1. 引言
对航天装备进行维修保障是航天装备保障工作的重要组成部分。航天装备的维修性是指装备在规定的条件下和规定的时间内,按规定的维修程序和方法进行维修时,保持或恢复其规定状态的能力。对装备的维修性进行评估,了解装备的维修性水平,确定其满足装备研制总要求的程度,是装备定型过程中的重要工作项目。
近年来,随着航天装备的发展,用户对装备维修性的要求相比以往越来越高也越来越具体,比如航天装备研制总要求中维修性战术技术指标往往规定具体的平均修复时间和最大修复时间。同时,国内航天装备研制单位也开始逐渐认识到维修性的重要性,开始注重维修性分析、试验与评估技术的研究,并在型号研制过程中推动维修性工作的开展,取得了显著的成果 [1]。然而,由于缺乏实际维修数据的积累,导致在航天装备定型过程中的维修性评估工作主要依靠定性分析,很难给出准确定量数据,难以满足装备定型要求 [2],仅有的少量定量数据,也由工业部门工艺操作人员进行的维修试验操作验证,无法从使用部队操作水平的基础上进行准确评估,造成装备后用户维修人力费用难以准确估算。
为了避免上述问题,本文结合航天装备发展的工程实际,设计了维修性试验,开展了基于维修性试验数据的平均修复时间与最大修复时间定量验证与评估,并结合某型号装备工程实际应用加以说明,为后续航天装备维修性评估工作提供参考。
2. 航天装备维修性要求
2.1. 定性要求
航天装备的维修性定性要求是为了使得产品修复、快速、简便和经济,而对产品设计、工艺及其他方面提出的要求,一般包括可达性、互换性于标准化、方差错及识别标志、维修安全、检测诊断、维修人素工程、零部件可修复性、减少维修内容、降低维修人员要求等方面 [3]。在实际工程应用中,一般航天装备定性要求通过维修性分析给出结论。
2.2. 定量要求
维修性定量要求是为了反映战备完好性、任务成功性、保障费用和维修人力等目标或约束,体现在维修保养、预防性维修、修复性维修和战场抢修等诸方面。目前,在装备维修性定量要求中,主要包括平均修复时间、最大修复时间等参数的要求。
2.2.1. 平均修复时间
平均修复时间MTTR是产品维修性的一种基本参数,也常记为
,是指在规定的条件下和规定的时间内,产品在规定的维修级别上,修复性维修总时间与在该级别上被修复产品的故障总数之比。从物理意义上讲,就是排除故障实际修理时间的平均值(不包括因供应和行政管理而导致的延误时间),排除故障的实际时间应当是各组成单元单项维修作业时间之和,包括故障检测、分解、更换、复原、调准和检验等时间。根据定义,平均修复时间MTTR可以表示为:
(1)
式中:
——第i个样本记录的修复时间;
n——子样数。
在实际工程中,一般认为修复时间呈对数正态分布,此时平均修复时间
评估模型 [4] [5] 如下:
(2)
式中:
——第i个样本记录的修复时间,min;
n——子样数;
——修复时间呈对数正态分布时的样本标准差;
(3)
平均修复时间评定结果按下列规则进行判断,如果平均修复时间
满足下式:
则产品平均修复时间符合要求而接受,否则拒绝。式中
为合同规定的平均维修时间,
为对应下侧概率的标准正态分布位数;β订购方风险。当β = 10%时
取1.28,当β = 5%时
取1.65。
2.2.2. 最大修复时间
最大修复时间是指产品达到规定维修度所需的修复时间;也即产品在规定的维修级别上,预期完成全部修复工作的某个规定百分数Z (通常为95%或90%)所需的时间 [6]。根据定义,最大修复时间
评估模型如下:
(4)
式中:
S——样本标准差;
(5)
当修复时间呈对数正态分布时,最大修复时间
评估模型 [5] 如下:
(6)
如果:
(7)
则产品最大修复时间符合要求而接受,否则拒绝。式中
为合同规定的最大修复时间。式中为合同规定的平均维修时间,
为对应下侧概率的标准正态分布位数;β订购方风险。当β = 10%时
取1.28,当β = 5%时
取1.65。
3. 装备维修性试验验证与评估
3.1. 总体思路
由于缺乏实际维修数据,无法应用第二章的维修性评估模型进行维修性定量评估。因此,在某型号定型阶段,笔者设计了专项维修性试验,用于积累维修数据进行评估工作,总体思路分三步:
首先,设计师系统首先根据装备的设计方案,梳理出了装备的LRU清单。并针对LRU维修性指标的估计结果,对LUR清单进行优化。
其次,根据梳理出的现场可更换单元LRU清单,在定型试验中,安排专项维修性试验,由用户选择操作的号手进行实际维修作业操做。
最后,在型号定型试验结束后,根据维修性专项试验结果,以维修试验数据代替实际维修工作数据,进行平均修复时间与最大修复时间的定量验证与评估。
3.2. 任务剖面分析
根据装备类型,明确装备的任务剖面,以便根据剖面中的使用维护条件,确定LRU清单。某装备的任务剖面如图1。
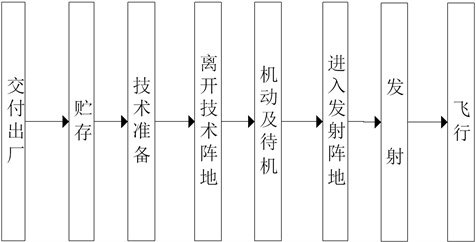
Figure 1. Mission profile of an equipment
图1. 某装备任务剖面
3.3. 明确现场可更换单元LRU清单
设计师系统根据装备的任务剖面,确定基层级可更换单元清单。装备在发射准备阶段与飞行阶段导弹武器系统不可维修,基层级维修级别的主要工作内容是在技术准备阶段和待机阶段进行自检、功能等测试,将故障隔离到最小可检测更换单元并进行更换。装备技术准备阶段可维修更换的分系统包括的各分系统在考虑了产品安装位置、现场维修条件、维修难度等差异,对现场可维修更换项目进行梳理,列出现场可维修更换项目清单,并针对LRU的故障率进行维修性指标初步估计结果,对LRU清单进行优化。
3.4. 进行维修性专项试验
为验证装备维修性指标的满足情况,设计师系统针对确定的LRU设计了维修性专项试验。维修性专项试验由用户选择普通的号手进行实际维修作业操做,结合部队真实三级阵地出库技术准备、待机阵地、发射阵地的相关测试工作,在测试工作进行过程中和结束后,进行模拟故障情况进行设备维修性专项试验,使用备件对上装设备单机或组件进行了更换,维修工作,并记录具体维修时间如表1所示。
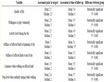
Table 1. Maintenance test operation record
表1. 维修性试验操作记录
3.5. 基于维修性试验数据的平均修复时间与最大修复时间定量评估
在维修性试验结束后,根据维修性专项试验结果,提出基于LRU的平均修复时间与最大修复时间定量验证与评估技术,采用正态分布理论模型对平均修复时间、最大修复时间进行评估的方案,并根据现场维修性专项试验结果,对上述指标进行评估。用户要求假设平均修复时间服从正态分布,其方差未知。评估方法按第二章计算。假设用户要求平均修复时间为25 min,则按照评估模型计算得:
(8)
因此平均修复时间符合要求而接受。最大修复时间评定结果按下列规则进行判断,如果:
(9)
则产品最大修复时间符合要求而接受,否则拒绝。式中
为合同规定的最大修复时间为2小时。
(10)
因此最大修复时间符合要求而接受。
4. 总结
本文结合装备发展的工程实际,总结了装备维修性要求,提出了基于维修性试验数据的平均修复时间与最大修复时间定量验证与评估方法,并结合装备工程实际应用加以说明,结果表明该方法可以成功应用于装备维修性评估工作,可为后续装备维修性评估工作提供参考。