1. 引言
白车身的模态分布是车辆NVH性能的重要指标,不合理的模态分布使整车易产生共振,造成各种NVH问题,且不易解决,因此白车身的模态测试工作已成为车辆开发中的必要工作之一 [1] [2] [3] 。试验模态分析的结果不仅可以与有限元分析结果进行对比修正,也可以迅速得到白车身的实际模态振型,用以检验和改进白车身的结构性能,必要时也可以利用白车身试验模态分析进行后续的分析,从而为汽车结构的优化设计提供有效而实用的信息 [4] 。对于汽车白车身而言,不同的连接技术和连接结构不可避免地会对汽车白车身的模态产生影响。
胶接技术是一种利用胶粘剂在连接面上产生的机械结合力、物理吸附力和化学键合力而使两个胶接件联接起来的工艺方法。与其他连接方式相比,胶接技术在应力分布、腐蚀性能、疲劳性能等方面具有极大的优势 [5] [6] [7] [8] 。因此,胶接技术广泛应用于汽车、航空、建筑等行业 [9] 。
传统汽车上通常采用点焊技术作为主要的车身连接技术。为了验证胶接技术在取代点焊技术应用于车身后对整车模态和性能的影响,本文对采用不同连接方式的白车身进行了模态试验与分析。
2. 试验方案
涂胶位置的确定
轿车白车身金属部件间最常采用的连接方式是点焊连接,通常每辆车身上的焊点有3000个左右,如果采用点焊 + 结构胶粘接的工艺则可以显著减少焊点数量。结构胶在汽车车身上的典型涂布位置如图1所示。本章主要对胶接白车身和传统的焊接白车身的模态进行对比,根据实际需求对涂胶位置进行了确定。
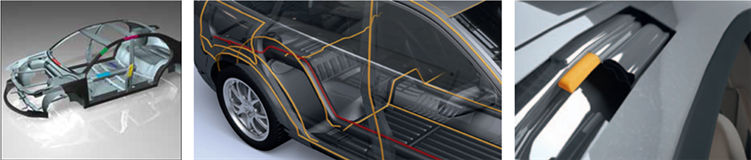
Figure 1. Typical application position of structural adhesive on automobile body
图1. 结构胶在汽车车身上的典型应用位置
车身上受空间局限而无法进行点焊施工的钢板焊缝区域,可以用结构胶粘接取代焊接。这些区域包括地板、车顶翻边处的粘接以及立柱、侧围和内增强板翻边处的粘接等。
本文基于上汽通用五菱宝骏某SUV车型的白车身进行模态研究。主要考虑的几个因素为:不便于施加焊点的位置、非重要承力位置和需要改善外观的位置。根据这些原则,大致确定了涂布结构胶的部分位置。本研究采用的胶粘剂为回天7130高温固化(170℃ × 20 min)结构胶,涂胶厚度为0.2 mm,宽度为13 mm。
在后侧围内焊合件的非主要承力位置进行结构胶的涂布,后围侧板焊合件处结构胶主要分布在以下区域:1) 后侧围内板与加强板之间以及后侧围内板与上边梁加强板之间;2) D柱下加强板与D柱下内板之间;3) 后侧围内板与后侧围上三角板之间;4) 后侧围内板与D柱下内板之间,以及后轮罩内板和后轮罩前连接板上;5) 后侧围上三角板与D柱上加强板之间,以及涂于D柱上加强板与上边梁加强板之间。后侧围内焊合件的结构胶涂布如图2所示。
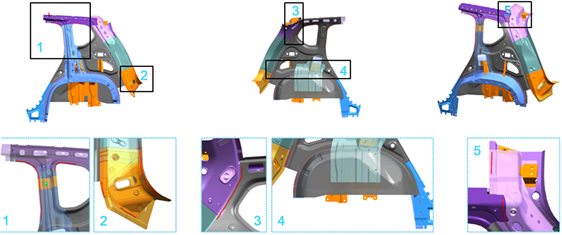
Figure 2. Coating position of structural adhesive on welded part of rearwall sidecover
图2. 后侧围内焊合件结构胶涂布位置
在侧围、A/B柱加强板等位置不便于焊接、需要缓解应力集中问题和非主要承力部位进行了结构胶的涂布,侧围、A/B柱加强板等位置结构胶分布主要包括:1) B柱内板和B柱加强板之间、上边梁内板和上边梁加强板之间;2) B柱内板与B柱加强板之间;3) A柱上内板与A柱上加强板之间;4) 后轮罩外板与中门槛外板之间;5) D柱上外板与后侧围上三角板之间。侧围、A/B柱加强板等位置结构胶分布如图3所示。
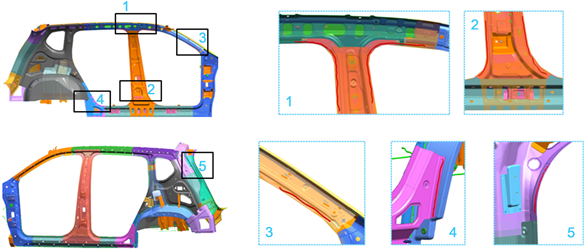
Figure 3. Coating position of structural adhesive on car body side and A/B pillar reinforcement plate
图3. 侧围、A/B柱加强板等位置结构胶涂布位置
在前围板、前大梁、前横梁等位置不便于焊接、需要缓解应力集中问题和非主要承力部位进行了结构胶的涂布,前围板、前大梁、前横梁等位置结构胶的具体涂布位置主要包括:1) 在放置前围板上安装板总成之前,涂在前围板上、前围板上横梁上以及前轮罩外板上;2) 前大梁总成与前轮罩总成之间,结构胶涂在前大梁A封板、前轮罩板前板上;3) 前围板前横梁总成与前围板之间、前围板上横梁与前围板之间、前轮罩板与前围板之间。前围板、前大梁、前横梁等位置结构胶的具体涂布位置如图4所示。
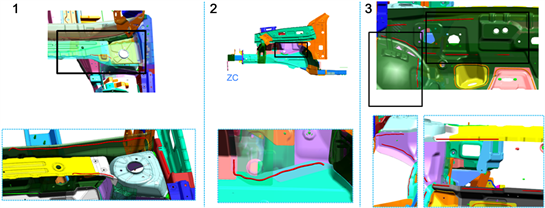
Figure 4. Coating position of structural adhesive on dash panel, boom and front beam
图4. 前围板、前大梁、前横梁等位置结构胶涂布位置
除了以上部位为结构胶在白车身上的主要涂布位置外,还在其他部位进行了结构胶的涂布,主要包括后地板与后车架的部分位置。前侧门与门槛的部分位置、尾端板的部分位置等,具体的涂胶位置包括:1) 在后地板与后车架分拼前,在车架的图示位置涂胶;2) 涂于前侧板焊接边上、前侧板上与A柱下加强板焊接边的位置、后大梁及后轮罩加强板上、门槛内板的下焊接边、安全带加强板上、门槛内板的上焊接边;3) 在放置后端板总成前,在尾端板总成图示位置涂结构胶,涂于后端上板总成以及后端下板上。后地板与后车架、前侧门与门槛、尾端板的涂胶位置如图5所示。
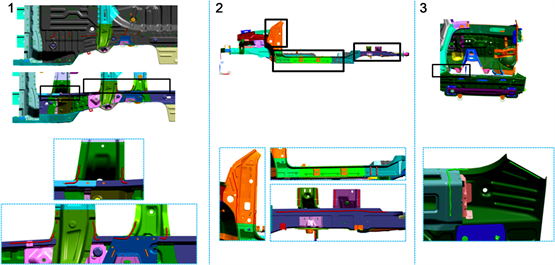
Figure 5. Coating position of structural adhesive onrear floor, rear frame, front side door, doorsill and transom piece
图5. 后地板与后车架、前侧门与门槛、尾端板的涂胶位置
在上述位置涂布结构胶后,采用关键点焊接或夹具夹紧的方式对胶接部位进行加压固定,随后进行固化及测试。
3. 白车身模态试验
本文针对上汽通用五菱宝骏某SUV车型采用了三种不同的连接方案,编号分别为1#,2#和3#。其中,1#为采用点焊连接技术进行连接的传统白车身,2#为采用结构胶替代部分焊点后的车身,3#在2#号的基础上,在D柱上、下腔体里增加塑料增强骨架,左右对称。
白车身模态分析的流程如图6所示,主要包括模型建立、试验准备、白车身的安装与传感器的布置、加载与数据采集、数据处理及结果评价等几个步骤。
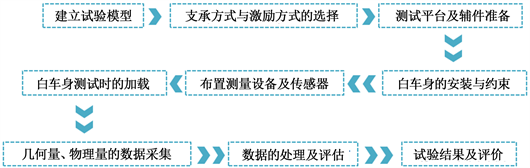
Figure 6. Modal test analysis process of white body
图6. 白车身试验模态分析流程
按照以上步骤进行对比测试的白车身为1#的原始状态点焊白车身及2#胶接白车身,以对原始状态点焊白车身和胶接白车身的性能差异进行对比与分析。
在模态测试中,汽车白车身的悬挂方式采用前麦弗逊后扭梁的悬挂方式,激励点的选取如图7所示。本文共选取了两个激励点,用激振器对白车身进行激励,分别在白车身的右前纵梁和后车架位置。激振器可以识别来自功率放大器的信号并将激振信号转化为相应特征的激振力传递给被测试的构件。
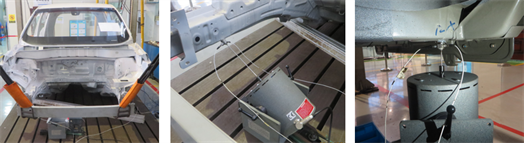
Figure 7. Position of excitation point in modal test of automobile white body
图7. 汽车白车身试验模态测试中的激振点位置
4. 白车身模态试验结果分析
本文对三种白车身进行了前五阶的模态试验,得到了采用不同的连接方式的汽车白车身的振型结果,如图8~12所示。
图8为一阶模态测试结果,三种白车身的振型均变为顶盖前横梁弯曲,其中2#白车身顶盖横梁弯曲位移最大,3#次之,1#最小,说明胶接车身相比于点焊车身刚度有所不足。
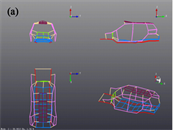
Figure 8. First-order vibration mode of white body: (a) 1#; (b) 2#; (c) 3#
图8. 白车身一阶振型:(a) 1#;(b) 2#;(c) 3#
图9为二阶模态测试结果,三种白车身的振型均变为尾门框菱形变形,可以发现2#白车身尾门变形与1#相近,说明胶接车身在尾门框局部刚度与点焊车身相近,而3#白车身变形最小,是因为增加了塑料骨架,加强了白车身尾门局部区域的刚度。
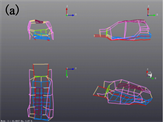
Figure 9. Second-order vibration mode of white body: (a) 1#; (b) 2#; (c) 3#
图9. 白车身二阶振型:(a) 1#;(b) 2#;(c) 3#
图10为三阶模态测试结果,三种白车身的振型均表现为呼吸模态,同时顶盖发生弯曲,其中2#白车身顶盖弯曲模式与1#相近,表现为前部和中后部向下变形,而3#白车身顶盖弯曲变为后部向上变形,且变形程度大于前两者。
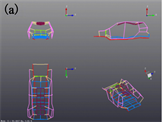
Figure 10. Third-order vibration mode of white body: (a) 1#; (b) 2#; (c) 3#
图10. 白车身三阶振型:(a) 1#;(b) 2#;(c) 3#
图11为四阶模态测试结果,三种白车身的振型变现为整车扭转与前舱横摆模态的复合振型,前舱横摆的变形从1#、2#、3#白车身依次增大。
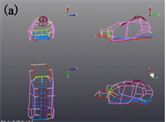
Figure 11. Fourth-order vibration mode of white body: (a) 1#; (b) 2#; (c) 3#
图11. 白车身四阶振型:(a) 1#;(b) 2#;(c) 3#
图12为五阶模态测试结果,三种白车身的振型变现为一阶弯曲,其中2#白车身和3#弯曲模式相近,表现为典型的一阶弯曲振型;而1#白车身变形很小,其刚度可能存在过设计。
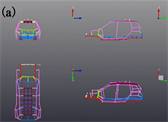
Figure 12. Fifth-order vibration mode of white body: (a) 1#; (b) 2#; (c) 3#
图12. 白车身五阶振型:(a) 1#;(b) 2#;(c) 3#
为了进一步定量比较三种连接方式的白车身性能,表1给出了三种白车身前五阶模态测试的频率和阻尼比。
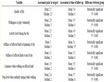
Table 1. Results of automobile white body modal test
表1. 汽车白车身试验模态测试结果
通过对模态振型综合比对可以发现,增加结构胶可以提高一阶至五阶模态频率的值。这是由于增加结构胶方案导致的白车身重量增加有限,但是对白车身刚度提升较大,因此导致模态升高。观察前五阶模态测试结果,可以发现胶接白车身阻尼比具有较明显的优势,相较于点焊车身阻尼比最大提高了2倍(第五阶模态),因此胶接车身在吸收减震方面具有较好的优势。
5. 结论
1) 在白车身的模态振型中,出现了几种复杂的振型,如白车身在整车呼吸模态的同时出现了顶盖的弯曲,整车出现呼吸模态的同时顶盖处的局部还存在模态振型,因此在该区域需要进行优化。
2) 白车身模态分析中,需要考量白车身的模态频率是否与外界激励源有差距,频率需要错开以避免产生结构共振。另外还需要考量车身整体和局部结构设计和强度是否能满足要求。
3)采用局部增加结构胶的方案可以使白车身固有频率提升1 Hz~3 Hz左右。
致谢
本课题由国家自然科学基金(51505139)支持。作者感谢上汽通用五菱汽车股份有限公司和湖南大学汽车车身先进设计制造国家重点实验室。
NOTES
*通讯作者。