摘要: 本文通过对物资的交货关键性和技术复杂性进行分析,在此基础上引入了一种基于风险矩阵确定督办等级评估方法。通过风险矩阵评估提高了督办等级确定的针对性和准确性,为项目的物资督办管理提供了一种结构化的评估工具,具有很好的指导意义。
Abstract:
Based on the analysis of schedule criticality and technical complexity, this paper introduces a risk matrix based evaluation method to determine the expediting level. Through the risk matrix assessment, the pertinence and accuracy of the determination of the material expediting level are improved, and a structured assessment tool is provided for the expediting management of the project, which has a good guiding significance.
1. 引言
督办即买方对卖方通过电话、邮件、会议、驻厂等不同的方式对生产过程进行监督,确保卖方按照买方的采购订单,及时完成设计文件、质量检验计划、运输计划、质量文件等的提交以及采购物资的交付,从而满足项目进度和施工对物料到场日期的需求。督办作为采购流程中的一个重要环节,对项目的成败有着举足轻重的作用。通过督办及时发现供应商供货中的各种问题,并及时采取措施加以补救,以免影响采购进度,从而影响到现场的施工组织计划。
国内关于物资督办管理的研究,主要具体集中在督办制度制定和督办业务流程的管控上,关于物资督办等级的确定主要以定性为主,运用风险分析方法的研究相对较少。本论文借鉴项目风险评估领域的成功经验,将基于风险矩阵方法理论方法体系,应用到物资督办等级的评估中,实现对物资督办等级的科学分析、合理评价,提高了物资督办的针对性和准确性,优化了督办资源配置,为督办等级确定提供一种结构性的风险评估工具。
2. 方法简介
风险一词的出现由来已久,对风险的评估和管理也可追溯至希腊、罗马时代之前,然而正式的风险分析在近代才开始出现 [1]。风险矩阵是在项目管理过程中识别风险重要性的一种结构性方法,并且还是对项目风险潜在影响进行评估的一套方法论 [2]。1995年4月美国空军电子系统中心(ESC)首次提出了风险矩阵方法,随后ESC的大量项目中所做的项目风险评估都应用了此方法 [3]。美国米托公司对美国空军电子系统中心的风险矩阵方法过程进行了改进和扩展,创建了基线风险评估过程 [4]。
近年来,风险矩阵法在工程项目领域的应用越来越多,其操作简单、结果易懂。不少国家或地区的标准和规范中采用了风险矩阵(或其变形)评估方法,我国在桥梁、地铁、隧道、管道等行业的规范和指南中,也将其作为基本的风险评估方法 [5] [6] [7]。风险矩阵法的关键在于其从项目的需求和技术可能性两方面进行项目风险识别和风险概率计算,并构建风险矩阵 [8] [9] [10]。
本文在有关风险矩阵方法研究成果的基础上,研究如何将原始风险矩阵加以改造后引入物资督办等级的评估,构建了用于物资督办等级评估的风险矩阵,设计了利用矩阵进行督办等级评估的基本流程。
2.1. 确定交货关键性等级
首先要根据施工需求确定不同物资的计划到货时间,然后根据物资的预计到货时间与施工需求时间进行对比,将交货关键性分为3个等级,详见表1。
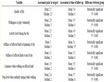
Table 1. Level of schedule criticality
表1. 交货关键性等级
2.2. 确定制造复杂性等级
根据物资的设计和制造难度,将制造复杂性等级分为3级,详见表2。
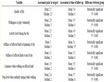
Table 2. Level of technical complexity
表2. 技术复杂性等级
2.3. 构建风险矩阵
在完成交货关键性和造复杂性等级的划分之后,构建一个二维风险矩阵,风险矩阵图见图1。
2.4. 确定督办等级
应用风险矩阵,对于不同等级的风险采用不同的督办等级,督办等级划分见表3。
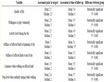
Table 3. Level of material expediting
表3. 物资督办等级划分
3. 应用举例
下面以某油气项目为例,来说明风险矩阵在督办等级确定中的应用。该项目共有采办包69个,首先根据材料交货状态表中不同物资的预计到货时间与现场需求时间进行比较,根据比较结果对采办包的交货关键性进行分类。然后督办人员通过与专业工程师进行沟通后,确定不同采办包的制造复杂性等级,最后依据风险矩阵确定出不同采办包的督办等级。由于采办包较多,本文仅列出部分采办包的督办等级作为示意,见表4。
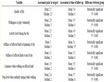
Table 4. Level of material expediting
表4. 物资督办等级划分
4. 结束语
本文引入了风险矩阵方法进行督办等级的确定,并结合实际项目进行了应用举例。结果表明,风险矩阵方法具有简单易操作的特点,为制定合理的督办等级提供重要参考,使得督办等级的确定更具有针对性、实效性和准确性。
NOTES
*通信作者。