1. 引言
伴随机械设备向着高转速、高精度的方向发展,超硬金属零件得到越来越多的应用,例如轴承、模具等领域,其硬度能够达到50~65 HRC并且具有较高的机械强度和抗疲劳磨损的能力 [1] [2] [3] [4] 。超硬金属零件一般采用淬火的方式提高其硬度,高硬度特征导致零件在数控加工中很难加工,属于典型的难加工材料。目前数控技术课程主要从数控加工程序编制、数控运动控制原理、数控装置与检测装置、伺服控制系统等方面开展教学,目的在于让学生掌握数控机床的刀具轨迹形成与等问题。但是实际加工过程中,刀具与零件相互接触,切削力会对刀具与工件产生激励,理想的刀具轨迹并不一定会加工出高质量的零件,在超硬度零件的加工中尤为突出。此外,基于智能制造领域对技术人员的高质量要求与需求、应用型本科建设的要求,培养具有解决实际工程问题思维方式的学生尤为重要,鉴于以上背景,在数控加工技术课程中,引入超硬度零件数控加工典型案例,并对涉及的关键技术问题进行探索,激发学生全局思考的能力与创新意识。
2. 超硬材料的常用加工方法
切削加工、磨削加工以及特征加工是三种典型的加工方式。下面对其进行介绍。
2.1. 金属切削加工
它是一种采用刀具切除硬质材料的加工方法。工件往往通过夹具安装在机床上,机床带动刀具或工件或两者同时进行运动。切削过程中,有力、热、变形、振动、磨损等现象发生,这些现象的综合作用决定了零件,典型的设备是数控切削机床 [5] 。超硬零件在切削时有以下特点:
1) 硬度高、强度高:这是超硬金属材料的主要切削特点。当硬度达到HRC50~60时,其强度可达σb = 2100~2600 MPa,按照被加工材料加工性分级规定,它的硬度和强度均为9a级,属于最难切削的材料。
2) 切削力大、切削温度高:从高硬度和高强度的工件上切下切屑,其单位切削力可达4500 MPa。为了改善切削条件,增大散热面积,刀具选择较小的主偏角和副偏角。这时会引起振动,要求要有较好的工艺系统刚性。
3) 不易产生积屑瘤:超硬材料的硬度高、脆性大,切削时不易产生积屑瘤,被加工表面可以获得较低的表面粗糙度。
4) 刀刃易崩碎、磨损:由于超硬材料的脆性大,切削时切屑与刀刃接触短,切削力和切削热集中在刀具刃口附近,易使刀刃崩碎和磨损。通常超硬材料的导热系数为7.12 W/(m∙K),约为45号钢的1/7。由于其导热系数低,切削热很难通过切屑带走,切削温度很高,也加快了刀具磨损。以上特征决定了所使用的刀具应该具有高的硬度与强度、韧性、耐热性与使用寿命等特性。目前普遍使用的刀具材料大致可以分为五种:立方氮化硼刀具、陶瓷刀具、金属陶瓷刀具、硬质合金涂层刀具、聚晶金刚石(PCD)刀具,其中立方氮化硼刀具在超硬零件加工中应用较广泛。立方氮化硼(CBN)是纯人工合成材料,是继人造金刚石之后,美国GE公司于1957年首先宣布利用高温超高压装置合成的另一种新型超硬材料。聚晶立方氮化硼(PCBN)是由CBN微粉与少量结合剂烧结而成的多晶体,PCBN自1973年研制成功以来,经过众多材料专家及刀具专家的努力,PCBN材料及其刀具已完全进入实用阶段,在工业发达国家PCBN刀具已应用于汽车、重型机械等机械加工行业。
除了对刀具材料有要求外,对刀具的几何角度也有特殊要求。例如:加工超硬材料时为确保刀尖的抗冲击性能减少打刀,提高刀具耐用度、前角要小。但是如果前角过小切削抗力加大、切削径向力将会加大,易引起工艺系统的振动,导致刀具寿命、加工表面质量、尺寸精度的降低,工件材料强度、硬度高,应取较小的前角;加工特别硬的工件(如淬硬钢)时,前角很小甚至取负值。一般应选前角为0˚~−8˚之间。淬火硬度越高负前角应取得越大。精车时前角可取0˚。图1为超硬材料的两种切削方式。
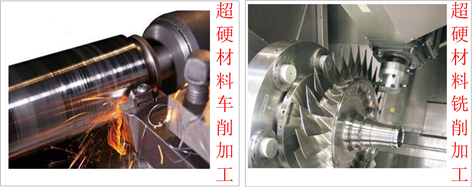
Figure 1. Turning and milling of superhard materials
图1. 超硬材料的车削及铣削加工
2.2. 磨削加工
磨削加工属于机械加工中的精加工方式,利用高速旋转的砂轮等磨具加工工件表面的加工方法。磨削可以用于加工各种工件的内外圆柱面、圆锥面和平面,以及螺纹、齿轮和花键等特殊、复杂的成形表面 [6] [7] 。砂轮上的每个磨粒都可以看成一个微小刀齿,砂轮的磨削过程,实际上是磨粒对工件表面的切削、刻削和滑擦三种作用的综合效应,如图2所示。图3为典型的超硬材料内外圆柱磨削的案例
磨削中,磨粒本身也会由尖锐逐渐磨钝,使切削能力变差,切削力变大,当切削力超过粘结剂强度时,磨钝的磨粒会脱落,露出一层新的磨粒,这就是砂轮的“自锐性”。但切屑和碎磨粒仍会阻塞砂轮,因而,磨削一定时间后,需用金刚石刀具等对砂轮进行修整。由于磨粒的硬度很高,磨具具有自锐性,磨削可以用于加工各种材料,包括淬硬钢、高强度合金钢、硬质合金、玻璃、陶瓷和大理石等高硬度金属和非金属材料。磨削时,由于刀刃很多,所以加工过程平稳、精度高,表面粗糙度小,磨削精度可达
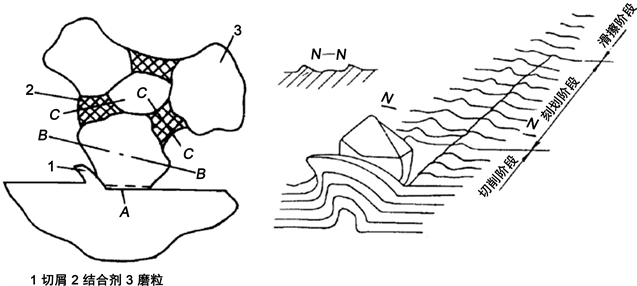
Figure 2. Abrasive particles and grinding process of grinding wheel
图2. 砂轮的磨粒及磨削过程
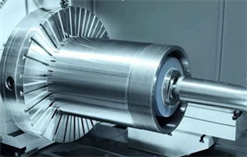
Figure 3. Grinding of inner and outer cylindrical surfaces of superhard materials
图3. 超硬材料的内外圆柱面磨削加工
IT7~IT5,表面粗糙度可达Ra 1.6~0.025 μm,甚至可达Ra 0.1~0.008 μm。
磨削与切削加工相比,具有以下特点:
1) 磨削速度很高,每秒可达 30m~50m;磨削温度较高,可达1000℃~1500℃;磨削过程历时很短,只有万分之一秒左右。
2) 磨削加工可以获得较高的加工精度和很小的表面粗糙度值。
3) 磨削不但可以加工软材料,如未淬火钢、铸铁等,而且还可以加工淬火钢及其他刀具不能加工的硬质材料,如瓷件、硬质合金等。
4) 磨削时的切削深度很小,在一次行程中所能切除的金属层很薄。
5) 当磨削加工时,从砂轮上飞出大量细的磨屑,而从工件上飞溅出大量的金属屑。磨屑和金属屑都会使操作者的眼部遭受危害,尘未吸入肺部也会对身体有害。
6) 由于砂轮质量不良、保管不善、规格型号选择不当、安装出现偏心,或给进速度过大等原因,磨削时可能造成砂轮的碎裂,从而导致工人遭受严重的伤害。。
7) 磨削加工时产生的噪音最高可达 110dB以上,如不采取降低噪声措施,会影响健康。
3. 超硬材料以切代磨加工
3.1. 超硬材料以车代磨的工艺比较
目前的超硬材料主要以磨削加工为主,磨削效率低,制造成本较高,切削加工效率高,以硬车为例对其加工特点进行说明。
制造商一直在追求低成本、高品质、快速装夹、低投资的加工方式。以车代磨能够满足以上的目标。对硬度超过45 RC的工件进行单点切削的过程称为硬车。一般硬车加工的工件硬度在58~68 RC之间。硬车时切屑能够带走至少80%的热量,以保持零件的热稳定性,合理的硬车削系统可以减少甚至省去磨削以及与之相关的高昂的刀具成本和太长的加工时间。车削45 HRC以上硬度的零件能够达到粗或半精磨削级的精度,甚至超过磨削精度。硬车技术非常具有吸引力,一套配置恰当的硬车加工单元其表现如下:表面光洁度0.00011 (0.003 mm)、圆度0.000009 (0.00025 mm)、尺寸误差0.00020 (0.005 mm)、生产效率相对而言是磨削加工的4~6倍。
3.2. 以切代磨关键问题探讨
1) 机床刚度的要求
机床刚度是指机床系统抵抗变形的能力。作用在机床上的载荷有重力、夹紧力、切削力、传动力、摩擦力、冲击振动干扰力等。按照载荷的性质不同,可分为静载荷和动载荷。机床刚度由机床床身刚度、夹具刚度、工件刚度以及刀具刚度等组成。静刚度与动刚度可以通过有限元软件理论仿真与实验测量两种方法获得。图4是采用实验的方法测量车床刀架-头尾架的静刚度示意图 [8] 。图5为施加的假设切削力与工件变形的关系图 [8] 。
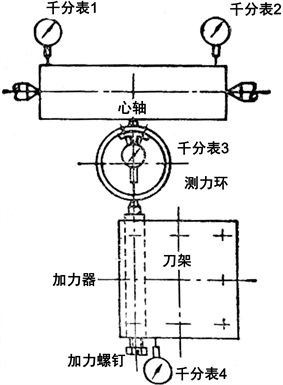
Figure 4. Static stiffness measurement sketch of lathe tool holder and head and tail holder
图4. 车床刀架、头尾架静刚度测量示意图
在图4试验时载荷逐渐加大,再逐渐减少,反复三次,图5中所示就是三次加载卸载的曲线,由图可见:
1) 力和变形的关系不是直线关系,不符合虎克定律,这反映了部件的变形不纯粹是弹性变形。
2) 加载曲线与卸载曲线不重合,它们间包容的面积代表了在加载卸载的循环中所损失的能量,也就是消耗在克服部件内零件之间的摩擦力和接触面塑性变形所作的功。
3) 当载荷去除后,变形恢复不到起点,这说明部件的变形不仅有弹性变形,而且还产生了不能恢复的塑性变形。
机床的动态刚度是指将工艺系统作为多自由度柔性系统,根据振动理论构建动力学模型,根据振动系统的传递函数识别动态刚度,它是振动系统的模态阶次相关的参数。例如某机床的动刚度被表示为:
其中,
为切削过程的传递函数,
为机床的传递函数。机床的动态刚度常采用模态实验或仿真的方法获得,图6为机床床身的第一阶和第二阶模态仿真结果。
(a) 第一阶振动模态
(b) 第二阶振动模态
Figure 6. The first two modes of machine tool bed
图6. 机床床身的前两阶模态振型
2) 机床精度的要求
高精度机床是高精度零件加工的基本前提条件,影响机床加工精度的因素很多,有机床本身的精度影响,还有因机床及工艺系统变形、加工中产生振动、机床的磨损以及刀具磨损等因素的影响。在上述各因素中,机床本身的精度是一个重要的因素。机床的精度包括几何精度、传动精度、定位精度、重复定位精度以及工作精度等。
a) 几何精度。机床的几何精度是指机床某些基础零件工作面的几何精度。是机床在不运动时的精度,它规定了决定加工精度的各主要零、部件间以及这些零、部件的运动轨迹之间的相对位置允差。
b) 传动精度。机床的传动精度是指机床内传动链两末端件之间的相对运动精度。
c) 定位精度。机床的定位精度是指机床主要部件在运动终点所达到的实际位置的精度。实际位置与预期位置之间的误差称为定位误差。
d) 重复定位精度。机床重复定位精度是指机床主要部件在多次(五次以上)运动到同一终点所达到的实际位置之间最大误差。
机床的几何精度、传动精度、定位精度和重复定位精度通常是在没有切削载荷以及机床不运动或运动速度较低的情况下检测的,故一般称之为机床的静态精度,静态精度主要决定于机床上主要零部件,如主轴及其轴承、丝杠螺母、齿轮以及床身等的制造精度以及它们的装配精度。
e) 工作精度。将工件装夹好后,对其进行切削加工,工件最终形成的加工精度称为工作精度,工作精度受切削力、夹紧力、机床内部热源、刀具磨损以及工艺系统振动等因素的影响。图7为典型机床部分位置的精度检测。
3) 超硬材料以切代磨加工效率问题
超硬材料的加工在满足加工精度的前提下,加工效率是影响其经济性的主要因素,因此探索高精加工前提下的高效加工尤为重要。切削过程的颤振现象是制约高效加工的主要因素,颤振是切削过程中引起的自激振动,会严重影响工件的加工质量。针对颤振现象,有多种解决方案,例如增加阻尼装置及主动控制单元、变工艺系统参数等,图8为伊斯卡公司通过改进刀柄结构设计的抗振导杆,图9为设计的镗削刀杆,图10为基于磁流变材料的镗削主动控制单元。
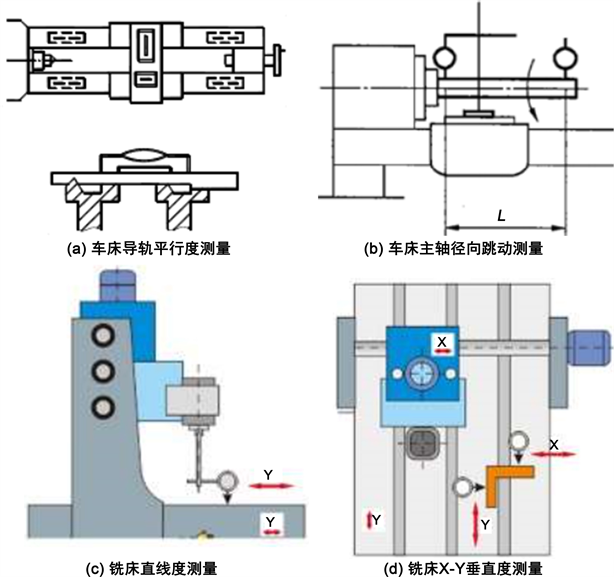
Figure 7. Typical case of machine tool accuracy measurement [8]
图7. 机床精度测量测量典型案例 [8]
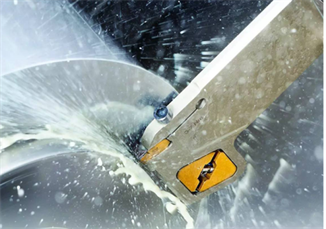
Figure 8. Damping module anti-vibration tool rod for Iska circular grooving
图8. 伊斯卡外圆切槽加工的阻尼模块防振刀杆
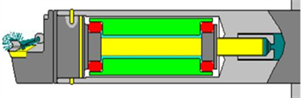
Figure 9. Damping vibration-avoiding boring bar designed for boring
图9. 镗削时设计的阻尼避振镗杆
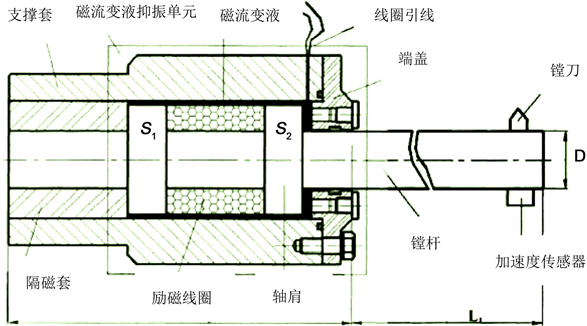
Figure 10. Active boring control unit based on magnetorheological materials
图10. 基于磁流变材料的镗削主动控制单元
4) 超硬材料切削过程的绿色制造问题
绿色制造是“中国制造2025”的重要组成部分。绿色制造技术是以传统制造技术为基础,并结合环境科学、材料科学、能源科学、控制技术等新技术的先进制造技术,其目标是使产品在制造过程中对环境的负面影响最小,资源利用率最高。
加工过程的绿色化是实现超硬材料切削加工全生命周期绿色化的重要途径,例如:据统计,汽车零件加工花费在切削液的总费用大约是刀具费用的3倍,采用干切削和微量润滑或开发环保切削液代替高成本、高污染的传统切削液可以减少对环境的冲击。研究表明数控机床在工件加工过程中,真正消耗在工件切削上的能量只有25%左右,其余能量均消耗在加工准备工作中。根据超硬材料的加工工艺,建立基于全生命周期的超硬材料能效模型,降低加工制造过程中的能量消耗,提升能效利用率,为超硬材料的绿色加工提供全面的解决方案。
4. 结论
文中对超硬材料的常用加工方法,即金属切削加工与磨削加工进行了介绍;在金属切削加工中,基于对超硬材料切削过程中存在的切削力大、切削温度高,刀具易崩碎磨损等问题,对常用的刀具材料进行了介绍。在金属磨削加工中,对磨削机理进行了介绍,并将磨削加工与切削加工进行了比较。鉴于以切代磨加工效率高的优势,开展了其关键问题的详细探讨,例如机床刚度问题、机床精度问题、加工振动问题以及基于节能减排概率的绿色制造问题。