1. 引言
无论在交通出行、物流运输还是军事国防领域,飞机作为一种高效快捷的交通工具被广泛应用。而作为飞机核心的航空发动机,需要保证提供高效动力的同时减少对环境的影响。为了达到这一目的,发动机燃烧室的设计需要做到在保证燃料在高效燃烧的时候减少氮氧化物(NOx)以及一氧化碳(CO)、二氧化碳(CO2)、粉尘等危害环境以及人体健康的副产物。常见降低CO2、CO、粉尘等物质排放的方法是提高燃烧环境的温度和压力,然而这一做法会加剧氮氧化物的产生量,对臭氧层造成不可逆的伤害。自二十世纪70年代起,美国航空航天局就开始投入研究节能低排放航空发动机 [1] [2] [3] 。到1990年,贫油直喷(LDI)燃烧室的结构被提出 [4] ,并且经过测试、实践证明:该结构的燃烧室在避免例如贫油预混蒸发(LPP)燃烧室的预混室中出现自燃和回火等问题方面具有明显的优势 [5] 。故而,近年间在研发节能低排放引擎时,通常会注重研究使用LDI燃烧室。为了保证汽化燃料与空气在燃烧室内以合理比例快速混合,避免出现局部燃料在高混合比下燃烧生成大量NOx,辅助空气与燃料混合的旋流器以及文丘里管的设计显得尤为重要。在实际应用中,通常会使用多单元的LDI燃烧室,但为了探索设计新一代更高效减排的LDI燃烧室,对单元LDI燃烧室的燃烧效果的研究进而对推进多单元LDI燃烧室的进步显得十分关键。因此,本文设计了小尺寸单元LDI燃烧室,以甲烷为燃料进行燃烧试验,观察研究了在使用不同构造的轴向旋流器对燃料与空气混合效果、火焰形成效果以及燃烧效果的影响,并且测试了改变火焰筒出口尺寸对燃烧性能的影响,进一步探讨了LDI燃烧室结构对其燃烧性能的影响。
2. 实验设计
燃烧实验使用的单元LDI燃烧室由火焰筒和燃烧室头部两部分组成。如图1所示,火焰筒设计使用具有矩形横截面和3.2 cm × 3.2 cm × 15.2 cm内尺寸的结构。为了便于观察记录,选择使用金属框架固定的耐高温石英玻璃制作火焰筒,便以观测火焰的形成状况,以检测燃烧效果。火焰筒顶端安装如图2所示金属卡槽与带有不同尺寸矩形开口的金属板,通过改变金属板放置的位置达到改变火焰筒出口尺寸的效果。燃烧室的下部分为燃烧室头部,结构如图3所示。燃烧室头部主要由喉部半径为0.635 cm的文丘里管,可拆卸更换的旋流器(旋流叶片安装角为55˚),均流管以及单元LDI喷嘴构成。
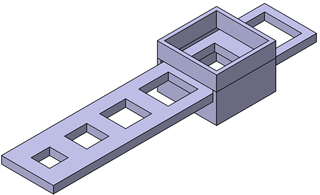
Figure 2. Combustion Liner exit area adjusting device
图2. 火焰筒出口尺寸调节装置
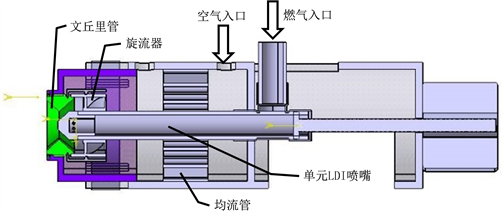
Figure 3. Combustion chamber head structure
图3. 燃烧室头部结构
本实验中主要研究测试旋流叶片安装角为55˚的轴向旋流器。选用的旋流器结构为单级轴向旋流器、双级同向旋流器和双级逆向旋流器。基于燃烧室的整体尺寸,如图4所示标注,设计旋流器通道横纵比L/b = 2,以及文丘里管与旋流器有效面积比为Aeff,Venturi/Aeff, Swirler = 0.9,对三种旋流器的各部位尺寸进行了计算设计。同向双级轴向旋流器和反向双级轴向旋流器尺寸一致,内环结构一致,外环旋流叶片安装方向相反。试验所需旋流器的各结构尺寸如表1所示。并且基于便于更换旋流器的考虑,在旋流器外部设计了卡扣结构,用于连接旋流器与文丘里管。设计所得各旋流器结构如图5所示。
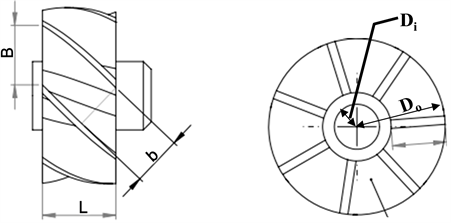
Figure 4. Single swirler cross session structure
图4. 单级旋流器截面结构

Figure 5. Design and structure of swirlers
图5. 旋流器设计与结构
燃烧实验中使用甲烷气体为燃料,并使用气泵向燃烧室内泵入空气与甲烷气体混合,通过外部点火的手段进行引燃。实验方案为在使用相同燃料(甲烷)、空气压力以及流量的情况下,使用同一单元LDI燃烧室,分别进行使用单级轴向旋流器、使用同向双级轴向旋流器和使用反向双级轴向旋流器的3次燃烧实验,观察记录火焰的形态以及燃烧效果,并且在每次实验的燃烧过程中逐步减小火焰筒出口面积,进一步观察记录火焰筒出口尺寸改变对燃烧效的影响。在每个实验方案中,对火焰形态进行连续拍摄记录,通过分析火焰稳定性以及形态对该方案下燃烧室的燃烧性能进行分析研究。
3. 实验结果与分析
如图6(a)所示,使用单级轴向旋流器时火焰不能很好的达到稳定燃烧状态。燃烧过程中火焰轮廓模糊,无法清晰的观察到燃烧室的流场结构,火焰浮空长度极小。同时由于这一原因,如图6(b)所示,当缩小火焰筒出口尺寸到50%的时候,火焰的稳定性受到了明显的干扰,出现火焰吹拉现象,从而可见此状态下燃烧效率较低,燃烧不充分,易产生大量污染物,甚至易造成回火等问题。
(a)
(b)
Figure 6. Flame shapes of LDI combustor with a single axial swirler (exit area 100%/50%) cases
图6. 使用单级旋流器(火焰筒出口100%、50%)时的火焰
使用双级轴向旋流器时,如图7(a)~(b)和图8所示,火焰均可达到较稳定燃烧状态,燃烧过程中火焰轮廓清晰,均可清晰的观察到燃烧室的流场结构与燃烧场相互耦合形成的旋流火焰。并且对比使用单级轴向旋流器时的火焰的状态,火焰浮空长度明显增加,火焰长度缩短,说明双级轴向旋流器能使燃料与空气迅速高效的混合。可见在有效面积比相同的情况下,双级轴向旋流器的结构较单级轴向旋流器的结构能够更合理的旋流空气,使得燃料与空气的混合效率提高,并且使二者的混合也更加均匀迅速,从而大幅提高燃烧室的燃烧效率,使燃料的燃烧更充分,降低排放CO、CO2以及粉尘等污染物。并且火焰燃烧状态稳定使得更有利于温度均匀分布,从而降低NOx的排放。
在进行使用双级轴向旋流器燃烧实验时,缩小火焰筒出口尺寸会引起短暂的火焰不稳定燃烧状态,但短时间内可以恢复稳定燃烧状态。达到稳定燃烧状态后,如图7(a)与图7(b)对比所示,使用同向双级轴向旋流器进行实验时,缩小火焰筒出口会一定程度上改变稳定燃烧状态的火焰形状,提高燃料与空气混合流场的旋流程度,小幅度增加火焰浮空长度。可见在合理范围内缩小火焰筒出口面积,通过提升火焰筒出口处流速,有助于提升燃料与空气的混合效率,从而提高燃烧室的燃烧效率。
如图7(a)与图8对比所示,使用反向双级轴向旋流器进行试验所得的燃烧状态与使用同向双级轴向旋流器时的燃烧状态总体相似。相较而言,使用反向双级轴向旋流器进行实验产生的火焰长度较短,火焰浮空长度较长,旋流强度较强,说明此方案下燃料与空气的混合更为迅速,燃烧效率更高。这一结果表明,在相同条件下,当有效面积比相同,旋流叶片数以及结构尺寸均一致的情况下,反向双级轴向旋流器的结构较同向双级轴向旋流器的结构而言,对空气旋流产生的流场旋流程度更高、切向流速更快流场,从而更有助于空气与燃料的迅速高效混合,达到提高燃烧室的燃烧效率,同时降低污染物排放的效果。
(a)
(b)
Figure 7. Flame shapes of LDI combustor with a co-rotating two-stage swirler (exit area 100%/50%)
图7. 使用同向双级旋流器时的火焰(火焰筒出口100%/50%)
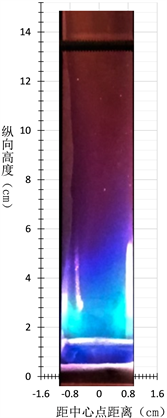
Figure 8. Flame shapes of LDI combustor with a counter-rotating two-stage swirler
图8. 使用反向双级旋流器时的火焰
4. 结论
· 旋流器的结构变化以及火焰筒的出口面积变化均可对单元LDI燃烧室的燃烧性能产生影响,并且因旋流器的结构改变而产生的影响尤为明显。
· 在相同燃烧条件以及相同有效面积比时,使用双级轴向旋流器比使用单级轴向旋流器能让LDI燃烧室有更高的燃烧效率和更低的污染物排放量。
· 在相同燃烧条件和结构尺寸下,反向双级轴向旋流器结构对提高燃烧室的燃烧效率和降低污染物的排放量优于同向双级轴向旋流器的结构。
· 缩小火焰筒的出口面积有利于提高燃烧室的燃烧效率和降低污染物的排放量,但效果有限,并且会对火焰的燃烧稳定造成影响,最佳火焰筒出口面积的选择需综合考虑效果与影响。