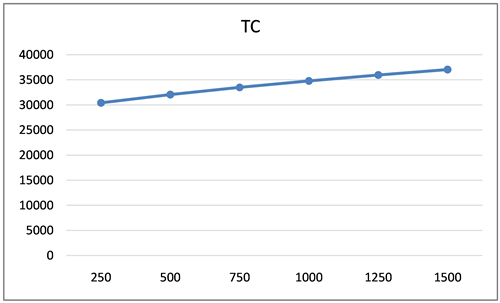
Figure 3. Sensitivity curve of total inventory cost to CO
图3. 订购费CO的灵敏度曲线
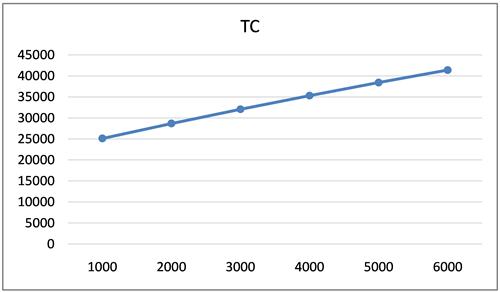
Figure 4. Sensitivity curve of total inventory cost to Cr
图4. 风险损失Cr的灵敏度曲线
5.5. 发生事故概率Pr的灵敏度分析

Figure 5. Sensitivity curve of total inventory cost to Pr
图5. 发生事故概率Pr的灵敏度曲线
由图5可知,当危险事故发生的概率Pr逐渐增大时,库存总费用随之增大。且发生事故的概率越大,企业为尽可能降低发生危险事故时的经济损失,会降低订购量并保持较低的安全库存水平。
5.6. 单位过期危化品处理费用Cm的敏感度分析
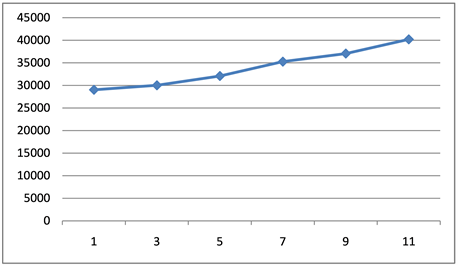
Figure 6. Sensitivity curve of total inventory cost to Cm
图6. 单位过期危化品处理费用Cm的灵敏度曲线
由图6可知,当单位过期危化品处理费用Cm逐渐增大时,库存总费用随之增大。
5.7. 比较得出最为敏感的参数
下面我们把不同参数的单位变化导致的库存总费用的平均变化率进行比较,得出相对敏感的参数。
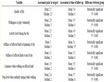
Table 2. Average change rate of total inventory cost caused by unit changing of parameters
表2. 不同参数单位变化导致库存总成本变化率
由上表2我们可以看出,随着参数Pr的变化,库存总成本TC的变化率最大,即发生事故的概率Pr是相比之下最为敏感的参数。因此Pr对企业的库存费用的控制至关重要,企业应关注产品的仓储管理以降低危险事故发生概率,从而降低库存总成本。
6. 结论与展望
相比于一般物资,化学危险品对储存环境、安全以及环保等多方面的诸多要求,导致化学危险品库存持有成本很高。另外,报废化学危险品的处理程序复杂、费用可观,高效的库存管理体系对化学危险品企业以及整个社会均有着重要的经济意义、社会意义和环境意义。危险化学品的事故风险成本和过期处理成本是与其他库存控制策略相区别的重要方面,是在进行库存优化过程中必须考虑的成本,本文设计的库存控制模型加入其相关内容,建立了更加符合化学品特性的库存控制模型,并带入数值进行验证,证明了模型的实用性。关于如何合理评估危险品库存的事故风险,将是今后研究的重点问题。