1. 引言
飞机复材料结构不可避免地会受到外来物的冲击,如工具坠落、跑道碎石、冰雹等。由于复合材料结构最大的弱点是对冲击事件非常敏感,这些外来物冲击将会对结构的功能或性能(强度、刚度降低等)产生不利影响 [1]。特别是当结构受到低速冲击损伤时,虽然从结构表面无法观察到任何痕迹,但内部可能已经产生了大面积的分层,使压缩强度急剧下降,降到无损状态的40%甚至更低 [2]。因此复合材料的冲击问题研究一直是航空复合材料领域的主要研究热点。
长期以来,目视检测是评估飞机状态最经济、最快捷的方法,军民用飞机每次飞行后的地面巡检主要为目视检查。因此选用目视可以检测到的参量,如冲击后的凹坑深度,来表征飞机损伤,是目前飞机复合材料结构损伤容限设计的重要前提。目前飞机强度规范中均采用目视勉强可见冲击损伤(BVID)作为结构有可能被检测出的初始缺陷/允许损伤,飞机设计师确定复合材料压缩设计许用值时也主要依据含BVID冲击损伤的复合材料结构冲击后的压缩试验结果 [3]。因此研究含BVID冲击损伤复合材料结构的特性具有非常重要的意义。在该方面,国内外均进行了大量的试验与理论研究 [4] - [11],但主要集中于静力特性研究,对于疲劳特性研究较少。本文主要进行含BVID冲击损伤的国产T300级碳纤维织物复合材料层压板的压–压疲劳特性试验研究,通过试验获取了其S-N曲线特征、刚度变化和损伤扩展等疲劳特性。
2. 试验件和方法
2.1. 试验件
采用某国产T300级织物预浸料通过热压罐固化工艺制备了试验所需的复合材料大板,其铺层形式为[(±45)3/(0,90)2/(±45)2/(0,90)2/(±45)]S,层压板厚度为4.2 mm。将所制备的复合材料大板切割成ASTM D7136所需要的试验件尺寸 [12],试验件长为150 mm,宽度为100 mm,厚度4.2 mm,总数为36件。
2.2. 试验方法
含BVID冲击损伤层压板压–压疲劳试验步骤如下:
a) 先进行BVID冲击损伤引入(摸索BVID损伤的冲击能量,并对全部试验件引入BVID损伤);
b) 引入BVID损伤后,进行CAI静力试验(确定疲劳试验的应力应变水平);
c) 最后进行疲劳试验,对于106次循环未破坏的试验件,进行剩余强度试验。
2.2.1. BVID冲击损伤引入
BVID冲击损伤引入试验参照ASTM D7136/D7136M-2015“测量纤维增强聚合物基复合材料对落锤冲击事件的损伤阻抗的标准试验方法”进行 [12]。
冲击损伤引入采用直径16 mm的半球形钢冲击头,对试验件中心进行冲击试验。冲击时首先取若干件试验件进行能量摸索,确定BVID损伤(冲击后立即测量的凹坑深度为1 mm)对应的冲击能量,此后以该能量对剩余试验进行冲击。冲击后立即测量的凹坑深度在(1.0 ± 0.2) mm范围内认定其为有效的冲击损伤。冲击后对所有试验件进行无损检测。
2.2.2. CAI静力试验
从带有BVID冲击损伤的试验件中各取5件进行CAI (冲击后压缩)静力试验,测定该铺层含BVID冲击损伤层压板的静强度。静力试验参照ASTM D7137/D7137M-2012“含损伤聚合物基复合材料板压缩剩余强度性能的标准试验方法”进行。试验时以1.25 mm/min的加载速率对试验件施加压缩载荷,直至试验件破坏。试验件破坏前的最大载荷除以试验件的宽度和厚度可得试验件的CAI静强度。图1为CAI静力试验状态照片。
2.2.3. 疲劳试验
含BVID冲击损伤层压板压–压疲劳试验参照ASTM D7137/D7137M-2017“含损伤聚合物基复合材料板压缩剩余强度性能的标准试验方法”进行 [13]。试验前按照标准要求在试验件表面背对背地粘贴4个应变计,在试验件正中位置粘贴温度传感器。试验在INSRON电液伺服疲劳试验机上进行。采用分级法与升降法的组合方法测定S-N曲线。分级时疲劳载荷确定依据2.2.2测定的平均静强度,按照试验件平均静强度的百分数选取疲劳峰值应力,分别取80%、70%和60%静强度作为每一级的疲劳载荷峰值,每一级至少5个有效数据,测定含BVID试验件在给定应力水平下的疲劳寿命。采用升降法测定106疲劳寿命对应的疲劳强度(疲劳门槛值)。对于80%及以上高应力水平,统一采用5 Hz的加载频率,其他载荷水平统一采用7 Hz。所有试验件表面监控到的温升均没有超过3℃。疲劳后对未破坏的试验件,进行无损检测确定了损伤扩展情况,然后进行了静力试验以测定其剩余强度。
3. 疲劳S-N曲线
表1给出了采用升降法获取含BVID冲击损伤复合材料试验件疲劳门槛值(106次疲劳寿命对应的疲劳强度)的数据表。由表1可以看出,其升降法的应力区间在59%~63%,应力区间较小,该材料表现出较好的疲劳稳定性。按照GB/T 24176-2009计算其疲劳门槛值,可得其按照强度表示的疲劳门槛值为163 MPa,按照应变表示的疲劳门槛值为3880 με。按疲劳门槛值强度/静强度百分比表示的疲劳门槛值为63.4%。
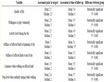
Table 1. Data sheet for determination of fatigue threshold by up-down method
表1. 升降法测定疲劳门槛值的数据表
图2给出了采用组合法绘制的含BVID冲击损伤复合材料试验件中值S-N曲线。由图2可见,含BVID冲击损伤T300级织物复合材料层压板的S-N曲线可以拟合为对数线性曲线。
4. 刚度变化
疲劳试验过程中试验件的刚度可以简单的表征为试验机夹头在载荷峰值与载荷谷值之间的位移差。如果在整个疲劳过程中,该位移差保持始终恒定,则表明试验件在整个疲劳过程中刚度未发生变化。如果该位移差在疲劳试验过程中不断变大,则表明该试验件的刚度在不断变小。
图3为典型的80%应力水平疲劳试验过程中载荷峰值与谷值处夹头位移差和循环次数之间曲线。可以看出:对于这类疲劳破坏循环次数在几万次之内的试验件,疲劳试验的初期和中期其刚度一直在缓慢减小;在临近疲劳破坏时(约破坏前的100次循环开始),试验件的刚度开始快速减小,直至突然破坏。
图4为典型的70%应力水平疲劳试验过程中载荷峰值与谷值处夹头位移差和循环次数之间曲线。可以看出:对于这类疲劳破坏循环次数在10万次之上的试验件,疲劳试验的初期和中期其刚度基本保持为恒定值,没有明显变化(变化小于1%);在疲劳试验的后期(约剩余5万次疲劳寿命),试验件刚度缓慢减小;临近疲劳破坏时(约破坏前的100次循环开始),试验件的刚度开始快速减小,直至突然破坏。
图5为典型的应力水平在疲劳门槛值之下(小于63.4%)未发生破坏试验件在疲劳试验过程中载荷峰值与谷值处位移差与循环次数之间曲线。可以看出:对于106次循环疲劳试验过程中未发生破坏的试验件,在整个疲劳试验过程中试验件的刚度基本保持为恒定值,没有明显变化(实际上也一直在缓慢减小,但变化小于1%)。
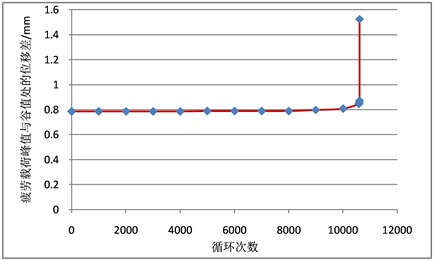
Figure 3. Curve: the change of the test specimen’s stiffness during fatigue of 80% stress level
图3. 80%应力水平疲劳试验过程中试验件刚度的变化曲线
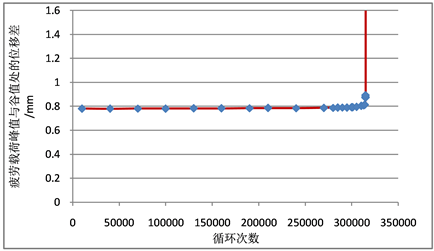
Figure 4. Curve: the change of the test specimen’s stiffness during fatigue of 70% stress level
图4. 70%应力水平疲劳试验过程中试验件刚度的变化曲线
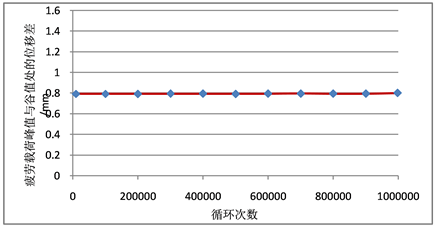
Figure 5. Curve: stiffness change of the test specimen with stress below fatigue threshold and without fatigue rupture during fatigue test
图5. 应力水平在疲劳门槛值之下且未疲劳破坏的试验件在疲劳试验过程中的刚度变化曲线
5. 损伤扩展
图6为一件在70%应力水平下进行疲劳试验的试验件在试验过程中采用超声C扫描无损检测所得的冲击分层损伤图像。该试验件的疲劳寿命为230,017次。由图中可以看到,在除疲劳末期的整个疲劳试验过程中,分层损伤一直在非常缓慢扩展,这种扩展主要发生在轮廓的边缘处,使“尖锐”或者“不连贯”的分层边界轮廓趋于“平滑”或者“连续”,而且这种损伤扩展不仅发生在层压板的最下面或者上面,而是同时出现在多个铺层之间。
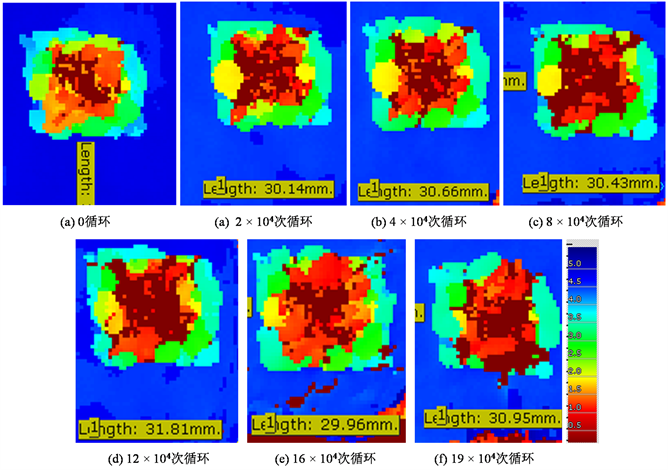
Figure 6. Delamination damage propagation in fatigue test
图6. 疲劳试验过程中的分层损伤扩展
图7中分别给出了两件分别在63%和61%应力水平下经过106次循环未发生疲劳破坏的试验件在疲劳试验之前和疲劳试验之后的超声C扫描无损检测图片。由该图可以看出,即使这些试验件在疲劳门槛值附件的应力水平下经历了106次循环未发生破坏,但在疲劳过程分层仍发生了缓慢地扩展。
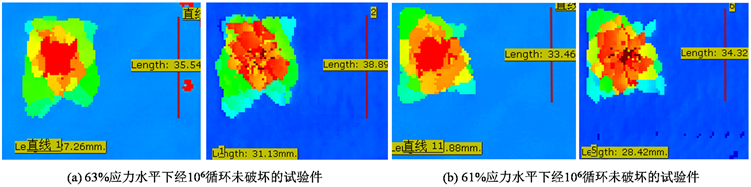
Figure 7. Delamination damage before and after fatigue test
图7. 疲劳试验前后的分层损伤扩展
根据上面的超声C扫描无损检测结果的对比分析,可以看出:在较高的疲劳应力水平下(约55%~70%),含BVID冲击损伤复合材料层压板的分层损伤实际上一直在非常缓慢的扩展,这种扩展主要发生在轮廓的边缘处,使“尖锐”或者“不连贯”的分层边界轮廓趋于“平滑”或者“连续”,而且这种损伤扩展出现在多个铺层之间。该结论和前面的第5节的刚度变化规律是一致的,这是因为刚度变化的正是由于冲击损伤的扩展所导致的。疲劳试验过程中随着分层的缓慢扩展,复合材料层压板试验件的整体刚度会发生缓慢的较小。
在使用“损伤无扩展”设计理念进行复合材料结构设计时,一定要关注结构所遭受的疲劳应力水平,在较高的疲劳应力水平下(约含冲击损伤结构静强度的55%~70%)冲击分层损伤会发生缓慢的扩展。因此在采用“损伤无扩展”设计理念进行复合材料结构设计时,进行适量的含冲击损伤复合材料结构疲劳试验(并在疲劳试验中监控损伤扩展情况)是非常有必要的。
6. 研究结论
a) 采用升降法获取该国产T300织物复合材料层压板含BVID冲击损伤的疲劳门槛值时,其升降法的应力区间在59%~63%,应力区间较小,该国产复合材料具有较好的疲劳稳定性。含BVID冲击损伤T300织物复合材料层压板的S-N曲线可以拟合为对数线性曲线。
b) 对于疲劳破坏循环次数在几万次之内的复合材料层压板:疲劳试验的初期和中期,其刚度一直在缓慢减小,在临近疲劳破坏时(约破坏前的100次循环开始)其刚度开始快速减小,直至突然破坏。
c) 对于疲劳破坏循环次数在10万次之上但不超过100万次的复合材料层压板:疲劳试验的初期和中期,其刚度基本保持为恒定值,没有明显变化(变化小于1%),在疲劳试验的后期(约剩余5万次疲劳寿命),其刚度开始慢减小,在临近疲劳破坏时(约破坏前的100次循环开始),其刚度开始快速减小,直至突然破坏。
d) 对于106次循环疲劳试验过程中未发生破坏的试验件,在整个疲劳试验过程中试验件的刚度基本保持为恒定值,没有明显变化(变化小于1%)。
e) 在较高的疲劳应力水平下(约静强度的55%~70%),含BVID冲击损伤复合材料层压板的分层损伤实际上一直在非常缓慢地扩展,这种扩展主要发生在轮廓的边缘处,使“尖锐”或者“不连贯”的分层边界轮廓趋于“平滑”或者“连续”,而且这种损伤扩展出现在多个铺层之间。
f) 在使用“损伤无扩展”设计理念进行复合材料结构设计时,一定要关注结构所遭受的疲劳应力水平。在较高的疲劳应力水平下(约静强度的55%~70%),冲击分层损伤会发生缓慢的扩展。因此在采用“损伤无扩展”设计理念进行复合材料结构设计时,进行适量的含冲击损伤复合材料结构疲劳试验(并在疲劳试验中监控损伤扩展情况)是非常有必要的。