1. 引言
涡轮是航空发动机的核心部件带动整个航空发动机正常运转,其表面的气流相当复杂,涡轮叶片设计的好坏直接关系到航空发动机的性能,随着航空工业的不断发展,对航空发动机的性能要求越来越高,满足这种要求最为有效的方法就是提高涡轮前气流入口的温度 [1] ,涡轮进口燃气温度已经成为航空发动机发展的一个重要标志,20世纪70年代,涡轮进口燃气的温度为1600 K~1700 K; 90年代末已达2112 K;而本世纪初将要达到2300 K~2400 K;平均每年以15 K~20 K的速度递增 [2] 。正在研制定向单晶、定向共晶、钨丝增强镍基合金和陶瓷材料,研制弥散强化镍基合金和新型粉末涡轮盘合金,以适应更先进发动机的耐高温涡轮叶片和涡轮盘的需要,数据显示发动机涡轮前温度每提高56 K,发动机的输出功率就可增大8%~13% [3] ,但高温在带来更高热效率的同时也使涡轮叶片的工作环境变得十分恶劣,叶片一方面受到很高的热负荷,另一方面要受到很强烈气流冲击载荷及离心载荷作用,使寿命大幅降低 [4] ;为了解决高温带来负面效应这一难题,仅仅依靠发展先进耐高温材料是远远不够的,涡轮进口燃气温度提升的速度要明显高于耐高温叶片材料发展的速度 [5] ,唯一可行的办法是采取冷却和防护措施。事实证明,冷却技术的效果极为显著,20世纪60年代,采用冷却技术而带来的冷却温降为60K~100K, 70年代中期冷却温降为300 K,目前冷却温降已达400 K~600 K [2] ;而且随着冷却方法的不断改进,冷却温降还有可能达到一个新的水平。当前先进发动机的涡轮进口燃气温度已达到2000 K左右,比高压涡轮叶片金属材料的熔点高400 K [6] ,可见冷却设计的重要性和迫切性,本文即在这种背景下对高温部件涡轮叶片的冷却结构进行设计,研究涡轮冷却叶片在工作状态下的温度分布特性。
2. 流固耦合传热方法
流固耦合传热一方面指流体与固体内传热过程通过流固交界面的位移、形变、传热和相变等作用相互耦合,另一方面指流固交界面上流动、辐射和烧蚀等不同物理过程相互耦合 [7] 。对于某些流体与固体之间的对流换热问题,热边界条件无法预先给定,而是受到流体与壁面之间相互作用的制约。
这时无论界面上的温度还是热流密度都应看成是计算结果的一部分,而不是已知条件。像这类热边界件是由热量交换过程动态地加以决定而不能预先规定的问题,称为流固耦合传热问题 [8] ,用流固耦合传热方法可以将流体与固体之间复杂的外边界条件变成相对简单的内边界进行处理,不但减少了边界条件,又符合实际状态从而提高了仿真的合理性和精度。流固耦合传热计算的关键是实现流体与固体边界上的热量传递。由能量守恒可知,在流固耦合的交界面,固体传出的热量应等于流体吸收的热量,因此,流固边界面上的热量传递过程可表示:
式中:
为固体导热系数;
为对流换热系数,
为固体壁面温度;
为流体温度。
涡轮冷却叶片的传热既包括流固耦合传热即叶片和外部高温燃气强对流换热及叶片与内部冷却气流换热,又包括固体叶片内部温差引起的热传导 [9] 。
热传导遵循傅立叶定律:
式中,
是热流密度
,
是导热系数
。
3. 不同冷却结构涡轮冷却叶片温度分布研究
现代航空发动机涡轮入口处的温度不断升高,燃气轮机工作时温度最高的地方是高压涡轮,涡轮叶片处于恶劣工作环境当中,受到高温载荷作用下的涡轮叶片经常出现因强度不够而产生失效破环的现象进而影响发动机的整体性能,本文以涡轮叶片不同的冷却结构为研究对象,以叶片整体温度分布最小为研究目标开展相关研究,寻找最优冷却结构的涡轮叶片,其优化数学模型为
式中,X为设计变量即冷却结构;
为叶片整体温度分布;
为冷却结构关键点坐标。
3.1. 带9个径向圆柱式冷却孔涡轮冷却叶片
为了寻求先进涡轮叶片冷却结构,本文首先对叶片的圆柱式冷却孔沿前缘往后缘方向进行结构设计,冷却孔具体尺寸见表1,本文中的叶片材料选用高温镍基合金GH4133,密度为8210 kg/m3。
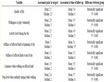
Table 1. Turbine cooling blade diameter with 9 radial circular holes
表1. 带9个径向圆形孔涡轮冷却叶片直径
带9个径向圆柱式冷却孔涡轮冷却叶片温度分布
基于三维流固耦合共轭传热计算涡轮叶片的温度分布,涡轮叶片外部与流入涡轮1600 K高温主流燃气进行对流换热,涡轮冷却叶片内部与300 K的冷却气流进行强对流换热,主流燃气入口设为压力进口,总压为1.81 MPa,燃气出口为压力出口,静压为1.13 MPa,内部冷却孔采用质量流量进口,具体边界条件见表2,边界对流换热系数由流固耦合计算得到,利用CFD仿真计算得到涡轮冷却叶片温度分布见下图。
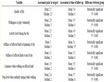
Table 2. Boundary conditions of internal cooling hole
表2. 内部冷却孔边界条件
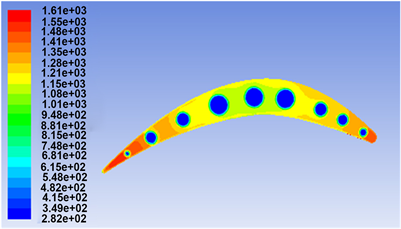
Figure 1. Temperature distribution on blade root surface of 9-hole cooling hole turbine blade
图1. 9孔式冷却孔涡轮叶片叶根面温度分布
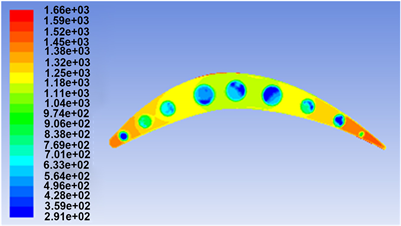
Figure 2. Temperature distribution on blade tip surface of 9-hole cooling hole turbine blade
图2. 9孔式冷却孔涡轮叶片叶顶面温度分布
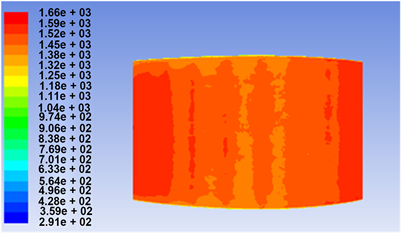
Figure 3. Suction surface temperature distribution of 9-hole cooling hole turbine blade
图3. 9孔式冷却孔涡轮叶片吸力面温度分布
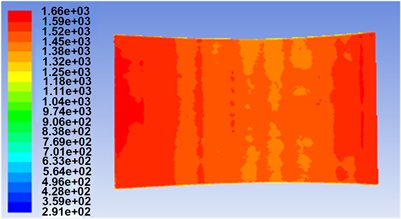
Figure 4. Pressure surface temperature distribution of 9-hole cooling hole turbine blade
图4. 9孔式冷却孔涡轮叶片压力面温度分布
通过对带9孔式涡轮冷却叶片壁面温度分布图进行分析,发现冷却气流给整个涡轮冷却叶片带来了较为显著的冷却效果,图1表明叶片冷却孔附近温度最低,且这种低温效应沿着各个方向进行梯度式发散,其周围出现了大面积的低温区域;各个圆柱冷却孔之间的区域温度有所回升,这是由于冷气流对孔之间区域辐射力度有所减弱所致;从前缘往后缘方向来看,4、5、6号孔给叶片带来的冷却效果最为明显,此三孔周围的一大片区域属于低温区域,而这三个孔的孔半径是最大的,而其余冷却孔随着冷却孔半径减小附近区域的冷却效果下降,总之,随着冷却孔半径逐渐增大,冷却效果也越加显著,此外,叶片前缘附近温度明显偏高,这是由于叶片前缘区域最先受到高温气流的灼烧作用温度往往偏高,一般也是容易出现高温损害的部位之一,1号冷却孔及时的给叶片前缘进行冷却降温,可以看出此区域温度大致保持在1410 K左右,实现了近200 K的降温效果,从1号冷却孔到4号冷却孔进行分析发现,叶片内部的降温效果越来越明显,这是由于冷却孔半径增大冷却气体流量随着增大使得冷却效果提升的缘故,从7号孔至9号冷却孔再到叶片尾缘进行分析发现,冷却孔逐渐变小冷却效果也在明显下降,叶片尾缘附近区域温度最高维持在1480 K左右,这是由于此区域远离主要冷却气流受冷却气流影响小所致。
通过对图1和图2进行对比发现,涡轮冷却叶片叶根面温度分布总体要低于叶片叶顶面处的,温差普遍达70 K左右,这是由于冷却气流最先从冷却叶片叶根面射入沿着叶高方向流动逐渐受到叶片壁面的加热作用气流温度逐渐升高使得其对叶片的降温效果有所下降。
分析图3和图4发现,涡轮冷却叶片压力面与吸力面上前后缘附近温度偏高,前后缘之间大范围面积温度显著偏低,这是前后缘之间区域分布着叶片内部主要的冷却气流使叶片得到显著冷却所致。
3.2. 带3个径向混合式冷却孔涡轮冷却叶片
先进冷却结构能够显著对高温部件涡轮叶片冷却降温的同时也能最大程度保持叶片的力学性能,为了探索高效冷却结构,本文下面对2个椭圆式冷却孔和一个圆柱式冷却孔组成的涡轮冷却叶片进行温度分布研究,冷却孔具体尺寸见表3。
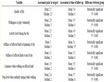
Table 3. Specific dimensions of turbine blades with 3 radial mixed cooling holes
表3. 带3个径向混合式冷却孔涡轮叶片具体尺寸
带3个径向混合式冷却孔涡轮冷却叶片温度分布
基于三维流固耦合共轭传热计算3孔式涡轮冷却叶片的温度分布,涡轮冷却叶片外部与从发动机燃烧室流入涡轮1600 K高温主流燃气进行对流换热,叶片内部与冷却孔处流动的300 K冷却气流进行强对流换热,主流燃气进口为压力进口,进口总压1,675,000 MPa,燃气出口为压力出口,出口压力1,200,000 MPa,冷却孔为压力进口,进口总压2,260,000 MPa,计算得到叶片温度分布见下图。
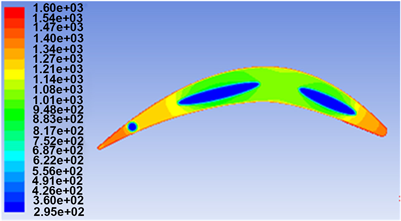
Figure 5. Temperature distribution at the blade root surface of 3-hole turbine cooling blade
图5. 3孔式涡轮冷却叶片叶根面温度分布
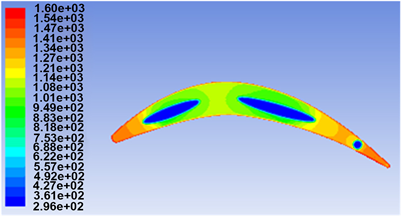
Figure 6. Temperature distribution on tip surface of 3-hole turbine cooling blades
图6. 3孔式涡轮冷却叶片叶顶面温度分布
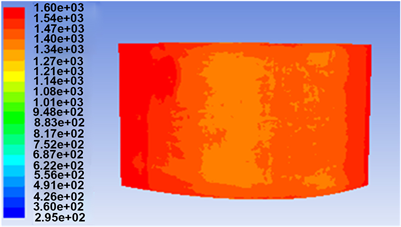
Figure 7. Suction surface temperature distribution of cooling blades of 3-hole turbine
图7. 3孔式涡轮冷却叶片吸力面温度分布
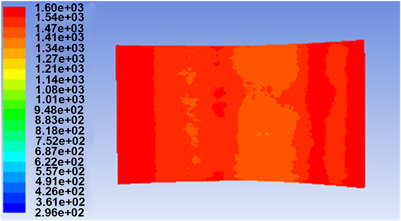
Figure 8. Pressure surface temperature distribution of 3-hole turbine cooling blades
图8. 3孔式涡轮冷却叶片压力面温度分布
通过对3孔式涡轮叶片温度场分布图5进行分析发现,3孔式冷却结构给叶片内部带来显著的冷却降温,沿叶片前缘至尾缘方向1号椭圆冷却孔和2号冷却孔给冷却叶片带来了极为明显的冷却降温作用,两孔周围辐射出一大片低温区域温度最高不超过1010 K,相比较1,2冷却孔的冷却效果,3号孔冷却效果要逊色很多,对周围很近小部分区域的冷却效果明显稍远的区域冷却效果偏弱,这充分说明,冷却孔体积的增大能够提升叶片的冷却效果;各个冷却孔之间区域温度逐步回升,尤其是2号孔和3号孔之间区域温度上升最为明显,这是由于冷却孔之间区域内不存在冷却气流且其它冷气源对这一区域沿距离梯度增加辐射力度有逐渐减弱所致。图5和图6涡轮冷却叶片叶根面与叶顶面温度分布图对比发现,叶片叶根面处的温度要明显低于叶顶面。
对涡轮冷却叶片吸力面和压力面温度分布图7、图8进行分析发现,涡轮叶片前后缘处的温度偏高,前后缘之间的区域温度明显偏低,前缘最先受到高温燃气的冲击灼烧一般容易损坏,可以看到靠近前缘区域的1号椭圆冷却孔给此区域带来了显著降温温度维持在1400 K以下,充分说明1号冷却孔对叶片前缘冷却作用较大,叶片尾缘区域温度1470 K左右是叶片所有部位最高的,这是由于靠近尾缘区域附近冷却气流流量小且受到外部高温燃气尾缘涡流影响冷却效果显著下降的缘故。
4. 对不同结构涡轮冷却叶片温度分布综合对比分析
通过对两组不同冷却结构涡轮冷却叶片温度分布特性进行研究发现,3孔式涡轮冷却叶片内部温度主要维持在1010 K,叶片表面温度整体约保持在1340 K,9孔式涡轮冷却叶片内部温度主要维持在1180 K,叶片表面温度整体约保持在1380 K附近,3孔式涡轮叶片整体冷却降温效果明显优于9孔式涡轮冷却叶片;冷却孔体积的增大能够显著提高涡轮冷却叶片冷却降温效果,3孔式涡轮冷却叶片的1、2号冷却孔的体积要远大于9孔式涡轮冷却叶片任何一个孔,其给叶片内部带来的实际冷却降温效果明显优于9孔式涡轮冷却叶片任何一个冷却孔,就9孔式涡轮冷却叶片温度分布来看,随着圆柱式冷却孔半径逐渐增大,冷却效果也越加显著,尤其是叶片中间半径最大的4、5、6号冷却孔带来了包围三孔区域的一大片低温区。
5. 结论
本文对两种不同冷却结构的涡轮叶片温度分布进行研究,发现不同冷却孔结构使涡轮叶片在工作环境下的冷却降温效果差别很大,总结如下:
1) 3孔式涡轮叶片整体冷却降温效果明显优于9孔式涡轮冷却叶片。3孔式涡轮冷却叶片内部及表面温度分布显著低于9孔式涡轮叶片,有利于提高工作状态下叶片的力学性能。
2) 随着圆柱冷却孔半径逐步增大,涡轮冷却叶片冷却降温效果不断提升。
3) 冷却孔体积增大可以改善叶片冷却效果。涡轮叶片冷却孔体积增大使得冷却孔内气体流量增大进而提升叶片的冷却效果并提高叶片的力学性能。