1. 引言
Al-Mg-Si系铝合金作为可热处理合金因其具有较高的强度、良好的成型性能、优良的腐蚀性能,以及可焊接性等,而被广泛应用于汽车制造业,成为汽车车身板材的首选材料 [1] [2]。但该合金在应用过程中仍面临这一些挑战,例如进一步提高其耐蚀性、成型性以及在短时间烤漆过程中获得较快的时效响应等 [3]。Fe元素在Al-Mg-Si合金中一般被视为一种杂质元素,主要是以FeAl3和AlFeSi等化合物形式存在。若合金中Fe含量 > 过剩Si含量,则Al基体中会形成α-Fe2SiAl8相;而当过剩Si含量 > Fe含量时,则更易形成β-FeSiAl5相。Fe可与Mn形成化合物来提高材料再结晶温度的效果,且少量Fe的添加有助于铸态晶粒的细化。但Fe元素的添加会使合金更易发生局部腐蚀,且会对合金进行阳极氧化着色,使合金表面质量、塑性以及抗腐蚀性能均下降,并使合金热处理强化效果减弱。故应使Fe元素的添加量低于0.20 wt%,让Al-Mg-Si合金的氧化着色能力与材料抗腐蚀性能得以提高 [4]。
目前,国内外对Al-Mg-Si合金进行了一定的研究,研究主要分两类,一类是研究Al-Mg-Si合金的热处理工艺对其组织与性能的影响 [5] [6] [7] [8],而另一类是研究Al-Mg-Si合金中微量元素的添加对其组织与性能的影响 [9] [10] [11]。在对微量元素的添加对Al-Mg-Si合金组织与性能的影响的研究中,主要集中在对微量Cu、Mn、Cr等元素的研究上,而研究微量Fe对Al-Mg-Si合金的组织与性能的相关研究相对较少。本论文主要以Fe元素含量不同的Al-0.7Mg-0.6Si合金为研究对象,分析讨论了其多相微观组织与性能之间的关联性,为Al-0.7Mg-0.6Si合金的生产及加工提供一定的理论和实践依据。
2. 实验材料及方法
2.1. 材料加工及试剂
本文实验研究材料为Fe元素含量不同的Al-0.7Mg-0.6Si合金型材,这3批合金微量Fe元素含量分别为0.1 wt%、0.2 wt%与0.3 wt%。表1为合金的主要化学成分(质量分数,%)。可知,实验研究的Al-0.7Mg-0.6Si合金材料除元素Fe含量存在差别外,其它化学元素含量无明显差别。沿Al-0.7Mg-0.6Si合金型材的挤压方向并参照国标GB/T15970.6-2007制备两组应力腐蚀试样,分别用与对腐蚀形貌的观察和剩余性能的测试,每组设置平行实验三个,试样厚度为3 mm,将机加工痕迹采用80#、320#、800#、1200#、1500#型水磨砂纸打磨至平整,最后配置3.5 wt% NaCl溶液(中性)和含少量HCl的溶液(酸性)两种腐蚀实验溶液。
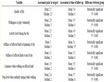
Table 1. The chemical composition of Al-0.7Mg-0.6Si alloy (mass fraction/%)
表1. Al-0.7Mg-0.6Si合金化学成分(质量分数/%)
2.2. 腐蚀性能测试
在恒应力拉伸试验机上进行不同环境的应力腐蚀实验,加载时间分别为0、5、10天,实验温度控制在25℃ ± 2℃,加载应力为150 MPa。应力腐蚀实验结束后,取下一组对试样用去离子水洗净并风干处理,转移至DDL-100型电子万能材料试验机处测试其残余应力,并使用引伸计在拉伸试验过程中测量屈服点。实验过程中拉伸速率为2 mm/min,相当于3.3 × 10−2 mm/s,实验温度为室温(25℃ ± 3℃)。
2.3. 微观组织测试
将另一组不同应力腐蚀10天的实验试样取下,洗净风干,采用ZEISS MA10扫描电子显微镜(SEM)观察其表面侵蚀形貌,并通过OxfordEDS型能谱仪并对其腐蚀坑及第二相粒子进行EDS能谱分析。随后切取试样的ND-TD面在室温进行镶嵌,将样品进行粗磨、细磨及机械抛光后,采用OLYMPUSGX71型光学金相显微镜(OM)观察在其腐蚀形貌及测量腐蚀深度。
3. 结果与讨论
3.1. 在中性溶液中合金微观形貌的变化
图1为不同Fe含量的Al-0.7Mg-0.6Si合金在3.5% NaCl溶液中进行恒载荷腐蚀实验10天时试样表面的腐蚀形貌。如图1(a),图1(c),图1(e)可见,Fe含量0.1 wt%的合金试样、Fe含量0.2 wt%的合金试样与Fe含量0.3 wt%的合金试样表面均未观察到沿晶界腐蚀的情况且没有微裂纹与较大的腐蚀坑。表明合金在3.5% NaCl溶液中应力腐蚀敏感性很低,合金材料几乎不发生任何应力腐蚀行为。如图1(b),图1(d),图1(f)所示将SEM图片放大至500倍后可观察到合金表面分布有一些细小的腐蚀坑。这些腐蚀坑洞会对合金表面质量产生轻微的影响,但几乎不会对材料的强度造成影响。对腐蚀坑洞中残留的第二相进行EDS能谱分析得到表2,发现第二相为杂质AlFeSi相。
图2为通过金相显微镜所观察到的在3.5% NaCl溶液中实验合金进行恒载荷腐蚀实验10天时的恒载荷腐蚀深度情况。由图2可以看出,实验合金在3.5% NaCl溶液中均未发生向合金内部延伸的腐蚀过程,但可观察到零散分布的缺口,这些缺口为合金表面细小腐蚀坑的截面。通过统计软件测量其腐蚀深度可知,含Fe量0.1 wt%的合金试样最大腐蚀深度为10.1 μm,含Fe量0.2 wt%的合金试样最大腐蚀深度为14.4 μm,含Fe量0.3 wt%的合金试最大腐蚀深度为18.5 μm。故合金在3.5% NaCl溶液中应力腐蚀性能较为优异,且未出现向合金深处的腐蚀。
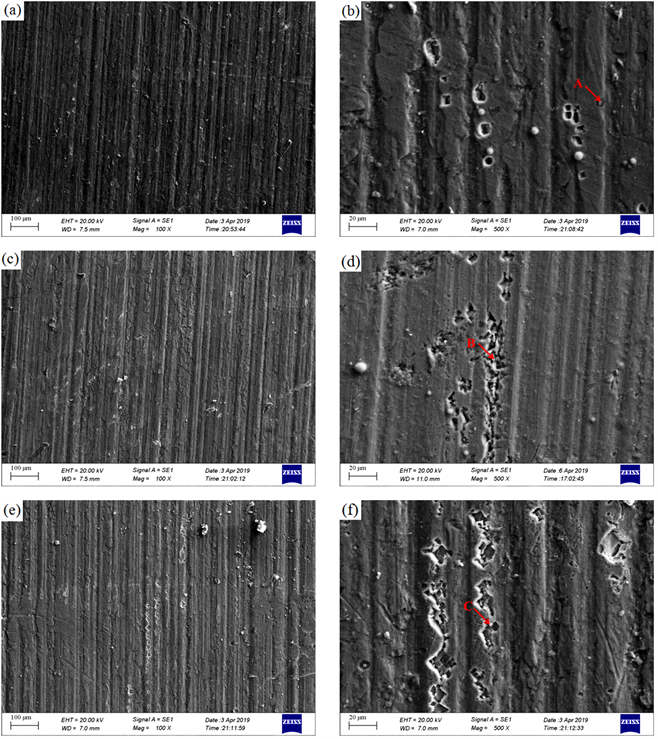
Figure 1. Corrosion’s morphology of Al-0.7Mg-0.6Si alloys in 3.5% NaCl solution with 10 d 150 MPa: (a) (b) 0.1 wt% Fe; (c) (d) 0.2 wt% Fe; (e) (f) 0.4 wt% Fe
图1. 10天150 MPa条件下在3.5% NaCl溶液下Al-0.7Mg-0.6Si合金的表面腐蚀坑形貌:(a) (b) 0.1 wt% Fe;(c) (d) 0.2 wt% Fe;(e) (f) 0.4 wt% Fe
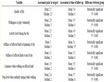
Table 2. EDS analysis results of second phase in Figure 1(b), (d), (f)
表2. 图1中(b)、(d)、(f)腐蚀坑内残留第二相EDS分析结果
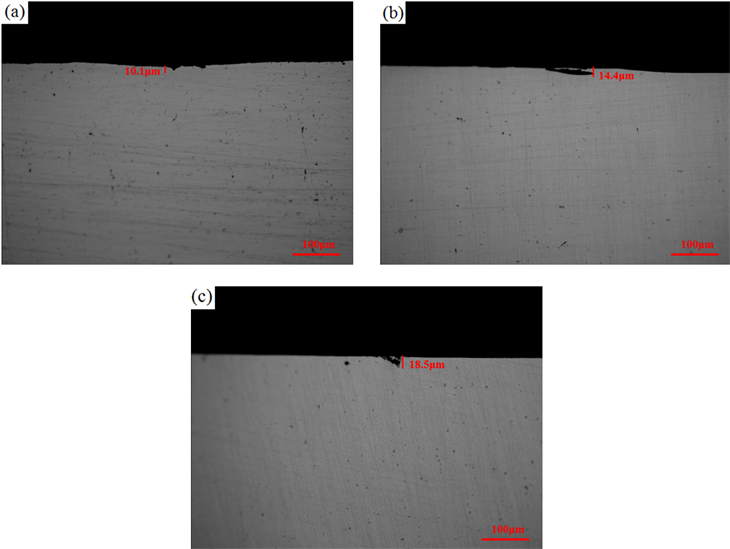
Figure 2. Corrosion depth of Al-0.7Mg-0.6Si alloys in 3.5% NaCl solution with 10 d 150 MPa: (a) 0.1 wt% Fe; (b) 0.2 wt% Fe; (c) 0.4 wt% Fe
图2. 10天150 MPa条件下在3.5% NaCl溶液下Al-0.7Mg-0.6Si合金的腐蚀深度:(a) 0.1 wt% Fe;(b) 0.2 wt% Fe;(c) 0.4 wt% Fe
3.2. 在酸性溶液中合金微观形貌的变化
图3为不同Fe含量的Al-0.7Mg-0.6Si合金在酸性溶液中进行恒载荷腐蚀实验10天时试样表面的腐蚀形貌。由此可见,在酸性溶液中,实验合金表面均发生严重的沿晶腐蚀和间距较宽的宏观裂纹,晶粒内亦可观察到众多的大小不一的腐蚀坑。由于外加应力的作用,在部分被腐蚀的晶界处会发生应力集中,使得裂纹更易产生。将SEM图片放大至500倍后对合金腐蚀坑的大小进行测量,含Fe量0.1 wt%的合金试样腐蚀坑大小在1 μm至20 μm之间不等;含Fe量0.2 wt%的合金试样腐蚀坑大小则在1 μm至25 μm之间不等;含Fe量0.3 wt%合金试样腐蚀坑大小在2 μm至20 μm之间。对腐蚀坑内残留第二相进行EDS能谱分析得到表3,腐蚀坑中残留第二相为AlFeSi相。在酸性溶液中进行恒载荷腐蚀,实验合金表面点蚀和晶间腐蚀行为较严重,故使得合金的强度出现明显的下降,且由于表面晶粒晶界被完全腐蚀,使得合金晶粒间结合力大幅减弱,引起材料塑性大幅下降。
图4为通过金相显微镜所观察到的在酸性溶液中实验合金进行恒载荷腐蚀实验10天时的恒载荷腐蚀深度情况。由图4可知,Fe含量0.1 wt%合金的试样最大腐蚀深度为127.2 μm,Fe含量0.2 wt%合金的试样最大腐蚀深度为208.7 μm,Fe含量0.3 wt%合金的试样最大腐蚀深度为283.5 μm。随着Fe元素含量的提高,合金的最大腐蚀深度值逐渐变大,说明合金的应力腐蚀性能随Fe元素含量的提高而逐渐变差。
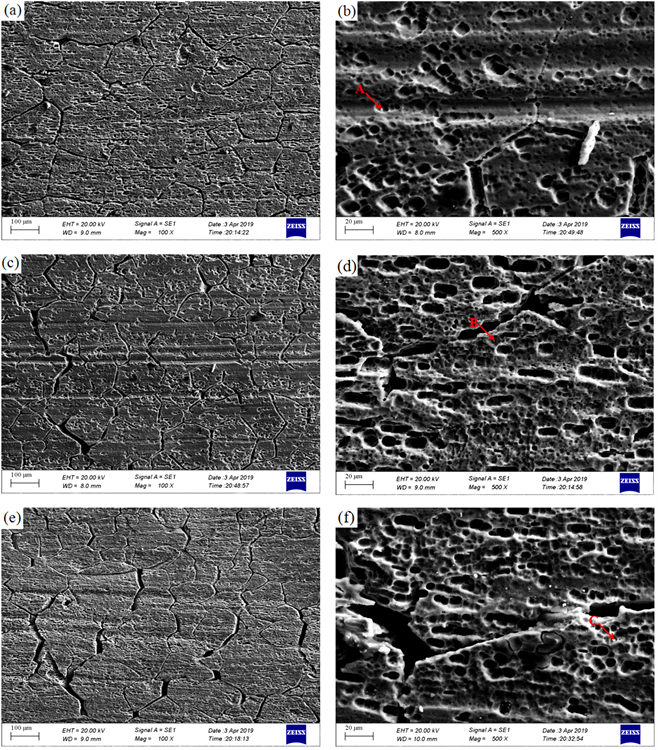
Figure 3. Corrosion’s morphology of Al-0.7Mg-0.6Si alloys in acidic solution with 10 d 150 MPa: (a) (b) 0.1 wt% Fe; (c) (d) 0.2 wt% Fe; (e) (f) 0.4 wt% Fe
图3. 10天150 MPa条件下在酸性溶液下Al-0.7Mg-0.6Si合金的表面腐蚀坑形貌:(a) (b) 0.1 wt% Fe;(c) (d) 0.2 wt% Fe;(e) (f) 0.4 wt% Fe
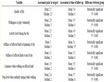
Table 3. EDS analysis results of second phase in Figure 3(b), (d), (f)
表3. 图3中(b)、(d)、(f)腐蚀坑内残留第二相EDS分析结果
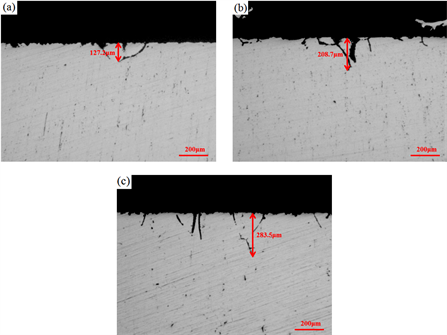
Figure 4. Corrosion depth of Al-0.7Mg-0.6Si alloys in acidic solution with 10 d 150 MPa: (a) 0.1 wt% Fe (b) 0.2 wt% Fe; (c) 0.4 wt% Fe
图4. 10天150 MPa条件下在酸性溶液下Al-0.7Mg-0.6Si合金的腐蚀深度:(a) 0.1 wt% Fe;(b) 0.2 wt% Fe;(c) 0.4 wt% Fe
3.3. 在中性溶液中合金性能的变化
图5为不同Fe含量的Al-0.7Mg-0.6Si合金在3.5% NaCl溶液中进行恒载荷腐蚀试验后试样的剩余强度情况。每组实验均取平行试样3个,数据均为平均值。由图5(a)可以看出,实验合金试样在加载载荷
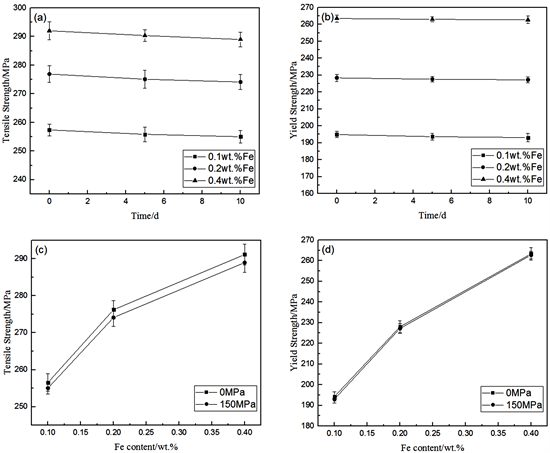
Figure 5. Constant load corrosion’s residual strength of Al-0.7Mg-0.6Si alloys in 3.5% NaCl solution: (a) Change of tensile strength with times; (b) Change of yield strength with times; (c) Tensile strength at 10 days; (d) Yield strength at 10 days
图5. 3.5% NaCl溶液下Al-0.7Mg-0.6Si合金恒载荷腐蚀剩余强度:(a) 抗拉强度随时间的变化;(b) 屈服强度随时间的变化;(c) 10天时的抗拉强度;(d) 10天时的屈服强度
为150 MPa时,材料经过恒载荷腐蚀实验后,其抗拉强度随实验时间的增加有微弱的下降。当实验时长为5天时,其抗拉强度的损失均低于2 MPa,不到初始抗拉强度的1%;当实验时长为10天时,其抗拉强度的损失也均低于4 MPa,损失为初始抗拉强度的1%左右。抗拉强度损失最大的为Fe含量0.3 wt%合金加载10天的试样,抗拉强度损失为3.0 MPa,相当于初始抗拉强度的1%。
对比图5中应力腐蚀强度损失的结果,发现合金在3.5% NaCl溶液中几乎不发生应力腐蚀,其对应力腐蚀极不敏感,材料强度未发生损失。当试样加载载荷为0 MPa时,合金材料在不受应力作用的状态下进行腐蚀,其抗拉强度损失同样均低于初始抗拉强度的1%。合金材料的强度在3.5% NaCl溶液中的耐腐蚀性能优异且无明显差异。
3.4. 在酸性溶液中合金性能的变化
图6为不同Fe含量的Al-0.7Mg-0.6Si合金在酸性溶液(57 g NaCl + 10 ml HCl的腐蚀溶液)中进行恒载荷腐蚀实验后试样的剩余强度情况。可以看出,当加载应力为150 MPa时,实验合金试样在经过恒载荷腐蚀实验后,其抗拉强度随实验时间的增加发生了明显的下降。实验5天时,Fe含量0.1 wt%、0.2 wt%、0.3 wt%合金抗拉强度损失分别为22.3 MPa、27.0 MPa与32.0 MPa,是材料初始抗拉强度的8.7%、9.8%与11.0%;实验10天时,Fe含量0.1 wt%、0.2 wt%、0.4 wt%合金抗拉强度损失分别为41.9 MPa、48.2 MPa与54.5 MPa,相当于材料初始抗拉强度的16.3%、17.4%与18.7%。这其中,随着合金内Fe元素含量的提高,合金抗拉强度的损失增大,说明合金的应力腐蚀性能随Fe含量的提高而变差。
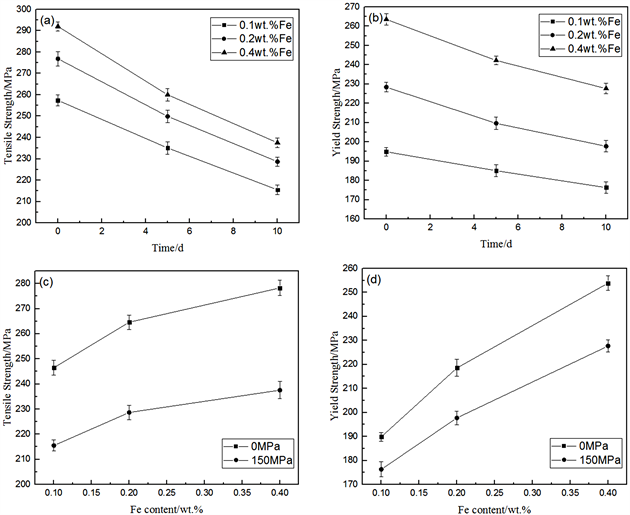
Figure 6. Constant load corrosion’s residual strength of Al-0.7Mg-0.6Si alloys in acidic solution: (a) Change of tensile strength with times; (b) Change of yield strength with times; (c) Tensile strength at 10 days; (d) Yield strength at 10 days
图6. 酸性溶液下Al-0.7Mg-0.6Si合金恒载荷腐蚀剩余强度:(a) 抗拉强度随时间的变化;(b) 屈服强度随时间的变化;(c) 10天时的抗拉强度;(d) 10天时的屈服强度
4. 结论
1) Al-0.7Mg-0.6Si合金材料的应力腐蚀性能存在差异。在3.5% NaCl腐蚀环境中,Al-0.7Mg-0.6Si合金对应力腐蚀不敏感,应力腐蚀性能未表现出明显差别;在酸性腐蚀环境中进行应力腐蚀实验,Al-0.7Mg-0.6Si合金强度的损失随着合金内Fe元素含量的提高而提高,应力腐蚀性能变差。
2) 随着微量元素Fe含量的提高,Al-0.7Mg-0.6Si合金内的AlFeSi相数量逐渐增多,并会使得合金材料的应力腐蚀性能变差。
NOTES
*通讯作者。