1. 引言
2018年,我国长征系列运载火箭共进行37次发射。航天发动机电磁阀作为增压输送系统的重要组成既具有多品种、变批量等生产任务的特点,又要满足高强度发射的要求。因此仅仅依靠增加人员、加班加点等传统提高产能的方式,只能短期内小幅度地提高生产交付能力,无法长期满足大幅增加的任务形势需求。简单的扩大生产规模提高产能的方式,又受限于硬件资源、人员培训、成本控制等因素,无法实施。因此,必须使用先进的制造模式,在制造模式层面开展研究与实践,挖掘潜力,提升能力。按照产品特点和生产现状,选择产品种类数量多、生产周期长、制约生产进度的电磁阀阀体,采用单元化生产模式。
单元化制造系统 [1] 是针对中小批量制造、订单驱动和非稳定不平衡制造环境下的一种制造管理方式,其管理与控制的目标是通过对物料、人力、设备等生产资源的合理计划、调度与控制,缩短制造周期,减少在制品,降低库存,提高生产资源的利用率,最终达到提高生产率的目的。目前,单元化制造系统研究的关键技术 [2] [3] [4] 已经基本突破,完成了单元化对单元要运行产品的生产特点的分析,建立工艺布局,进行生产组织,然后注意进行工艺管理、物流管理、人员管理、设备管理,并制定有效的质量控制措施。
2. 电磁阀阀体的产品特点
在液体航天发动机中,电磁阀控制推进剂或控制气体进入推力室和燃气发生器和其他部件,关闭时切断推进剂或控制气体的供应,其阀体的精度影响着可靠性,响应时间,电磁阀的阀体毛坯一般由两端为磁性材料,中间为隔磁材料焊接而成。因此阀体的用量大、工艺复杂、材料难加工、制造周期长。
2.1. 阀体材料分析
对目前在制生产的几十种电磁阀阀体进行了分析。阀体毛坯由端头、法兰盘、隔磁环三种零件焊接而成见图1。从材料上分析,阀体主要由表1材料组成。各种阀体的材料组成相似,切削性相似。
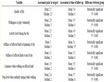
Table 1. Material composition of valve
表1. 阀体材料组成
2.2. 阀体结构分析
从结构上分析,阀体结构主要为入口接嘴、中间为绕线窗口和引线槽、后一段为对外接口(法兰或接嘴)和内部装阀芯、挡铁的、阀座的密封和电磁响应部分,精度要求为μm级。如图2所示。
另外,阀体有一个特点,三类阀体结构虽然不同,但是使用的设备基本相同。各类阀体的各个型号的阀体除尺寸有所变化外结构基本相同,这使得电磁阀阀体制造单元不受某一具体型号限制,覆盖面更加广泛,任务量更加饱满。
2.3. 阀体工艺流程分析
在电磁阀最初研制时,我厂几乎没有数控车床、数控铣床及加工中心,电磁阀阀体原加工工艺以普通车床和铣床为主要设备,由于受机床的装刀数和加工能力所限,每个机床只能完成部分尺寸加工工作,产品需要在不同的设备间多次流转,频繁变换设备、更换工装,造成产品加工工艺流程长。在单元内加工,需要对产品加工工艺流程进行调整和优化,其原则是:使每一个工序和其他工序能够实现同步化流动生产。即实现“一个流”生产作业。优化后流程如图3。

Figure 3. Flow diagram of simple valve
图3. 简单型阀体加工流程
经过对阀体的流程分析,阀体流程基本可以满足工序的流水节拍,能实现“一个流”的生产。
3. 建立电磁阀阀体制造单元
3.1. 设备布局
设备布局考虑时要基于产品的加工工艺流程,实现高效生产,同时要综合考虑产品的通道安排、工装摆放和物料路径,进行设备选择和设备布局。在设备布局前,首先进行了产品零件簇梳理;对各簇零件进行工艺流程优化;并对工艺路线、工艺顺序进行了绘制和分析;对并工序负荷、机床的能力进行计算,最后确定电磁阀阀体的单元平面布局图如图4。
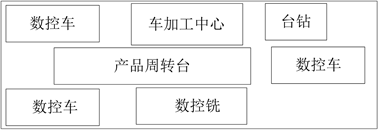
Figure 4. Layout diagram of valve processing unit
图4. 阀体加工单元布局图
经过综合计算分析,将电磁阀阀体加工单元设计为“U”形布局,使用设备为车间原有的经济性数控车2台,全机能数控车2台,数控铣1台,台钻1台。单元化的布局在厂房改造时按要求重新进行了建设。
按照单元化的布局,将电磁阀阀体生产所需的人员和设备按加工工序重新布局,大大缩短了物流路径,提高了生产效率。
在工艺布局的过程中,对原有工艺流程进行了深入的优化,把原来的18工序减少为7个工序,有效地减少了设备和人员的占有,大幅度地提高了单元内的生产效率。
3.2. 工艺管理
工艺管理的变化要随着生产管理方式的变化而变化。原来零件按批量流转时,工艺规程随着零件一起流转。但是在单元化的生产中,操作者必须都要看到自己的工艺规程。因此工艺规程必须进行单元内的工序拆分,每位单元化内的操作者就可以看到用于指导本工序操作的工艺规程。在阀体加工单元内,并且对刀具、工装的管理进行了要求。工装由技术人员申请设计、试用后,对工装的使用寿命、检查要求进行了规定,操作者按要求除完成齐套后,必须按照要求更换和检查。在单元内,某些工序所需刀具数量多,并且刀具的安装对产品的质量也有影响,因此每件刀具在单元内除对寿命有要求外,还对其在机床的刀塔上的位置、伸出长度等都有详细的规定。
3.3. 质量控制
传统的质量控制措施是每一个工序中首先加工零件,操作者自检,其他人互检,由专职检验进行检验,即“三检”;然后操作者进行批加工,再有专职检验进行检验。这是由操作者和检验挑出合格品、超差品、报废品,然后进行返工处理。在整个检验过程中,主要是依赖检验对产品质量进行事后“把关”。检验人员本身存在着检验换型,检验准备,检测时间,不但需要大量的检验员,而且还需要花费大量的时间,存在着产品加工出来,检不出来的现象。生产的效率很低。
阀体加工单元强调在加工前对产品质量进行控制,把产品质量控制相关的每一个措施都明确到操作过程中,例如刀具、夹具、找正、数控加工程序、量具等。在产品进行单元化加工前,并且实施一件产品(首件)在单元内完成,每一个工序实施三检,保证初始的正确性。然后进行单元化加工,操作者对自己加工的零件进行100%自检,检验过程被当成标准的操作计入到加工的节拍中。专职检验在操作过程中,进行巡检,并且进行10%的抽检。在单元完成后,实施全尺寸件件测量。
在阀体加工单元中,操作者的自检被列入节拍,并且明确为标准动作,另外阀体的特点是每个尺寸可以测量,这样使得产品的质量严格受控制。当操作者在加工过程出现质量问题时,立即采取挽救措施。并且技术人员在在控制措施上进行完善,保障产品的质量完全受控。
目前阀体加工单元在7个工序之间设置了一个专检,进行产品的首检,巡检和抽检工作。单元完成后,产品进入总检,由专职检验进行全检。
4. 制造单元的试运行情况
阀体加工单元的运行结果非常明显,选用车间每年投产量为2200件为阀体进行了运行。运行了五批(各160件)后,通过单值控制图(如图5)可以看出,生产效率提高了的5倍左右。
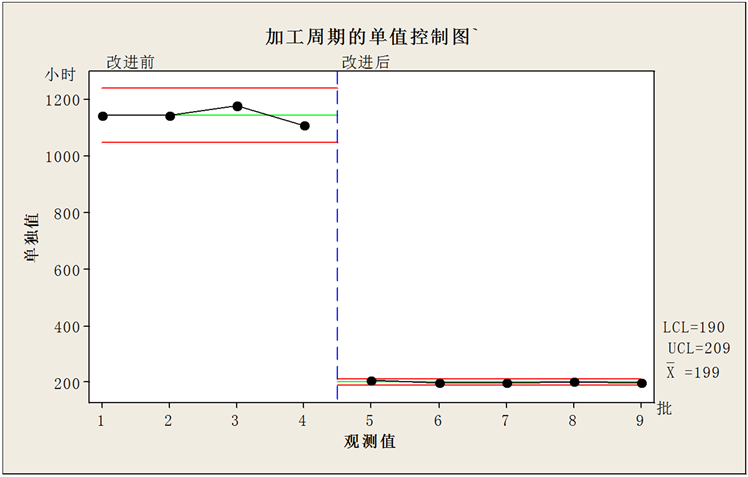
Figure 5. Statistical diagram of processing cycle
图5. 加工周期统计图
5. 总结
5.1. 保证产品质量,保证一致性
通过单元化运行,对产品加工的刀具、设备、加工参数、装夹方式、找正方式等进行了规范化的规定,可以更好地保证各加工部位尺寸及形位公差,同时因为减少了装夹及定位次数,减少了返修的工作量,更好地保证单元化内加工产品内在质量和表面质量,保证了产品的一致性。
5.2. 降低产品的生产成本
通过单元化运行,极大地降低了生产成本。因为减少了周转、装夹及定位次数,提高了表面质量,降低了返修率从而降低了加工成本。同时,通过工艺改进,减少了设备和人员的占用,降低了人力成本。
5.3. 提高产品的生产效率
单元化的实施,极大地提高了加工效率。在单元内,可以减少周转和生产准备时间、换型等待时间,生产效率可以大幅度提高。经过某型号阀体的加工统计,生产效率可以提高5倍。阀体加工单元运行还处于初期,还有大量的其他型号的阀体要在具体的技术环节进行摸索、改进,提高单元化的工作能力,促进企业能力的发展。