1. 引言
微通道板(Microchannel Plate, MCP)是由104~107个平行的微型通道电子倍增器组成的二维阵列,起着电子倍增、信号增强的作用。广泛应用于微光夜视、天文学、核辐射探测、医学成像等领域 [1] [2] [3] [4]。
微通道板打拿极电子倍增器的概念由Farnsworth [5] 于1930年提出,20世纪60年代该理论得以实施。微通道板打拿极由二次电子发射层和导电层组成。二次电子发射层起着电子倍增作用,入射电子通过与发射层碰撞形成二次电子;导电层影响器件电阻,当在MCP两端施加偏置电压时,电流会在导电层内传导,同时补充二次电子发射而损失的电子,使MCP稳定持续工作。由此可见,导电层对MCP的性能起着十分重要的作用。
传统MCP通过在通道内部插入可酸溶芯玻璃棒,再经过玻璃纤维拉制、切片、研磨、抛光、芯玻璃溶蚀和氢还原处理等工艺制成,又称作还原铅硅酸盐玻璃微通道板(Reduced Lead Silicate Glass-Microchannel Plate, RLSG-MCP)。该工艺依赖于玻璃的结构和成分来确定MCP的几何形状和增益性能 [6]。RLSG-MCP选取的材料和工艺技术有着局限性,玻璃成分在满足MCP要求的同时,还必须满足对玻璃粘度,熔融温度和热膨胀系数的要求,通常电阻非常高,对低温下颗粒检测有严重的计数率限制,无法进一步提高MCP二次电子发射特性 [7] [8];由于氢还原处理,MCP工作过程中会形成离子反馈效应等,影响MCP使用寿命 [3]。随着微电子机械系统技术的发展,高长径比微通道阵列结构和加工产生了新的制备工艺,美国伽利略电子–光学公司的J R Horton [9] 等人于20世纪90年代提出了以硅为基体材料制备MCP,称作先进技术微通道板(Advanced Technology Microchannel Plate, AT-MCP)。该工艺使用干法刻蚀技术制备高长径比的硅微孔结构,再通过低压化学气相沉积(Low Pressure Chemical Vapor Deposition, LPCVD)制备功能层,实现了功能层和基体的分离制备,使得材料的选择多样化、工艺灵活性大、得到的薄膜纯度高、提高了空间分辨率和整体性能、可以使用高熔点的材料作为基底,热稳定性好,可以在恶劣环境中工作等,被认为是MCP制备技术的一次革命 [10]。然而沉积高质量的薄膜工艺比较复杂,难以做到基体绝缘,薄膜电阻率也不易调控 [11] [12]。原子层沉积技术(Atomic layer deposition, ALD)具有自限性、厚度可精确控制和沉积温度低等优势。如今,玻璃微通道阵列的制备工艺较为成熟 [13],通过ALD技术在微通道阵列中制备导电层薄膜为高性能MCP的制备提供一条非常有利的途径。
本文综述了ALD技术制备薄膜的原理,对MCP导电层薄膜进行了设计,综述了MCP导电层研究的进展,最后对打拿极导电层的发展趋势进行了展望。
2. ALD-MCP打拿极导电层结构设计
2.1. ALD技术原理
ALD是可以将物质以单原子膜的形式一层一层镀在衬底表面的方法,与化学气相沉积类似,但是ALD过程中新一层的形成与上一层有所关联。每个ALD周期一般分为四个步骤 [14]:向反应腔中通入第一种前驱体,与基体表面发生化学吸附与反应;通入惰性气体去除多余前驱体和反应副产物;通入第二种前驱体,与吸附在表面的第一种前驱体进行反应形成所需薄膜,最后用惰性气体将多余的气体冲走。
ALD过程包括两种自限制机制,分别为化学吸附自限制和顺次反应自限制,前驱体能够在基体表面快速形成稳定的化学吸附层是化学吸附自限制过程的必要条件,而对于顺次反应自限制过程,通常在反应前需要进行表面的活化,来保证基体表面存在生长位。不断重复这两种自限制反应就可以得到所需要的薄膜 [15] [16]。以原子层沉积Al2O3为例,第一种前驱体三甲基铝(TMA)通入反应腔中,如图1(a)所示,在表面的生长位上进行化学吸附,如图1(b)所示,直至达到化学吸附饱和,如图1(c)所示。用惰性气体N2去除多余前驱体和反应副产物。随后通入第二种前驱体水,如图1(d)所示,发生化学反应生成一层Al2O3的同时为下一层的生长提供条件,如图1(f)所示。不断重复这个过程就能得到所需厚度的Al2O3。
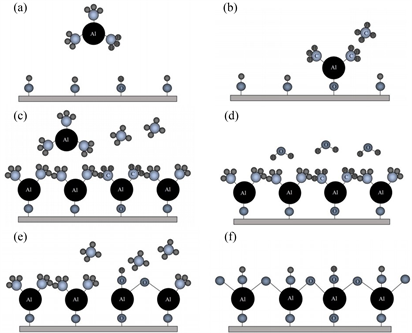
Figure 1. Schematic diagram of the Al2O3 reaction cycle of atomic layer deposition
图1. 原子层沉积Al2O3反应周期示意图
2.2. ALD-MCP导电层优势
ALD-MCP导电层是在微通道阵列基底上通过ALD技术制备薄膜,这种技术实现了功能层和基体材料的分离。相对于RLSG-MCP和AT-MCP的导电层,ALD-MCP导电层具有以下优势:
1) ALD法制备的薄膜在厚度上通过反应循环数控制,可以达到精确的调控,薄膜组分均匀、平滑致密、纯度较高 [17] [18] [19]。薄膜在各个通道内均匀保形覆盖,有利于二次电子倍增,提高增益、延长器件寿命。
2) 对于不同需求的电阻率,制备过程中只需要调节薄膜的循坏百分比就可以实现,工艺相对于传统氢还原更加简单。现已研究出多种材料用于制备高阻薄膜,在材料的选择上具有多样性 [20]。
3) 由于复合薄膜在不同循环配比下具有不同的物理特性,可以根据器件工作条件,在满足器件电阻率允许范围内微调循环比例,实现器件工作稳定,提高器件性能。
4) ALD法制备薄膜生长温度低,降低了工艺的温度要求。ALD法制备薄膜存在窗口温度,一般为150℃~450℃,这使得衬底有了多种选择,尤其是玻璃衬底材料,不会在沉积过程中由于温度过高而发生形变。
2.3. 导电层结构设计
MCP由大量平行的通道组成,这些通道在工作过程中相互并联。当在MCP两端施加工作电压后,每个通道导电层均有电流通过。通过计算可得通道数量和每个通道的电阻,进而得到导电层的电阻率,具体计算过程如下:
通道数量N可由公式(1)计算。
(1)
C为最小周期性单元面积,r为有效区半径。假设MCP外径为25 mm、孔径为6 μm、中心距为7.5 μm、有效区直径等于18.6 mm,板厚0.3 mm。可以计算出通道数量N为5.8 × 106个。假设每个通道电阻都是相同的,整个MCP电阻R可以近似表示为:
(2)
式中,Rchannel为单个通道电阻。
导电层电阻率为ρ,根据电阻率计算公式可以得到MCP每一个通道电阻为:
(3)
L表示通道长度,s表示一个通道导电层横截面积。微通道板工作电压一般为800~1000 V,MCP体电阻R的范围为100~300 MΩ。在已知通道个数的条件下可以计算出Rchannel应为5.8 × 1014~1.7 × 1015 Ω。为了保证打拿极导电层为器件提供连续、稳定的电流,所以设计导电层厚度200 nm。将参数带入(3)中可得导电层电阻率为7.0 × 108~2.1 × 109 Ω·cm。
由于单种材料难以满足导电层的高电阻率要求,因此研究人员提出由两种材料复合形成高阻导电层,通过改变复合薄膜的组成,可以调整电阻率 [21]。图2为研究人员提出的导电层纳米叠层结构示意图。
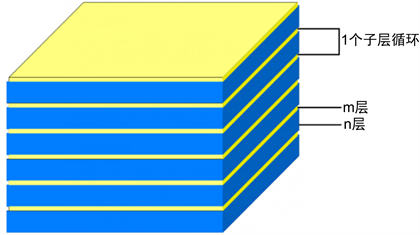
Figure 2. Schematic diagram of nano laminate structure
图2. 纳米叠层结构示意图
图2中m和n分别代表不同材料的层数,最终得到的薄膜是经由两种材料薄膜交替堆叠而成。通过微调叠层纳米复合薄膜材料组分的比例,设计不同总循环数来实现控制薄膜电阻率。
2.4. 通道内薄膜制备分析
对于理想的ALD反应,每个化学反应都发生在经过处理的表面的生长位上。直到反应达到饱和,反应停止,表面生长位全部发生反应。对于平面ALD薄膜制备,根据气体动力学理论 [22],表面的通量J (每单位时间和单位面积从一侧穿过平面的分子数)可以用公式(4)表示
(4)
式中P为被吸附分子的蒸气压(Pa),m分子质量,k是玻尔兹曼常数(1.38 × 10−23 J·K−1),T是温度(K)。由于ALD技术的优越性,沉积可以发生在微通道孔内。但是,由于分子需要更多的时间沿通道向下扩散才能达到通道的中部,因此在通道内部达到饱和要比平面达到饱和需要更多的时间。通道顶部首先接触前驱体,反应先达到饱和,然后反应在通道中进行的越来越深。根据真空中气体流动公式估算分子进入通道的通量。单个通道的特征图如图3所示,沿着通道向下移动一段距离后,平面上的通量减少了的系数(CF)由公式(5)给出
(5)
λ是已经反应饱和通道的长度,p是通道孔的周长,A是通道的横截面积。
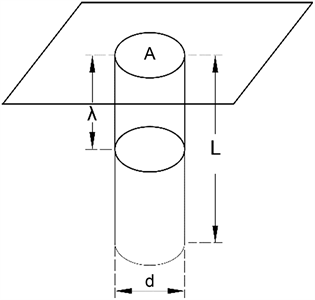
Figure 3. The geometry of film deposition in a hole
图3. 通道内沉积薄膜的几何形状
得到通道深度为λ处的通量J为:
(6)
随着前驱体通过的涂覆长度λ变长,该通量随时间减小。通道内薄膜生长增加长度dλ所需的时间增量dt为可以通过饱和表面覆盖率S算出:
(7)
对公式(7)进行积分,从通道口反应直到通道中部(
),得到公式(8),
(8)
将结果写成长径比
的形式,
(9)
公式(9)表明,相较于平面制备薄膜,在通道内制备薄膜若要做到完全覆盖,必须增加前驱体通入时间。在沉积薄膜的过程中,薄膜厚度的增加是不可忽略的,会引起长径比的变化。因此即使在较窄的通道中制备薄膜时,最小暴露量的标准应从沉积结束时通道的最终长径比计算得出。对于导电层薄膜,通常由两种材料组合形成,制备时需要计算不同材料交替时所产生的损耗 [23]。
3. 导电层研究进展
3.1. AZO复合薄膜
为满足大面积光电探测器应用所需求的薄膜材料,2003年,J. W. Elam与D. Routkevitch、S. M. George等人 [21] 探究了高阻ZnO/Al2O3(AZO)复合薄膜材料。ALD-ZnO和ALD-Al2O3分别采用二乙基锌(DEZ)/H2O和TMA/H2O作为前驱体。将ZnO的循环比在0%~100%范围内调节,探究了不同ZnO循环比对薄膜各项性能的影响,其中包括生长速率、折射率、组分、表面粗糙度、结晶度、电阻率。得到的AZO薄膜几乎是均匀的。另外研究发现,Zn摩尔百分比≥81%的AZO薄膜呈现晶型,随着Al含量的增加,薄膜趋向非晶型。采用电感耦合等离子体原子发射光谱法测得Zn含量随ZnO循环比的变化,发现不同材料前驱体发生交替时,出现蚀刻现象。将这种现象归因于在两种材料交替过程中,TMA上脱落的甲基(-CH3)与Zn反应生成Zn(CH3)2,Al代替了表面的Zn,造成蚀刻。
ZnO/Al2O3复合薄膜的电阻率与Zn含量关系如图4所示,薄膜的电阻率可以在10−3~1016 Ω·cm之间调节,可满足导电层电阻率的需要。
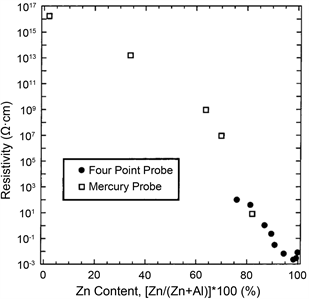
Figure 4. The relationship between resistivity of ZnO/Al2O3 composite film and Zn content [21]
图4. ZnO/Al2O3复合薄膜电阻率与Zn含量的关系 [21]
同年,J. W. Elam等人 [24] 探究了AZO薄膜在高长径比通道中制备问题。通过ALD技术成功在长度为50 μm,孔径为65 nm的阳极氧化铝微通道中沉积了AZO薄膜。研究发现前驱体的脉冲时间对高长径比基体上的薄膜覆盖程度有着很大影响。
2011年,A. U. Mane等人 [25] 在直径为33 mm,通道孔径为20 μm,长径比为60:1的硼硅酸盐玻璃微通道阵列种制备AZO薄膜作为导电层,并在石英基板上同时制备相同参数的AZO薄膜作为比较。实验发现薄膜电阻率与ALD前驱体比例呈线性关系。微通道阵列和石英基板上测得的电阻率有所偏差,这是由于微通道阵列内通道几何形状与理想状态存在偏差。测试了薄膜电阻稳定性,在恒定的100 V偏压,5 × 10−6 Torr下,测试的电阻。测试结果表明,电阻及其稳定,表现出<5%的电阻变化。
2015年,C Ertley等人 [26] 导电层在直径33 mm,通道孔径20 μm,长径比为60:1的硼硅酸盐玻璃中以AZO作为导电层制备MCP。控制电阻在30~500 MΩ,在具有交叉延迟线的光子计数成像仪器中测量了暗计数,为0.085 events/(s·cm2),低于RLSG-MCP。
AZO复合薄膜虽然在电阻率上满足导电层要求,但是实验发现,AZO复合薄膜在不同电压下有着不同的电阻率,电阻率随着电压增大而减小,虽然退火处理能一定程度上减少这种变化,但是MCP工作时需要有更加稳定的体电阻 [27]。同时当施加高压时MCP性能并不稳定,并伴随着导电层被击穿的现象。
3.2. TNO复合薄膜
2010年,Alan Brodie等人 [28] 探究了高阻Nb2O5/Ta2O5(TNO)复合薄膜。用五(二甲胺)钽(PDMATa),五乙氧基铌(NbOEt)作为金属源,水作为氧源,制备不同组分的TNO复合薄膜。研究表明在真空条件下,薄膜有着相对稳定的电阻率,当Ta含量<40%时,电阻率对Ta浓度的依赖性较弱,电阻率随着Ta含量增加增幅不大。当Ta含量>40%时,电阻率随着Ta含量增加明显增加。TNO复合薄膜的电阻率可以在105~109 Ω·cm范围内调整,满足导电层电阻率要求。
制备TNO纳米复合薄膜时,需要对前驱体源进行加热,增加了工艺难度。制备过程发现Ta的浓度要远低于设计的理论值,需要进一步研究这种现象产生的机理。并且研究发现,在高压电场、空气环境等不同环境中薄膜也会有着不同的电阻率。与AZO相比,TNO薄膜的电阻率在电场下的变化大多是不可逆的。
3.3. W/Al2O3、Mo/Al2O3复合薄膜
2013年U. Mane与J. W. Elam等人分别对ALD-W/Al2O3和ALD-Mo/Al2O3的纳米薄膜生长特性和电学特性进行了研究。使用六氟化钨(WF6)、六氟化钼(MoF6)和乙硅烷(Si2H6)作为W、Mo前驱体源,TMA和水作为Al2O3前驱体源。研究发现该薄膜是由非晶态的电介质基质和嵌入其中的导电金属纳米颗粒组成。两种复合薄膜电阻率与金属循环百分比的关系如图5所示。W/Al2O3的电阻率曲线与Mo/Al2O3相似,但Mo/Al2O3复合薄膜的斜率要陡得多。这种差异是由于在相似的生长条件下,ALD-Mo(~10Å/循环)相对于ALD-W(~4Å/循环)的沉积速率高得多。W/Al2O3通过将W的循环百分比控制在10%到30%之间时,电阻率可以控制在108~1012 Ω·cm内。Mo/Al2O3通过将Mo的循环百分比控制在5%到15%之间时,电阻率可以控制在105~1012 Ω·cm范围内,均满足导电层要求。W/Al2O3和Mo/Al2O3在生长过程中均出现两种材料相互抑制的现象。
MCP的电阻会随着温度变化很大,对Mo/Al2O3与W/Al2O3电阻随温度的变化进行了研究,如图6、图7所示,Mo/Al2O3的电阻会随温度升高而减低但是变化较小,电阻会随着Mo的含量而明显变化。测试了三种不同W含量的W/Al2O3薄膜,实验得出W含量越高,越适合在低温的工作环境中。因此对于不同的工作环境,根据实际工作条件,可以通过调整ALD工艺参数来调节MCP导电层金属含量,而不会影响二次电子发射性能。2016年,该团队 [29] [30] [31] [32] 在玻璃微通道内制备了W/Al2O3与Mo/Al2O3复合薄膜作为导电层。在面积为20 cm × 20 cm,孔径为20 μm、长径比为60:1的硼硅酸盐玻璃制备厚度为94 nm的W/Al2O3和Mo/Al2O3,整体增益的不均余小宁<15%,暗计数为0.029 events/(s·cm2)。
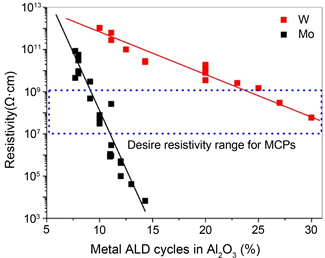
Figure 5. The relationship between the resistivity of W/Al2O3 and Mo/Al2O3 composite films and the metal cycle percentage [32]
图5. W/Al2O3与Mo/Al2O3复合薄膜电阻率与金属循环百分比关系 [32]
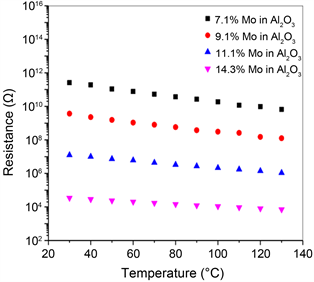
Figure 6. The relationship between Mo/Al2O3 resistance and temperature of different Mo cycle percentages [32]
图6. 不同Mo循环百分比下Mo/Al2O3电阻与温度的关系 [32]
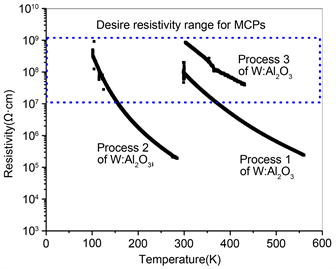
Figure 7. The relationship between temperature and Wo/Al2O3 resistance of different W components [32]
图7. 不同W组分对W/Al2O3电阻率温度的关系 [32]
W/Al2O3与Mo/Al2O3复合薄膜相对于AZO和TNO电阻率随温度变化较小,可以通过工作条件来改变薄膜组分实现稳定工作。同时解决了高压下薄膜被击穿的问题,制备工艺也相对简单。可以作为大面积MCP导电层材料,具有非常好的前景。
3.4. 国内研究现状
国内对MCP的研制较晚,目前国内商业化的MCP主流制备方法还是传统铅硅酸盐玻璃工艺,该方法制备的MCP噪声大、增益低且寿命短。对于高性能的MCP仍需要国外进口。
近年来,ALD制备MCP功能层逐渐成为研究热点,采用的导电层多为AZO。长春理工大学 [11] 分别使用LPCVD和ALD在硅微通道阵列中制备功能层,发现ALD制备导电层的优越性,电阻率更易于控制。2015年中国科学院高能物理研究所的闫宝军等人 [33] 证实ALD技术能够在具有复杂结构的基板(例如玻璃MCP)上沉积均匀的纳米氧化物薄膜,厚度均匀性为2%左右。当导电层厚度为122 nm (ZnO循环百分比75%)时,在直流800V电压下,增益达到最大值2000。
国内ALD-MCP的研究大多数还是集中在二次电子发射层的制备,如2016年,北方夜视丛晓庆等人 [34] 制备Al2O3作为发射层的并研究MCP的性能。研究表明沉积Al2O3后的MCP比传统MCP增益更高,在MCP两端施加的电压为800 V时,增益可以提升12倍。2018年,微光夜视技术重点实验室的郝子恒等人 [35] 探究了ALD沉积工艺参数对MCP二次电子增益的影响。制备了不同厚度的Al2O3发射层,当厚度为93 Å时,增益达到7891。
4. 结论与展望
ALD的自限性、厚度可精确控制和沉积温度低等特点在MCP打拿极导电层制备中有着很大的优势,在增益性能和稳定性上已经有了突破性的进展。然而,目前仍存在一些问题需要研究。
导电层复合薄膜制备过程中,会出现偏离混合规则的情况,导致薄膜组分不均匀,厚度无法准确预测。复合薄膜的生长机理和不同材料之间的腐蚀机制仍需要进一步研究。
ALD-MCP比传统MCP显示出更好的成像效果和较低的本底率。然而由于基体制备工艺的限制 [36],基体结构存在形变,导致薄膜涂覆不均匀,使得MCP整体增益不均匀。在基体制备上,仍需要很多工作。