1. 引言
电机作为电能转换为机械能的能量转换装置,其运行过程中必然会产生一定的能量损失,而绝大部分的损耗将以发热的形式耗散掉,进而导致电机的工作温度升高。电机工作温度过高会使绝缘老化,严重情况将导致电机烧毁。
屏蔽泵电机热分析计算可用于预测屏蔽泵电机定子线圈的最大表面温度,国内多位学者已经对屏蔽泵电机发热的问题做了很多的研究 [1] [2] [3] 。本文热分析主要使用通用软件MATLAB [4] 对结构进行建模和计算,并生成最大线圈温度计算程序,为稳态热分析计算。程序要求输入各关键参数,通过自身迭代得到分析结果,计算速度快,并与有限元计算结果一致;因程序分析模型与其他的屏蔽泵电机模型类似,具有一定应用性。
本文以某一屏蔽泵电机为例,简述其分析方法、建模过程以及最大线圈温度的敏感性分析。
2. 最大定子线圈温度计算
2.1. 分析目的
屏蔽泵电机使用的是F级绝缘,绝缘承受的最高温度为155℃;本分析的目的,为确认最大线圈温度小于155℃。
2.2. 分析方法
使用程序软件MATLAB,运用有限差分法,将结构离散化,计算绕组最高温度及各部件温度,为稳态运行的计算。因为忽略一些热传导路径只会提高峰值温度,故计算模型求得的温度相对保守。用于计算线圈温度的热模型和方程如2.3节所示。
计算分析过程:1) 得到线圈到各部件的径向热传导路径以及线圈的轴向热传导路径;2) 建立热分析网络法的计算模型,迭代得到线圈和各部件的温度结果。
2.3. 计算模型说明
线圈温度模型包括线圈的轴向温度热传导模型和把线圈热量带走的径向传导系数模型。
线圈温度计算模型的建立需要假定以下条件:
1) 由于定子铁心叠片的径向热传导能力远远大于轴向热传导能力,不考虑定子铁心叠片处的轴向热传导;
2) 由于定子线圈端部对机壳的空间距离不大,不考虑定子线圈端部对机壳的热辐射。考虑热辐射时,线圈端部的部分热量会以热辐射形式传导出去。因此,不考虑定子线圈端部的热辐射时计算的结果更为保守。
3) 电流在线圈中的涡流产生热量以等效系数进行修正。
基于上述假设,将线圈温度计算模型分为轴向温度热传导模型和径向传导模型。
2.3.1 .轴向传导模型
根据导热的基本定律,一维稳态热传导方程为:
(1)
线圈热量由线圈电阻产生的热量和径向的热传导组成:
1) 电阻产生的热量可以通过线圈导体上的电流计算得到。单位长度线圈电阻产生的热流密度为:(导体截面积As)
(2)
2) 根据牛顿冷却式,单位长度线圈的径向热传导方程:
(3)
h:表面传热系数;
Aw:与流体接触的壁面面积;
Tw:线圈壁面的表面温度;
:流体温度。
径向热损失是根据容积进行计算,所以需要除以导体的截面积As。
带入(1)式得到
(4)
注意:由于径向热传导沿线圈长度s是不同的,因此有不同的径向热传导方式,公式(3)只表达了一种径向热传导方式。
对方程(4)使用有限差分法进行计算,边界条件见2.5节。这种解法满足能量守恒,总的径向导出能量等于总产生能量。
2.3.2. 径向传导模型
径向热传导考虑了定子冲片和齿压板的热传导。由于端部线圈没有直接的导热路径,只有通过辐射和自然对流传导至端部定子腔的空气中,所以端部线圈的径向传导效率是很小的。而铁芯槽部的线圈具有很好的传导路径,能够将热量传导到定转子屏蔽套环域和定子机壳外面的水中,因而径向热传导效率相对来说较高。同样的,齿压板处的线圈也有相对较高的热传导效率。本计算中只考虑铁心和齿压板处的径向传导,忽略了端部的径向传导。径向传导模型示意图见图1。
由于股线的热传导系数较高,这里假设股线间是各向同性的。定子线圈需要进行真空压力浸渍,线圈绝缘与槽之间都是树脂,线圈绝缘和树脂的热传导系数却很难通过试验测定,因此线圈股线与槽的周向传导系数是通过股线与槽的间隙定义的。
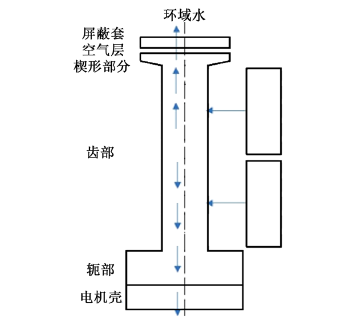
Figure 1. Schematic for radial conductance calculation
图1. 径向热传导模型示意图
(5)
铁心齿部在径向按照槽楔位置,划分为一个楔形部分和由10个单元组成的直线部分。线圈产生的热量经由周向传到铁心齿部,然后沿铁心径向分别传导到定转子环域循环水和机壳外侧的环境中。内径侧的径向传导路径包括铁芯齿部、铁芯齿部与屏蔽套的空气间隙,屏蔽套和环域间隙水。外径侧的径向热传导路径包括铁芯齿部、铁芯轭部(剩余硅钢部分)、定子机壳和环境。屏蔽套和环域水的表面强制对流换热系数详见2.4.3节说明,由于定子机壳与环境的热传导按自然对流考虑,因而计算结果相对保守。
通过径向热传导模型的求解,可以得到径向节点的温度分布和最高温度值、线圈的最高温度、线圈热量流向内、外径侧的百分比。热传导的基本公式如下:
(6)
同理,齿压板径向热传导过程也是相似的。
径向导热介质主要为定子铁心和齿压板。由于铁心的径向热传导率为轴向热传导率的10倍以上,而齿压板相对厚度较小且轴向两端分别空气和铁心,齿压板的径向热传导占主要部分。
基于上述简化,对已运行机组进行了线圈温度计算校验,计算结果比真机实测值高约表0%~10%,总体上能够满足设计需求,验证了该简化的有效性。
2.3.3. 定子屏蔽套表面强制对流换热系数
单边定转子屏蔽套环域间隙为δ,线速度为v,温度为31℃,得雷诺数为:
(7)
普朗特数 :动量扩散厚度与热量扩散厚度之比的一种度量:
(8)
对于管内湍流强制对流换热,得努塞特数为(《传热学》(5-54)) [5] :
(9)
得定子屏蔽套表面的热传导系数为:
(10)
其中:ν为运动粘度;α为导温系数;μ为动力粘度;cp为等压比热容;k为热导率;λ为水的导热系数。
2.4. 线圈温度输入条件
结构参数、铁损与定子屏蔽套损耗来自于电磁计算。输入条件如下:
1) 结构参数;
2) 损耗;
3) 各部件材料随温度变化的热传导系数;
4) 铜的电阻率(铜电阻率为0.0172 μΩ∙m)。
2.5. 温度边界条件
1) 电机壳外侧
电机壳静置于空气环境中,使用空气的自然对流换热系数的最小值10 W/m2K。
2) 定转子环域水
定转子环域水温度31.2℃,环域表面的热传导系数为屏蔽套表面的强制对流换热系数。
海水通过定转子屏蔽套环域带走热量,使用热生成率和流量保守的计算环域水温升。
其中:
为热生成率;
为海水的质量流量,数值来自于水力计算;
为水域温升。
使用热生成率与流量计算得水上升的温度。海水上升的温度如表1所示。
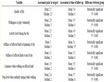
Table 1. The temperature of the annulus
表1. 环域水上升的温度
2.6. 最大线圈温度结果
结果表明最大线圈温度为96.6℃,小于温度限值155℃,满足设计要求,热分析结果详见表2。线圈温度沿轴向的变化曲线详见图2,该曲线的形状符合线圈温度轴向分布规律;定子铁芯处,冲片的径向温度分布和线圈的径向温度分布详见图3,由图中得到,屏蔽套与冲片的温度差值较大,主要是它们之间的空气层对热传导的影响,下一章节会对空气层厚度的敏感性进行分析。
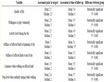
Table 2. The result of the thermal analysis, unit: ℃
表2. 热分析计算结果,单位:℃
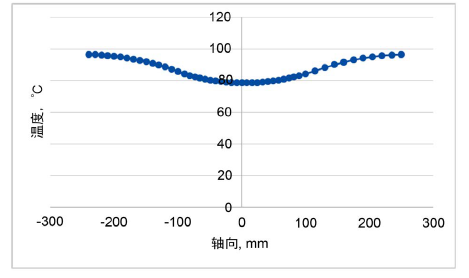
Figure 2. Motor winding temperature distribution
图2. 线圈温度沿轴向的变化曲线
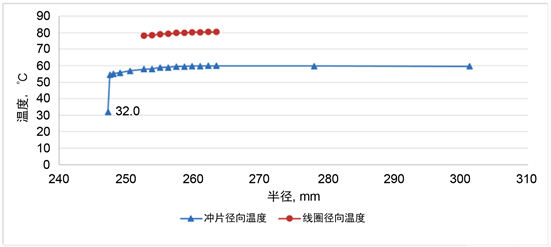
Figure 3. The radial-distribution temperatureat the location of stator core
图3. 定子铁芯处部件径向温度分布
3. 最大线圈敏感性分析
1) 屏蔽套与冲片间的空间层厚度直接影响径向传导系数,对最大线圈温度影响较大,结果如图4所示。
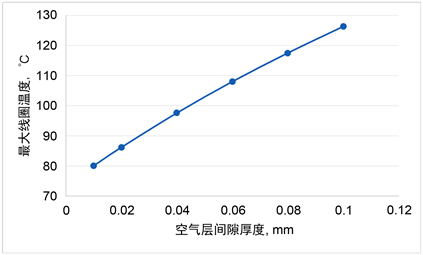
Figure 4. The curved line between maximum winding temperature and air layer thickness
图4. 最大线圈温度与空气层厚度的关系曲线
2) 屏蔽套表面的强制对流换热系数直接影响屏蔽套的温度,而对最大线圈温度影响几乎没有。最大线圈温度、屏蔽套温度与屏蔽套表面的强制对流换热系数关系曲线如图5所示。
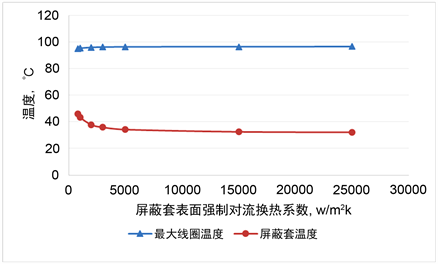
Figure 5. The curvedline between the maximum winding temperature, can temperature and the forced convention heat transfer coefficient on inner surfaceof can
图5. 最大线圈温度、屏蔽套温度与屏蔽套表面强制对流换热系数的关系曲线
3) 小节:屏蔽套与冲片间的空气层厚度直接影响最大线圈的温度和其他各部件的温度;屏蔽套表面的强制热对流系数在一定范围内,仅会影响屏蔽套的温度,几乎对全局温度没有影响。
4. 总结
1) 由计算分析得到,最大线圈温度热分析模型可以忽略冲片的轴向热传导,忽略端部线圈的热辐射;
2) 该计算程序适用于铁芯槽部形状为狭窄等宽槽,对梨形槽计算精度不高;
3) 通过计算结果,得到屏蔽套与冲片间空气层厚度直接影响最大定子线圈温度;环域屏蔽套强制热对流系数,在一定范围内对最大线圈温度影响较小,对屏蔽套温度有一定的影响;
4) 该程序相对于有限元计算,计算速度快,无需建模,直接输入参数得出结果。