1. 前言
蓝宝石衬底(Sapphire substrate)是具有优异的光学性能、机械性能和化学性能的物质,该物质的表面质量对器件质量以及寿命有着重要影响,同时具有高强度与硬度、耐高温、耐腐蚀、透光性能好及电绝缘性能优良等一系列优良的理化特性,使得蓝宝石成为了极好的半导体、超导衬底材料 [1] [2] [3]。蓝宝石衬底需要经过切割、研磨与抛光等一系列工序加工而成,其中在研磨工艺上的加工需求:具有良好的表面品质与高切削效率,并能塑造表面粗糙度,提高工件的表面精度等。研磨粉料介质在选用上,大部分以碳化硼(Boron Carbide)与碳化硅(Silicon Carbide)为主,其中碳化硼硬度较高,仅仅次于立方氮化硼以及金刚石。另具有高温耐磨性质,故适合循环使用,使得碳化硼成研磨加工首选材料,常见于产业量产中使用 [4] [5] [6]。
研磨工艺的均匀性与加工时间、质量及成本有直接的影响,是生产中直接受控的重要参数之一。双面研磨是以磨粒的微小塑性切削与滚轧为主体形式对材料进行去除。作为抛光前道工序,需满足粗糙度(Ra)、表面最大深度(Rt)以及表面刮痕(Scratch)等,因此磨粒的颗粒大小分布与质量状况会对加工过程产生一定影响,由此可知磨粒对研磨加工的重要程度 [7] [8]。
原材碳化硼微粉经由处理与各式破碎加工,以及分选、包装与运送等,使碳化硼成本普遍处在高价位,不利于进行成本降低或节约使用等改善项目推行 [9]。为进一步提高碳化硼磨料的再使用效率,本研究参考了文献 [10] [11] 的方法,通过一系列流程得到中心粒径D50在JIS#280范围的微粉。本研究通过磨液调配,测试回收再处理的碳化硼微粉在实际量产上的状况,分析加工后蓝宝石衬底的品质,进而提供产业一种可再利用的方式。
2. 研究方法与步骤
研磨加工后的废液中,仍含有部分粒径较大的碳化硼颗粒,故本研究对废液中的碳化硼颗粒进行处理与筛分,对可使用的磨粒与全新碳化硼以及润滑/分散剂经一定比例混合,再次应用于研磨加工,实现再次循环利用。
2.1. 研磨微粉制备
研磨微粉是一次研磨后的废液,在废液收集池进行处理,由收集池中沉淀后的废浆料,经过一系列步骤制备而成。总体大致可分为3步骤,包含:1. 物理处理;2. 化学处理;3. 分析检验。具体说明,物理处理为废液池中捞出的碳化硼废弃的粉料,经过烘干与再破碎后,进行200网目筛分,其目的是剔除较大杂质,如来自研磨盘面的铁削以及蓝宝石衬底的碎渣等。第2阶段的化学处理为此废液中除了碳化硼外,另含有分散剂与切削液等各种化学成分混合组成,因此要得到可用的微粉,需再通过酸与碱洗,对已一次筛分后的粉进行表面的改质与分散。第3步骤为分析与检验,通过多次的水洗烘干筛分出不同规格粒径的微粉,最终对成粉的外观,颗粒形态以及粒径分析进行检测判定。
2.2. 粒径及外观分析
本次研究回收的碳化硼微粉,使用激光粒度分布仪(厂牌:丹东百特仪器公司,型号:BT-9300ST),检验后汇总粒径分布如表1所示,与JIS#280规格相近,D50规格约在44~51 µm,整体粒径范围约在51~56 µm。再由显微镜形貌,如图1,可看出整体筛分后并无其他金属或氧化铝等杂质存在,颗粒呈均匀分布,色泽整体为可用的黑色,碳化硼颗粒形貌圆滑,未具有片状或长条状等粉料,且亦可发现有些颗粒是经磨削破碎过。
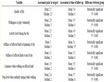
Table 1. Specification of particle size after screening (unit: µm)
表1. 筛分后粒径规格表(表中单位:µm)
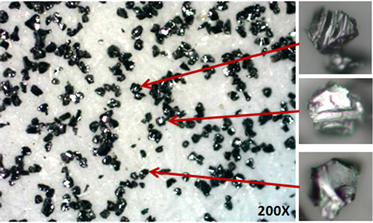
Figure 1. The morphology of the recovered fine powder under the microscope after screening
图1. 筛分后显微镜下回收微粉形貌
2.3. 导入量产实验方法
本次实验使用以业界主流的研磨机(厂牌:苏州博宏源精密机械制造有限公司,型号:22BF-4M5PL)进行,实验应用于研磨精磨加工。在实验设计中,机体参数设置为:流量500 mL,压力为3.8 Kpa,下盘(逆时针旋转)转速为22 rpm,中心齿轮(顺时针旋转)与内齿圈(逆时针旋转)转速设置比例为1:2。同时对粉料的不同配比应用性能进行验证:对照组(CTL, Control)设置为4:0 (全使用新粉),实验组(Experimental)设置为3:1、2:2、1:3以及0:4 (全使用回收粉)等条件比例下(粉料配比以kg计算),并添加1 L悬浮分散剂,以及20 L的水混合作业观察。粉料的不同配比影响蓝宝石衬底片的各项参数,因此在作业过程对其各实验条件进行移除率、表面粗糙度以及外观良率进行比较分析。
3. 结果与讨论
3.1. 移除率分析
图2为移除率对比分析,对照组(CTL, Control)为全新碳化硼微粉,移除率约在2.74 µm/min;实验组1 (Exp.1, Experimental)为3 kg新粉与1 kg回收微粉条件,其移除率为2.66 µm/min。其馀各实验组依序为新粉与回收粉混合比例2:2、1:3以及0:4 (全使用回收粉)。由结果可得知,全新粉为JIS#240使用时移除率较高,系因游离磨料对工件的滚轧作用明显,但随者回收粉混合比例提升,使得大颗粒粉料减少,整体粒径降低进而使移除率下降,且呈现正相关。此说明由于粉料颗粒较大,在相同压力转速等条件下,同一时间内在研磨区域的磨料颗粒越少,并且由于磨料的均匀性问题,将存在部分小颗粒,大小颗粒存在研磨区域内使得部分小颗粒受力不佳,在相同总压力下每个受力颗粒的分压越大,对加工过程中对表面进行微切削获得较大的材料去除量。若全使用回收微粉会因粉径过低而使得移除率降至最低,如:Exp.4约2.03 µm/min,移除率不断变低导致作业时间增长,作业时间增长影响产出效率,但全新粉成本耗用高,而如Exp.1的3:1移除率可与全新粉差异可接受。故此可建议回收后的微粉可与新粉配比在一定的作业效率范围内混合使用,使移除率维持在一定范围内,降低新粉的使用以节约成本。
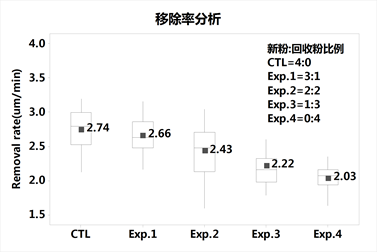
Figure 2. Analysis of removal rate of different experiment conditions
图2. 不同实验组合的移除率分析
3.2. 表面粗糙度分析
图3是不同实验组合的表面粗糙度分析。用以粗糙度仪(厂牌:Mitutoyo,型号:S-3000)测量全新粉料的对照组Ra约为1.02 µm,配比3:1、2:2、1:3以及0:4的实验组Ra分别为0.99 µm、0.90µm、0.88 µm与0.88 µm,由实验结果可以观察到随着对照组中回收粉比例的不断增加,碳化硼微粉的Ra值有不断下降的趋势,其中新粉及微粉为3:1配比的实验组1 (Exp.1)与全新粉对照组(CTL)的Ra较为相近,直至Exp.3与Exp.4达到0.88 µm接近相同。探究其原因可能为随着研磨加工进行,一部份微粉由于作业压力使之压入研磨盘中,进行磨削加工导致粉料粒径下降,当粉料粒径下降至一定程度,磨料崩碎切削所塑造的表面微裂纹降低,其表面粗糙度改变。蓝宝石衬底研磨加工是磨料在一定压力参数下相对于工件转动和磨料颗粒滑动摩擦的作用现象,而此游离态磨料依靠磨料在工件和研磨盘之间滚轧,由于铸铁研磨盘本身的弹性模量较大,使衬底表面脆性裂纹加剧,损伤较严重,此现象在当磨料粒径越大时,体现在Ra会越明显。另一方面,在混合配比的实际操作中,颗粒粒度大小不一致、颗粒在研磨剂中分散性较差,可能导致磨料在盘面上的分布及衬底表面接触的磨液不均匀。由本次实验确认,实验Exp.1的Ra均值与对照组CTL是最为相近,整体Ra差异值可接受,故混合比例以3:1与全新碳化硼微粉粗糙度差异较小,此比例进行加工作业尚可接受。
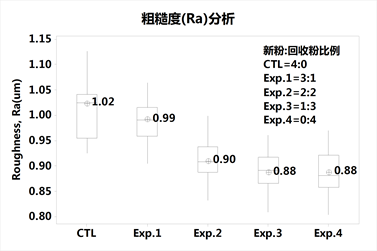
Figure 3. Surface roughness analysis of different experimental conditions
图3. 不同实验组合的表面粗糙度分析
3.3. 表面质量分析
表2为作业外观良率分析表,在研磨加工过程中,衬底会因局部受压异常等导致崩裂或表层刮伤等缺陷,此通常是由碳化硼的颗粒与杂质状态,以及作业期间引发的团聚现象所引起。经由测试结果可知,使用全新微粉的对照组良率平均为99.66%,使用配比3:1、2:2、1:3以及0:4的良率依序为99.67%、99.63%、99.62%以及99.44%。回收粉配比在1:3以上(Exp.1~Exp.3)的良率差异仅在0.01~0.04%之间,但Exp.4已与CTL差异至0.22%,显示在此条件下已对衬底外观崩破造成损失。使用回收粉料的占比越高使的作业外观的良率降低,造成该实验结果的原因可能为大小颗粒存在比例提高,使衬底研磨后的表面容易产生微划痕与亚表面损伤等质量缺陷提高。另因粉料粒径低使切削率降低,加工时间变长进使崩破损伤机率变高。综合上述,建议能符合量产作业需求的条件在新粉与回收粉配比1:3以上,仍可获得较佳的良率水准。
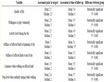
Table 2. Appearance yield analysis table
表2. 作业外观良率分析表
4. 结论
本研究针对废弃的碳化硼微粉进行物理化学等处理,通过一系列流程得到中心粒径D50约在44~51 µm范围的微粉,通过实际量产作业得知全使用回收微粉会因粉径过低而使得移除率降低,故使用回收后的微粉可与新粉配比合并使用,使移除率维持在一定范围内,可降低新粉的使用。而磨料崩碎切削所塑造的表面微裂纹,由于新粉与回收粉搭配3:1作业下Ra分别在1.02 µm与0.99 µm较为相近,以及表面良率分析上回收粉配比在1:3以上与对照组99.66%的差异仅在0.01%~0.04%范围内,较佳。全新碳化硼微粉与回收的碳化硼粉混合比例在3:1时的移除率、表面粗糙程度、作业外观良率和与使用全新碳化硼微粉得到相近结果,说明在一定程度全新碳化硼微粉中加入一定比例的微粉可以在较不影响作业时间、良率以及产出效率的情况下降低成本。综合上述,本研究在废碳化硼的微粉回收与加工再应用结果是可被接受,并且能够对研磨废液实行高效利用,故可将此方案导入于量产作业上,提供产业一种可再利用的方式。