1. 引言
中国石油天然气管道第二工程有限公司(以下简称“管道二公司”)在克拉苏气田克深5区块试采地面工程中,在传统施工工艺的基础上,创新工艺管线模块化施工技术,采气单井井场工艺管线现场预制率达95%,工艺管线现场安装全部通过法兰连接,实现现场快速安装或者搬迁,节省施工时间60%以上,在维护、操作和管理上更加方便安全。2016年至2018年,管道二公司应用本工法先后完成克拉苏气田克深5区块试采地面工程井场4座、伊拉克鲁迈拉油田地面项目井场14座、长庆油田第二采气厂2018年产能建设地面工程井场21座工艺管线施工,施工成本低、施工周期短,设备重复利用效率高。管道二公司通过总结、梳理形成《油气田井场工艺管线模块化施工工法》,为类似油气田井场工艺管线安装工程施工提供良好的技术借鉴。
“油气田井场工艺管线模块化施工技术”2017年荣获中国石油管道局工程有限公司技术革新二等奖。
2. 工法特点
2.1. 模块化预制功效高
井场工艺管线分成多个独立的预制模块,每个模块具有独立的结构,单独安装成橇,模块化焊接预制率达到95%以上,工期缩短60%。
2.2. 安装速度快、安全风险低
井场预制模块之间、预制模块与采气(油)树、放空管线之间通过法兰连接,安装速度快,且为不动火安装,有效降低油气场所作业的安全风险。
2.3. 避免工序交叉、便于整体吊装
将传统的混凝土管墩及设备墩改为两个钢制安装撬,管墩基础为整体条形基础。可提前在场外进行预制焊接,避免了与土建的交叉施工。每个模块具有独立的结构,便于后续整体吊装。电气仪表设备可同时预制安装就位,减少了电气仪表机组的现场工作量。
2.4. 可重复利用、经济效益好
井场工艺管线可在因特殊原因停井时直接拆卸、搬迁至其他井场进行快速安装,工艺管线及设备重复利用率高。
3. 适用范围
本工法适用于DN80-DN200,输送介质为原油、天然气、地下水等井场工艺管线安装施工。
4. 工艺原理
根据井场标准化设计图纸,结合井场工艺设备及仪表管阀件分布情况,对其进行功能分析和分解,在此基础上合理划分并设计施工标准撬装模块,采用各模块独立预制拼装、现场整体就位组合的施工方法,快速完成单井地面建设,最终实现缩短工期、降本增效的目的。具体关键技术工艺原理如下:
4.1. 模块划分技术
根据井场标准化设计图纸中工艺设备及仪表管阀件的分布情况,遵循方便后续吊运、组装的原则,利用三维制图软件,将井场工艺管线和设备划分为多个标准撬装模块。
4.2. 模块化预制技术
以法兰为界,将各标准撬装模块细化分解为预制单元,按照设计图纸及现场测量数据绘制单管图,利用预制平台的胎具对管道、设备等进行空间定位,完成各预制单元组对焊接。利用各类型钢制作撬装底座,结合井树及撬装基础等的实际位置、标高,在撬装底座上完成各撬装模块的成撬拼装。
5. 施工工艺流程及操作要点
5.1. 施工工艺流程见(图1)
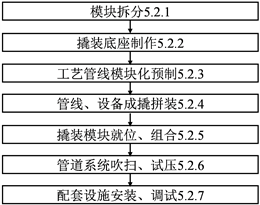
Figure 1. Construction process flow chart
图1. 施工工艺流程图
5.2. 操作要点
5.2.1. 模块拆分
模块划分需要结合各部分工艺管线不同的功能和安装位置,利用三维制图软件分解成多个独立的模块如(图2)所示。各模块独立预制,通过法兰连接拼装成撬,整体吊运至井场就位组合,完成井场工艺管线安装。
模块划分原则:工艺设备及仪表管阀件密集管段成撬原则;模块之间法兰连接原则;方便后续吊运、组装原则。
下面以KS501单井为例,介绍各模块划分要点: [1]
克拉苏气田克深5区块试采地面工程采用标准化井场设计,井场工艺管线主要由三部分构成:高压采气树部分、放空及计量部分、连接管部分。
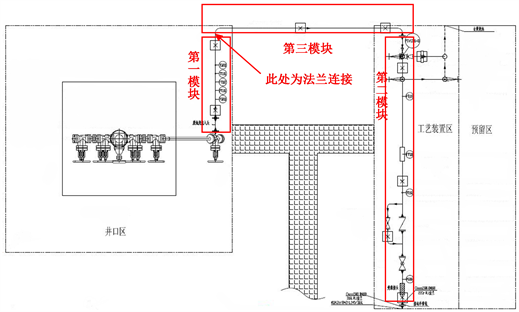
Figure 2. Schematic diagram of module division
图2. 模块划分示意图
1) 第一模块
第一模块为高压采气树部分,主要包括甲醇加注头及配套阀组、压力表及压力变送器、温度表及温度变送器如(图3)所示。
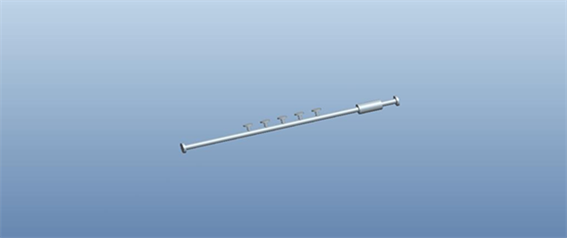
Figure 3. 3D model of the first module process pipeline
图3. 第一模块工艺管线三维模型
采气树的安装一般由钻井单位完成,试油完成后井树如(图4)所示。井场试油完成后只安装至一级节流部分,然后井盖封存如(图5)所示,待正式施工后再安装二级节流部分。
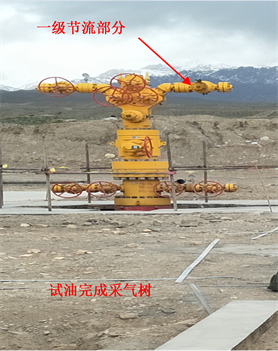
Figure 4. Schematic diagram of well tree after oil test
图4. 试油完成后井树示意图
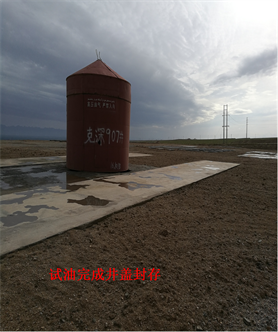
Figure 5. Block diagram of well tree after completion of oil test
图5. 试油完成井盖封存图
采气树二级节流部分在井盖吊装以后才能安装。因为一级节流球阀、二级节流角阀短节不是固定长度(主要是重复利用造成),所以每一口井的采气树高度都会不同,如果都按照统一高度安装,后期施工会造成管件和焊道增加,如(图6)所示。为避免出现以上情况,第一模块预制时将双相不锈钢管预制到水平弯头连接部分,并在此位置增加2片法兰,以便与第三模块快速安装拆卸。具体位置如(图7)所示的点“1”。
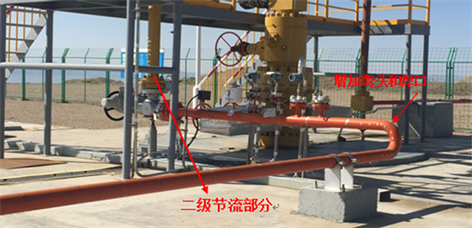
Figure 6. Schematic diagram of traditional single-well wellsite process pipeline
图6. 传统单井井场工艺管线示意图
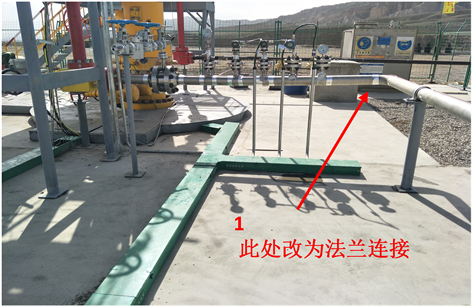
Figure 7. Schematic diagram of the first module process pipeline
图7. 第一模块工艺管线示意图
2) 第二模块
第二模块为放空及计量部分:主要包括工艺管线放空阀组、超声波流量计、出站球阀及预留球阀组、绝缘接头、压力表及压力变送器、温度变送器、出站材质转换法兰如(图8、图9)所示。
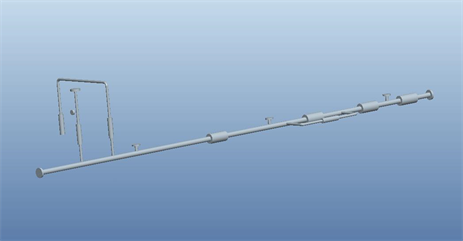
Figure 8. 3D model of the second module process pipeline
图8. 第二模块工艺管线三维模型
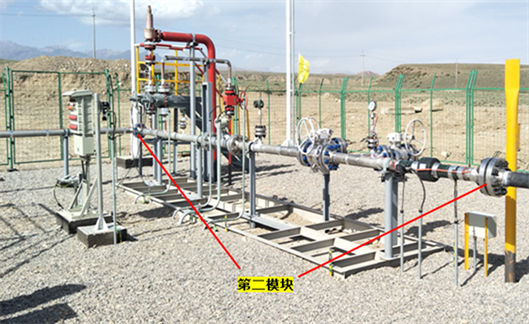
Figure 9. Schematic diagram of the second module process pipeline
图9. 第二模块工艺管线示意图
第二模块连接放空管线,如(图10)所示,为线路紧急放空使用,设计压力较低,后端连接井场外焚烧池,管线材质为普通碳钢管,施工难度相对较低,且不在三大模块范围内,可根据资源前期施工,施工时不与三大模块冲突,可待三个模块主体连接及试压完成后再接入井场工艺管线。
3) 第三模块
第三模块为连接管部分,用于连接第一模块与第二模块。在第一模块的90˚弯头处增加一对法兰,由原来的弯头固定连接变为法兰活动连接,便于快速拆卸。三个模块通过法兰连接,最终实现井场工艺管线成型。如(图11)所示。
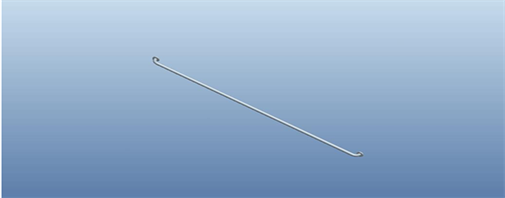
Figure 11. 3D model of the third module process pipeline
图11. 第三模块工艺管线三维模型
连接管线最终长度通过撬装模块现场组合时实际测量确定。测量时,要先将第一模块和第三模块的水平调到高度一致,轴线一致,避免强力组对造成法兰处泄露或增加焊口,可以通过管支撑的高度进行调节。
5.2.2. 撬装底座制作
根据设计图纸,结合现场实际情况,对各类基础进行统一浇筑,同时使用型钢和钢管制作整体撬装底座。制作撬体底座时利用水准仪、全站仪等核对基础和撬体的标高,避免因高度差异而造成的后期组装错位。撬装底座制作如(图12)所示。
5.2.3. 工艺管线模块化预制
1) 积极组织图纸会审,明确细化预制单元。会同设计、监理单位等相关方,开展图纸会审。结合设计图纸及现场测量数据,明确预制深度,细化各模块至预制单元,并绘制单管图,各预制单元通过法兰连接拼装成撬。
2) 根据物资到场情况,合理选择预制场地。如果井场物资到货时间集中,可将预制场设置在井场附近,利用挖机平整预制场场地,井场物资使用吊车和平板车集中吊运至预制场,模块预制和拼装全部在现场完成,可减少后期运输和吊装就位工作量,但需采取措施对现场焊接环境(如风速、温度、湿度等)进行有效控制。如果井场物资到货分散,可将预制场设置在营地内,利用营地市电进行预制,可全天候开展模块化预制,质量、进度可控,但后期预制模块吊运、就位工作量相对较大。
3) 检查核对到货物资,分类入库妥善存放。配合监理、设计单位等相关方,完成到场物资验收。严格按照设计文件及规范要求,检查核对到货物资材质、规格、数量、质量等。验收合格的物资分类存放,质量证明文件、检验报告等出厂材料分类造册。物资存放需重点保护管件坡口、法兰密封面、防腐层等。同时,应避免不锈钢和碳钢直接接触,杜绝“碳污染”发生。如遇特殊情况要在室外存放时,必须进行管口封堵,并采取必要的防晒、防雨措施。对于未通过验收的物资,应立即退场,严禁入库、使用。
4) 利用胎具空间定位,预制安装工艺管线见(图13)。工艺预制遵循先大管后小管、先水平后纵向、先埋地后地面的预制顺序。选择可调支架作为胎具,完成工艺管线、设备的空间定位,如图13所示。若预制单元为不锈钢材质,需在其与胎具间加垫10 mm厚橡胶板,以减少震动造成的金属间相互磨损,同时杜绝“碳污染”。可调支架的高度可利用扳手或管钳转动锁紧螺母进行调节,其亦可用于后期工艺管线、设备成撬拼装过程,制作简便,应用广泛,可批量制作。组对前,按照施工图核对、登记每根管子的管号、炉号、管径、长度、壁厚、材质等信息,将管口的尺寸进行级配,保证管口组对尺寸符合焊接工艺规程要求。组对由管工、起重工、机械操作手完成,所用的吊装设备、对口器、吊具等应具有足够的载荷能力,且处于正常工作的安全状态下。电焊工应持有效资质证件,并通过上岗考试,按照监理批准的焊接工艺规程要求施焊。仪表根部元件密集管段的焊接可采用反变形法,防止管段受焊接应力影响弯曲变形。如井场工艺管线材质为双相不锈钢,焊接过程中必须严格控制线能量和层间温度,以保证焊缝和接头处具有优良的力学和耐腐蚀综合性能,焊后须使用铁素体检测仪进行铁素体含量及分布检测。焊接完成后,管口处须采取有效措施进行封堵,同时,按照要求做好各工序施工记录的记录工作。
5.2.4. 管线、设备成撬拼装
撬装底座及各模块工艺管线预制完成后,按设计图纸将预制管线、阀门、可调支架等拼装、固定在撬装底座上,预制管线与阀门之间通过法兰连接,可调支架与撬装底座通过满焊连接。预制管线、阀门等应按照管道系统图顺序、对号拼装,法兰连接应符合规范要求。
5.2.5. 撬装模块就位、组合
1) 管线、设备成撬拼装完成后,利用吊车和半挂车将其从预制场吊运至井场。吊运过程中应注意对撬装模块的成品保护,避免撬体损伤、变形。吊装时,撬体两端应设专用牵引绳,以便撬装模块的准确就位。运输时,必须采用绳索固定撬体,并妥善设置橡胶皮或其他软质材料衬垫,以免运输途中颠簸损伤撬体。
2) 撬装模块就位前,需确认撬装基础验收合格,并在基础上测量放线,确定装置轴线,使得第一和第二模块轴线平行,同时实测第一和第二模块的跨距,提前预制第三模块。现场撬装模块就位应保证撬装底座水平,若基础水平度不足,应加垫铁,垫铁选择合适厚度,每处垫铁不应超过3块。
3) 第一和第二模块就位完成后,调节可调支架高度使得井口工艺管线与井口节流阀高度一致,以便于井口工艺管线与井口节流阀连接。将第三模块吊装就位,通过法兰连接与第一、第二模块连接为一个整体。在第三模块预制过程中,可预留一道焊口作为调整焊口,各模块就位组合时现场焊接,用以解决采集树出口的位置偏差。利用可调支架使井场工艺管线向出站水平方向有2‰落差,防止工艺管线内积存液体造成腐蚀。
5.2.6. 管道系统吹扫、试压
1) 管道吹扫使用空压机进行爆破吹扫,吹扫流程与工艺流程一致,爆破压力控制在0.3 MPa~0.5 MPa之间,爆破膜选用青稞纸。不参与系统吹扫的设备及管道系统,应与吹扫系统隔离。管道支吊架应牢固,必要时进行加固。管道吹扫后在管道末端排气口用白靶检查,以无铁锈、灰尘及其他杂物为合格。
2) 管道试压分为强度试验和严密性试验,试验介质的选择应符合设计及规范要求。升压时速度应缓慢平稳,达到30%强度试验压力时稳定15 min,检查所有管件和连接段是否有异常情况。确认无异常继续升压至60%强度试验压力,停止升压,稳定观察15 min,检查是否有异常情况和系统的完整性。确认无异常继续升压,直至试验压力。压力稳定后,开始4小时的强度稳压,试验管段无变形、无渗漏、且压降不大于1%试验值,即通过强度试验。强度试验合格后进行严密性试验,严密性试验压力稳定后,开始24小时的严密性稳压,试验管段无泄漏、且压降不大于1%试验值,即通过严密性试验。
5.2.7. 配套设施安装、调试
吹扫、试压后,按施工图将放空管线与第二模块工艺管线连接并安装安全阀,对管线进行氮气置换。同时,完成设备间内的通信、电气设备的安装、调试,达到投产条件。
5.3. 劳动力组织
以KS501井场为例,其工程量如(表1),其劳动力配备如(表2)。
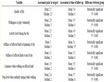
Table 1. KS501 Wellsite engineering volume
表1. KS501井场工程量
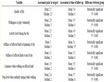
Table 2. Workforce Allocation Table
表2. 劳动力配备表
所列劳动力(表2)是单个井场人力配备情况,当多个井场同时施工时,需适当增加焊工、管工、工艺配合人员和土建施工人员。
6. 材料与设备
6.1. 设备
以KS501单井施工为例,主要施工设备见(表3)。
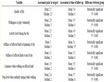
Table 3. Main equipment configuration table
表3. 主要设备配备表
6.2. 材料
以KS501单井施工为例,主要材料配备见(表4)。
7. 质量控制
7.1. 井场工艺管线安装施工中执行的质量标准
1) 《石油天然气建设工程施工质量验收规范》 SY4200—SY4209
2) 《油气田集输管道施工规范》 GB50819-2013
3) 《承压设备无损检测》 NB/T 47013-2015
4) 《石油天然气站内工艺管道工程施工规范》 GB 50540-2009
5) 《2205 双相不锈钢材料焊接施工及验收规范》 Q/SY TZ 0110—2004
7.2. 质量保证措施
1) 工艺管线安装前必须将管内泥土、砂石等异物、杂物、污物清除干净,经监理工程师进行确认后方可安装施工。
2) 如果管件和管材材质较多,必须仔细对照设计图纸,避免材质使用错误,并且严格按照焊接工艺操作规程使用对应焊材。
3) 管道焊接前将坡口表面和边缘内外侧100 mm范围内的油污、铁锈、毛刺等清除干净。
4) 为保证焊接质量,施工现场应采取防风措施,并按照工艺规程施焊。
5) 焊接过程中,作业环境相对湿度不得大于90%。
6) 模块预制时需注意焊接热量集中部位的变形,可采用反变形法降低主管的变形量。
7.3. 质量关键控制点明细见(表5)
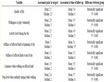
Table 5. List of key quality control points
表5. 主要质量关键控制点明细表
8. 安全措施
8.1. 安全标准
1) 《重大危险源辨识》 GB18218-2000
2) 《石油天然气工业健康、安全与环境管理体系》 SY/T6276-2014
3) 《职业健康安全管理体系规范》 GB/T28001-2011
4) 《施工现场临时用电安全技术规范》 JGJ46-2005
5) 《石油工业动火作业安全规程》 SY/T5858-2004
8.2. 安全保证措施
8.2.1. 动火作业
1) 施工作业前各方共同召开技术施工协调会,共同制定安全防范措施。
2) 施工前对施工人员进行交底,确保施工人员在发生危险时有序撤离。
3) 施工现场要搞好场地平整和易燃易爆品的清理,并确保有足够的施工作业面和道路畅通。
4) 施工作业点要配置足够的灭火器,各类器材的摆放位置符合要求。
5) 严格服从运行人员的管理,进场前严格检测高压井口施工区可燃气体浓度及空气含氧量,并随时监测。
6) 高压井口处使用两个可燃气体检测仪进行监控,如可燃气体检测仪发出报警,立即停止一切作业,撤出施工人员,确定泄漏点,进行处理,待可燃气体含量符合要求后,才可继续施工。
8.2.2. 吊装作业
1) 模块吊装应使用专用吊具,吊装作业要由持有特种作业证的起重工指挥。
2) 吊装时,应用牵引绳控制物资的摆动,防止碰撞伤害。
9. 环保措施
9.1. 环保标准
1) 《建设工程施工现场环境与卫生标准》 JGJ146-2013
2) 《建筑施工场界环境噪声排放标准》 GB12523-2011
3) 《污水综合排放标准》 GB8978-1996
9.2. 环保措施
9.2.1. 土壤污染
1) 工程施工过程中加强对施工工程废料、设备、生产生活垃圾的控制和治理,遵守有关防火及废弃物处理的规章制度。
2) 设置垃圾桶回收废弃物,将施工中用的抹布、手套等废弃物回收,统一处理。
3) 现场施工做到标牌清楚、齐全、各种标识醒目、施工场地整洁文明。
9.2.2. 水体污染
试压废水排放前进行检测,达标后在指定区域排放。
10. 效益分析
10.1. 经济效益
以KS501单井为例,传统施工方法多采用单井井场现场顺序组对安装,受单井采气树安装工期、工艺管线及设备土建基础成型制约,施工周期长、占用成本高。管道二公司创新将井场工艺管线分成三个预制模块,每个模块具有独立的结构,单独安装成橇,独立预制,模块化焊接预制率达到95%以上,与传统工艺管线施工比较,模块化工艺管线施工工期由原40天缩短至15天。经济费用对比分析见(表6)所示。
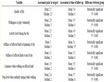
Table 6. Comparison of economic costs between traditional wellsite process pipeline construction and modular construction
表6. 传统井场工艺管线施工与模块化施工的经济费用对比
单井井场工艺管线模块化施工与传统工艺管线施工比较,可相应节省施工费用:54 − 20.93 = 33.07万元。
2016年~2018年,本工法先后在克拉苏气田克深5区块试采地面工程、伊拉克鲁迈拉油田地面项目、长庆油田第二采气厂2018年产能建设地面工程等工程中推广应用,累计节省成本828.10万元。
10.2. 社会效益
本工法在油气田井场地面建设施工中进行了大量推广应用,模块划分和模块化预制等关键技术持续得到升级和优化。采用模块化施工的工艺管线,可在因特殊原因停井时直接拆卸用于其他井口工艺管线安装,实现重复利用,节支降耗效果良好。
11. 应用实例
11.1. 克拉苏气田克深5区块试采地面工程 [2]
克拉苏气田克深5区块试采地面工程中单井井场工艺主管线为DN100双相钢材质,所有管阀件总长约20 m,DN100焊口28道、DN50焊口12道(不含放空管线),仪表根部原件焊接8处。2016年~2018年管道二公司在克拉苏气田克深5区块试采地面工程中采用本工法先后完成了4座双相不锈钢16 MPa高压气井的工艺管线安装,模块化焊接预制率达到95%以上,最大限度降低了现场施工的工作量,与传统工艺管线施工相比,单井模块化工艺管线施工工期由原40天缩短至15天,工效提高60%。不仅解决了单井施工工期要求高、交叉作业多的问题,而且在特殊原因停井时可直接拆卸工艺管线和设备安装至其他井场,实现重复利用,安全经济效益显著。目前,业主已在整个油田全面推广应用撬装化、模块化安装技术。
11.2. 长庆油田第二采气厂2018年产能建设地面工程 [3]
长庆油田第二采气厂2018年产能建设地面工程包括集输线路157.83 km (管径φ60~φ323),集气站2座,井场35座,及配套道路、通信工程。管道二公司采用本工法将井场单井工艺管线模块化预制,单井工艺预制焊接从井口连接处至汇管连接处,现场施工部分仅进行地下汇管部分焊接及安装。模块化焊接预制率达到95%以上,最大限度降低了现场施工的工作量,与传统工艺管线施工相比,模块化工艺管线施工工期(井场按4口井计)由原10天缩短至4天,工效提高60%。
11.3. 伊拉克鲁迈拉油田地面管线项目
伊拉克鲁迈拉油田地面管线项目φ168-φ219井口管线安装165.76 km,φ406站间管道安装4.5 km,φ762注水管道安装14.15 km,井口工艺安装87座,脱气站工艺安装22座,脱气站注水分输撬安装3座,脱气站连头3处,脱气站撬装设备维修7座,等级公路顶管穿越685 m/45处,工艺管件预制78套,混凝土管墩安装16,433个,旧管线冲洗试压122条,260米跨接井口管线安装,井口管线保温管墩调整1345个,完成管线保温累计218.25千米;不锈钢扎带绑扎218.25千米,CPS6水站升级改造。管道二公司采用本工法将井场工艺管线分模块预制,预制率达到95%以上,最大限度降低了现场施工的工作量,与传统工艺管线施工相比,单井模块化工艺管线施工工期由原20天缩短至7天,工效提高65%。