1. 引言
这种复合管材的特殊性给通球、测径、试压时收发球筒和封头的焊接带来了很大的问题。传统意义上封头一般材质绝大部分都为碳钢材质,母材也为碳钢材质,焊接都为同种钢焊接。但到目前位置,公司还未进行过复合管与碳钢管相连接的焊接技术,给施工带来了很大挑战。为此,通过不断的研究和试验,在常规碳钢管的基础上进行了革新,通过堆焊和增加过渡复合管的形式实现了复合管高压试压。通过革新,这项技术成功应用于克深5地面试采工程中,完成约18 Km管线试压,4口单井试压,为复合管施工积累了宝贵经验。
2. 方案制定 [1]
目前双金属复合管在塔里木油气田地面开发建设应用较为广泛,常见的双金属复合管根据生产工艺大致分为两种,即冶金双金属复合管和机械双金属复合管。
冶金双金属复合管(见图1)是把初级工业材料和高技术的冶金处理过程结合起来,采用离心浇铸管坯经挤压、冷轧(或冷拔)生产方式,从而获得高品质的复合管材。这种新型复合管材可以是一般普碳钢与不锈钢、一般不锈钢与高品质不锈钢,也可以是普通钢种与镍、铬、钼合金的复合;还可以根据用户要求实现多种金属的多层复合。这种管材的优势在于可以根据施工需要任意切割,焊接时也可以与纯碳钢管材正常对口焊接,操作方便,但价格昂贵,生产周期长,且多数为进口材料。
机械双金属复合管(见图2)是将碳钢管和不锈钢钢管分别生产完成后,将不锈钢管嵌入碳钢中,将装配好的内外管完全密封呈密闭长筒,再将液体注入筒内,逐步加压筒内的液体,使得内衬不锈钢管逐步的在直径方向向外扩张,在轴向方向向内收缩。通过连续逐步施压,使得内衬管最终达到塑性变形,外基管仍处于弹性变形范围内,当通过压力表判定内外管已达到塑性变形,外基管处于弹性变形要求时,施放压力,复合形式。
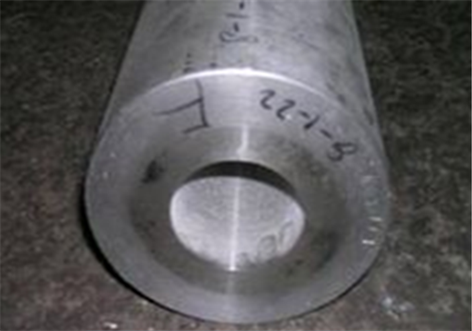
Figure 1. Metallurgical bimetal composite pipe
图1. 冶金双金属复合管
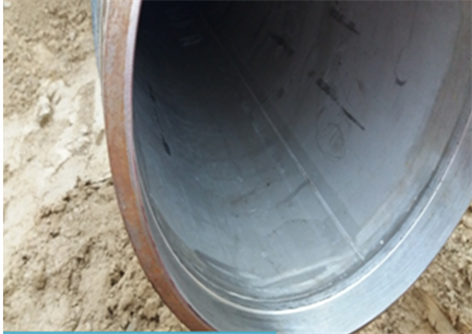
Figure 2. Mechanical bimetal composite pipe
图2. 机械双金属复合管
机械双金属复合管以碳钢管为基体材料,承受管道系统的工作压力,以耐腐蚀合金材料为内衬防腐层,充分发挥耐腐蚀合金优异的耐蚀性能。这种管材的优点在于价格低廉,制作工艺简单可靠。缺点在于,由于是机械复合,两层金属间属非扩散结合,在堆焊段以外进行切割时,复合管会产生分层倾向(见图3),以释放制造工艺带来的应力。为保证施工质量和管道运行安全,施工中通常按照复合管管径采用堆焊(见图4)或封焊(见图5)的方式对切割管段进行处理 [2]。
机械双金属复合管(以下简称复合管)由于其承压高、耐腐蚀、价格低廉的优点,而被西气东输主力气源地——克拉苏气田的开发并广泛采用至今。
四川油建作为塔里木油田最早接触复合管施工的单位,也是经过不断的摸索才形成自己的一套施工方法。线路焊接时需要的短节通过封焊的方式进行处理,而在管道试压时则利用冶金复合管作为过渡管进行焊接,如图6所示:
这种施工方法焊接简单,试压完成后可直接切割冶金复合管,然后用机械复合管直接对接焊就可以完成,但是对冶金复合管的浪费较大,费用昂贵。
为了既保证复合管正常试压,又避免浪费,降低施工成本,经过研究讨论制定了以下几种方案:
1、增加法兰连接法;
2、增加过渡复合管法;
3、管段堆焊法。
3. 实施情况
3.1. 增加法兰连接法
这种施工方法就是利用法兰将复合管与碳钢管连接在一起,试压封头或者收发球筒再与碳钢管对接焊,具体如图7所示:
经过现场试验,这种施工方法存在以下优缺点:
1) 连接方便,焊接工艺简单。
2) 由于要承受≥24 MPa的高压,所以堆焊法兰和碳钢法兰外形尺寸偏大,单片重量达到约200 Kg,对口焊接时必须挖掘机配合,运输装卸极为不便。
3) 如上图矩形虚线框内所示部分,完成后在进行封头单独试压时还需增加一块法兰盲板,这样造成试压封头部分重量加大,操作极为不便。
4) 不锈钢法兰在完成一次焊接后需要切割下来重复使用,这样造成带颈法兰的颈部会被切除一部分,连续使用后造成法兰颈部与对接焊主管存在外形尺寸大的偏差,最终无法使用,需重新加工制作,浪费较大,成本增加。
3.2. 增加过渡复合管法 [3]
经过现场反复研究和总结与对比,综合了冶金复合管过渡法和法兰连接法的优缺点,克深5试采工程大胆使用了此方法,具体做法如图8所示:
双金属复合管试压封头的制作难点在于,如何保证复合管管端的原始封焊或堆焊段在试压完成切割后还能继续使用。首先,在施工过程中如果碳钢管与双金属复合管直接对接焊,会造成碳钢管内铁素体由于受高温影响向焊道方向移动,造成焊道位置铁素体超标,焊道铁素体会继续沿着焊道周向扩散一直延伸至原复合管管端堆焊位置上,这种加速渗透造成晶体结构会由奥氏体转变成马氏体结构,导致焊道强度减弱,在后期运行中发生穿孔刺漏情况。
另外,复合管出厂时管端自带的堆焊段是由管材厂家通过特制的旋转操作台加工而成,为保证试压后连头施工,需尽可能保证其完整性,为此我们在试压封头一侧加入了一根过渡复合管,这样既保证了复合管管道不至于完全破坏,又保证了切割后管端堆焊还可以继续正常使用。具体现场做法如下:
1、过渡复合管一侧保留原始堆焊段,另外一侧现场做管端封焊处理(见图9),这样就解决了切割后复合管出现缝隙的问题,封焊端可以直接与碳钢封头对接焊,焊材选用625合金钢(见图10)。
2、碳钢试压封头与过渡管焊接完成经试压后切除就可在管线上使用。
这种施工方法已经在克深5现场成功应用,并完成了7段,约18 Km管线,4口单井试压,无一处因为该技术方案发生泄露事故。
过渡复合管法的缺点在于:由于过渡管管端堆焊宽度按照设计要求一般在20 mm左右,如果试压封头第一次试压完成后需要从与已焊接完成的管线上切割下来,每切割一次,堆焊宽度就会减少,所以造成试压封头重复利用率低。
3.3. 管段堆焊法
为了最大化发挥过渡复合管的优势,经过反复的研究重新对过渡复合管管端堆焊宽度进行现场堆焊(见图12),通过增加堆焊宽度以此来发挥过渡复合管的优势。按照设计技术规格书要求堆焊管端的宽度为20 mm,为满足现场施工需要,将管端的堆焊长度增加至60 mm,这样就可以重复切割至少4次以上,最大限度的利用了堆焊技术。具体做法如图11所示:
4. 创新点
1、突破了传统的冶金复合管试压封头焊接技术,可以重复使用,降低了施工成本。
2、通过研究优化了双金属复合管试压封头焊接技术,更便于现场操作,灵活性更强。
3、创造了复合管试压封头焊接技术的先例,为后续复合管施工提供了技术支持。
5. 效果
5.1. 经济效益
费用明细如表1所示。
小计节约费用:35,827元(仅以克深5试采地面工程为参考)。
5.2. 安全效益
通过对复合管封头焊接技术的优化革新,大大降低了复合管焊道因碳化而造成对焊层穿孔腐蚀的情况,保证了全线管道的运行安全。
双金属复合管封头焊接技术的研究和革新弥补了公司复合管封头焊接技术上的空白,同时在克深5试采地面工程上的成功应用证实了革新成果的可行性,更为重要的是打破了传统意义上冶金复合管试压封头的焊接技术,充分发挥了复合管堆焊技术,更大的提高了现场的可操控性,随时可以现场堆焊,避免受管材限制而影响工期,最大程度的节省了施工时间,同时降低了材料成本,具有较强的推广应用效果。