1. 引言
随着自动化程度的不断提高,SMT产线的高度自动化与仓储物料执行的传统手工作业越来越不相协调,劳动用工分配不合理 [1]。因此,自动导引车(Automated Guided Vehicle,AGV)逐渐成为生产线自动化物流系统的关键设备,来实现物料的仓储、分拣、校核、配送的自动化和智能化。由多辆AGV组成的自动导引车系统(Automated Guided Vehicle System,AGVS)广泛运用于许多行业的物流自动化中 [2]。然而由于AGVS属于典型的离散事件动态系统,在系统分析与优化过程中需要考虑的方面很多,如:AGV导引路径网络布局及装卸点位置安排、AGV配置数量确定、AGVS任务调度策略,以及AGVS交通管理策略等等 [3]。AGV价格昂贵,且AGV数量过多反而会阻碍其利用率的提升,造成资源浪费 [4]。因此如何根据生产计划配置相应数量的AGV并制定合适的调度策略,使其满足产能需求一直是企业关注的问题。
本文以某公司SMT车间为研究对象,针对车间AGV物流系统,以物料配送时间最小化为目标,基于Plant Simulation仿真软件建立模型,以改变AGV配置数量以及车间单元布局为手段,总结最优车辆配置与布局方案,为车间生产物流方案提供决策支持。
2. 应用背景
以AGVS在某公司SMT车间的应用为例,车间布局如图1所示。
图1中车间布局涉及到物料配送区和贴胶工位区。贴胶工位区又可分为四个区域,包括:
➢ 区域1:全自动贴胶机区域
➢ 区域2:紧凑型在线贴附机区域
➢ 区域3:多功能贴标机区域
➢ 区域4:全自动贴胶机区域
其中,区域3共有工位24个,上下料点12个;区域2共有工位16个,上下料点8个;区域3共有工位23个,上下料点5个;区域4共有22个,上下料点11个。全部车间包含两种加工设备:压敏胶贴合55台,高温胶贴合46台。两种设备所用物料与物料配比均相同,仅生产节拍不同。
3. 仿真建模
生产物流系统属于典型的离散事件系统,离散事件系统仿真的一般步骤包括:系统建模、确定仿真算法、建立仿真模型、设计仿真试验、运行仿真实验以及输出仿真结果分析数据 [5]。
3.1. 仿真软件选择
目前应用于生产线仿真的软件有 Plant Simulation、Flexsim、Witness等,都采用了面向对象的虚拟仿真技术,并可以对模型系统进行模型规划和数据统计等操作。Plant Simulation原名em-plant,是以色列Tecnomatix开发的软件工具,被西门子公司收购后改名。
3.2. 生产系统建模
根据上文描述,贴胶工位涉及到的设备包括:压敏胶贴合55台,高温胶贴合46台,并且两种设备所用物料与物料配比均相同,仅生产节拍不同,因此在本次仿真中采用相同的模型。通过设置相应的节拍时间以区别两种设备。
3.3. AGV系统建模
3.3.1. 轨道模型
在Plant Simulation中,AGV运行轨道用Track对象实现,采用单向单通道的方法,AGV在轨道上只能按照规定的方法依次通过。在装卸站点附近时,当AGV执行装卸作业时,该轨道仍将被占用,后续车辆不得通过。
每段线路根据其长度与AGV长度,限制了其可容纳车辆数量,因此当车辆进入各轨道前,设置传感器触发检测路段容量程序,程序由Method对象中编程语言实现。
在轨道的交汇点,通过设置sensor对象,控制车辆遵循先到先行的原则。
3.3.2. 车辆模型
AGVS由AGV、导引路径网络以及AGVS控制系统组成,在Plant Simulation仿真软件中,AGV和导引路径可分别用Transporter和Track等对象来表示。AGVS控制系统可以分为AGVS中央决策层与AGV执行层。其中,中央决策层负责接受来自MES系统的物料配送指令,然后发布出库、备料、AGV调度等控制指令,并反馈执行信息给MES系统。物料配送流程如图2所示。
AGV每次只能搬运一个托盘,AGV运行速度为1 m/s,装卸载时间为25 s。AGV蓄电池充电特性为:每工作4 h需充电1 h。
3.3.3. 交通管理
每台AGV的工作均在上位机系统监控下运行,AGV随时向系统汇报自身工作状态,等待系统给出下一步将要经过的线路指令 [6]。当多辆AGV运行于同一个路径系统中时,不可避免地会存在相互干涉、冲突的现象。在单向路径网络中,AGV运行过程中常见的干涉如图3所示。
AGV运行过程中常见的干涉如图3所示。
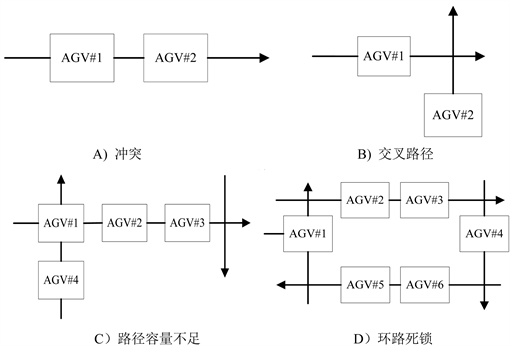
Figure 3. The common interference during AGV operation
图3. AGV运行过程中常见的干涉现象
本次仿真由于车间轨道布局原因,采用等待规则,即若下一路段已被其他车辆占用,则车辆不能通行,必须等待系统许可后,继续前行。
3.3.4. 调度及路径规划
搬运任务分配及AGV调度可理解为当系统中存 在多个搬运任务和空闲AGV时,确定搬运任务和AGV的分配关系。针对本文所研究的系统,采用先到先服务的策略,在Plant Simulation中,可以通过Table对象记录新的搬运任务及其产生的时刻,当系统中产生一辆空闲AGV时,立即执行Table对象中最先记录的搬运任务。
由于本文所研究的AGVS均是基于单向路径网络,AGV在每条路径段上允许的运行方向预先确定且在运行过程中不变,这就使得AGV自主路径规划成为可能,各AGV均存有地图(路径网络),各AGV一旦获得目标工位点,即可通过Dijkstra算法规划一条从自身位置到目标节点的最短有向路径。
按照上述信息,结合本文研究对象实际背景构建仿真模型如图4。
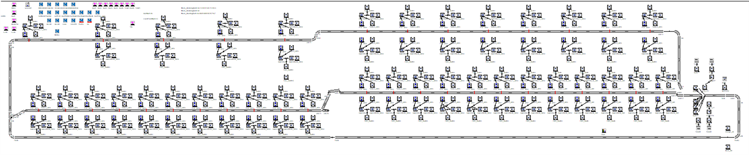
Figure 4. The equipments layout in simulation software interface
图4. 车间设备布局仿真界面
4. 仿真模型的应用
根据该车间生产实际情况,随机生成多份模拟订单待完成;AGV中央系统获得订单后,将待加工原材料储存于物料柜,并开始发布任务。AGV每次运载柔性电路板原料12套或贴纸5份,其中每份贴纸可供生产10套电路板。AGV运行速度为1 m/s,原料取料及卸料时间均为30 s。
该生产车间为71个加工工位,根据本项目所设计物流方案,每两个工位公用一个送料点与一个回收点,生产节拍均假设为1 min/套。工位上料阈值为2套,即当线边暂存区库存低于2套时,向上位机系统发布上料请求。
4.1. 基于AGV配置数量的仿真
由于AGV成本昂贵,AGV数量过多,不仅会造成资源浪费,也容易引起AGV之间的干涉和冲突,造成堵塞,增加调度的难度。反之,若AGV数量不足,将无法满足生产需求,造成设备等待和停机,影响车间的经济效益。
为此,本项目首先基于系统仿真模型和上述的参数设置,评估保证生产车间满负荷运行、稳定运行所需要的AGV数量,在此基础上制定AGV调度策略。仿真时,将系统中所需AGV数量作为可变参数,逐渐增加模型中的AGV数量。在每一班开始工作前,需AGV提前配送各工位所需物料,在每一种AGV数量下,记录AGV完成全部工位上料的准备时间作为评价指标。仿真结果如图5所示。
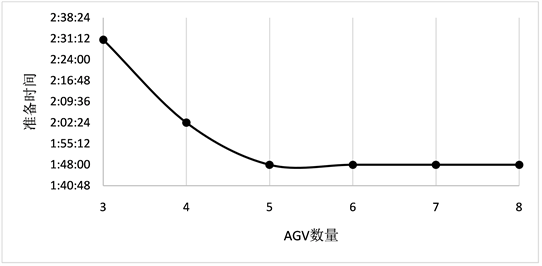
Figure 5. The relationship between AGV’s quantity and set-up time
图5. AGV数量与准备时间之间关系
从图中可以得出如下结论:
1) 当AGV数量低于5辆时,增加AGV数量可以有效提高物料配送效率,减少生产前的准备时间。例如,当配置三辆AGV时,AGV完成全部工位上料任务所需时间为2.52 h,而当AGV数量为5辆,AGV完成全部工位上料任务所需时间为1.8 h;
2) AGV数量的增加与准备时间的缩短不完全成反比关系。随着车辆数量的增加,准备时间减少趋于不明显。尤其,当AGV数量达到5辆以后原因在于:多辆AGV同时作业时,需共用同一取料点,当前序车辆在取料点取料时,后续车辆不得通过或同时进行取料作业,造成堵塞。
另外,本项目所设计的轨道布局较为简单,任意两点之间路径均为唯一的,当车辆的行驶路段上,有其余车辆正在进行卸料或取料回库作业,同样会造成车辆堵塞,降低物流效率。
因此当AGV数量超过五辆后,单纯地增加车辆数量已毫无意义。
3) 在现有参数下,五辆AGV已足以将准备时间缩短至最小。考虑在满足生产实际需要的同时,需留有一定的余裕,因此配置六辆AGV是较为理想的方案。
4.2. 基于取料点设置的仿真
根据上述结论,当前方案所设计的单一取料点,在AGV数量增加的情况下,容易造成堵塞,不能满足物料配送需求,因此设计仿真试验,改变取料点数量,分析其与生产物流系统性能之间的关系,为确定AGV最佳停靠点设置提供合理依据。仿真方案及主要性能指标比较见图6。
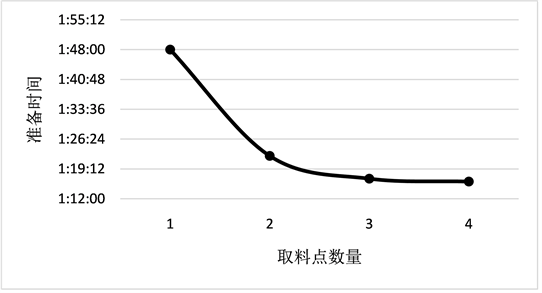
Figure 6. The relationship between material handover point’s quantity and set-up time
图6. 取料点数量与准备时间之间关系
由图中可以看出,增加取料点可以实现多台AGV同时取料,提高AGV取料效率,从而降低取料点堵塞程度,缩短准备时间。但是当取料点超过3以后,取料点数量对缩短准备时间的作用趋于不显著。原因在于:本仿真试验中AGV数量为固定值,当仿真运行时,很少存在过多AGV同时等待取料的现象,此时继续增加取料点数量则不能发挥相应的作用。
5. 结论
本文以Plant Simulation仿真软件为工具,以某轨道交通企业电子器件SMT生产车间为研究对象,建立了系统仿真模型并完成一系列仿真实验,得到系统在各种参数配置和调度策略下系统的性能指标,详细分析了AGV数量、停靠点设置与生产准备时间、加工设备利用率之间的对应关系。在此基础上得出结论:同时也验证了本项目所设计的AGV智能调度算法相较于简单调度策略的合理性与可行性,有效地提高了AGV服务能力。