1. 引言
1.1. 多孔金属研究进展
在上个世纪80年代后期,一种新型金属材料因为内部均匀地分布着大小相近的孔隙而迅速吸引了大批研究人员的目光,并且得到快速发展,这种新型金属材料就是金属多孔材料 [1]。通常,结构材料的研究人员视这些孔洞是材料内部的缺陷,大部分的科研人员在材料制备处理过程中,都会努力地把孔洞数量尽可能降到最低 [2]。然而,多孔材料大量地分布于自然界中,这个现象说明,存在大量孔洞的材料,可以在相对较轻的质量下,拥有良好的物理性能和特殊功能的 [3]。
早期,铜和镍常被用来制备金属多孔材料,上世纪80年代,随着工艺的进步和对材料的不断开发,研究人员成功制备出多孔镍,多孔钛,随后,有着特殊用途的多孔银、多孔钨、多孔钽及难熔金属化合物多孔材料也都相继涌现,多孔材料的研究迎来快速发展的时代 [4]。由于金属多孔材料中孔隙的大量存在,使其与致密材料相比具有独特的物理化学性能。金属多孔材料具备优异的物理性能,比如其拥有较小的密度的同时,又具有较大刚度和比表面积,并且具有一定的电磁屏蔽、消音降噪和吸能减振能力;此外,金属多孔材料还具有较强的热量传递能力和较好的渗透性等优点。
当金属多孔材料的孔径达到纳米级时,其性能得到进一步的提升。纳米多孔金属材料具有金属高强度、良好的导热性和导电性的特性,以及多孔固体优秀的综合性能,如比重小、比表面积大、节省原料 [5]。纳米多孔金属材料是纳米多孔材料的一个重要分支,指的是内部均匀地分布着大小相近的孔隙,其孔径大小为纳米级的金属多孔材料。纳米级孔径使得纳米多孔铜在具有多孔金属材料的特性的同时,还具备了一定的纳米材料的特性,如小尺寸效应、量子尺寸效应和表面效应 [6]。
传统纳米多孔材料制备工艺较为困难,成本高昂,而纳米铜的出现改变了这样的局面,由于展现出优异的物理和化学性能,并且价格低廉,纳米多孔铜有望取代纳米多孔贵金属(如多孔金等),在催化、生物传感器、能源等领域展现巨大的应用潜力 [7]。
多孔铜是最常见的金属多孔材料之一,由于其具有较高的比表面积、较低的密度、较高的通透性、较强的耐蚀性和抗疲劳性以及结构灵活可调等一系列优点,使其在催化、分离、能源等领域中的应用受到了广泛的关注。多孔铜优异的物理力学性能,使其成为一种优秀的工程材料,当其空隙的大小达到纳米级时,多孔铜会展现出更好的力学性能,同时拥有更大的比表面积,在工业催化、分子筛、高效电极材料、太阳能电池等领域得到广泛应用,具有很好的开发前景 [8]。
为了得到各种不同结构和性能的多孔金属材料,针对不同金属,各种多孔材料的制备方法被接连提出,常见的有直接发泡法、气泡法。烧结法、精密铸造法和电沉积法等 [9]。而纳米多孔金属由于对孔径尺寸要求较高,目前采用的制备纳米多孔金属材料的方法主要有两种,分别是模板法和去合金化法两种。模板法具有工艺复杂、模板制备困难、模板结构受限制等缺点,使得模板法的应用与发展很大程度上受到限制。脱合金法,也称为选择性腐蚀,是利用合金中不同组分之间的化学活泼性差异,通过化学或者电化学方法有选择性地除去较为活泼的一个或者多个组分(有时称为贱组分),腐蚀过程中,在固液界面出现相分离,相对活泼的金属先溶解于溶液,剩余组分(也被称为贵组分)的原子扩散、聚集,形成二维簇,而被腐蚀的区域不断扩展,最终形成三维双连续的多孔金属 [10]。相比于模板法,脱合金化法制备纳米多孔金属材料的工艺过程简单,且可对纳米多孔金属材料的孔洞排列方式和孔径尺寸进行动态控制 [11]。因此本次实验采用脱合金化法制备纳米多孔铜。
1.2. 去合金化研究进展
20世纪中期,Pickering和Swann [12] 第一次用TEM去观察出现去合金现象的腐蚀之后的材料,发现材料中的纳米孔洞。1990年,Sieradzki和Newman [13] 首次提出用金属纳米多孔结构的概念,并将金属纳米多孔材料的制备方法——去合金化法申请专利。在随后的研究中心,两人在去合金化法制备金属纳米多孔材料的过程中,发现并提出了临界电位和组分阈值的概念。并且认为要使用去合金化法,前驱体合金必需满足两个条件,一是两种不同合金元素的原子比必须在某一范围内,二是两合金的电位差要足够大。2001年,Erlebacher [14] 等人的研究成果发布在Nature杂志上,他们通过硝酸腐蚀金银合金的前驱体,首次制得孔径大小为10纳米左右的多孔金。此外,Erlebacher等人还提出去合金化法中,多孔结构形成的动力学原理,既由于电位差的存在,较为活泼的金属会率先进入腐蚀液中,而较为稳定的金属原子将会在固液界面扩散,聚集,形成二维簇,而被腐蚀的区域不断扩展,最终形成三维双连续的多孔金属。并通过计算机模拟,结合其所作的实验,得出多孔金的微观纳米多孔结构。
除此之外,针对去合金化过程中,两种相互溶解的金属原子,在腐蚀过程中相互分离,并留下孔洞的微观现象,国内外的学者都提出不同的机制来解释。目前的机制主要有四种,包括体扩散机制,表面扩散机制,渗流机制和相分离机制 [15]。
其中,体扩散机制是由Pickering等 [16] 提出,认为合金内部原子的体扩散保证了去合金化腐蚀过程的进行。首先,金属表面被腐蚀的原子溶解后产生空位,产生浓度梯度,从而使空位往金属内部扩散,同时较活泼金属往金属表面扩散,腐蚀得以继续。
表面扩散机制由Forty等 [17] 提出,认为活泼金属溶解之后,合金内部失去平衡,而惰性金属通过表面扩散使得合金恢复平衡。合金表面活泼金属溶解的同时,惰性金属在表面聚集,表面能降低,从而变得有序。
渗流机制由Sieradzki等提出,其理论是基于表面扩散机制的,认为随着溶解进行,若合金中剩下的某一相的占比或者溶液中活泼金属的浓度达到某一值时,合金内部会产生活泼金属原子通道,而接下来的腐蚀既是沿着这些通道进行下去的。渗流机制可以解释腐蚀过程中的临界电位问题,也解释了活泼金属占比达到某一临界值才能形成连续孔洞的现象。
相分离机制是Erlebacher基于渗流机制提出的,认为惰性金属在固液界面处的相分离中获得驱动力从而扩散聚集在一起,形成二维簇。随着腐蚀的继续,表面积不断变大,从而产生孔洞。
目前,对于纳米多孔铜的制备,吕海波等使用磁控溅射沉积的方法,在玻璃片上合成Cu-Zr合金,并使用浓度为0.1 mol/L的HCl溶液对合金进行电化学腐蚀,成功制备出孔径大小约为500 nm的多孔铜。Hayes等使用去合金化法对Mn-Cu合金进行腐蚀,并得出多级尺寸的纳米多孔铜 [18]。
1.3. 放电等离子烧结(SPS)
由于去合金化后的产物会继承前驱体的部分结构,所以前驱体的制备十分重要。首先组成前驱体的合金元素一定要有较大的电位差,才能保证腐蚀的顺利进行。其次,前驱体最好由单项组织构成,腐蚀之后才能获得均匀的孔洞结构。最次,前驱体的组织成分应分布均匀,才能保证最终所得多孔材料孔隙分布均匀。
目前,前驱体合金主要由晶态和非晶态两种状态组成。制备非晶态前驱体,主要使用快速凝固和磁控溅射技术,得到厚度为微米级的薄膜。制备晶态前驱体,常见方法很多,如:磁控溅射法、熔融快焠法、粉末烧结法、热压烧结法 [19]、以及放电等离子烧结(Spark Plasma Sintering, SPS)技术等。其中,SPS烧结,一种能快速地烧结并能达到较高温度的烧结技术,是制备材料的一种常见技术。具有升温速度快,加热时间短,组织结构可控等优点 [20]。
等离子态是物质处于高温状态下或在特殊的激励状态下所表现出来的一种状态,是经由电离的准中性气体,由表现出集体行为的大量正负带电粒子和中性粒子组成。材料在一定的等离子气体氛围之内,通过气体放电产生的能量以及电子能量提供烧结的热量,使材料迅速升温到烧结温度,在一定的压力下烧结在一起,从而获得理想试样。
SPS烧结的工艺是将制备好的粉末装入模具,使用上下模冲对粉末施加压力,并对电极施加特定电源,模具内的粉末经过放电活化,热塑变形及随炉冷却后,获得致密的材料。烧结过程中,由于升温迅速,一方面晶粒孕育时间较短,从而抑制了晶粒长大,可得到晶粒较小的材料。另一方面,升温过快导致样品内外产生温度梯度,从而使材料内部组织结构不够均匀,且在加热时,样品容易开裂,为了防止试样开裂,可以通过预烧的处理使得部分致密化。
1.4. 研究内容
目前金属多孔材料的制备方法众多,却仍然面临着所得材料孔径较大的问题,成熟的制备工艺所得多孔铜孔径往往大于500 μm;而大部分研究制得纳米多孔铜却尺寸较小,其厚度往往小于100 μm。这使其使用场合受到限制,因此,制备孔隙较小且厚度较大的多孔铜具有重要意义。本文旨在探索SPS烧结法制备的Cu-Al合金前驱体,利用去合金化法,使用不同浓度HCl溶液作为腐蚀液,制备孔隙较小且分布均匀,尺寸较大的多孔铜的工艺参数。
由于以往的实验中,Cu-Al合金前驱体中Cu的占比为30 at%左右,本次实验采用15 at%的比例,试图得到孔隙率更大的多孔铜。并且,本次实验探索烧结压力及腐蚀液浓度对最终纳米多孔铜表面形貌和微观结构的影响,并试图找到合理的参数范围。
2. 实验方法及过程
2.1. 实验原料与设备
由铝铜二元合金相图可知,当铜原子占比在5 at%到30 at%之间时,温度低于548℃的情况下,会出现一个两相区。根据液相线548.2℃的温度,考虑到SPS烧结升温迅速,烧结温度应低于液相线温度150℃左右,选用400℃作为粉料的烧结温度。为了探索烧结压力对最终腐蚀后多孔铜微观形貌的影响,故分别选用10 Mpa、20 Mpa和30 Mpa三个不同压力对粉末进行烧结。为了探索不同腐蚀液浓度对最终腐蚀后多孔铜微观形貌的影响,分别选用0.5 mol/L、1.0 mol/L和1.5 mol/L三种不同浓度盐酸对样品进行腐蚀。
实验用行星式高能球磨机为南京球磨机厂生产的型号为HFG7-R75S2球磨机;放电等离子烧结仪购于日本住友石炭矿业株式会社生产,型号SPS320MKI;场发射扫描电子显微镜是由ESCAN生产,型号为MRA3,图1列出了实验中需要用到的相关设备。
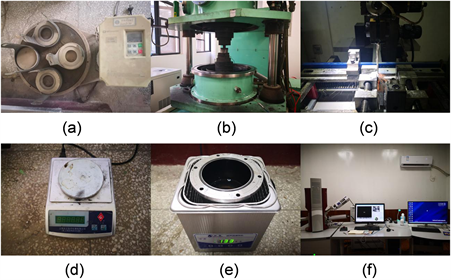
Figure 1. Experiment instruments. (a) Ball mill; (b) SPS instrument; (c) Linear cutting machine; (d) Electronic scale; (e) Ultrasonic cleaner; (f) Scanning electron microscope
图1. 实验仪器。(a) 行星式高能球磨机;(b) 放电等离子烧结仪;(c) 电火花线切割机床;(d) 电子秤;(e) 超声波清洗仪;(f) 扫描电子显微镜
2.2. 实验过程
2.2.1. 球磨混料
烧结粉末如果不均匀,会导致烧结后所得前驱体的组织和成分分布不均匀的情况,这会影响到前驱体的进一步腐蚀。因此,本次实验采用行星式高能球磨机进行粉料混合。
为了加快铜粉和铝粉的混合过程,以及获得更加细小均匀的粉料,选用直径为5 mm,密度为5.85 g/cm的氧化锆珠子作为金属球。因为其密度介于铜铝之间,不会在球磨时出现分层现象,且硬度较高,耐磨性较好,有利于粉料的充分混合。
粉料的原子比例(Cu:Al)为15:85,其中Cu粉的质量为9.53 g,Al粉的质量为22.93 g,球磨机转速为80 r/min,球磨时间6小时,每30分钟换向,球料质量比为3:1。
首先用超声清洗仪清洗球磨罐子和球磨珠子,并用电吹风机干燥。然后使用电子秤依次称量如表所示的足够质量纳米铜粉和铝粉,称量时,使用油性纸以防止粉末沾黏,称量完后迅速将粉末放入球磨罐子,加入既定比例的氧化锆球,并使用勺子搅拌使粉料和氧化锆球混合均匀。迅速盖上球磨罐的盖子并拧紧螺丝,使罐子内部保持密封状态,用真空泵将罐子内部抽成真空,以防止铝粉氧化。
2.2.2. SPS烧结
本次实验前驱体采用SPS技术烧结而成,具体步骤如下:
称取粉料。考虑到所需样品较多,故选用20 mm直径的石墨磨具来烧结,以便在烧结后切割成多个样品。用电子秤分别称取三组10 g粉料,编号分别为ABC。
设定参数。参考Cu-Al二元相图,虽然其液相线温度为548℃,但考虑到实际操作时,防止粉末出现熔融现象,将烧结温度定于400℃,其升温过程如下图2:

Figure 2. Heating process during sintering
图2. 烧结升温流程
烧结前将罩内抽真空,当罩内气压下降到60 MPa时,运行烧结程序,并对试样施加1KN的预压力。开始升温,3 min时间,炉内温度由室温升至300℃,一分钟后,温度升至370℃,再1 min后,炉内温度升至398℃,开始对试样施加压力(表2.3),对D1-A,D1-B和D1-C分别施加10 MP,20 MPa和30 MPa压力,10 min后,温度升至400℃,随后断开电源,直至试样随炉冷却至室温后取出模具。
2.2.3. 去合金化腐蚀
用砂纸打磨烧结所得前驱体,完全去除表面碳纸且表面较为光洁平整,再用线切割机将试样切成厚度约为1 mm的均匀薄片。
将线切割所得样品用不同粒度砂纸进行打磨,直至表面氧化层被去除,且表面较为光洁平整。将打磨后的样品用无水乙醇擦拭清洗后,泡在无水乙醇中,用超声清洗仪再次清洗,除去油污和表面难以清洗的污垢。随后用电吹风机将试样无水乙醇吹干并放入样品袋密封保存。值得注意的是,由于样品较为疏松,所以应该延长电吹风吹干的时间,以保证试样完全干燥。
将分析纯盐酸(11.8 mol/L)分别稀释到0.5 mol/L,1.0 mol/L和1.5 mol/L。将经线切割所得3个薄片分别用这三个不同浓度的盐酸进行自由腐蚀。
3. 实验现象及结果分析
3.1. SPS烧结
3.1.1. 烧结前后微观形貌对比
由图3可知,大颗粒的铝粉尺寸更集中,且形状更接近于球形。粉料经由不同压力烧结出不同前驱体,烧结后样品表面附着碳纸,呈炭黑色,经不同粒度砂纸依次打磨后,样品表面都呈现出金属光泽,用肉眼观察,更接近铝的颜色。且由于烧结压力的不同,尽管3个前驱体所用粉料质量相同,但烧结出来的体积明显不同,烧结压力越小,所得前驱体体积越大,此外,在表面抛光时发现,使用较粗砂纸时,会将10 MPa前驱体的粉料磨散,说明10 MPa压力下烧结的前驱体内部疏松,而20 MPa和30 MPa压力下烧结的样品没有这样的现象。
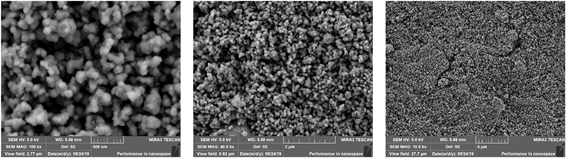
Figure 3. Microstructures of precursor powder
图3. D1球磨粉微观形貌
根据Li [21] 等实验证明,烧结压力增大,会提高原子的表面扩散能力和体积扩散能力,从而提高粉末的流动性,使烧结所得样品更加紧密。测量不同烧结压力下的前驱体体积,发现烧结压力越大,前驱体体积越小,由于烧结粉末质量相同,可以得出烧结压力越大,前驱体密度越大,内部越致密。
驱体截面做SEM电镜(图4),可见前驱体截面由400 nm到2 μm左右的球状颗粒组成,分布均匀且较为疏松,存在500纳米到2 μm左右大小的孔隙。与烧结前的粉末相比,前驱体发生了结晶,产生了固溶体颗粒,且固溶体颗粒明显大于烧结前粉料中的颗粒。
3.1.2. 烧结前后成分对比
如图5,从上到下依次为前驱体D1-A、D1-B、D1-C的EDS图谱,可见各个前驱体中除了Al和Cu元素之外,还有O元素,说明混粉和烧结的操作过程中,粉料被氧化。前驱体D1-A、D1-B、D1-C的EDS原子比分别为13.0:1,7.4:1和12.5:1,可以看出D1粉料经SPS烧结后,得到的前驱体相对不均匀,并且3个前驱体经EDS所测得的Al含量均高于所用粉料,推测是因为球磨时间相对较短,且球磨转速相对较低,球料比也相对较小,导致混粉不均匀。但是几乎都存在前驱体表面Al原子比例高于所用粉料中Al原子比例的现象,分析其原因,可能是因为烧结过程中,形成固溶体时,元素发生了扩散,此外,还可能因为铝粉末较大,而EDS测试时所取面积较小,小于铝元素集中区域面积,导致最终检测结果出现偏差。
3.2. 去合金化腐蚀
将烧结后的样品用线切割切成厚度为1 mm的圆形薄片,在10 MPa压力下烧结的前驱体较为疏松,试样较脆,在线切割的过程中折断,而在20 MPa和30 MPa压力下烧结的前驱体则完好无损。说明在较大压力下烧结所得前驱体拥有更好的硬度。
因为合金中Al的电极电位是−1.662 V,而Cu的电极电位是0.337 V,远高于Al,所以反应能够进行,其化学方程式为:

用分析纯盐酸(11.8 mol/L)分别稀释出浓度为0.5 mol/L,1.0 mol/L和1.5 mol/L的稀盐酸。腐蚀过程中,烧结压力越小,盐酸浓度越大,反应越剧烈,去合金化所需时间越短。
相同盐酸浓度下,烧结压力越小,试样内部越疏松,致密度越小,试样比表面积越大,盐酸更易进入试样内部,盐酸与试样接触面积越大,反应越迅速,且固溶体AlCu中的Al被腐蚀之后,剩下没有配位的Cu原子向表面扩散聚集,而致密度越小,Cu原子扩散速度越快,从而去合金化过程越快。
相同烧结压力,盐酸浓度越大,反应越激烈。此外,样品中铝元素的原子比例越高,反应初始速度越快,但腐蚀所需时间越长。
3.2.1. 去合金化前后成分对比
对比样品腐蚀前后的成分比例,参见表1,不难发现,除D1-B1号样品腐蚀得不太完全之外,其他样品腐蚀情况良好。
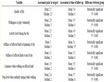
Table 1. Ingredients before and after corrosion
表1. 腐蚀前后成分
腐蚀刚开始时,可以清楚地观察到,盐酸浓度越高,烧结压力越小,反应越剧烈,反应过程伴随着大量气泡的产生和温度的升高,反应越剧烈,气泡产生越多且试剂瓶温度越高。
待腐蚀液中的样品表面不再冒出气泡时,分别记录下各个样品的反应时间,并用镊子小心的取出样品,防止样品破损。用无水乙醇清洗样品,并用电吹风机长时间烘干,随后浸泡于无水乙醇中用超声清洗仪洗去表面污垢,将所得样品保存在无水乙醇中,待观察时再取出。在用扫描电子显微镜观察前,将样品从无水乙醇中取出,并用电吹风机迅速烘干以防氧化,至于敞开的试剂瓶内,放入真空干燥器中抽真空24小时,使样品完全干燥。将样品按照编号排序,用镊子将每个腐蚀所得样品掰成小块,取每个样品截面观察。用双面胶将小块样品黏在样品台的铝箔上,将样品进行120 s喷金处理,然后将整个样品台放入MIRA3扫描电子显微镜中观测。与此同时,线切割后剩下的前驱体也经过无水乙醇清洗,超声清洗,电吹风机烘干和抽真空机干燥后,进行排序,放置于样品台并喷金,最后将整个样品台放入MIRA3扫描电子显微镜中观测。用于比较去合金化腐蚀前后样品表面形貌和元素比例的变化。
由标号为D1的粉料烧结而来的8个样品中,Al元素的含量分别从85%下降到10%以内,且大部分在4%左右,通过计算可以得出,Al元素的腐蚀效率为99.35%左右,腐蚀比较完全。并且可以看出当盐酸浓度从0.5 mol/L提高到1.5 mol/L时,Al元素的腐蚀率虽然仍然会提高,但是提高的效果显著降低,可以想见,进一步提高盐酸的浓度对Al元素的腐蚀率影响极其有限,因此1.5 mol/L的盐酸腐蚀效果较好且最为稳定,相比较其他两种浓度的盐酸,能在较短的时间内达到较高的腐蚀率。
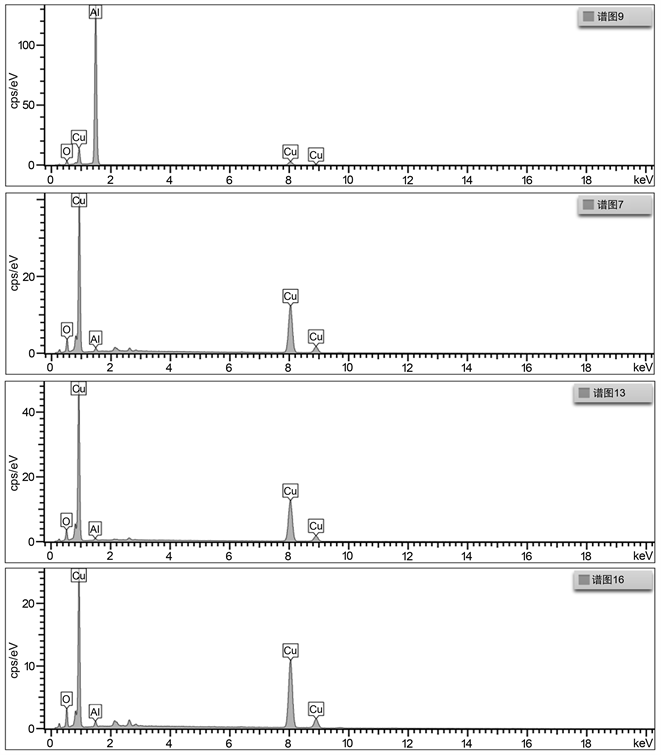
Figure 6. EDS spectrum of D1-A before and after corrosion
图6. D1-A前驱体腐蚀前后EDS图谱
上图6从上到下依次为前驱体D1-A及其在不同浓度盐酸腐蚀所得样品D1-A1、D1-A2和D1-A3。
关于微米级孔隙形状,由D1粉烧结而来的样品,孔径接近圆形,且孔径大小集中在50~200 μm之间。其原因在于其Al的含量大,腐蚀时间更长,所以铜出现了一定程度的钝化。对比腐蚀前(图5)和腐蚀后(图7(a)),不难发现,样品颗粒变得更加细小,疏松,出现了200 nm到1 μm左右大小的孔隙,且分布不均匀,形状不规则。放大后可以看到腐蚀后的样品出现20 μm到100 μm大小不等的孔洞,且形状接近圆形,较为规则。
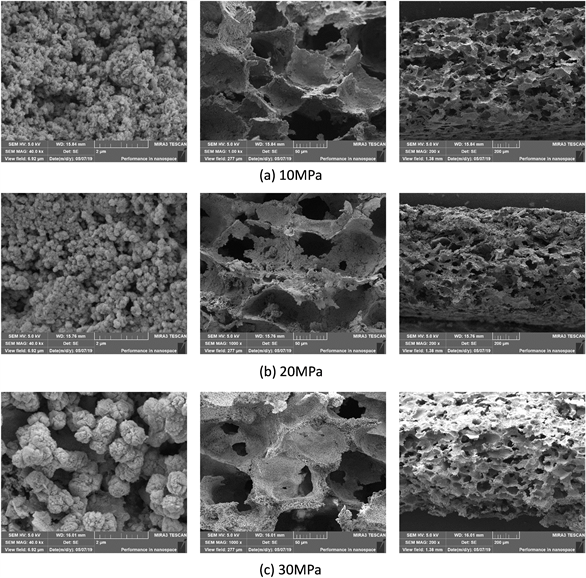
Figure 7. Microstructure of D1-A3, D1-B3, D1-C3 after corrosion
图7. D1-A3,D1-B3,D1-C3前驱体腐蚀后微观样貌
为了作进一步对比,实验制备了铝粉和铜粉原子比例为70:30的粉料(粉料S),采用200 r/min的较高转速和10 h的较长球磨时间,并每30 min转向旋转,以保证充分混合且粉末细小。对S粉料进行烧结时,步骤和之前烧结D1前驱体一致,只是在最后的施压阶段施加了20 Mpa的压力,得到新的前驱,即S-B前驱体。将S-B前驱体放在1.5 mol/L的盐酸中腐蚀4.5小时,腐蚀温度同样是20℃,得到的多孔铜样品S-B1,其腐蚀比例达到99.8%。
如图8所示,由S粉烧结而来的样品,孔径形状较为不规则,但孔隙相对较小,孔隙尺寸集中在20~100 μm之间,分析其原因,一方面,腐蚀时间较短,另一方面,S粉球磨时间较长,粉末混合更加均匀,球磨转速更高,使得铝粉末更加细小。结合D1粉和S粉的电镜图片,由于S粉球磨时间更长,转速更高,球料比更大,所以铝粉被球磨珠子挤压变形,导致形状不规则,从而使腐蚀所得孔隙形状也不规则。
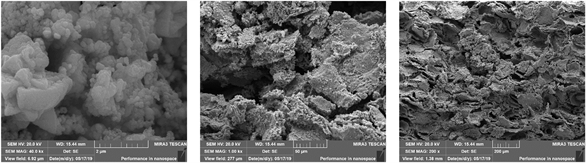
Figure 8. Microstructure of S-B1 after corrosion
图8. S-B1前驱体腐蚀后微观样貌
4. 实验结论
烧结压力从10 MPa增加到30 MPa,制备的Cu15Al85前驱体外观体积越小,材料内部越致密,随后的去合金化速率越低,且孔隙尺寸分布在200 nm到1 μm范围内的孔隙数量越少。
对比盐酸浓度0.5 mol/L、1.0 mol/L和1.5 mol/L的腐蚀剂对Al-Cu合金进行去合金化,1.5 mol/L的盐酸对Al的去除率最高,且表现出最快的腐蚀速度。
Al、Cu原子比分别为85:15和70:30的两种合金前驱体进行去合金化,前者腐蚀速率较慢,获得孔隙尺寸较大且孔隙率较高的多孔铜。