1. 前言
由于中高合金钢坯/锭内部应力大,因此该类合金钢生产过程中钢锭裂纹、切割面裂纹、钢锭与钢板防炸裂、探伤、高低倍组织将是生产过程中控制的难点和重点。为了避免炸裂及裂纹产生,同时为了保证钢锭内部质量,一般情况下,采用常规铸铁模生产,好处是锭模散热慢内部质量好且锭模保温能够释放钢锭内部应力。
近期,我公司与客户甲签订一单250 mm规格F5合同,其F5要求合金含量达6.5%~7.4%,属于中合金钢,受合同量限制,只能采用我公司自主知识产权的水冷模铸锭生产,而我公司之前未采用水冷模生产合金含量高的钢种,对我公司来说,是一个极大的挑战。
根据协议要求,该合同保化学成分、保S2E2探伤,保高低倍组织,其化学成分要求如表1:
2. 生产总体情况概述
本钢种根据合同技术协议要求:交货状态为热轧两切,保化学成分,保S2E2探伤。采用模铸生产,锭型为46.4 t常规水冷模,规格为250 * (2000 - 2300) * L,成材率82%。
围绕本钢种生产的难点和重点,生产过程需重点做好以下几方面控制:
a. 冶炼环节:钢水精炼夹杂控制、B元素控制、H含量控制;
b. 钢锭管理:及时堆冷,带温清理,清理大于面积50%;
c. 钢锭加热:带温装炉,慢速升温,延长闷钢;
d. 轧制堆冷:低温、高速、大压下,高温下线,做好缓冷;
e. 钢板切割:带温切割,切后立即转运;
f. 去应力:采用高温退火,以消除内部应力。
通过以上各环节的控制,最终实现了:冶炼成分全部内控;N、H、O、S、P大五有害元素含量小于150 ppm;钢板外检合格率100%;探伤合格率100%;两张钢板采用火焰切割的方式切为6块,所有切割面未有异常。最终全部顺利入库发货。
3. F5生产关键技术和工艺要点
3.1. 模铸冶炼
本钢种冶炼工艺流程:铁水(KR脱硫)→转炉(氩站)→VD真空氧脱碳 [1] →LF精炼→VD真空处理→模铸浇注。
3.1.1. VD真空氧脱碳
降低钢水氧含量是控制钢水各种内生夹杂的关键,同时根据本钢种特点,必须控制钢水初始C含量在一个较低的水平。因此在本钢种生产时采用了“VD真空氧脱碳”工艺。其原理如下:
钢水中[C]、[O]反应公式如下:
(1)
(2)
由公式(1)和(2)得:
(3)
(4)
和
分别表示C和O的浓度,k为平衡常数,T为钢水温度,Pco,表示真空中CO分压。
由公式(3)可以看出,平衡常数仅与钢水温度T有关,在一定温度下,减少CO的分压Pco,可以极大的降低C、O深度积
。在降低Pco的同时,增大[o]可极大的降低钢水中碳的浓度。
利用以上原理,转炉出钢后不进行钢水脱氧和合金化,直接以合适的温度进入VD进行真空处理,根据我厂生产数据,可将钢水碳含量控制到0.01%以下。
3.1.2. C成分控制
本炉理论合金加入量104 kg/t,LF精炼纯加热时间60分钟,合金增碳及加热增碳约0.09~0.11%。因此C成分控制是难点,LF精炼一加热碳含量必须≤0.03%,冶炼时间需控制在2 h以内。
实际工艺执行情况,VD残氧脱碳保压10分钟,LF精炼一加热碳含量0.03%,过程配加碳粉10 kg,纯加热时间67 min,成品碳0.13%。成品成分如表2:
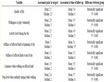
Table 2. Finished product analysis of F5
表2. F5成品分析
3.1.3. 精炼造渣
钢水脱氧值是精炼造好白渣的关键,为此在VD残氧脱碳的同时,根据工艺要求补加碳粉若干,以达到钢水C、O同时去除(以CO气体的形式排出钢水)的效果。在此基础上,LF精炼过程中增加前期脱氧剂、石灰的加入量,以尽快造出粘稠合适的泡沫性白渣。二加热阶段醮渣变白,白渣保持时间满足工艺要求。
3.1.4. VD脱气
钢水H含量高会加剧钢锭/钢板的裂纹敏感性,本炉要求VD产前试车确认,保压标准按照H含量1.3 ppm以下控制;
实际预抽6 min,保压20分钟,H含量测定值和破空温度全部一次达到工艺要求。
3.2. 钢锭管理
3.2.1. 钢锭堆冷
本炉钢锭严格按照工艺要求,浇毕10 h脱模,脱模后1 h内转之缓冷坑,采用集中堆放、上部热锭覆盖的方式堆冷;钢锭在装炉前始终保持带温集中堆放状态。
3.2.2. 钢锭清理
本炉两支钢锭在堆冷12小时后于安排热清,清理温度约300℃;对于裂纹敏感区采取的清理方式为:中部通清,清理面积不小于50%。清理过程中仅1支钢锭单面头部存在20 mm * 300 mm裂纹,清理结果符合要求。清理情况见下图1和图2:
3.3. 钢锭加热
由于Cr含量高达到5%,加热最高温度需控制,按照现行III组钢工艺执行,对最高加热温度和钢锭表面温度进行了工艺优化。具体加热曲线如下图3:
3.4. 钢锭轧制
钢锭采用热轧的轧制方式,执行“高温、低速、大压下 [2] ”工艺,过除鳞箱后表面一次铁皮情况良好,开轧温度均>1020℃,后三道次压下量按照50 mm,轧制平均电流6000~6500 A,终轧温度 > 980℃,轧制热态公差按照4.5~5.0 mm控制;
为保证钢板拆垛后具备高温火切条件,轧后采用夹钳高温下线,集中堆冷48 h后视钢板温度进行拆垛切割。
3.5. 带温切割
根据我厂生产实际,因缓冷和切割工艺执行不当,已造成多起碳素钢、铬钼钢钢锭、钢板炸裂及切割面出现延时裂纹,从而对生产和合同履约造成了重大影响。因此针对本钢种必须强化带温切割和堆冷工艺。
待钢板堆冷到达时间后,对其进行拆垛,钢板实际测温150℃~180℃,满足工艺要求,之后立即转至火切场进行切割处理,切割时控制切割方式,限定切割温度和切割时间。同时提前做好下步安排,切割完毕后1 h内转至下道工序。
3.6. 高温退火
退火工艺:钢板150℃~200℃进台车炉,在560℃~580℃恒温保持10 h,然后转缓冷坑缓冷至50℃左右拆垛。堆冷过程中做好监控,禁止倒垛和提前拆垛。
3.7. 检测环节
3.7.1. 探伤
钢板按照EN10160-1999探伤标准执行,探伤结果全部满足S2E2要求,合格率100%。
3.7.2. 外检
外检6块,初检合格6块,最终正品发货6块,正品率100%。
3.7.3. 低倍情况
根据GB/T 226-2015要求,对250 mm钢板进行检测,结果如下表3:
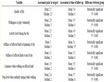
Table 3. Non-destructive testing table for steel plate
表3. 钢板探伤检测情况表
3.7.4. 成分偏析分析
1) 取样分析
为进一步分析采用水冷模铸生产中合金钢板成分偏析情况,为性能稳定性提供参考,在钢板不同部位进行了取样和成分分析,取样情况如图4:
注:尾部宽1/2取样,厚度方向从上到下编号1-2-3; 尾部边部取样,厚度方向从上到下编号4-5-6; 头部宽1/2取样,厚度方向从上到下编号7-8-9; 头部边部取样,厚度方向从上到下编号10-11-12。
Figure 4. Schematic diagram of sampling position of steel plate
图4. 钢板取样位置示意图
采用M10直读光谱分析仪对各位置取样进行光谱成分分析,分析结果如表4:
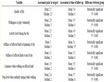
Table 4. Spectral component analysis
表4. 光谱成分分析
注:红色代表高值,绿色代表低值。
按照以下公式:
(5)
(6)
k表示分配系数,k0表示分配比,C1表示任意处某成分浓度,C0表示熔炼成分浓度。
最终算得各成分偏析系数如表5:
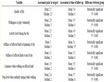
Table 5. Segregation coefficients of elements in F5
表5. F5各元素偏析系数
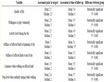
Table 6. Segregation coefficients of different elements in iron [3]
表6. 不同元素在铁中的偏析系数 [3]
2) 结果分析
根据取样光谱分析情况,可得出以下结果:
a. 成分偏析相对较大元素为C、P、Als (浇钢未采取保护浇铸,浇钢过程钢水吸氧,导致Als降低);
b. 正偏析较大的部分出现在钢板头部厚1/2处;负偏析较大的部分多出现在钢板尾部厚1/2处;整体偏析情况符合模铸法钢锭偏板情况分布趋势;
c. 铬元素含量为4.86%,其偏析系数为0.04%,偏析程度较低;
d. 采用水冷模铸生产,钢板整体成分相对均匀,与表6各元素分配系数相比,各成分偏析都要明显优于参考数据。
3) 偏析原理分析
a. 依靠铜板通水强制冷却,促使锭模内的钢水尽快消除过热度,减轻钢锭发达的柱状晶,确保钢锭中心组织较致密,同时大大减轻中心偏析的影响;
b. 采用大的宽厚比,以增加钢锭的比表面积,从而增大冷却强度,细化晶粒,减轻疏松和偏析,从而提高本体凝固过程的凝固率;
c. 为保证钢锭本体的充分补缩,防止二次缩孔和中心疏松产生。采用钢锭本体厚度方向上的较大锥度以形成喇叭口的补缩通道,使液相穴前沿呈V型,考虑到水冷铜板的加工制作难度,取钢锭大面锥度为0.6%~0.8%;
d. 就现场生产实际而言,一般采取高温慢、低温快、开浇稳、跟流准,到模帽接口减流,保证流不散,圆流浇铸的原则。
4. 结论
通过以上分析,得出以下结论:
1) 可采用“转炉 + VD”生产低碳中高合金钢;
2) 通过工艺优化和控制,利用我厂现在设备可以生产250~350 mm保国标探伤超厚板;
3) 通过合适的工艺控制,可以利用传统火焰切割对高碳、高合金钢进行切割;
4) 我厂水冷模铸生产的产品具有成分偏析小、内部质量优良等优势,能满足大特厚度钢板的研发和量产需求。