1. 引言
利用铆钉将两个或两个以上的元件(一般为板材或型材)联接在一起的一种不可拆卸的静联接简称铆接。相比其他连接方式,铆接的工艺简单、重量轻、成本低联接可靠、抗振、耐冲击、相比螺接更具技术优势,故应用的比较普遍。
电磁铆接技术起源于上世纪60年代美国。主要是为了解决波音公司普通铆接存在的问题而产生的一个铆接技术。电磁铆接在铆接难以成型的材料过程中起到了积极的作用,但是当时的铆接采用的是高压铆接,易出现裂纹,工具也十分笨重,因此没有得到广泛应用。1986年低压电磁铆接研发成功后,电磁铆接技术开始大量应用并得到快速发展 [1]。
在我国,佘公藩1981年开始进行电磁铆接技术的研究,并研制了电磁铆接设备。进入九五后,曹增强等人对电磁铆接技术进行较为系统的研究,并对低电压电磁铆接技术也进行了初步的研究 [2]。高彬采用有限元方法对应力波安装干涉配合紧固件的过程进行了模拟,对应力波安装过程获得一定新的认知 [3]。
本文主要采用直径为12 mm的铆钉进行铆接,并且采用电磁铆接技术,通过使用ANSYS软件对铆接过程进行仿真计算。
2. 有限元模型建立
2.1. 仿真方法选择
有限元仿真设计是近年来使用较多的一种仿真设计方式,因为其具有安全、可靠、准确性高等优势,越来越多的领域开始使用有限元仿真 [4] [5] [6]。本文采用ANSYS软件进行仿真,其建模简单,与制图软件可以进行直接的数据配合、计算分析快捷和清晰的特点,广泛应用于生产前期的模拟仿真。
电磁铆接是电磁成形的一种应用,成形过程更为复杂。本文中采用的是松散耦合法(见图1),对电磁场和变形场各自进行建模分析;电磁场分析采用ANSYS软件、变形场计算采用LS-DYNA软件进行分析。
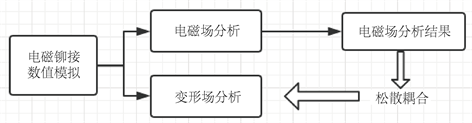
Figure 1. The simulation flow of loosely coupled methods
图1. 松散耦合仿真流程
2.2. 电磁场模型建立
根据电磁铆接原理,发生作用的元件是线圈和驱动片,故可把复杂的电磁场模型简化成线圈和驱动片的二维模型;本文中建模的线圈匝数为17,线圈与驱动片的间隙为1 mm。由于只考虑对电磁场起作用的线圈和驱动片,所以根据其模具具有对称性,在ANSYS建模中我们只需要建立其1/2就行;由于实际的电磁场附近会有空气场的影响,所以我们需要建立近空气场模型和远空气场模型,近空气场模型半径是其驱动片半径的两倍,远空气场模型的半径是近空气场模型半径的两倍;其中线圈、驱动片以及近空气场的单元类型为PLANE13单元;远空气场的单元类型为INFIN110单元;对每个部分进行划分,对于线圈和驱动片用规则划分,近空气场用自由划分、对远空气场进行放射性划分;电磁场的模型和材料及单元类型如图2。
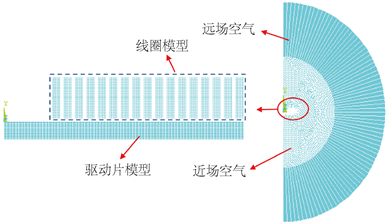
Figure 2. The FEM model of electromagnetic fields
图2. 电磁场有限元模型
2.3. 变形场模型建立
根据实际铆接模具建立如下模型,由于结构是对称的,所以我们只需要建立模具的1/2分析即可;模型中主要包含线圈、驱动片、放大器、冲头,铆钉、板材5部分。铆钉材料为45钢,铆钉直径为12 mm,本文铆接应用对象为卡车车架,因此,板材厚度分别选为5 mm和4 mm。采用PLANE162单元类型对整个模型进行网格划分,结果如图3所示。
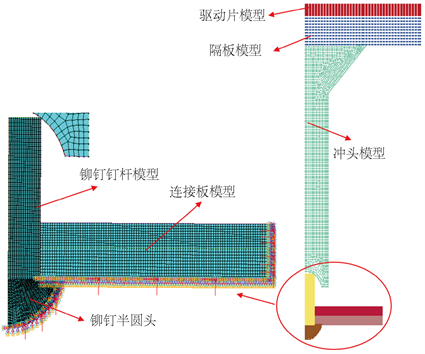
Figure 3. The FEM model of mechanical fields
图3. 变形场有限元模型
3. 结果分析与讨论
3.1. 电磁结果分析
3.1.1. 驱动片上磁场强度
从本文设置的40个子步中提取第1、11、21、31子步分别进行电磁场强度分析;如图4为电磁场强度矢量和云图,在通电后形成的涡流磁场从下往上、从右向左扩散。随着时间的增长,磁场分布变得离散均匀,这说明电流产生的磁场在工件中产生了感应电流同样也产生了感应磁场;两磁场的斥力作用于电压放大器和冲头,使铆钉被冲击成形。
(a) 第1个子步
(b) 第11个子步
(c) 第21个子步
(d) 第31个子步
Figure 4. Magnetic field intensity results on the driver plate
图4. 驱动片上磁场强度结果
3.1.2. 驱动片上磁通密度
驱动片上磁通密度如图5所示,由四个子步云图可知,在通电流的开始,驱动片下方的磁通量密度为0,而驱动片上方的磁通量密度很大,驱动片表面聚集了大量的磁通密度;这是由于高强度的交变电流作用在线圈上,在驱动片和线圈的间隙中产生较大的交变磁场,然后驱动片中形成电涡流,电涡流又会形成磁场。由实验结果图可知,驱动片下方的磁通密度随着时间的增加而增加。涡流磁场和交变磁场之间的相互作用力促进铆钉铆接的过程。这样不仅加快了铆接速度,同样会使得铆钉干涉均匀,干涉量小。
(a) 第1个子步
(b) 第11个子步
(c) 第21个子步
(d) 第31个子步
Figure 5. Magnetic flux density results on the driver plate
图5. 驱动片上磁通密度结果
3.2. 变形场结果分析
3.2.1. 铆接过程
冲头下压,导致铆钉成形的过程主要集中在前二十个子步中,仅占整个铆接行程的三分之一左右,由此可见铆接速度之快。铆接过程完成后,冲头向上运动,回到原来的位置,为下一次铆接做准备。由于铆接过程中,变形较明显部位主要集中在铆钉上,所以单独截取了前三十个子步中不同过程的铆钉的变形情况。由图6可以看出,铆钉的塑形变形最先发生在铆钉杆与冲头接触的部位,整个铆接过程中塑性变形主要发生在铆钉杆的上方以及刚与铆接上板接触的地方,铆接完成后的形状与铆钉圆头相似。塑形变形最明显的区域主要集中在铆钉头与冲头接触的那一小部分区域。通过对比图6(e)和图6(f)发现,由于弹性能的作用,铆接头发生了些许偏移。
3.2.2. 铆接应力分析
数值模拟过程给出了不同时刻应力应变在不同单元的分布情况,如图7。图7为四个不同时刻Y方向的应力变化图。五个主要部件的应力具有一定程度的变化,其中铆钉处的应力分布最为复杂,变化最为明显。铆接过程中,冲击载荷势必会影响两块铆接板,因此两块铆接板的应力变化也很明显。因为铆接过程成形效率高,成形速度快,所以部件残余应力小。
(a) 第1个子步(b) 第15个子步
(c) 第28个子步 (d) 第40个子步
Figure 7. Stress distribution results during electromagneticriveting
图7. 铆接过程应力分布结果
4. 结论
(1) 驱动片上磁场强度和磁通密度与线圈厚度中心相对位置最大,并且越靠近线圈厚度中心大小分布越均匀。
(2) 由于集肤效应作用,磁通密度沿着驱动片厚度方向,由靠近线圈一侧向另一侧逐渐减小,主要分布在驱动片表层。
(3) 在线圈磁场和感应涡流磁场斥力作用下,铆钉变形和应力分布相对均匀。
基金项目
湖南省教育厅一般项目(18C0208)资助。