1. 引言
工件质量的问题制约着我国机械制造业的进一步发展,切削加工产生的毛刺与加工后工件的表面质量是影响工件质量的主要问题 [1]。工厂在生产零件时增加了去除毛刺的工序,但是去除毛刺工序力度过大会对工件造成不可逆的损伤,严重甚至会导致工件报废或损毁。去除毛刺工序力度较小,会使毛刺不能清除彻底,导致工件质量降低,影响下一道工序 [2]。毛刺的产生严重影响工件的质量。
国内外学者很早就开始了研究高速切削加工对工件质量的影响,并且有了较为深入的研究,取得了丰硕的成果。Martellotti [3] 通过多尺度构造法建立了铣削动态模型,确立了铣削表面质量的基本理论。Lee [4] 等人将实际测量的加速度信号加入到仿真算法与程序中来研究刀具–工件之间的相对振动。Omar [5] 等人改进了加工表面三维模型。Arizmendi [6] 等人通过建立刀具轨迹多项式的方式来预测加工表面粗糙度。魏立峰 [7] 分析了球头铣刀铣削加工表面形貌的影响因素并提出了球头铣刀表面形貌仿真算法。李成峰 [8] 通过微铣刀柔性变形量的数据,提出了微铣刀周铣加工表面形貌集成模型。程凯 [9] 提出了切削表面集成化仿真模型。李荣斌 [10] 获得加工中系统振动与振动参数将其与理论切削表面叠加获得实际切削表面。
通过上述文献可以了解,众多学者对加工质量的研究已经取得了丰硕的成果。但由于切削加工过程十分复杂,以往的研究建立的模型只是基于宏观方面,并不能显现出材料的微观变化,进行的研究分析并不全面。
综上,本文建立了基于高温镍基合金材料在高速切削条件下的多晶体仿真模型,结合实验通过有限元方法进行影响工件质量因素的分析,得到了影响毛刺形成的因素,为优化工件质量提供了依据。本文的研究成果可用于推进难加工材料高速切削研究,对提高在军用和民用零件的制造水平及工件质量有重要的实际意义和研究价值。
2. 建模与实验
2.1. 多晶体有限元模型的建立
建立适当的多晶体有限元模型对研究高速切削过程中影响毛刺形成的因素以及犁耕现象的发生与影响因素很重要。本文使用Voronoi方法进行多晶体建模,通过控制Voronoi种子的方法来获得多晶体有限元模型,并且结合晶体学的知识赋予每个Voronoi胞相应取向,建立了金属切削模型。
建立的多晶体模型如图1所示:
2.2. 材料的本构方程
为了得到有效的仿真,需要在ABAQUS中赋予工件材料属性。因此采用了Johnson-Cook材料本构模型,该模型目前应用最为广泛。具体数学表达式见式(1):
(1)
式中
是等效塑性应力,
是等效塑性应变,
是等效塑性应变率,
是参考应变率,A是初始屈服应力,B是硬化模量,C是应变率相关系数,n是加工硬化指数,m是热软化系数,
是室温,T是材料动态温度,
材料融化温度。
Inconel 718合金的Johnson-Cook材料本构模型的参数如表1所示 [11]
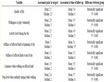
Table 1. Parameters of Johnson cook model for Inconel 718 Alloy
表1. Inconel 718合金Johnson-Cook模型的参数
2.3. 实验过程
机床:CA6140普通车床。
工件材料:镍基合金Inconel 718,材料成分及物理力学性能分别见表2、表3。
刀具材料:YG8。
采用高温镍基合金进行爆炸式快速落刀试验,取得切削根部,制成金相标本,用金相显微镜进行观察,得到切削根微观形态。
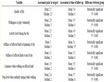
Table 2. Main chemical components of Inconel 718 (wt%)
表2. Inconel 718主要化学成分(wt%)
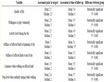
Table 3. Physical and mechanical properties of Inconel 718 (20˚C)
表3. Inconel 718的物理力学性能(20℃)
3. 结果与讨论
3.1. 切削过程中晶粒的变化
实际中的金属多晶体塑性变形是晶内变形和晶间变形的总和。金属多晶体在变形的时候由于各晶粒的大小,形状,位向和分布情况不同,因而各晶粒状态也不同,比较复杂。每个晶粒变形必将影响到其他周围的晶粒,同时也将受到其周围晶粒的限制。各晶粒不能同时变形,且变形不均匀。这种现象可以在本文建立的多晶体切削仿真模型中表现出来。
切屑形成实际上是由于刀具产生的外加应力作用在晶粒上,使各晶粒中产生滑移变形并与工件基体分离。切应力引起的位错源s向外散发位错,由于晶界的存在,位错源s引起的位错在晶粒中移动到晶界处受阻,滑移就不能继续下去,如图2所示。因为在一般情况下,在相邻晶粒中不能找到与它的Burgers矢量b相匹配的平面,位错将会在晶界处发生塞积,塞积会使晶界处应力集中,应力慢慢增大,当应力增加到一定程度时,相邻晶粒的位错源p将被启动,相邻晶粒发生滑移,使晶粒的变形得以协调配合继续进行,晶粒的微观变形形成了工件被切削部分的宏观变形,即切屑是由晶粒之间滑移的传递形成的。塞积群作用在滑移面上的距离晶界为r的处切应力表示为式(2) [12]:
(2)
式中,
是切应力,L是位错源s距离晶界的距离,r是塞积头与相邻晶粒内最近的位错源之间的距离。设触发相邻晶粒滑移的临界应力值为
,当
时,晶粒会发生滑移,切屑才会形成。这一过程实际上是当塞积头处应力集中应该如此之大,以至晶界附近的位错源在切应力
作用下被激活。
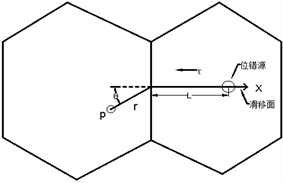
Figure 2. Dislocation slip model of adjacent crystal
图2. 邻晶位错滑移模型
设L等于晶粒直径d (因为晶界阻碍位错运动,故位错的平均自由程不能超过晶粒尺寸d),则:
(3)
随着晶粒直径d与塞积头与相邻晶粒内最近的位错源之间的距离r的变化情况如图3所示:
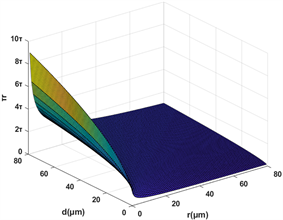
Figure 3. The change of τr with r and d
图3. τr随r与d的变化情况
在实际的晶粒滑移传递过程中,切应力
会被位错运动时所遭受的各种摩擦阻力所消耗,设被摩擦阻力消耗的切应力为
,其余部分
才是作用在滑移带上,构成位错塞积群的有效切应力。故上式应写为:
(4)
当
达到能触发相邻晶粒的滑移(即位错源开动)所需的最小切应力
时,变形就可继续,此时的外加切应力
,就是多晶体的屈服应力
,即 [13]:
(5)
可得:
(6)
上式如用正应力
表示,就得到Hall-Petch公式:
(7)
式中
是位错移动的摩擦阻力,
,是与晶界对滑移传播的阻碍有关的常数,它代表位错在障碍前被塞积的程度。
根据上面的推导过程,多晶体金属的拉伸屈服强度是由晶粒之间的滑移传递产生的。即切屑的形成是由于多晶体金属内的晶粒相互协调变形且切削层晶粒与工件基体分离产生的。这一现象可以在建立的多晶体模型中直观的表现出来。观察切削根金相图4,对比仿真现象图5,仿真现象与金相图相符。
3.2. 毛刺产生机理
观察切削仿真过程可以发现,在刀具即将离开工件时,在工件末端形成了毛刺。
仿真结果表明:在刀具靠近切出端部位时,工件末端晶粒的支撑刚度不足,随着刀具的前进,工件末端受到的切削力值达到GH4169的屈服强度临界值,形成了第四剪切区。可以从仿真现象发现,第四剪切区晶粒温度升高,发生热软化现象,如图6所示。第四剪切区晶粒由于热软化现象发生软化变形,使工件末端围绕支点发生弯曲变形和塑性剪切滑移变形。毛刺的形成可以分为三个阶段,如图7所示:
第一阶段为稳态切削阶段,工件末端材料弯曲变形极小,可以看作未发生弯曲,此时工件被切削处材料沿第一剪切区不断发生滑移位错。
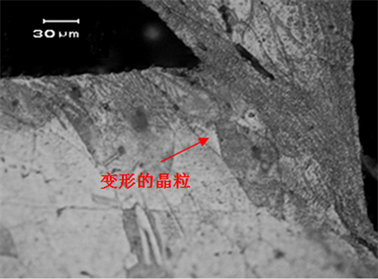
Figure 4. Metallographic picture of cutting root of deformed grain
图4. 变形晶粒的切削根金相图片
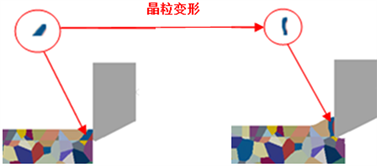
Figure 5. Grain deformation in cutting simulation
图5. 切削仿真过程中的晶粒变形
第二阶段为支点形成阶段,当刀具靠近工件末端时,切削力值达到材料的屈服强度临界值,导致工件末端发生剪切变形,形成了第四剪切区,如图8所示,这是毛刺形成的初始阶段。
第三阶段是毛刺的产生阶段,此时刀具逼近工件终端,第四剪切区晶粒由于热软化硬度进一步降低,被切削材料受切削力作用围绕工件末端支点O发生旋转,若切屑最终沿第一剪切区断裂,形成正毛刺,沿第四剪切区断裂,形成负毛刺,若切屑并未脱离工件,形成滞留毛刺。
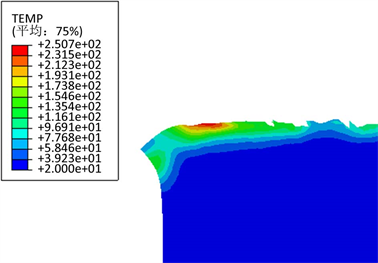
Figure 6. Increase of grain temperature in shear zone
图6. 剪切区晶粒温度升高
3.3. 切削厚度对毛刺高度的影响
建立了切削厚度为0.25 mm~0.5 mm~0.75 mm的有限元模型,进行切削仿真。观察现象发现厚度越大,毛刺高度越高,如图9所示。
假设毛刺的整个形成过程是在材料发生塑性变形时发生的,即工件材料的断裂不影响毛刺的形状与尺寸。
毛刺形成的过程如图10所示。直线AD为切屑的剪切滑移线,切屑沿着AD方向发生剪切滑移。直线AB为刀具进给方向。AB与AD的夹角为剪切角ψ0。根据切削原理有:
(8)
随着刀具的继续前进,毛刺逐渐产生。AE为第四剪切区中的剪切线,点E处受到的应力值为材料的剪切屈服强度。
随着切削过程的继续,毛刺开始逐渐产生,刀具由A点处前进到A1点处,此时材料不再生成切屑,由于工件末端的支撑刚度不足,材料的变形在第四剪切区发生,宽度方向不发生压缩变形。根据相关研究,在毛刺生成阶段,材料的变形只发生在E点处,即工件末端材料围绕E点发生旋转。设毛刺开始产生时,刀具刀口到工件末端的直线距离为s,即AB的初始长度为s。定义BE长度为a,CD长度为b,将a与b用s进行表示:
(9)
(10)
根据切削变形区处工件材料总体积不变的原则,即
,随着刀具的前进工件末端支撑高度不足,弯曲变形,围绕E点旋转,转角Ψ变增大,剪切角ψ0随之减小。假设毛刺产生过程中没有断裂现象产生,工件末端没有外力作用,最终使剪切角ψ0旋转减小至最小,即剪切面与AD2重合。为了便于后续的分析计算,由于旋转角度大致相同,近似的将四边形BEC2D2看为梯形。则有:
(11)
联立得:
(12)
对切深ap求偏导得:
(13)
可以看出随着切削深度ap的增加,毛刺高度H也随之增大。从图11进行分析,这是由于切削深度增大,会使四边形ABCD的体积增大,四边形ABCD的体积就是变形的面积,变形面积增加,导致了毛刺的高度也随着增加。
3.4. 切削速度对毛刺形态的影响
建立速度不同的有限元切削模型,对结果进行对比分析,如图11所示。
(a)
(b)
Figure 11. Simulation results at different speeds: (a) At 120 m/min; (b) At 200 m/min
图11. 不同速度下的仿真结果:(a) 速度为120 m/min时;(b) 速度为200 m/min时
由仿真现象可以发现,当切削速度较低时,切屑并没有从工件上完全撕裂下来,形成滞留毛刺。当切削速度较大时,切屑从工件末端脱落,形成负毛刺。这种情况是由于切削速度较低,切削力低,刀具行进到刀具末端时,切屑对支点的惯性力矩较小,切屑无法与工件基体分离,滞留在工件基体上,形成了滞留毛刺。随着切削速度的增大,切削力也增大,工件末端变形随之增大,第四变形区的应力值也随之增大,工件末端发生断裂,切屑脱离工件基体,形成毛刺。工件末端切屑与工件基体发生断裂的情况分为两种:
第一种是在刀具未切出工件前,切屑没有与工件基体分离。当刀具切出工件以后,由于惯性的作用,切屑围绕工件末端支点旋转,产生比较大的应力,切屑与工件的连接点发生断裂,滞留毛刺与工件基体分离,形成负毛刺。
第二种是由于切削速度足够大,在刀具切出工件之前,第四剪切区受到足够大的切削力,使得毛刺与工件基体发生撕裂,脱离工件基体,形成负毛刺。
可以发现,速度越大,越不容易形成滞留毛刺。因此在切削加工过程中,应该保持足够大的切削速度,杜绝形成滞留毛刺,来生成负毛刺,从而提升工件质量。
4. 总结
本文通过建立基于高温镍基合金材料的多晶体高速切削模型,结合实验与仿真结果,得出结论如下:
1) 所建立的高温镍基合金多晶体有限元模型能够很好地反映出金属材料的内部情况,使其更加接近真实的金属材料微观形貌。
2) 通过对不同切削深度条件下产生的毛刺进行分析,发现切削深度越大,形成的毛刺高度越高。这是由于切削深度增加,会使切屑的变形以及增大,最终刀具切出工件时,生成的毛刺体积也随之增大,从而使毛刺的高度增加。
3) 通过对不同切削速度条件下产生的毛刺进行分析,发现切削速度越大,越不容易形成滞留毛刺。这是由于切削速度的增加,会使切削力也随之增大。当切削速度较小时,切削力不足以使产生的切屑与工件基体脱离。当切削速度增加以后,切削力增大,工件末端变形增大,第四变形区的应力值也随之增加,工件末端发生断裂,切屑脱离工件基体,形成毛刺。所以切削速度越大,越不容易形成滞留毛刺。
致谢
历时将近两个月的时间终于将这篇论文写完,在论文的写作过程中遇到了无数的困难和障碍,都在同学和老师的帮助下度过了。尤其要强烈感谢我的论文指导老师——范依航老师,她对我进行了无私的指导和帮助,不厌其烦的帮助进行论文的修改和改进。另外,在校图书馆查找资料的时候,图书馆的老师也给我提供了很多方面的支持与帮助。在此向帮助和指导过我的各位老师表示最中心的感谢!
感谢这篇论文所涉及到的各位学者。本文引用了数位学者的研究文献,如果没有各位学者的研究成果的帮助和启发,我将很难完成本篇论文的写作。
感谢我的同学和朋友,在我写论文的过程中给予我很多素材,还在论文的撰写和排版过程中提供热情的帮助。
基金项目
国家自然科学基金:切削镍基高温合金的刀-屑界面形膜机制及刀具抗磨损机理研究*(51605043)。