1. 引言
完井是钻井工作最后一个重要环节,又是采油工程的开端,与以后采油、注水及整个油气田的开发紧密相连。而油井完井质量的好坏直接影响到油井的生产能力和经济寿命,甚至关系到整个油田能否得到合理的开发。完井液是新井从钻开产层到正式投产前,由于作业需要而使用的任何接触产层的液体。完井液按其组成可分为水基完井液、油基完井液、气基完井液。为降低完井液对储层的伤害,通过采用无固相完井液,可分为无机盐类无固相和有机盐类无固相钻井液两大类,无机盐主要有NaCl、CaCl2、KCl、NaBr、BaBr2等,有机盐主要为甲酸盐,如:NaCOOH、KCOOH、CsCOOH等。对于井眼不稳定、摩阻高的高难度井则采用油基完井液。
2. 深测钻井概况
A井是部署在阿克库勒凸起西南部的一口开发侧钻井,在原三开f177.8 mm套管上进行二次开窗侧钻,侧钻点井深6487.0 m,钻头尺寸为f149.2 mm,目的层位为奥陶系一间房组。该井钻至井深7100.0 m后接单根困难,上提下放摩阻高达40~50 t;钻进至井深7330.0 m后接单根上提下放摩阻高达50~58 t,钻至井深7552.0 m完钻。所用钻井液体系为聚磺混油钻井液体系,完钻时钻井液性能:密度1.20 g/cm³;粘度51 s;塑性粘度21 mPa×s;动切力7 Pa;静切力3/8 Pa;中压滤失量4.2 mL;泥饼0.5 mm;高温高压滤失量11.4 mL/130℃;pH10;含砂0.1%;固相含量8%;坂含35 kg/m³;含油量8%;CL− 21,800 mg/L;Ca2+ 380 mg/L。
测井作业前进行了两趟通井作业,进入裸眼段后摩阻随井深增加而不断增加,采用f149.2 mm牙轮钻头通井时,起钻最大摩阻高达70 t,下钻摩阻最大高达50 t。测井仪器下测至井深6564.0 m时仪器信号中断,检查发现四臂井径仪器线路故障导致仪器信号中断,分析认为6512.16~6570.06 m井段狗腿度高达16.49˚/30m~29.21˚/30m,井段允许的刚性长度远小于仪器串长度,仪器的蹩扭导致内部线路或电路板变形出现短路,同时致使连接扣变形。下支撑管柱前采用31/2模拟管柱进行通井,井段6487.0~7092.0 m下放最大摩阻32 t,上提最大摩阻54 t,通井至井深7214.0 m,下放最大摩阻40 t,上提最大38 t。组下裸眼支撑管柱(带封隔器)至裸眼井深6605.0 m时遇阻2 t,下放管柱加压0~40 t内活动6次无效,被迫起出支撑管柱。
鉴于本井实钻及后期通井摩阻情况,为有效降低后续支撑管柱下入摩阻以及保证裸眼段内桑塔木地层和恰尔巴克地层的井眼稳定性,选用具有强的防塌护壁能力、强的抑制性、优良的流变性和稳定性、良好的润滑性能、较好的储层保护能力的具有低粘高切流变特征的油基钻井液进行完井作业 [1] - [9]。
3. 油基钻井液性能优化
3.1. 拟用回收油基钻井液性能评价
为降低成本,重复利用已回收的油基钻井液,A井拟重复利用泥浆站储存的90 m3回收油基钻井液。室内对其流变性及乳化稳定性进行了测定,结果如表1所示。
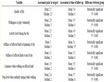
Table 1. Performance of recovered oil-based drilling fluid
表1. 回收油基钻井液性能
注:热滚条件130℃、16 h;在60℃下测试钻井液流变性能。
由表1可知,密度1.85g/cm3的油基钻井液经130℃高温热滚16h后,老化罐底部粘稠,表明该油基钻井液悬浮稳定性较差,老化前后的破乳电压值均低于油基钻井液通常要求的400V,且塑性粘度偏高;另外该回收油基钻井液的固相含量高达38%,含油32%,含水30%,油水比接近1:1。综合数据表明回收油基钻井液的存在粘切高、固相含量高、含水量高、破乳电压低、悬浮稳定性差等问题,需提高油基钻井液的破乳电压,改善其乳化稳定性,并调整其油水比、改善流变性,确保具有良好的悬浮稳定性。
3.2. 回收油基钻井液性能优化
根据A井井眼容积及地面循环需求,需配制280 m3密度为1.20 g/cm3的油基钻井液,基于新配制油基钻井液密度为0.95 g/cm3,则需新配制200 m3油基钻井液,并混入80 m3密度为1.85 g/cm3的回收油基钻井液,剩余10 m3密度为1.85 g/cm3的回收油基钻井液作为替浆时隔离液使用。
鉴于回收油基钻井液粘切高、破乳电压值低、水相含量高,选用具有多个亲油亲水基团的聚合物类乳化剂,使乳化剂分子能紧密地排列在乳化液滴上,牢固地吸附微小水珠,获得更大的界面强度,增强油基钻井液的乳化稳定性 [10] [11]。同时为提高油基钻井液封堵性能,新配油基钻井液所用配方为:90份0#柴油 + 10份氯化钙盐水 + 4.0%主乳化剂 + 2.0%辅乳化剂 + 2.0%有机土 + 3.0%油基降滤失剂 + 2.0%氧化钙 + 0.2%流型调节剂 + 2.0%刚性封堵剂 + 2.0%弹性封堵剂,新配制的油基钻井液及其与回收油基钻井液按2.5:1混合后配制油基钻井液的性能如表2所示。
由表2可知,新配制的低密度油基钻井液具有良好的流变性和乳化稳定性,并且将新配制的低密度油基钻井液与回收油基钻井液按2.5:1的比例混合后,无论高温老化前后,其流变性和乳化稳定性均显著改善和提高。室内测定混合后密度为1.20 g/cm³;的油基钻井液的固相含量数据表明,其固相含量为14%,油相含量为70%,水相含量为16%,油水比为81:29。
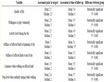
Table 2. Performance of newly prepared low-density oil-based drilling fluid and recovered oil-based drilling fluid
表2. 新配低密度油基钻井液与回收油基钻井液混合后性能
注:热滚条件130℃、16 h;在60℃下测试钻井液流变性能。
由表2可知,新配制的低密度油基钻井液具有良好的流变性和乳化稳定性,并且将新配制的低密度油基钻井液与回收油基钻井液按2.5:1的比例混合后,无论高温老化前后,其流变性和乳化稳定性均显著改善和提高。室内测定混合后密度为1.20 g/cm³;的油基钻井液的固相含量数据表明,其固相含量为14%,油相含量为70%,水相含量为16%,油水比为81:29。
4. 现场油基钻井液配制及性能监测
4.1. 低密度油基钻井液配制
基于室内回收油基钻井液评价及优化实验,结合现场实际循环罐情况,现场新配制了3批次低密度油基钻井液。油基钻井液配制时,为实现油水两相在较低黏度下充分乳化,先在柴油中加入主乳化剂、辅乳化剂,然后加入氯化钙盐水,最后加入有机土、氧化钙、油基降滤失剂、封堵剂等。剪切速率越高越有利于油基钻井液的配制,故现场用砂泵充分剪切。将现场配制的油基钻井液在搅拌速度12,000转每分钟下搅拌20分钟后,加热测流变性及破乳电压值,结果如表3所示。
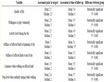
Table 3. Performance of a newly prepared low-density oil-based drilling fluid in Well A
表3. A井现场新配制低密度油基钻井液性能
注:在60℃下测试钻井液流变性能。
由表3可知,现场配制的低密度钻井液经高速搅拌后均具有良好的流变性和乳化稳定性,第3批次新配制低密度油基钻井液粘切偏高的原因为配制时受罐面条件限制,将剩余CaCl2溶液全部混入,导致其水相含量偏高。
4.2. 油基钻井液配制
现场将新配制的低密度油基钻井液与回收油基钻井液按2.5:1的比例混合,配制的油基钻井液性能如表4所示。
由表4可知,现场配制的油基钻井液密度为1.20~1.21 g/cm3,塑性粘度为25~28 mPa×s,动切力为7.7~8.5 Pa,破乳电压值为538~629 V,具有良好的流变性能和乳化稳定性。
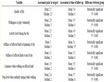
Table 4. Performance of oil-based drilling fluid prepared on site in Well A
表4. A井现场配制油基钻井液性能
注:在60℃下测试钻井液流变性能。
4.3. 替浆后油基钻井液性能监测
A井采用10 m3回收的高密度油基钻井液作为隔离液,顺利完成油基钻井液替浆作业后,油基钻井液循环期间对其性能进行了监测,结果如表5所示。
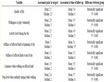
Table 5. Performance of oil-based drilling fluid in Well A
表5. A井现场油基钻井液性能
注:在60℃下测试钻井液流变性能。
由表5可知,循环期间油基钻井液密度、粘度平稳,高速搅拌后破乳电压值可达500~700 V之间,加热50℃后,塑性粘度21~24 mPa×s,动切力6~8 Pa,表明现场油基钻井液具有良好的乳化稳定性和流变性。
5. 油基钻井液施工效果
油基钻井液循环结束后,进行了短起下作业,期间加强了对摩阻数据监测,起钻期间摩阻数据如图1所示,下钻期间摩阻数据如图2所示。
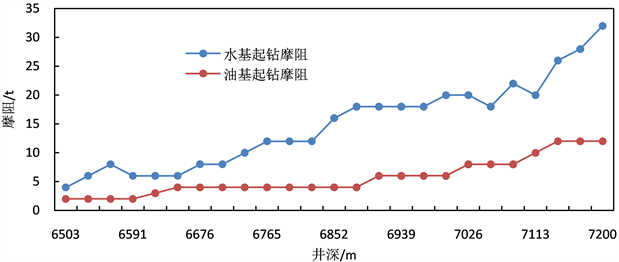
Figure 1. Comparison of friction between water-based and oil-based during tripping out
图1. A井起钻水基与油基摩阻对比
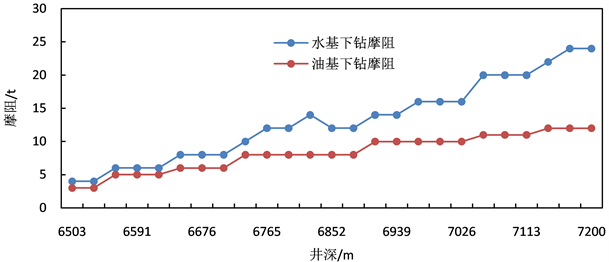
Figure 2. Comparison of friction between water-based and oil-based during tripping in
图2. A井下钻水基与油基摩阻对比
可见替换油基钻井液后上提摩阻为2~12 t,下放摩阻为3~12 t,而替换油基钻井液前,井内为聚磺混油钻井液时,起钻摩阻最高达32 t,下钻摩阻最高达24 t,表明采用油基钻井液后摩阻显著降低。
A井组下支撑管柱所用钻具组合:120.65 mm PDC (0.23 m) + 变扣(1.01 m) + 滚珠扶正器(0.4 m) + 变扣(1.82 m) + 31/2″打孔油管(7根 * 65.05 m) + 31/2″油管(66根 * 659.19 m) + 变扣(1.57 m) + 油钻变扣(0.42 m) + 88.9 mm钻杆3根 * 28.63 m (S135) + 88.9 mm短钻杆1根(1.1 m) + 88.9 mm钻杆(S135) * 147根 * 1422.79 m + 88.9 mm钻杆(G105) * 174根 * 1675.82 m + 311 * DS550变扣(0.75 m) + 127 mm钻杆 * 218根 * 2088.08 m + DS501 * 520 (0.92 m) + 139.7 mm钻杆 * 91根 * 876.05 m + 521 * DS550 (0.92 m) + 139.7 mm非标钻杆 * 36根 * 348.24 m,支撑管柱顺利下至预定井深7170.0 m,下管柱期间摩阻数据如图3所示。可见,随着井深的增加下放摩阻略有增加,下放摩阻最高仅为6 t,上提最大摩阻10 t,而前期采用混油水基钻井液时,下至井深6605.0 m后,下压高达40 t无效,被迫起出支撑管柱。
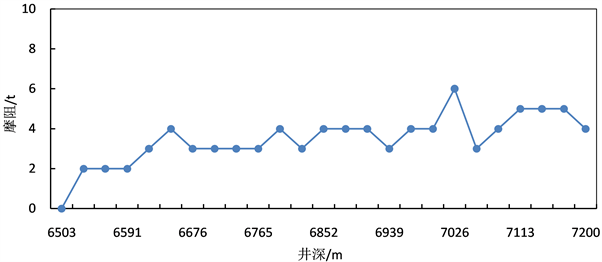
Figure 3. The friction curve of tripping in supporting string
图3. A井下支撑管柱摩阻曲线
6. 结论
1) A井采用聚磺混油钻井液钻井、中完期间摩阻大,主要原因为井眼轨迹不平滑,狗腿度大,局部地方井径大,钻井液性能不能满足施工需求。
2) 在合理利用回收油基钻井液的基础,优化、配制出了具有良好乳化稳定性、流变性的油基钻井液采用油基钻井液完井后,能够显著降低摩阻,确保了完井支撑管柱顺利下到预定井深。
3) 建议在油基钻井液替换、回收、运输、储存等环节,做好防护措施,尽力避免或降低对油基钻井液性能的影响。
致谢
感谢中国石化石油工程技术研究院钻井液研究所油基钻井液团队的大力支持。
基金项目
重大专项“耐高温高性能钻井液体系及井筒强化技术”(项目编号KTBE170004000201)。
参考文献