1. 引言
根据海洋强国战略部署,我国将大力开发海洋油气工程装备,海洋平台等海洋工程设施,海洋平台苛刻的使用环境,对材料性能力学性能、耐蚀性能均提出了更高的要求。海水的氯离子含量约1.83%,海水浓缩液的氯离子浓度3.4%,操作压力约为7 MPa,当海水超过临界流速时,传统奥氏体不锈钢耐晶间腐蚀、应力开裂腐蚀、疲劳腐蚀、空泡腐蚀、以及耐冲刷和抗海生物污损等性能均受到影响。腐蚀速度急剧增加,现有不锈钢材料已远远不能适应海洋苛刻环境条件下的应用。
目前,世界各国针对海水特定腐蚀介质,不断在节省资源成本、专用化等方面开发了新型及特殊用途的超级双相不锈钢新钢种,并已在海洋、石油化工等通用阀门上得到应用 [1] 。
2. 试验材料与方法
试验钢采用采用氮气保护和氮合金化方法进行熔炼,待铸锭完全凝固冷却、切除冒口后,将铸锭切成二部分,一部分在1180℃保温,采用真空加压气淬工艺,由控制冷却工艺控制析出相的比例;一部分铸锭直接进行固溶处理。化学成分如下。
C:≤0.03%,Si:0.5%~0.8%,Cr:26%~28%,Mn:0.5%~2.0%,Ni:5%~10%,Mo:1.5%~6.0%,N:0.4%~0.6%,Al:0.8%~2.0%,Nb:0.025%~0.035%,Fe:余量。
真空加压气淬工艺,由控制冷却工艺控制析出相的比例。控制冷却采用分段式冷却控制,1180℃~650℃温度区间,氮气压力9~10 MPa;650℃~50℃温度区间,氮气压力6~7 MPa。
分别从控制冷却状态、固溶态剖取试样,加工成标准拉伸试样、V型缺口的夏比冲击试样。按《GB/T228-2002金属材料室温拉伸试验方法》在WE-300型300千牛顿液压万能试验机上进行室温拉伸试验,拉伸速率1 mm/min。测定抗拉强度Rm、屈服强度RP0.2、断后伸长率A、断面收缩率Z。按照《GB/T229-1994金属材料夏比摆锤试验方法标准》在JB-30摆锤式冲击试验机,用V型缺口标准试样进行室温冲击试验,测量试验钢的冲击功。
将样品磨抛后,用氢氧化钾和铁氢化钾试剂腐蚀,制成标准金相试样,利用Axio vision显微图像分析系统测定双相不锈钢中两相的含量,根据不同的染色分辨奥氏体相、铁素体相,根据《GB/6401不锈钢中a-相面积含量金相测定法》和《GB/T 13305奥氏体不锈钢中a-相面积含量金相测定法》标准对每个试样选定3个视场进行测量取平均值。采用日本RIKAGU (D\max-2550 40 kV 300 mA) X射线衍射仪对试样进行XRD分析,测定相比例。试样经过砂纸打磨后,经双喷电解液穿孔后在透射电子显微镜(JEM-200CX)上进行析出相观察及衍射分析。
不同热处理状态试样经磨床磨平、抛光后,根据国标《GB/T 4334-2008金属和合金的腐蚀–不锈钢晶间腐蚀试验方法》,用10%硝酸–3%氢氟酸试验溶液在70℃煮两个周期。每个周期2小时,共4小时,计算每个周期的腐蚀速率。
3. 试验结果与讨论
3.1. 力学性能结果
两种工艺处理后的试样力学性能见表1,采用控制冷却工艺处理后抗拉强度、屈服强度、延伸率明显得到提高,断面收缩率、冲击功基本相差不大。
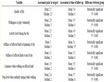
Table 1. The mechanics property of duplex stainless steel
表1. 不同处理工艺的双相不锈钢力学性能
3.2. 微观组织分析
双相不锈钢经固溶处理后的组织为奥氏体+铁素体,图1,组织经染色处理后,测得奥氏体含量52%,铁素体48%。选用γ(200)和α(200)衍射峰的积分强度,图2,利用公式(1)计算双相不锈钢中铁素体与奥氏体的相比例体积分数,经计算奥氏体含量52%,铁素体48%。XRD的计算结果与金相组织评定一致,基本达到铁素体、奥氏体的平衡组织。
(1)
双相不锈钢经控制冷却处理后的组织为奥氏体、铁素体和少量的析出相,图3,利用图4中的衍射峰积分强度,计算奥氏体含量为45%,铁素体55%;将该试样深度电解腐蚀后通过TEM观察,亚晶界、晶界有沉淀相析出,图5,经电子衍射分析是Cr23C6,此外可以看到有少量的氮化物的析出物,呈透镜状,经电子衍射分析是Cr2N,氮化物形貌见图6。
双相不锈钢的含氮量在0.5%左右,固溶在钢中的氮能稳定奥氏体组织,抑制铁素体的生成,使两相的比例保持稳定,铁素体和奥氏体双相组织的平衡,使得双相不锈钢具有优良的综合力学性能强度、韧性等显著得到提高。与316奥氏体不锈钢相比,固溶态的屈服强度几乎提高一倍 [2] 。
在控制冷却状态下,氮元素和其他合金元素形成合金碳氮化合物,阻碍晶粒的长大;由于金属间化合物和碳氮元素的析出,导致铁素体的含量在逐渐增多,两相比例的变化及金属间化合物的析出导致抗拉强度和屈服强度优于固溶态。
3.3. 晶间腐蚀试验结果及讨论
晶间腐蚀是材料的晶间区的腐蚀速度远远大于晶粒内部的腐蚀速度,腐蚀沿着晶间发生和发展,发生晶间腐蚀后晶粒间的结合力大大降低,使得力学性能大大降低,晶间腐蚀具有隐蔽性,金属表面不易察觉,因此许多突发事故均是由晶间腐蚀引起 [3] 。
两个酸煮试验周期后的腐蚀速率见表2,可以看出,两种处理状态的双相不锈钢在试验溶液中煮2小时后的腐蚀速率相差不大,但在第二个试验周期,即酸煮4个小时后,控制冷却状态腐蚀速率高于固溶处理状态;控制冷却状态在两个酸煮试验周期内的平均腐蚀速率比固溶处理态提高14.6%;利用扫描电镜从微观的角度可以看到,腐蚀试验第一个周期,两种状态双相不锈钢在相界出有明显的黑色的腐蚀坑,即发生了明显的晶间腐蚀,图7;经过第二个周期的酸煮实验,可以看出相比于第一个周期在控制冷却状态在晶界处有更深更宽更明显的腐蚀沟,固溶态出现了一条更长更宽的腐蚀沟,图8。
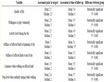
Table 2. The Corrosion rate after acid boiling
表2. 酸煮后的腐蚀速率

Figure 7. The SEM microstructure after acid boiling 2 hours
图7. 酸煮2小时后的SEM图

Figure 8. The SEM microstructure after acid boiling 4 hours
图8. 酸煮4小时后的SEM图
晶间腐蚀涉及材料的晶体结构,元素的固溶含量,沉淀物的析出过程、固态相变等,早期学者对晶间腐蚀产生原因及机理进行研究,取得许多成果,如早在30年代就发现含有一定量铁素体的奥氏体 + 铁素体双相不锈钢与同样碳含量的奥氏体不锈钢相比,能改善其晶间腐蚀性能。
两种工艺相比较,奥氏体与铁素体的相比例发生改变,控制冷却状态的铁素体含量由固溶态的48%提高到55%,并有析出物产生。铁素体增加了晶界和相界的面积,含铬量较奥氏体高很多,而且铬的扩散速度也比奥氏体中快,虽然在相界和晶界析出碳、氮化物时消耗了铁素体中的部分铬,但容易补偿,不容易形成贫化区;碳、氮化物在铁素体中的析出、长大,使得奥氏体、铁素体晶界界面移向铁素体相,虽然铁素体增加了晶界和相界的面积,但是氮能够扩大奥氏体相区,有效地控制了相比例的平衡,因此控制冷却状态的强度虽已达到热轧态的强度,远高于固溶态,但其由沉淀析出造成耐蚀性能的损失并不大。
4. 结论
1) 双相不锈钢钢采用控制冷却工艺处理后抗拉强度、屈服强度、延伸率明显得到提高;断面收缩率、冲击功基本相差不大。
2) 固溶处理后的组织为奥氏体+铁素体,奥氏体含量52%,铁素体48%;控制冷却后的组织为奥氏体、铁素体和少量的晶内、晶界有碳化物、氮化物沉淀相析出,奥氏体含量为45%,铁素体55%;两相比例的平衡控制与第二相沉淀析出是提高强度的主要原因。
3) 在两个试验周期内,控制冷却状态的平均晶间腐蚀速率比固溶处理态提高14.6%,虽然铁素体增加了晶界和相界的面积,但是氮能够扩大奥氏体相区,有效地控制了相比例的平衡,因此控制冷却状态的强度虽已达到热轧态的强度,远高于固溶态,但其由于沉淀析出造成的耐蚀性能的损失并不大。