1. 引言
低碳铝镇静钢多为热轧向钢种,对成分硅的要求比较严格,通常硅含量要控制到0.03%以下,当硅含量超过0.03%时,钢材屈服强度和抗拉强度上升,严重影响钢材冲压性能 [1]。湛江钢铁炼钢厂低碳铝镇静钢工艺流程为KR→LD→LATS→CC。正常情况下,转炉吹炼结束后,钢水中硅被氧化至微量,完全符合钢种要求。但KR故障或定修时,转炉出钢后钢水需要进LF炉脱硫,对应工艺流程为LD→LF→CC。LF处理过程中,渣中(SiO2)会被还原进入钢水,导致钢水硅含量增加,2018年以来数次出现硅含量超标,改钢降级的问题。因此,有必要对影响LF炉钢水回硅的因素进行分析,稳定控制钢水硅含量。
转炉采用前后挡渣或留钢留渣操作,减少炉后下渣量 [2] 可以从根本上减少硅的还原,但是前后挡渣操作会严重缩短转炉滑板使用寿命,影响生产节奏;留钢–留渣操作,留钢量无法稳定控制,会对炉产量的稳定造成一定的负面影响。因此,本文主要分析LF炉过程参数控制对钢水回硅量的影响,通过改变LF炉造渣方法,加强温度、过程铝含量及处理时间的控制,达到降低LF炉处理过程钢水回硅量得目的。
2. LF炉回硅分析
LF炉处理过程中,钢水回硅反应方程式如下所示 [3] :
(1)
(2)
(3)
式中:
——钢液中硅的质量分数;
——标态平衡常数;
——渣中(SiO2)活度;
——渣中(Al2O3)活度;
——钢液中硅的活度系数;
——钢液中铝的活度系数。
湛江钢铁未脱硫铁水,转炉吹炼结束后钢水硫含量范围为0.015%~0.040%,而低碳铝镇静钢,由于钢种的不同,硫含量上限在0.006%~0.020%之间,LF炉脱硫前后钢液及炉渣成分如表1和表2所示。
由于LF炉处理终钢水硅和铝含量较低,钢液中硅活度系数
和铝活度系数
均取1,渣中(SiO2)和(Al2O3)活度可由熔渣等活度图确定 [4]。将炉次结束温度、钢液及炉渣成分带入(2)~(3)式计算可得,LF炉处理结束时的钢水硅含量与平衡硅含量的关系如图1所示。从图1可知,LF炉处理结束时,钢液回硅反应远未达到平衡状态,实际硅含量约为平衡硅含量的三分之一,即LF炉处理结束后,渣中(SiO2)仍然具有强烈的还原趋势,在适当的反应条件下,钢水硅含量仍然可能进一步增加 [5]。同时由(SiO2)-[Al]反应方程式可知:降低渣中(SiO2)含量或降低钢液铝含量均可减少硅的还原,增加渣中(Al2O3)含量或提高钢水温度也可以一定程度抑制硅还原反应的发生。
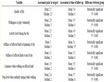
Table 1. Temperature and composition change of low carbon steel before and after LF desulfurization
表1. 低碳钢LF炉脱硫前后钢水温度及成分变化
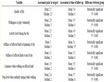
Table 2. Slag composition change before and after LF treatment of low carbon steel
表2. 低碳钢LF炉处理前后炉渣成分变化

Figure 1. Relationship between actual silicon content and calculation balance silicon content of LF treatment
图1. LF炉处理结束实际硅含量与平衡硅含量的关系
3. 过程铝含量对硅还原的影响
LF炉处理过程中,必须保证钢液铝含量降低钢液及渣中氧,才能确保脱硫效果,但钢水铝含量增加,会促进渣中(SiO2)的还原,钢水回硅量增加。处理前渣中(SiO2)含量6.40%~12.5%,(Al2O3)含量29.5%~40.3%的条件下,过程铝含量与成品硅含量的关系如图2所示。
从图2可知,随着过程铝含量的增加,钢液硅含量呈增加的趋势。当过程铝低于0.03%时,成品硅可以稳定控制在0.03%以下;过程铝均高于0.07%时,基本所有炉次硅含量均在0.03%以上。为了降低钢液回硅量,过程铝应控制到0.03%以下,但研究表明 [6],铝含量低于0.02%时,渣–金硫分配比急剧降低,炉渣脱硫能力变差,铝含量在0.03%左右时,实际硫分配最佳,综合考虑脱硫效果和回硅量,LF炉脱硫过程铝目标可控制在0.02%~0.04%之间。

Figure 2. The effect of process aluminum content on silicon reversion
图2. LF处理过程铝对回硅的影响
4. 初始温度对硅还原的影响
温度LF炉最重要的参数之一,其对处理时间,化渣速度和脱硫速率有直接影响。在过程铝含量0.02%~0.04%的条件下,LF炉初始温度与钢水回硅量的关系如图3所示。
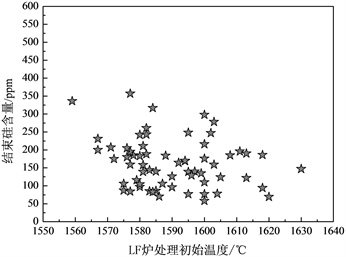
Figure 3. The effect of initial temperature of LF furnace on silicon reversion
图3. LF炉处理初始温度对回硅的影响
从图3可知,随着初始温度的增加,LF炉结束硅含量呈降低的趋势,硅含量超0.03%的炉次,初始温度均低于1580℃;初始温度高于1605℃时,硅含量可以稳定控制在0.025%以下。分析认为,随着初始温度的增加,化渣速度增快,脱硫速率增加,LF处理周期缩短,有效减少回硅量。从热力学的角度来看,由(2)式可知,提高温度一定程度上抑制了硅的还原,适当提高LF炉初始温度有利于降低钢水回硅量,综合考虑温度控制的可操作性及回硅量控制,LF进站初始温度可控制在1600℃ ± 10℃之间。
5. 辅料加入对硅还原的影响
湛江钢铁LF炉脱硫,采用铝铁和铝渣同步脱氧(铝铁脱钢水氧,铝渣脱渣中氧)。铝渣为成分以金属铝、Al2O3和CaO为主的球状辅料,其特点是铝含量高,密度小,直接加入渣中可迅速将渣里氧化铁和氧化锰还原,形成高还原性炉渣,实现钢水的快速脱硫和深脱硫。但是高还原性渣,容易导致钢水脱硫过深,远超低碳铝镇静钢要求,同时渣中(SiO2)更容易被还原,钢水硅含量增加。铝铁脱氧和铝渣脱氧回硅情况如图4所示。

Figure 4. The effect of deoxidation method on silicon reversion
图4. 脱氧方式对硅还原的影响
从图4可知,加铝渣炉次硅含量控制不稳定,波动较大,多个炉次硅含量在0.04%以上;铝铁脱氧炉次,硅含量波动较小,硅含量最高仅为0.035%,回硅量整体控制稳定。分析认为,铝铁比重大,投入后直接加到钢水中,脱完钢液中氧后,再以扩散脱氧的方式脱渣中氧,渣中全铁含量在3%左右,使炉渣保持一定弱氧化性,有效降低了硅的还原。铝铁脱氧,炉渣脱氧不完全,炉渣脱硫能力相对变差,但是低碳铝镇静钢本身对硫含量要求不高,完全可以满足钢种脱硫要求。
6. 改进后回硅情况
2018年1~12月,湛江钢铁LF炉生产低碳铝镇静钢149炉,硅高于0.03%炉数20炉,数次出现改钢降级的问题。通过将LF进站目标温度控制在1600℃ ± 10℃,过程铝含量控制到0.02%~0.04%,用铝铁代替铝渣脱渣中氧及缩短LF处理周期,目前LF回硅量可以稳定控制在0.03%以下,2019年1月至今,LF炉生产低碳钢27炉,硅含量低于0.03%炉数27炉,没有出现改钢降级的问题,具体回硅情况如图5所示。

Figure 5. Comparison of silicon content before and after optimization
图5. 改进前后回硅量对比
7. 结论
1) LF炉处理结束后,渣–金之间硅还原反应远没有达到平衡,渣中(SiO2)仍然可能被还原,钢水硅含量增加。
2) 随着过程铝含量的增加,回硅量增加。在LF炉处理前硅含量 ≤ 12.5%时,过程铝含量低于0.03%时,有利于将回硅量控制在0.03%以下。随着LF炉初始温度的增加,化渣速度增快,脱硫速率增加,处理时间变短,钢水硅还原量降低。
3) 采用铝铁代替铝渣脱渣中氧,使炉渣保持一定的弱氧化性,可以满足低碳铝镇静钢脱硫要求的同时,有效降低钢水回硅量。
4) 渣中初始(SiO2)含量 ≤ 12.5%时,通过将LF炉初始温度控制在1600℃ ± 10℃,过程铝含量控制到0.02%~0.04%,采用铝铁代替铝渣脱氧,同时缩短LF炉处理时间,可以将低碳铝镇静钢硅含量稳定控制到0.03%以下。
NOTES
*通讯作者。