1. 引言
桥梁的耐久性预测是减少事故发生的有效措施。处于海洋环境中的钢筋混凝土结构,由于海风、海雾中的氯离子直接渗入混凝土并到达钢筋表面,形成原电池破坏金属表面钝化膜,使钢筋产生多种氧化铁导致锈蚀 [1] [2] [3] [4] 。目前构建的常规计算模型无论是锈蚀度的、还是力学性能计算模型都几乎是在不受力状态下给出的,而在长期载荷下,应力会导致结构变形和应力分布不均,影响建筑使用寿命,也未添加应力腐蚀因子,显然与实际情况不符。桥梁钢筋腐蚀前期以抗弯失效为主,后期以抗剪失效为主,加速混凝土保护层失效,加大钢筋腐蚀速率 [5] [6] [7] 。由此得出的计算结果,与实际桥梁存在着较大的差异,无法给耐久性预测提供有效的科学支撑。
由于混凝土结构内部钢筋锈蚀程度受外界影响因素颇多而且相当复杂,特别是锈蚀后钢筋其力学性能退化情况受到内、外因综合因素的影响 [8] [9] ,所以本文模拟了实际桥梁的腐蚀环境,并使钢筋在受力的状态下进行锈蚀试验(用加力架固定钢筋,用液压泵给钢筋试件预加力并做好防腐措施)。基于电化学原理的检测方法可以得到定量的检测结果,但由于仪器受外界因素干扰较大,适用于实验室中的加速模拟实验 [10] ,电化学方法包括半电池电位法、电阻率法、恒流脉冲、直流线性极化电阻法等。线性极化法是钢筋无损量化检测的有效手段 [11] [12] 。故本实验采取线性极化法进行为期两个月的电化学检测,并对锈蚀后钢筋做了力学性能测试。通过试验初步揭示出受力钢筋的锈蚀度与力学性能退化规律。
2. 试验材料与方法
2.1. 实验材料
钢筋材料:采用型号为HRB400E的钢筋,弹性模量E = 2.00 × 105 MPa。钢筋锈蚀试件长度为1.2 m,直径Φ20 mm,(公称面积A = 314.20 mm2,材料型号HRB400)。
2.2. 加力辅助设备
1) 加力设备:HTS-PHS150-2400型号手动泵,HTS010180STD型M18螺栓拉拔器(挪威产品),液压面积为1516 mm²,最大载荷:228 kN。
2) HTS-PHS-2段手压泵:REHOBOT 2段PHS手压泵标配一个压力表。
3) 测力仪器与称重测力装置:EVT-14TP-20T垫圈式压力传感器,量程200 kN。EVT-800 A显示仪表。
4) 加力架:经过综合考虑及腐蚀试验的可实施性,采用H型钢两端焊接开孔厚钢板做加力架,根据可移动性初步拟定加力架长1.2 m,工字钢采用20b (标号Q235),两端焊接钢板厚20 mm (平面尺寸200 mm × 160 mm)。H型钢拟采用150 × 150 × 7 × 10型(标号Q235),两端焊接钢板厚20 mm (平面尺寸200 mm × 160 mm)。
5) 耐腐蚀实验槽:采用壁厚为10 mm的工程塑料制作,内部高25 cm,长150 cm,宽80 cm。
6) CS电化学工作站:本次试验用到的仪器是CorrTest电化学测试系统包括CS系列电化学工作站(恒电位/恒电流仪)和相应的CorrTestTM控制软件for windows98/2000/XP。
7) 钢筋力学性能试验机:电子拉力试验机可以对金属材料进行拉伸(检测出其屈服强度、极限强度),弯曲、冲击以及硬度等力学性能测试。本试验想通过力学性能退化规律来印证锈蚀度与受力大小的关系。
2.3. 实验过程
1) 钢筋预加力试验,确定各应力水平的拉拔控制力。对钢筋进行表面处理,清除钢筋表面的油污与杂质。
2) 加力架预先做好防腐处理,最大程度保证钢筋构件的独立并且绝缘。防止钢筋构件与加力架接触,导致实验结果的不准确。
3) 在做好绝缘工作后,在加力架上张拉锚固试验钢筋,在锚固钢筋之前,在加力架两侧加绝缘垫片并利用拉拔仪和手动泵在加力架上对实验钢筋加力,分别加33 Mpa,67 Mpa,100 Mpa,150 Mpa,同一锈蚀度的试件锚固在同一加力架上,测量张拉应力,不满足要求重新拉拔锚固定;对不同应力水平的钢筋做永久标记。
4) 在保证绝缘的情况下,将加力架放入快速腐蚀液内进行腐蚀,注意腐蚀液槽要盖盖板封闭,避免盐酸挥发,最后将三电极安装在CS电化学工作站上。
5) 将试件与加力架一同放入腐蚀试验槽后,计算加入浓盐酸的体积。加入浓盐酸后迅速搅拌使其均匀混合,然后用笔试酸度计检测pH采用非受力钢筋做腐蚀前期试验,建立各种锈蚀测量方法测量数据与钢筋腐蚀程度的关系曲线。
6) 使用CS电化学工作站,用动电位扫描的方法按一定的时间间隔测量试验钢筋的腐蚀情况,记录测量数据;达到预期腐蚀要求的钢筋终止腐蚀,按力学性能测试的试件要求及微观分析的试件要求,分别切割截取试件,并预留验证腐蚀度试件。力学试验试件应留有适度的余量。
7) 试件力学性能测试及腐蚀试件微观结构检测分析。
3. 试验分析
3.1. 受力钢筋抗锈蚀性能随时间变化规律
自腐蚀电位能直观的表明腐蚀情况,当开路电位中测得的自腐蚀电位稳定后(见下图1)就可以通过极化曲线中测得自腐蚀电流密度来判断腐蚀速率。达到量化的条件自腐蚀电流密度表征腐蚀速率,腐蚀电流密度越大,腐蚀速率越大。当腐蚀电流密度 < 0.1 μA/cm2时,钢筋属于不腐蚀状态;腐蚀电流密度 > 1 μA/cm2时钢筋处于高腐蚀状态 [13] [14] 。
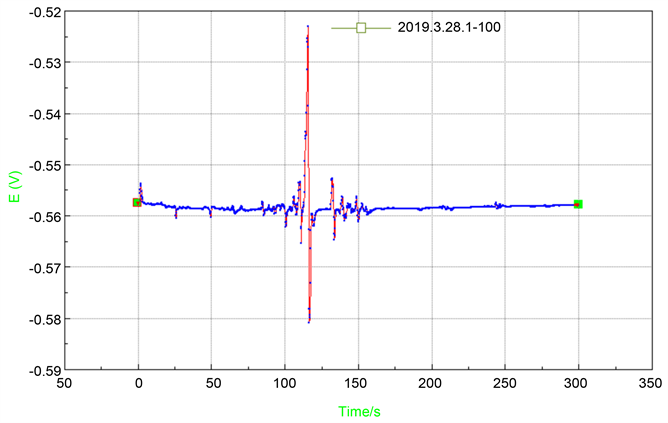
Figure 1. Stable from the corrosion potential
图1. 自腐蚀电位呈稳定状态
根据采集的数据,使用“CS Studio5”对实验数据进行处理整合,并使用“OriginPro 8”软件对图像进行优化处理绘制出如下所示的4组试件随时间变化的极化曲线图,以1号池受力为33 Mpa的钢筋构件为例,得到如图2所示信息。
通过数据的分析大致可定性判断:在前12天里,腐蚀溶液槽中的受力钢筋试件基本处于钝化状态,但是测得的腐蚀电流密度也在变大,表明腐蚀性离子正在缓慢进入受力钢筋试件中;在第16天后进入低腐蚀状态,并逐渐加剧,第18天后检测试件逐步进入中度腐蚀状态。
由图可知高浓度盐酸溶液中钢筋混凝构件在各个时间点所测得的极化曲线较为分散,且从表中也可以看出,腐蚀电位都是向负电位移动,腐蚀电位整体负移0.11 V,腐蚀量较大。
观察图3可以发现腐蚀电流密度和腐蚀电流速率两者的变化趋势一致,即在前期数值都是逐渐增大,随后便大幅度增加,符合拟合计算后两评价参数指标呈现出正相关变化的情况。参照腐蚀电流密度与腐蚀情况的对应关系,可定性判断出浸泡在高浓度盐酸溶液中钢筋构件在12天时就已步入低腐蚀状态,表明前期钝化过程结束,并且腐蚀性离子已经进入钢筋内部,与混凝土内部空隙中的物质共同作用,对钢筋产生前期腐蚀;而后在20天后测得随着腐蚀性离子的不断侵入,腐蚀电流密度和腐蚀速率都有一定幅度地变大。
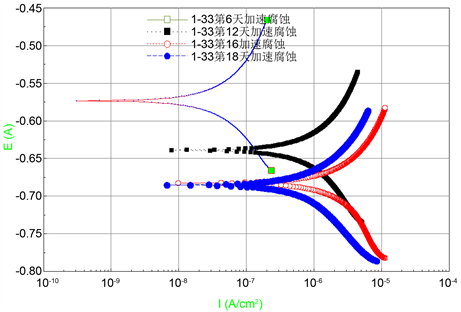
Figure 2. Polarization curve of 33 Mpa stressed steel bar with time in hydrochloric acid solution of pH = 3
图2. 33 Mpa的受力钢筋在pH = 3的盐酸溶液中随时间变化的极化曲线
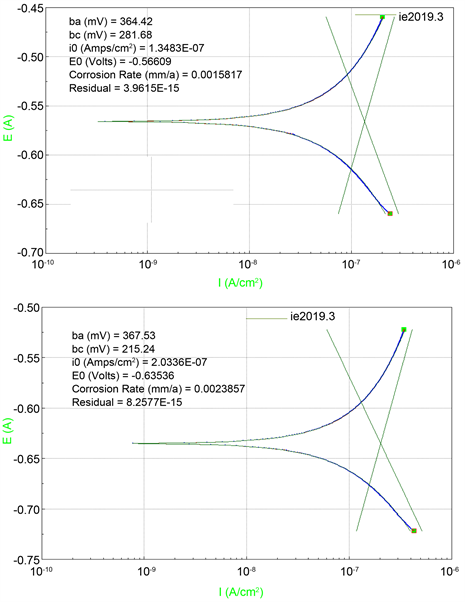
Figure 3. Polarization curve (the upper is rust until the 6th day, the next is the rust until the 12th day)
图3. 极化曲线(上为锈蚀进行至第6天,下为锈蚀进行至第12天)
所以,得到结论腐蚀电流密度icorr越大表明腐蚀越快,根据上图可知腐蚀电流密度值icorr所示0.13483 μA/cm2 (第六天)增长到0.20336 μA/cm2 (第十二天)呈现出逐步增大的变化趋势。
通过腐蚀电流密度可得到腐蚀速率值CR,它可以更加直观的表示钢筋构件在盐酸溶液中的腐蚀速度的快慢,由上图可知浸泡在盐酸溶液中的钢筋试件的腐蚀速率随天数的增长逐渐变大。表明了钢筋构件的锈蚀是循序渐进的,也是逐渐变大的。
3.2. 应力大小对受力钢筋锈蚀度的影响
根据采集的数据,使用“OriginPro 8”软件绘制出如下所示的随时间变化的极化曲线图,以进行至第25天的2#腐蚀溶液槽中的33 Mpa,67 Mpa,100 Mpa,150 Mpa的钢筋构件为例(溶液pH = 3),得到以下信息(见表1,图4)。
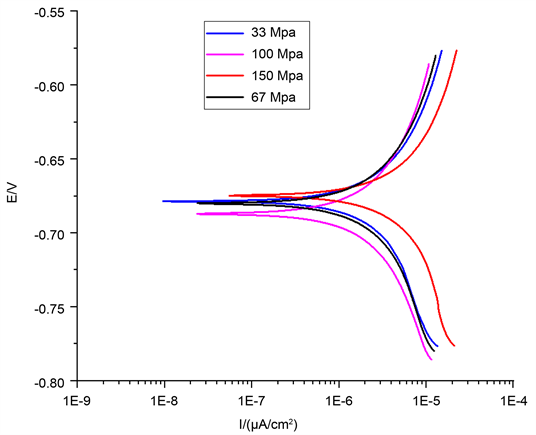
Figure 4. Polarization curve of steel specimens with different stresses in time in a hydrochloric acid solution of pH = 3
图4. 受不同应力的钢筋试件在pH = 3的盐酸溶液中随时间变化的极化曲线
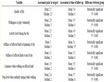
Table 1. Electrochemical parameters corresponding to each stressed steel bar
表1. 各受力钢筋所对应的电化学参数
上图为在同一时间测得的极化曲线,由表1可以发现浸泡在pH = 3的盐酸溶液中预加不同应力的钢筋试件(33 Mpa, 67 Mpa, 100 Mpa, 150 Mpa),腐蚀电流密度方面:各钢筋试件的腐蚀电流密度随受力增大而增大。腐蚀电位方面:虽然150 Mpa的钢筋试件的腐蚀电位有所上升,但大体上也呈现出下降趋势,符合预期结果,造成这种结果的原因可能是因为腐蚀试验体系过大,不能保证所有的腐蚀电极与参比电极的电阻都一样大小。从最直观的腐蚀速率方面来看,依旧符合,受力越大,腐蚀速率越大的规律。结合图4发现随着腐蚀程度的加深,其极化曲线塔菲尔区外推的交点也逐渐向右侧移动,也就是说,腐蚀电流密度随应力的增大而逐渐增大。
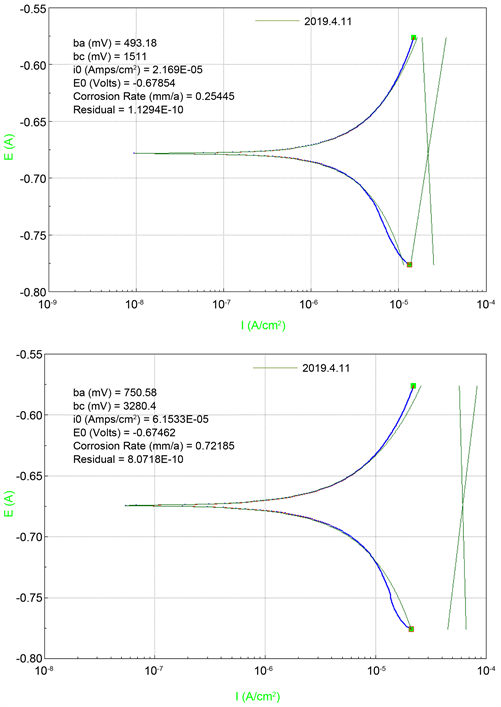
Figure 5. Electrochemical detection results of various stress bars
图5. 各应力钢筋电化学检测结果
具体来说:由上图5可以发现,从33 Mpa到150 Mpa,它们的腐蚀电流密度从0.2169 μA/cm2增长到0.6234 μA/cm2,33 Mpa、67 Mpa、100 Mpa处于低腐蚀状态,但100 Mpa已接近中等腐蚀状态的边缘。150 Mpa也即将进入高腐蚀状态。在整个检测过程中,虽然67 Mpa与100 Mpa的腐蚀电流密度非常接近,但总体趋势与预期结果相符。
结论:根据塔菲尔区直线外推的交点的横坐标,对应为腐蚀电流密度,腐蚀电流密度越小越好,所以耐腐蚀性能从好到差依次为蓝、黑、粉、红,即33 Mpa,67 Mpa,100 Mpa,150 Mpa。基本符合实际规律,受力越大的钢筋试件,腐蚀电流密度越大,腐蚀速率越大,耐腐蚀性也就越差。
4. 结论
桥梁内部钢筋发生锈蚀并继续发展下去,会引起桥梁的其它病害,降低桥梁的通行能力,降低桥梁的耐久性,更严重者,导致重大垮塌事故,造成财产损失及人身安全事故。其它工程行业也存在同样的问题,金属材料的腐蚀问题是工程界亟需研究与解决的问题。因此本论文在实验室进行模拟实际桥梁钢筋试件的加速腐蚀实验,用电化学的方法检测钢筋试件的腐蚀电流密度、腐蚀电位、阻抗以及腐蚀速率,以此建立一套锈蚀度评价分级标准来预测桥梁的耐久性能,并结合力学性能实验以达到理论上的精确预测。通过校内分阶段进行的模拟试验以及力学性能试验得出以下结论:
1) 实验前对几种电化学检测设备特点进行了对比分析。认为线性极化法给出的钢筋锈蚀速率相对可靠,且简便易行,目前较适合混凝土中钢筋锈蚀速率的现场检测。通过腐蚀电流密度可得到腐蚀速率值CR,它可以更加直观的表示钢筋构件在盐酸溶液中的腐蚀速度的快慢,由上图可知浸泡在盐酸溶液中的钢筋试件的腐蚀速率与腐蚀天数的增长成正相关。
2) 钢筋的加速模拟实验表明,随着钢筋受力的不断增大,钢筋的锈蚀速率也在增大。钢筋的加速模拟锈蚀实验表明,预加应力越大钢筋的腐蚀速率越大。从腐蚀时间上来看,腐蚀速率在前期上升随后有小幅的下降后来再次上升,这是因为在腐蚀初期,大量的腐蚀物阻碍了腐蚀性离子侵入钢筋表层,造成对钢筋腐蚀的阻碍作用;随着时间的增长,腐蚀产物溶解,使得大量腐蚀性离子与钢筋发生化学反应,腐蚀速率再次增大。
通过试验研究所得到的应力状态对钢筋锈蚀状态的影响规律及建立的锈蚀钢筋力学性能退化规律模型,可以为钢筋混凝土及预应力混凝土桥梁的现实状况研判、养护维修、寿命预测提供科学的依据,对提高桥梁的耐久性具有现实意义及实用价值。
致谢
1) 交通运输部公路科学研究所科技创新专项资金项目,项目名称:钢筋锈蚀的评价方法、标准及力学性能退化模型;项目编号:2018-E0011。2) 北京高等学校高水平人才交叉培养计划项目:基于受力钢筋电化学信号的锈蚀度与力学性能理论计算模型的实际桥梁应用及分级评价;项目编号:2019100170416。