1. 引言
目前我国约80%的电力由火力发电厂提供,但煤炭储量有限,燃烧后释放大量CO2等有害气体,对环境不友好;风电、水电等又受自然条件限制,电力不稳定;核能对比火电、风电和水电则具有较环境友好、可持续、能满足人类对能源长期需求的特点。在核电站的发展过程中,安全问题一直是大众关注的重点,流动加速腐蚀(flow accelerated corrosion, FAC)是核电站二回路管道中常见的腐蚀现象,影响着核电站的安全运行。FAC会造成管壁减薄,当管壁厚度减至某一临界值时,若未能及时探测到减薄的管道并进行维修或替换时,在后续运行过程中一旦工作压力超过这一临界值,管道就会因为过载而失效。对于电站中的大直径管道,其疏运流体流量较大,常以剧烈的爆裂形式失效,破坏性极强 [1]。喷涌而出的高温水或是水汽混合物会影响电站的正常运行,造成经济损失,还可能造成人员伤亡 [2],因此缓解并防止FAC的发生是一种提高核电站经济效益和运行安全的有效手段。研究影响FAC的形成因素 [3] [4] [5],制定有效的预防方案具有重要的意义。本项目着重研究在碳钢基体上沉积Fe3O4涂层,目前Fe3O4涂层的多种制备方法众多,如溶胶凝胶法 [6]、共沉淀法 [7]、脉冲激光沉积 [8]、分子束外延法 [9]、电沉积法 [10] [11] 等,其中电沉积法具有操作简单、成本低等优势,且影响涂层生长和性能的关键参数易于控制,这对涂层性能优化有着重要意义。本研究还通过模拟服役工况环境下的耐腐蚀性能测试,研究了涂层性能并优化了制备工艺与参数,为预防FAC提供理论基础。
2. 实验
2.1. 样品制备
准备尺寸合适的阳极石墨和阴极碳钢片(样品),取适量TEA、蒸馏水、NaOH、Fe2(SO4)3配置电镀液,并持续搅拌至完成配置,再将已配置好的镀液放置于恒温水浴锅中加热到80℃,保温30 min。此后将石墨和碳钢片放入镀液,开通直流电源,使用不同的电流密度进行电镀。电镀完成后,样品洗净吹干。图1为电镀装置示意图。
2.2. 实验条件
为探究电流密度对涂层性能的影响,使用不同的电流密度制备涂层样品,工艺参数及实验材料见表1,表2。
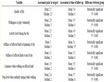
Table 1. Coating preparation conditions
表1. 涂层制备条件
实验所用阳极为高纯石墨片(纯度>99.9%),阴极为二回路管道所用碳钢。
2.3. 测试设备
本研究过程中使用了场发射扫描电子显微镜观察涂层形貌,电子探针测试分析涂层的元素,拉拔测试仪测定涂层结合力,电化学工作站测定涂层的电化学阻抗谱和动电位极化曲线,详细仪器信息见表3。测试使用三电极体系,工作电极是制备的涂层,对电极为金属铂网,参比电极是饱和甘汞电极(SCE)。使用质量分数为3.5%的NaCl溶液作为腐蚀液,实验在室温中进行。模拟工况下的水腐蚀实验采用的反应釜是三电极腐蚀试验磁力驱动反应釜,试样尺寸及摆放位置图见图2,内圈4个样品,外圈8个样品。
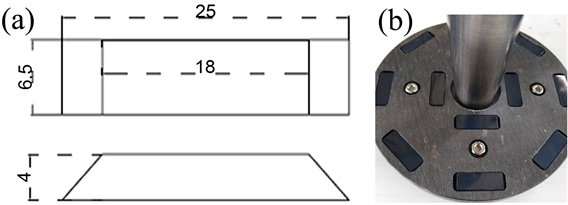
Figure 2. Water corrosion test sample size (a); sample placement diagram (b)
图2. 水腐蚀实验样品尺寸(a);试样摆放位置图(b)
3. 结果与讨论
3.1. 微观形貌
不同电流密度下制备的涂层的微观形貌如图3。当电流密度小于1.5 mA/cm2时,涂层表面出现了明显零星的无规则团簇。在电流密度为1 mA/cm2时,其中较大的团簇直径超过了5 μm,随着电流密度增加,这些团簇逐渐变多变大;到3 mA/cm2时,团簇基本分布在整个涂层表面而引起了局部的聚集。再次放大后发现,随着电流密度增加,涂层表面晶粒的尺寸随之增大。当电流密度小于2 mA/cm2时,涂层表面较为平整,无明显的凸起,涂层更加致密,晶粒尺寸更均匀。当电流密度大于2.5 mA/cm2时,晶粒尺寸变得不均匀,表面不再致密平整,晶粒的形状呈现出不规则状的多面体。因为在大电流密度下,沉积系统中提供了更多能量,得Fe3+的沉积更容易,晶粒的生长有更大的动力。
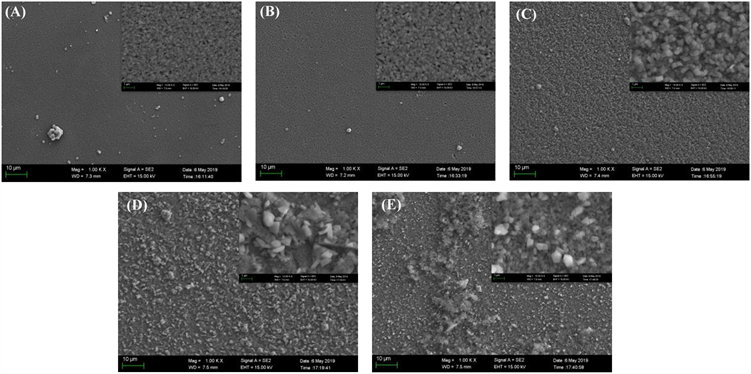
Figure 3. SEM pictures of coatings prepared under different current densities, A~E for 1、1.5、2、2.5、3 mA/cm2, The magnification is 1000×, the illustration is magnified 10000×
图3. 不同电流密度下制备的涂层的SEM图片。A~E分别是1、1.5、2、2.5、3mA/cm2,放大倍数1000×,插图放大10000×
为深入研究涂层表面的元素分布,分析了1.5 mA/cm2电流密度所制备涂层的元素含量,取点位置如图4。
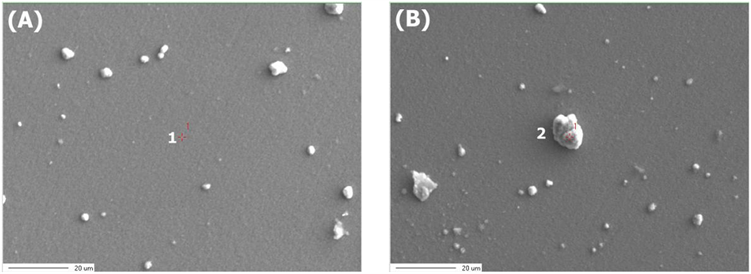
Figure 4. The position of the EPMA
图4. 电子探针元素分析的取点位置
其中包含了较平整的区域1和有团簇的区域2。由表4分析结果可知,在平整的区域主要含元素O和Fe。二者的原子比约为1.44,接近Fe3O4的原子比1.33,氧元素比例偏高可能是涂层制备后在空气中有了少量的氧化。在有团簇的区域,出现了大量的C,这可能是两方面的因素导致的。第一是阳极材料为石墨,石墨在电镀中会不可避免地发生溶解并进入镀液中,而后沉积到阴极表面。第二是镀液中的四价C在沉积过程中被还原后留在了涂层表面。此处,O和Fe的原子比已经超过3,因为Fe的氧化物中,氧铁原子比最大为1.5 (Fe2O3),所以在位置2有部分氧原子与碳原子形成了复杂的氧化物。
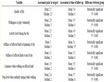
Table 4. The result of element atomic percentage analysis
表4. 元素原子百分数分析结果
3.2. 涂层物相分析
在制备Fe3O4时,γ-Fe2O3是易出现的副产物,因此有必要测试涂层的相结构。因γ-Fe2O3和Fe3O4晶体结构上的相似性,使用X射线衍射时,产生的峰强和峰位都很接近,故用X射线衍射并不能够将二者区分出来。Roman光谱则可以通过散射峰的位置的不同将二者区分开。理论上,Fe3O4在室温下五个拉曼活性震动模式:3T2g + Eg + A1g,在670 cm−1附近对应的A1g振动模式有最高的频率,这是Fe3O4拉曼光谱的特征峰 [12]。而γ-Fe2O3在660 cm−1附近有一个峰,位置与Fe3O4相近;另外,在1300、720、500、和360 cm−1附近也存在拉曼散射峰 [13] [14]。1、2、3 mA/cm2下制备的涂层的拉曼光谱如图5所示,除了在670 cm−1附近出现散射峰,还在300、540 cm−1附近出现了散射峰。这些峰位和γ-Fe2O3的相去甚远。因此可以确定涂层中没有γ-Fe2O3。
再对涂层进行了X射线光谱测试,测试结果如图5,其中PDF#19-0629标示出的峰位是标准卡片中Fe3O4的位置。由结果可知,本研究制备的涂层物相是Fe3O4。
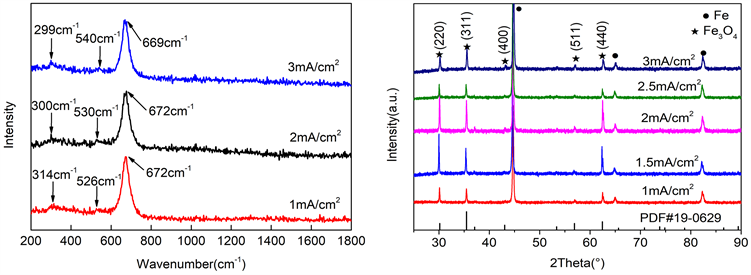
Figure 5. Raman spectra and XRD results of coatings prepared with different current densities
图5. 不同电流密度制备涂层的Raman光谱及XRD结果
3.3. 涂层的结合力与厚度
不同制备条件下涂层的结合强度,结果如图6所示,涂层样品的结合力分布在16~20 Mpa之间,并未随着电镀电流度的变化而变化。再观察图7涂层样品结合力测试后的表现,涂层表面完整未被破坏,因此涂层的实际结合力是高于测试结果的。
图8显示了不同电流密度下样品的增重和涂层的厚度。结果表明,电流密度小于2 mA/cm2时,随着电流密度增加,样品的增重越来越大。这是因为大的电流密度可以在相同时间内提供更多的能量,更多的Fe3+就能够获得电子,发生还原反应并沉积到基体上。电流密度大于2 mA/cm2时,增重并没有继续增加。
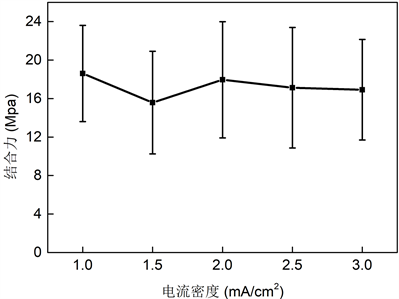
Figure 6. Cohesion of coatings deposited under different current densities
图6. 不同电流密度下沉积的涂层的结合力
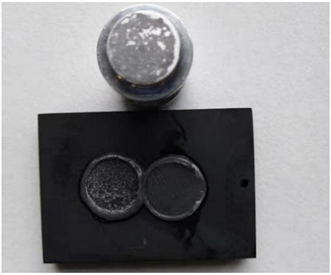
Figure 7. Macro morphology of coating after drawing test
图7. 拉拔测试后涂层宏观形貌
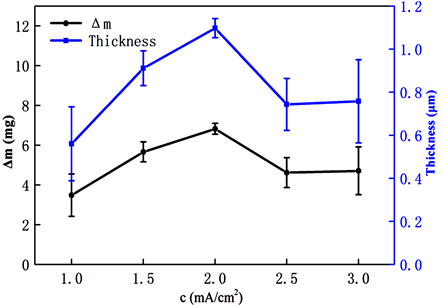
Figure 8. Weight gain and thickness of coatings prepared under different current densities
图8. 不同电流密度下制备涂层的增重与厚度
此处涂层的厚度是涂层样品的整体平均厚度,是通过样品的增重与表面积计算出来的数据,计算公式为:
(1)
其中T是涂层厚度,单位是μm,
是样品的增重,单位是g,
为Fe3O4密度,5.18 g/cm3,s为样品表面积,12 cm2。为了验证计算结果的准确性,对电流密度为1.5 mA/cm2下制备的涂层进行了截面观察,观察结果如图9所示。
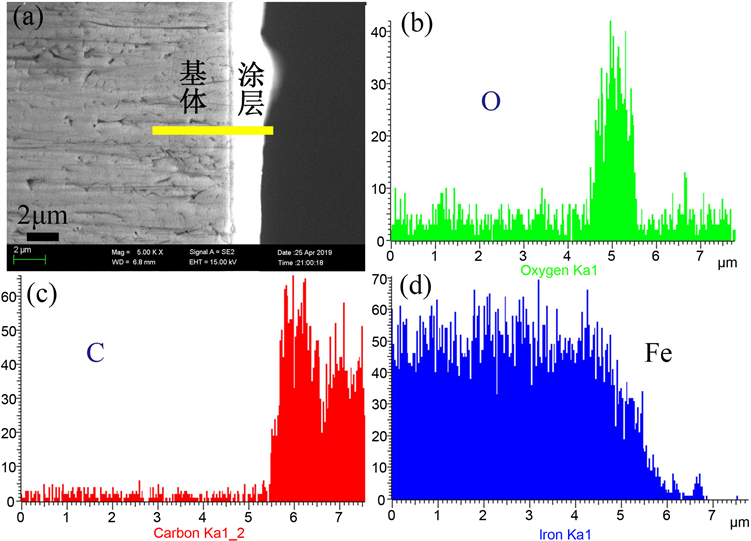
Figure 9. Cross-sectional view (a) and element line distribution (b)~(d) of the coating deposited at 1.5 mA/cm2
图9. 1.5 mA/cm2下沉积的涂层的截面图(a)和元素线分布(b)~(d)
从上的O元素的分布可知Fe3O4涂层的厚度约为0.9 μm,这与图8中电流密度为1.5 mA/cm2时制备的涂层厚度的数据十分吻合,因此本实验中使用公式(1)计算涂层厚度是合适的,同时也表明了本实验中制备的涂层厚度均匀性良好。
3.3. 电化学测试
不同电流密度制备的涂层样品经过电化学工作站测试后,对Nyquist曲线进行分析处理,可以得到电极/溶液界面电荷转移电阻Rt,对动电位极化曲线进行Tafel拟合,可以得到腐蚀电位Ecorr和腐蚀电流Jcorr;Rt越大,则Jcorr越小,表明材料耐蚀性越好。图10展示了涂层的Nyquist曲线,在测试的频率范围内,所有涂层都只有一个容抗弧,因此全部的电极过程都是受基体与镀液接触界面的活化控制的。随着电流密度的增加,容抗弧的直径逐渐变大,说明电子在溶液和基体之间传递受到的电荷转移电阻增大了,这是因为大电流密度下的涂层的厚度增加和表面结构变化导致的。又对所有涂层样品进行了动电位极化曲线的测试,测试结果如图11所示:所有涂层的极化行为类似。在阴极支的−0.75~−0.8 V (vs. SCE)的区间内,都出现了析氢过程。析氢完成后,较大的电位区间内,极化电流没有出现剧烈下降,因为此时电极表面已经出现乏H+区域,电极反应要继续进行,就要依靠远离电极表面的H+的迁移,即此时的电极反应受到浓差极化控制。电位继续增大,来到阳极极化支。所有涂层在阳极极化支的表现类似,在测试区间内没有出现电流增速的剧烈波动。即在阳极支内只有一个电化学过程。所有涂层的极化电流的对数值随电位增大而基本呈线性增加,符合Tafel线性拟合对曲线的要求。
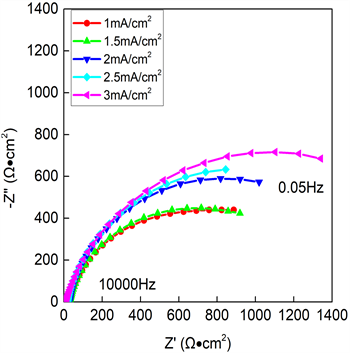
Figure 10. Nyquist curve of Fe3O4 coating
图10. Fe3O4涂层的Nyquist曲线
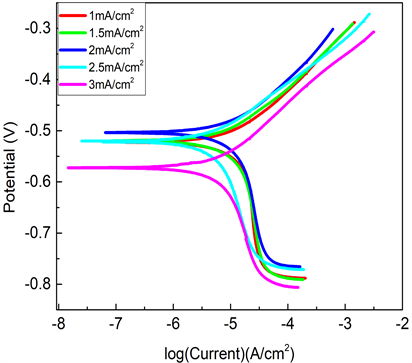
Figure 11. Potential polarization curve of Fe3O4 coating
图11. Fe3O4涂层的动电位极化曲线
选取极化曲线的阳极支进行Tafel拟合计算出了涂层的腐蚀电流密度Jcorr和腐蚀电位Ecorr。如表5,可知当电流密度为3 mA/cm2时,涂层有最小的Jcorr 4.01 μA/cm2,此时的涂层耐腐蚀性最好和Nyquist曲线情况相吻合。
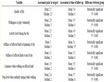
Table 5. Corrosion current density and corrosion potential of coatings under different deposition current densities
表5. 不同沉积电流密度下的涂层的腐蚀电流密度Jcorr和腐蚀电位Ecorr
3.4. 水腐蚀测试
因为本研究的目的是在一个流动的水环境下使用上述制备的涂层,所以还需模拟FAC的条件下来探究涂层的耐腐蚀性。根据以上的测试结果筛选合适的制备工艺参数,制备了用于水腐蚀实验的涂层样品,水腐蚀实验参数是依照核电站二回路管的服役条件设置的,水腐蚀实验条件与涂层制备条件见表6。
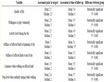
Table 6. Water corrosion test and preparation conditions
表6. 水腐蚀测试及制备条件
3.4.1. 失重结果与分析
腐蚀失重由腐蚀前的质量减去腐蚀后的质量得到。图12为试样的腐蚀失重,图13为不同位置的试样腐蚀前重量。由结果可知,三组带涂层的试样和不带涂层的试样的质量都有所降低,说明了在模拟工况的环境下有腐蚀发生。同样制备条件下的外圈B1组和内圈A组的涂层经过腐蚀后,环境中水流速度大涂层样品的失重越多,这和流动加速腐蚀的已有研究相吻合——流速越大,Fe3O4的溶解速率越大 [4]。而在相同的腐蚀环境下,外圈B2组比外圈B1组有更小的失重,说明涂层制备过程中不搅拌镀液得到的涂层有更好耐腐蚀性。而且通过与不带涂层的基体对比,能明显发现带有涂层的试样失重均比不带涂层的基体要小;充分说明了涂层能有效缓解模拟工况环境下的腐蚀程度。其中外圈B2组相比于无涂层基体,失重率降低了约64%。
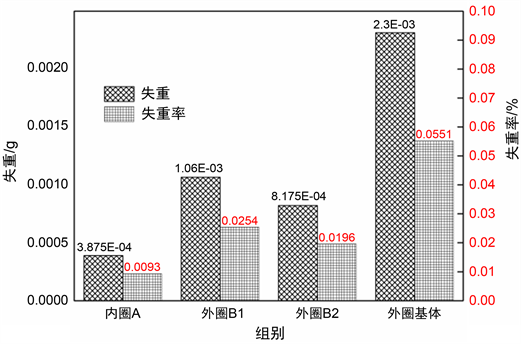
Figure 12. .Sample corrosion weight loss and weight loss rate
图12. 样品腐蚀失重与失重率
3.4.2. 腐蚀后微观形貌
图14展示了内圈A组的涂层样品腐蚀前后的微观形貌。图14(A)中涂层样品在腐蚀前表面除了少许颗粒外整体平整,晶粒较为致密。在图14(B)中可以看到,涂层中央部分表面完整腐蚀程度小,而边缘区域涂层腐蚀程度变大。图14(b1)~(b5)是中央到边缘的局部放大形貌图。在图14(b1)中,涂层形貌和腐蚀前图14(a1)基本一样,表面晶粒仍然呈现出柱状。在图14(b2)中,出现了一些小颗粒,这些小颗粒覆盖在柱状的晶粒上;图14(b3)中出现了尺寸在约500 nm的更大的球形颗粒,这些颗粒疏松的堆积在一起;图14(b4)中柱状晶粒的开始溶解,柱状晶粒的交界处出现了与图14(b2)中相似的小颗粒;图14(b5)是最靠近边缘位置,柱状晶粒已经完全消失。
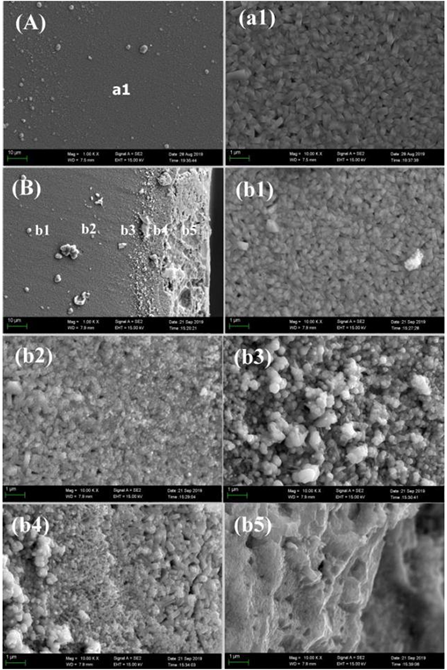
Figure 14. The morphology of the coating of the inner ring group A before corrosion A and after corrosion, the multiple is 1000×, (a1) and (b1)~(b5) are the magnifications of the corresponding parts in A and B, the magnification is 10000×
图14. 内圈A组的涂层腐蚀前A和腐蚀后B形貌,倍数1000×。(a1)及(b1)~(b5)为A和B中相应部分放大,倍数10000×
图15是外圈B2组的涂层腐蚀前后的微观形貌。如图15(B)所示,在涂层边缘部分,有大小不一的凹坑出现,越靠近边缘,凹坑尺寸越大,最大的约5 μm。图15(b1)为靠近涂层中部位置,腐蚀程度小,晶粒形态保持着棱柱状,和图15(a1)腐蚀前的形态相似;在图15(b2)中出现了明显的团簇和凹坑;在图15(b3)能观察到更大的凹坑。从腐蚀前后的微观形貌结果分析,经过水腐蚀实验后涂层样品表面除了出现凹坑和团簇外,表面晶粒形态未发生变化。再与内圈A组涂层样品腐蚀前后的微观结果对比研究,发现内圈A组涂层试样经过水腐蚀实验后,涂层表面的晶粒之间还出现更小的颗粒,而外圈B2组则没出现此种情况。
3.4.3. 腐蚀后涂层表面元素分析
根据上述分析结果,再针对A组涂层样品表面深入分析。通过电子探针对涂层样品表面进行元素分析,主要分析元素是C,O及Fe。扫描结果如图16,图16(A)是扫描区域,图16(B)、图16(C)及图16(D)分别是C,O、Fe的含量分布情况,含量从低到高表现为从蓝色到红色。
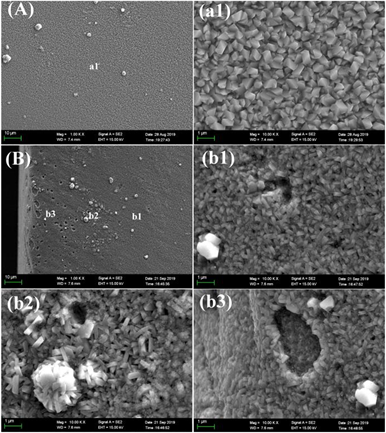
Figure 15. Outer ring B2 group coating before corrosion A and after corrosion B morphology, multiples of 1000× (a1) and (b1)~(b3) are the magnifications of the corresponding parts in A and B, with a multiple of 10000×
图15. 外圈B2组涂层腐蚀前A和腐蚀后B形貌,倍数1000×。(a1)及(b1)~(b3)为A和B中相应部分放大,倍数10000×

Figure 16. Scanning results of electron probe elements
图16. 电子探针元素扫面结果
分析图16展示的三种元素分布及含量结果,C元素整体分布较少,极大区域内的含量都在1%以下,这跟涂层制备后进行的元素分析结果能吻合,此处的C是来源于石墨电极和电镀液;Fe元素和O元素在整体分布上接近,两者的含量分别为44%与16%,Fe与O的含量比为2.75接近Fe3O4 (2.625),说明涂层在经过水腐蚀后,主体没有被破坏,任然保持着原有的成分;同时还有小部分区域的Fe元素含量最高达到了82%,观察(A)中对应的形貌可知这些Fe元素富集的区域是涂层表面突出的部位且形貌与涂层微观形貌不同,所以这些部位只是Fe元素聚集产生的形貌不是涂层被腐蚀破坏的。经过对A组涂层的元素分析,可以说明A组涂层经过水腐蚀后涂层表面保持完整,保护了基体不受腐蚀。
4. 结论
本项目通过不同电流密度制备得到了Fe3O4涂层,并对制备的涂层进行了微观形貌观察,涂层结合力测试和电化学测试,得到了以下结论:
1) Fe3O4涂层能在1~3 mA/cm2的电流密度范围内沉积得到;
2) 当电流密度小于2 mA/cm2时,晶粒尺寸分布较为均匀,当电流密度增大后,涂层表面出现了团簇;
3) 涂层厚度在电流密度为2 mA/cm2时达到最大;涂层的结合力均大于20 Mpa;
4) 使用1.5 mA/cm2电流密度,80℃的镀液,电镀5 min得到的涂层经过60天水腐蚀实验后,比不带涂层的基体失重率降低64%,有效的保护了基体不受腐蚀影响。
基金项目
本研究由项目“核电蒸汽发生器热交换管和二回路管道的服役行为评价技术研发”支持。
NOTES
*通讯作者。